Horizontal Pallet Wrapping Machine: Effective Delivery and Installation Steps
- Horizontal Pallet Wrapping Machine: Effective Delivery and Installation Steps
- Introduction
- 1. Understanding the Horizontal Pallet Wrapping Machine
- 2. Pre-Delivery Considerations: Preparing Your Facility
- 3. Machine Delivery: Ensuring Safe Transportation
- 4. Unpacking and Inspection on Arrival
- 5. Positioning the Machine: Proper Placement for Optimal Operation
- 6. Electrical Connections and Power Setup
- 7. Testing and Calibration for Optimal Performance
- 8. Operator Training: Ensuring Safe and Efficient Use
- 9. Post-Installation Testing and Quality Control
- 10. Routine Maintenance: Prolonging Machine Lifespan
- 11. Documentation and Reporting: Keeping Records of Installation and Maintenance
- 12. Ensuring Proper Film Supply and Usage
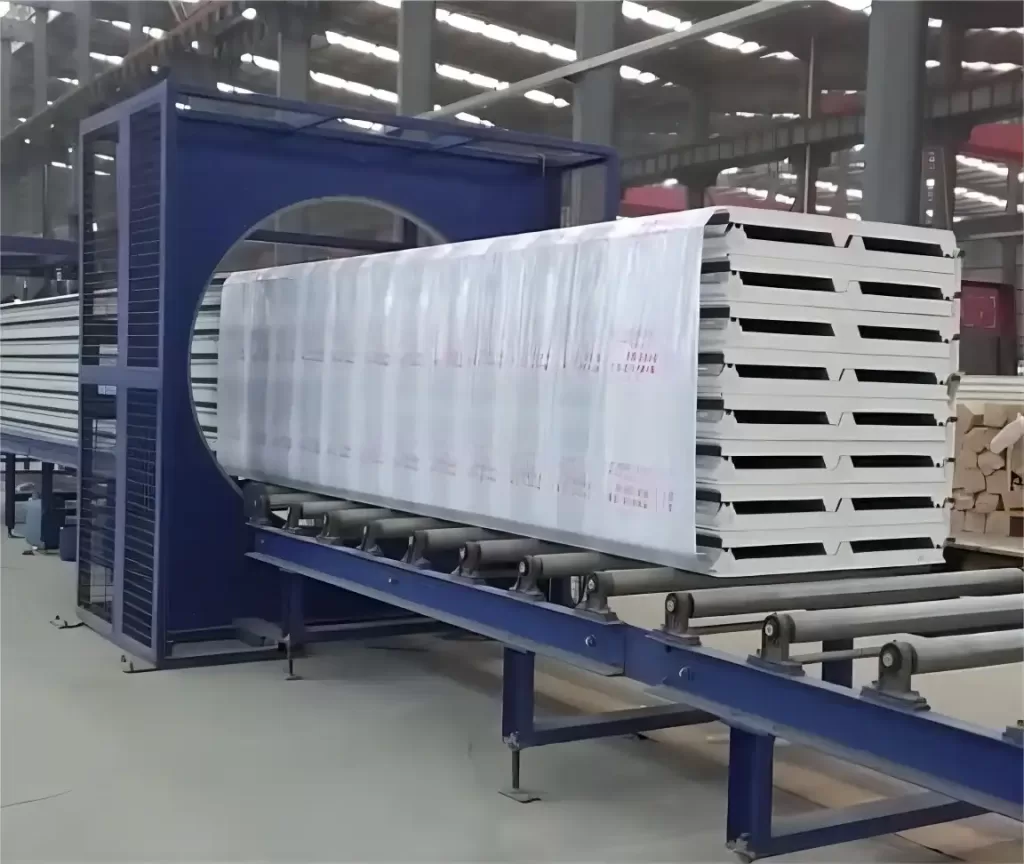
Introduction
In today’s fast-paced industrial landscape, horizontal pallet wrapping machines play a crucial role in ensuring efficient, safe, and secure packaging. Whether you are in the warehousing, logistics, or manufacturing sector, delivering and installing these machines is a pivotal process. A seamless installation can save time, reduce costs, and help avoid unnecessary operational disruptions. However, to achieve this, it’s essential to follow a series of well-planned steps to ensure the machine’s optimal performance. This article will explore the effective delivery and installation steps to guarantee that your investment in a horizontal pallet wrapping machine leads to high productivity, minimal downtime, and maximum ROI.
1. Understanding the Horizontal Pallet Wrapping Machine
Before diving into the specifics of delivery and installation, it’s crucial to understand what a horizontal pallet wrapping machine is and how it fits into your packaging line. Horizontal pallet wrapping machines are used to secure products on pallets using stretch film. Unlike vertical machines, horizontal wrappers move around the pallet horizontally, which can be particularly beneficial for wrapping long or bulky items. These machines ensure consistent tension and even film distribution, providing superior load stability for transportation.
2. Pre-Delivery Considerations: Preparing Your Facility
One of the most overlooked aspects of machine installation is preparing the facility for the arrival of the equipment. It’s vital to ensure that your space can accommodate the size and weight of the machine. Here are key things to consider:
- Space Requirements: Horizontal pallet wrapping machines vary in size. Review the machine’s dimensions and ensure there’s enough floor space for its placement and operation.
- Power Supply: Most machines require a dedicated power source, often three-phase electricity. Make sure your facility has the necessary power configurations.
- Floor Condition: The surface where the machine will be installed should be level and able to support the machine’s weight, as uneven or unstable flooring can cause operational issues.
3. Machine Delivery: Ensuring Safe Transportation
Once the machine is ordered, ensuring a safe and timely delivery is the next crucial step. Delivery logistics can be complex, particularly when dealing with heavy and large machinery. Here’s what you need to pay attention to:
- Shipping Method: Depending on the distance and urgency, machines can be shipped by road, rail, or sea. The method chosen should prioritize minimizing movement during transit to avoid damage.
- Handling and Crating: Ensure the machine is properly crated and supported with padding to prevent any vibrations or shocks during transportation. Incorrect handling can cause significant wear or even damage before installation.
- Insurance: It’s recommended to invest in comprehensive shipping insurance to cover any unforeseen damages that may occur during transportation.
4. Unpacking and Inspection on Arrival
When the horizontal pallet wrapping machine arrives at your facility, it’s vital to carefully inspect it before moving forward with the installation process. Here’s a checklist to follow:
- External Inspection: Check the exterior for any visible signs of damage to the crating or the machine itself. Look for dents, scratches, or other marks that may have occurred during transit.
- Internal Components: Open the packaging and verify that all internal components, such as motors, sensors, and belts, are intact and secure.
- Cross-Check with Packing List: Ensure all parts, accessories, and documents (e.g., manuals, warranties) are accounted for by comparing them with the packing list provided by the manufacturer.
5. Positioning the Machine: Proper Placement for Optimal Operation
After unpacking the machine, the next step is positioning it correctly in the facility. This step is critical as improper placement can lead to inefficiencies and safety hazards. Here’s what to focus on:
- Accessibility: The machine should be placed in an area where it is easily accessible for operators and maintenance personnel. This includes ensuring that there is enough space around the machine for movement.
- Material Flow: Make sure that the machine is integrated smoothly into your production line. The material flow to and from the wrapping machine should be uninterrupted and efficient.
- Alignment: Use precision tools to check that the machine is aligned perfectly. Misalignment can lead to operational inefficiencies or even machine breakdowns over time.
6. Electrical Connections and Power Setup
Connecting the machine to your facility’s power grid is one of the most technical aspects of installation. This should only be done by a licensed electrician or a technician from the machine manufacturer. Important factors to consider include:
- Voltage Matching: Ensure that the machine’s voltage requirements match your facility’s supply. An incorrect voltage setting can damage the machine or lead to operational issues.
- Grounding: Proper grounding is essential to avoid electrical shocks and ensure the safety of the machine and operators.
- Power Capacity: Check that your power system can handle the additional load introduced by the machine, especially if multiple machines operate simultaneously.
7. Testing and Calibration for Optimal Performance
Once the machine is connected to power, the next step is testing and calibrating it to ensure that all parts are working as expected. During this phase, it’s crucial to:
- Run Initial Tests: Operate the machine at low speeds to check if all moving parts function smoothly. Ensure that sensors, motors, and wrapping heads are performing correctly.
- Calibration: The machine’s settings must be calibrated according to the specific needs of your products, including the tension of the stretch film, wrapping speed, and film overlap.

Get Your Best Solution !
8. Operator Training: Ensuring Safe and Efficient Use
One of the most important but often overlooked aspects of installing a horizontal pallet wrapping machine is ensuring that your staff is adequately trained to operate it. Even the most advanced machines require skilled operators to achieve their full potential. Key components of training include:
- Safety Procedures: Operators need to be familiar with the machine’s safety features, including emergency stop functions, to minimize the risk of accidents.
- Operational Techniques: Training should cover the correct way to load and unload pallets, adjust film tension, and set wrapping speeds.
- Troubleshooting: It’s also important that operators know how to troubleshoot basic problems, such as clearing jams, replacing film rolls, and performing minor adjustments.
Comprehensive training ensures that the machine operates at peak efficiency, reduces downtime caused by user errors, and enhances safety.
9. Post-Installation Testing and Quality Control
After the initial installation and operator training, the horizontal pallet wrapping machine should undergo rigorous testing to ensure everything is functioning correctly. This post-installation testing is essential to identify any remaining issues before full-scale operation begins. Testing procedures typically involve:
- Test Runs with Actual Products: Conduct test wraps with the products you’ll be packaging to ensure the machine is functioning as expected. This will help identify any issues with film application, load stability, or speed adjustments.
- Fine-Tuning: During testing, the machine’s settings may need further fine-tuning to match the specific requirements of your products and ensure maximum efficiency.
- Final Inspection: A final inspection by the manufacturer’s technicians is often recommended to ensure that all parts of the machine are correctly installed and calibrated.
10. Routine Maintenance: Prolonging Machine Lifespan
Even the best machines require regular maintenance to ensure long-term reliability. Implementing a routine maintenance schedule will help you avoid unexpected breakdowns and costly repairs. Key areas to focus on include:
- Lubrication: Make sure all moving parts, such as gears, motors, and rollers, are regularly lubricated to prevent wear and tear.
- Belt Tension: Periodically check the tension of belts and chains to ensure they are properly aligned and not too loose or too tight.
- Sensor Calibration: Ensure that sensors, especially those responsible for detecting load presence or adjusting film tension, are regularly calibrated for accuracy.
A well-maintained machine will not only last longer but also reduce downtime, improve wrapping consistency, and increase overall productivity.
11. Documentation and Reporting: Keeping Records of Installation and Maintenance
Keeping detailed records of the installation process, along with regular maintenance and repair work, is critical for tracking machine performance over time. This documentation will help in:
- Warranty Claims: Proper records ensure that you can easily claim warranty support if needed.
- Predictive Maintenance: Reviewing past issues can help you identify patterns and proactively address potential problems before they escalate.
- Training New Staff: Having written records of the installation process and subsequent maintenance can be an invaluable resource when training new operators or technicians.
12. Ensuring Proper Film Supply and Usage
For a horizontal pallet wrapping machine to operate efficiently, it’s essential to have a reliable supply of stretch film and ensure it’s used optimally. This involves:
- Film Quality: Use high-quality film that is compatible with your machine’s specifications to avoid poor wrapping, which can compromise load stability.
- Monitoring Usage: Keep track of how much film is being used per pallet to ensure that you’re not overusing materials, which can drive up costs.
- Adjusting for Different Loads: Different types of loads may require different film thicknesses, tension levels, or wrap patterns. Ensure that your operators are familiar with adjusting the machine settings accordingly.

Get Your Best Solution !