Understanding the Horizontal Orbital Stainless Steel Coil Wrapping Machine
For professionals in manufacturing, logistics, and metal processing, understanding the mechanics and capabilities of a horizontal orbital stainless steel coil wrapping machine is key to optimizing packaging operations. This specialized equipment plays a crucial role in protecting valuable stainless steel coils during storage and transit. This guide provides an in-depth look at the design, functionality, operational benefits, and considerations for implementing these systems.
What is a Horizontal Orbital Wrapping Machine?
Horizontal orbital wrappers are automated or semi-automated packaging systems designed specifically for applying protective materials (like stretch film, VCI paper, or other wraps) around the circumference of coiled products, particularly heavy items like stainless steel coils. The "horizontal" aspect refers to the orientation in which the coil typically travels through the machine, and "orbital" describes the motion of the wrapping material dispenser as it revolves around the coil's outer diameter.
Anatomy of the Machine: Key Components
Understanding the core components helps clarify how these machines achieve efficient and secure coil packaging:
1. Rotating Ring Assembly
The heart of the orbital wrapper. This ring holds the film carriage and rotates around the coil as it passes through the machine's aperture. Its speed and precision are critical for consistent wrap application.
2. Conveyor System
An integrated system (often powered rollers or chain conveyors) designed to move heavy stainless steel coils into the wrapping zone, hold them steady during wrapping, and transport them out. System design varies based on coil size, weight, and line integration needs.
3. Film Carriage and Dispenser
This unit is mounted on the rotating ring and houses the roll of wrapping material. It typically includes features for pre-stretching the film (improving yield and load containment) and controlling application tension.
4. Control System (PLC)
The machine's brain, usually a Programmable Logic Controller (PLC) with a Human-Machine Interface (HMI). Operators use this to set parameters like rotation speed, conveyor speed, number of wraps, film tension, and overlap percentage. Modern systems offer recipe storage for different coil types.
5. Clamping and Cutting Unit
Automated systems feature mechanisms to grip the leading edge of the film at the start of the cycle and to cut and secure the film tail at the end, enabling seamless operation without manual intervention.
Design Characteristics and Operational Impact
Several design features contribute directly to the machine's effectiveness in an industrial environment:
* Through-Ring Design: Allows coils to pass directly through the rotating ring, facilitating inline integration with production or slitting lines.
* Variable Speed Control: Enables optimization of the wrapping process based on coil dimensions and desired throughput.
* Robust Construction: Built with heavy-gauge steel frames and durable components to handle the weight of steel coils and withstand continuous operation in demanding industrial settings.
* Customizable Configurations: Machines can often be tailored regarding ring size, conveyor type, level of automation, and wrapping material capabilities to match specific application needs.
The Orbital Wrapping Process Explained
The typical operational sequence for wrapping a stainless steel coil involves several steps:
- Coil Infeed: The coil is placed onto the infeed conveyor, often via crane, forklift, or an upstream process.
- Positioning: The conveyor moves the coil into the wrapping zone, centered within the rotating ring's aperture. Sensors confirm correct positioning.
- Wrapping Cycle Initiation: The operator starts the cycle via the control panel, or it begins automatically if integrated into a line.
- Film Application: The clamping unit secures the film start, the ring begins to rotate, and the film carriage dispenses the wrapping material around the coil. Simultaneously, the conveyor may slowly move the coil forward or rotate it to ensure complete coverage depending on the wrap pattern selected.
- Wrapping Completion: Once the preset number of wraps is applied, the ring stops, and the automated cutting/sealing unit finishes the cycle.
- Coil Outfeed: The securely wrapped coil is transported out of the machine via the outfeed conveyor for storage or shipping.
Essential Safety Features
Operator safety is paramount when dealing with heavy machinery and rotating components:
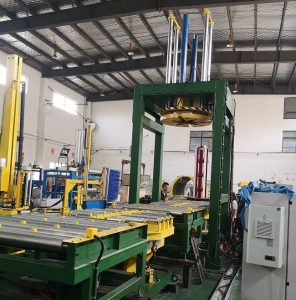
- Safety Fencing/Guarding: Physical barriers prevent accidental contact with moving parts during operation.
- Light Curtains: Presence-sensing devices that stop the machine if an object or person enters a hazardous zone.
- Emergency Stop Buttons: Strategically placed E-stops allow for immediate shutdown in case of an issue.
- Interlocked Access Doors: Prevent machine operation if access gates or panels are open.
- Load Stability Sensors: Ensure the coil is properly positioned before the cycle begins, preventing potential machine damage or wrap failure.
Operational Benefits of Orbital Wrapping Technology
Implementing horizontal orbital wrappers for stainless steel coils offers tangible advantages:
- Enhanced Product Protection: Provides a tight, consistent wrap that shields coils from moisture, dust, dirt, and surface damage during handling and shipping. Using VCI (Vapor Corrosion Inhibitor) film adds rust protection.
- Increased Throughput: Significantly faster than manual wrapping methods, boosting overall packaging line efficiency.
- Reduced Material Consumption: Film pre-stretch capabilities can optimize material usage, leading to cost savings compared to manual wrapping.
- Improved Load Security: Consistent tension control ensures coils are securely unitized, reducing the risk of shifting or telescoping during transit.
- Lower Labor Costs: Automation reduces the need for manual labor in the packaging process.
Maintenance and Ensuring Longevity
Like any industrial equipment, regular maintenance is crucial for reliable performance:
- Routine Inspections: Regularly check wear parts like drive belts, rollers, film carriage components, and cutting blades.
- Lubrication: Follow manufacturer guidelines for lubricating bearings, chains, and other moving parts.
- Cleaning: Keep the machine free of dust, debris, and film residue, which can interfere with sensors and mechanical parts.
- Preventive Maintenance Schedule: Adhere to the recommended schedule for inspections and parts replacement to minimize unexpected downtime.
Real-World Applications and Industry Impact
Horizontal orbital wrappers are indispensable in sectors dealing with large cylindrical or coiled products:
- Steel Service Centers: Protecting slit coils, master coils, and blanks after processing.
- Metal Processing Facilities: Packaging coils of aluminum, copper, and other metals.
- Wire and Cable Industry: Wrapping large spools or reels of wire and cable.
- Pipe and Tube Manufacturing: Bundling and wrapping pipes or tubes for shipment.
Example Scenario: A stainless steel service center processing high-value, surface-critical coils for the automotive industry utilizes a horizontal orbital wrapper. The machine applies multiple layers of stretch film with controlled tension, preventing scratches and edge damage. Integrated VCI film provides corrosion protection. This automated process ensures consistent quality, reduces packaging time, and minimizes damage claims, directly impacting the center's profitability and customer satisfaction.
Future Trends in Coil Wrapping
The technology continues to evolve:
- Smart Integration (Industry 4.0): Connectivity for remote monitoring, diagnostics, performance tracking, and integration with plant-wide Manufacturing Execution Systems (MES).
- Advanced Automation: Fully robotic loading/unloading, automatic adjustment based on coil dimensions read by sensors.
- Sustainable Solutions: Development of machines optimized for thinner gauge films or biodegradable/recyclable wrapping materials.
- Enhanced Safety Systems: More sophisticated sensor technology and predictive safety features.
Conclusion
The horizontal orbital stainless steel coil wrapping machine is a vital asset for industries requiring efficient and reliable packaging of metal coils. Its specialized design delivers superior protection, optimizes material usage, increases throughput, and enhances safety compared to manual methods. By understanding its components, operation, and benefits, businesses can leverage this technology to protect their products, streamline operations, and maintain a competitive edge in the market. Proper selection, integration, and maintenance are key to maximizing the return on investment for this essential packaging equipment.