Horizontal Orbital Wrapper and Strapping Machine for Panel and Board: Solution Evaluation and Comparisons
- Horizontal Orbital Wrapper and Strapping Machine for Panel and Board: Solution Evaluation and Comparisons
- 1. Understanding the Horizontal Orbital Wrapper
- 2. The Role of the Strapping Machine
- 3. Evaluating Key Features of Horizontal Orbital Wrappers
- 4. Key Features of Strapping Machines
- 5. Solution Comparisons: Orbital Wrapper vs. Strapping Machine
- 6. Industries Benefiting from Horizontal Orbital Wrappers and Strapping Machines
- 7. Cost Considerations: Upfront Investment vs. Long-Term Gains
- 8. Customization Options for Horizontal Orbital Wrappers and Strapping Machines
- 9. Safety Features in Orbital Wrappers and Strapping Machines
- 10. Integration of Orbital Wrappers and Strapping Machines into Existing Systems
- 11. Real-World Case Study: A Packaging Line Transformation
- 12. Environmental Impact of Horizontal Orbital Wrappers and Strapping Machines
- Conclusion: Finding the Right Packaging Solution for Your Business
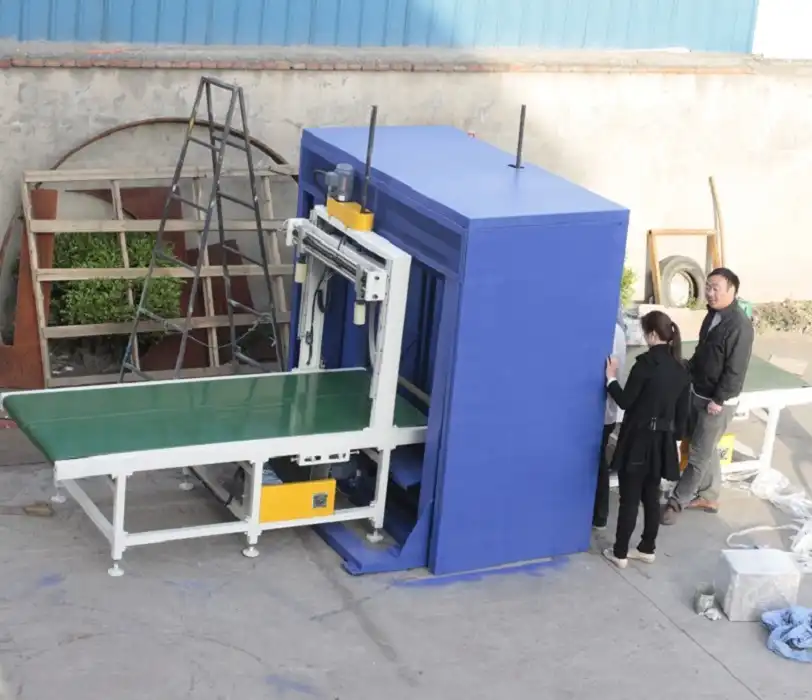
In today’s fast-paced manufacturing world, efficient packaging solutions are critical to maintaining high levels of productivity, especially for industries handling panels and boards. The need for automation in packaging has driven innovations like the horizontal orbital wrapper and strapping machine—two key tools designed to ensure that products such as wood panels, boards, or even drywall are safely packaged for transport or storage.
This article delves into the evaluation and comparison of horizontal orbital wrappers and strapping machines, exploring their key features, benefits, and how they cater to various industrial packaging needs. By the end of this guide, you’ll gain a clearer understanding of which solution best fits your operation’s unique requirements.
1. Understanding the Horizontal Orbital Wrapper
A horizontal orbital wrapper is a machine designed to wrap long or flat items such as panels, boards, or lumber in protective stretch film. The horizontal wrapping mechanism moves around the item horizontally, encasing the product in a secure layer of material that shields it from moisture, dust, and damage during transport.
Key Benefits of Horizontal Orbital Wrappers:
- Versatility: Suitable for various product shapes and sizes.
- Protection: Wraps products securely, preventing potential damage.
- Efficiency: Significantly reduces the time required for manual wrapping.
One of the main advantages of using a horizontal orbital wrapper is that it minimizes the need for manual labor. In high-volume operations, this machine can increase productivity, allowing workers to focus on other tasks while the wrapper ensures consistent and precise wrapping.
2. The Role of the Strapping Machine
While wrapping provides a solid layer of protection, strapping machines ensure that the package remains intact throughout transport. Strapping machines apply strong plastic or metal straps around the package, preventing it from moving or coming apart.
For large, heavy items like boards and panels, strapping is crucial in maintaining package integrity. Automated strapping machines are typically integrated with the orbital wrapping system, providing a seamless packaging solution.
Key Benefits of Strapping Machines:
- Increased Stability: Secures the package, reducing movement and ensuring safer transportation.
- Time Savings: Automated strapping processes are much faster than manual methods.
- Consistency: Provides uniform tension and strap application across all packages.
3. Evaluating Key Features of Horizontal Orbital Wrappers
When selecting the right horizontal orbital wrapper, there are several key features to consider:
- Wrapping Speed: Look for machines that offer adjustable speeds to accommodate different production rates.
- Film Tension Control: Ensure that the machine has precise control over film tension to prevent product damage.
- Customization Options: Some machines allow for customized wrapping cycles, catering to specific product dimensions and shapes.
Horizontal orbital wrappers are especially useful for industries that package large flat items, such as wood panels, metal sheets, or even doors. Their ability to automate the wrapping process ensures faster turnaround times and reduced labor costs.
4. Key Features of Strapping Machines
When comparing strapping machines, some of the most important factors include:
- Strap Material Compatibility: Machines should be able to handle different types of straps, including polyester (PET), polypropylene (PP), or even steel for heavier loads.
- Automatic Tension Control: Ensures straps are applied with uniform tension, reducing the risk of product damage.
- Cycle Speed: A faster cycle means more products can be strapped in less time, ideal for high-volume operations.
Both horizontal orbital wrappers and strapping machines provide vital protection for products, but choosing the right machine depends heavily on your specific operational needs.
5. Solution Comparisons: Orbital Wrapper vs. Strapping Machine
When evaluating these two machines, it’s essential to recognize their unique strengths. Orbital wrappers are designed to encase products in film, offering protection against environmental factors, while strapping machines ensure the package’s structural integrity by securing the wrapped items tightly.
- For Lightweight Products: If your operation deals with lightweight materials, an orbital wrapper may be sufficient to protect the items. However, for heavier or more delicate products, adding a strapping machine ensures added stability during transit.
- For Heavy Products: For heavier loads, both machines working together provide the best protection. The orbital wrapper will protect the surface of the product, while the strapping machine ensures that the load remains secure.
6. Industries Benefiting from Horizontal Orbital Wrappers and Strapping Machines
Woodworking and construction material industries are the largest benefactors of these machines. The ability to wrap and strap large items like plywood sheets, metal panels, and drywall makes these machines essential for packaging in these sectors.
Other industries include:
- Furniture manufacturing
- Glass and window production
- Automotive parts
By adopting these automated packaging machines, companies in these industries can reduce labor costs, increase throughput, and ensure safer handling of their products.
7. Cost Considerations: Upfront Investment vs. Long-Term Gains
One of the major factors when evaluating these machines is cost. While the initial investment for a horizontal orbital wrapper or strapping machine might seem high, the long-term benefits far outweigh the costs.
Key Cost Benefits:
- Reduced Labor Costs: Automation eliminates the need for multiple workers, freeing up resources for other tasks.
- Lower Product Damage Rates: Consistent and secure packaging reduces the chances of damage during shipping.
- Higher Productivity: With faster cycle times, more products can be wrapped and strapped, increasing overall output.
8. Customization Options for Horizontal Orbital Wrappers and Strapping Machines
One of the most significant advantages of modern horizontal orbital wrappers and strapping machines is their flexibility. Most manufacturers offer a wide range of customization options to suit the specific needs of different industries.
Customizable Features to Look For:
- Variable Speed Control: Adjusting the wrapping or strapping speed based on the product type allows for greater control over packaging output.
- Size Adjustability: Machines that can handle different dimensions of panels or boards enable manufacturers to package a wider range of products without needing separate machinery.
- Film or Strap Type Selection: Depending on the material being wrapped, you can select from various film thicknesses and strap types, ensuring optimal protection and load security.
Customizing these machines can lead to higher operational efficiency, as it allows businesses to tailor the equipment to their specific needs, ensuring minimal downtime and consistent performance.
9. Safety Features in Orbital Wrappers and Strapping Machines
When working with heavy or large items such as boards or panels, safety is a top priority. Automated systems like the horizontal orbital wrapper and strapping machine come equipped with features that ensure the safety of both the product and the operator.
Essential Safety Features Include:
- Automatic Shutoff: Machines stop automatically when a jam or error is detected, preventing potential damage to the product or the machine itself.
- Emergency Stop Buttons: Easily accessible buttons allow workers to halt operations instantly in case of an emergency.
- Safety Sensors: These sensors detect any obstructions or misalignment in the package, ensuring that the wrapping or strapping process proceeds smoothly without causing harm.
By incorporating these safety features, companies can reduce the risk of workplace accidents, ensuring a safer environment for their employees.
10. Integration of Orbital Wrappers and Strapping Machines into Existing Systems
For companies looking to improve their packaging lines, the integration of horizontal orbital wrappers and strapping machines into existing systems is relatively straightforward. Most of these machines are designed with modular architecture, allowing them to be added to existing conveyor systems or production lines.
Benefits of Integration:
- Seamless Operation: Integrated systems allow for smooth transitions between wrapping and strapping, reducing the need for manual intervention.
- Higher Throughput: By automating the entire packaging process, from wrapping to strapping, companies can significantly increase their production capacity.
- Improved Workflow: Integration reduces the number of steps in the packaging process, simplifying workflow and boosting overall efficiency.
Proper integration of these machines into existing systems can transform a manual, labor-intensive packaging process into a fully automated, high-speed operation.
11. Real-World Case Study: A Packaging Line Transformation
To demonstrate the impact of implementing a horizontal orbital wrapper and strapping machine, let’s explore a real-world case study. A leading furniture manufacturer was struggling with manual packaging of large wooden panels, which resulted in inconsistent wrapping quality, product damage during shipping, and high labor costs.
By investing in an automated orbital wrapper and strapping system, the company experienced several improvements:
- Reduced Damage: The machine applied a uniform layer of film and straps to each product, preventing damage during transport.
- Labor Savings: Automation allowed the company to reduce the number of workers needed for packaging, saving labor costs by over 30%.
- Increased Output: Packaging speed doubled, allowing the company to meet growing demand without increasing operational hours.
This case study shows the significant advantages of adopting automated systems for packaging large and heavy items.
12. Environmental Impact of Horizontal Orbital Wrappers and Strapping Machines
One growing concern in the manufacturing and packaging industry is the environmental impact of packaging materials and processes. Fortunately, modern horizontal orbital wrappers and strapping machines offer eco-friendly options that help reduce waste.
Sustainable Features to Look For:
- Film Optimization: Machines that optimize film usage can minimize waste, ensuring that only the necessary amount of material is used for each package.
- Recyclable Materials: Many machines are compatible with recyclable films and strapping materials, reducing the overall environmental footprint.
- Energy Efficiency: Advanced models consume less energy, making them more sustainable in the long run.
By incorporating these eco-friendly features, companies can not only lower their operational costs but also demonstrate their commitment to environmental sustainability.
Conclusion: Finding the Right Packaging Solution for Your Business
In the world of panel and board packaging, choosing between a horizontal orbital wrapper and a strapping machine depends heavily on your specific needs. Both machines offer substantial benefits, from increasing productivity and consistency to reducing labor costs and product damage. However, the most effective packaging line often incorporates both machines, working in tandem to deliver comprehensive protection and secure transportation for your products.
By carefully evaluating the features, customization options, and long-term benefits, companies can make informed decisions that maximize efficiency and minimize costs. The right combination of wrapping and strapping solutions can transform your packaging process, providing faster, safer, and more consistent results that directly impact your bottom line.

Get Your Best Solution !