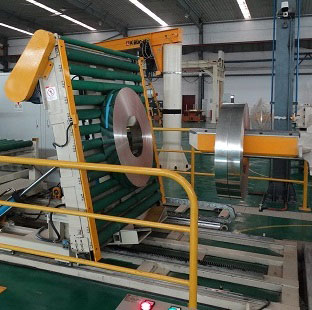
When it comes to packaging coiled materials, the choice between a horizontal and vertical coil wrapping machine is not simply a matter of preference; it’s a strategic decision that affects efficiency, cost, and product integrity. Each machine type offers unique benefits, designed to address different operational needs and challenges. For companies that rely on high-volume coil packaging, understanding the distinctions between these two machines is essential. It’s about more than wrapping coils—it’s about enhancing productivity, improving consistency, and ultimately supporting long-term growth.
Both horizontal and vertical coil wrapping machines are indispensable in industries that handle heavy-duty materials, yet they function differently and offer distinct advantages. Horizontal machines, for example, are often favored for larger coils and high-speed operations, whereas vertical machines excel in space-constrained environments or with smaller coils. Deciding which machine aligns best with my operation requires a closer look at how each type performs and the specific benefits they provide.
This article explores the characteristics, advantages, and ideal use cases for horizontal and vertical coil wrapping machines, offering insight into which solution might be the best fit depending on operational goals.
[claim] Choosing between a horizontal and vertical coil wrapping machine depends on coil size, facility layout, and production requirements. Each machine offers unique advantages that can improve efficiency, consistency, and overall productivity.
- 1. How Does a Horizontal Coil Wrapping Machine Work?
- 2. What Are the Key Advantages of Vertical Coil Wrapping Machines?
- 3. How Do Space and Facility Layout Affect the Choice?
- 4. What Impact Does Coil Size and Weight Have on Machine Selection?
- Conclusion: Making the Right Choice for Optimal Efficiency and Quality
1. How Does a Horizontal Coil Wrapping Machine Work?
1.1 The Mechanics of Horizontal Wrapping
A horizontal coil wrapping machine is designed to wrap coils that are placed on their sides. The coil remains stationary while the machine’s arm rotates around it, applying the wrapping material layer by layer. This setup ensures that the entire coil circumference is covered in one smooth motion. The machine’s automated features make it easy to adjust wrapping tension, speed, and material thickness to fit different coil types. Horizontal machines are often equipped with adjustable arms and tension settings to accommodate coils of varying sizes, adding to their versatility.
This wrapping style is particularly advantageous for large coils, as the horizontal position provides stability and allows the machine to apply wrap uniformly. The mechanics behind the horizontal machine support quick, efficient wrapping without the need for manual adjustments during each cycle. This feature is valuable in high-volume environments where speed and consistency are essential.
1.2 Enhanced Speed and Throughput
Horizontal coil wrapping machines are built for efficiency. By automating the wrapping process and positioning the coil horizontally, these machines can wrap products faster than their vertical counterparts. In high-demand operations, where production speed can make a significant difference in profitability, a horizontal machine helps maintain a steady flow. Every coil is wrapped consistently, meeting production deadlines with ease.
The speed of a horizontal wrapping machine makes it ideal for industries with rigorous output demands. For example, steel and aluminum manufacturers who handle heavy, large-diameter coils benefit greatly from the quick turnaround these machines provide. The result is a boost in throughput, as coils move smoothly through the wrapping line, reducing downtime and increasing overall productivity.

1.3 Applications and Best Use Cases
Horizontal wrapping machines are best suited for facilities with ample space and high production needs. These machines excel in handling large, heavy coils that require uniform, secure wrapping. Industries that produce steel, wire, or cable coils find horizontal machines invaluable for ensuring each coil is adequately protected for transport or storage. Additionally, the stability provided by the horizontal setup is critical for heavy-duty applications, as it reduces the risk of coil displacement or shifting during the wrapping process.
Facilities that prioritize speed, consistency, and high-volume output often choose horizontal machines to streamline their operations. For any business that relies on continuous, uninterrupted production, a horizontal wrapping machine is an investment in both efficiency and quality.
2. What Are the Key Advantages of Vertical Coil Wrapping Machines?
2.1 Efficient Space Utilization in Compact Environments
Vertical coil wrapping machines are designed with space efficiency in mind, making them ideal for facilities where floor space is limited. Unlike horizontal machines that require more room for both the machine and coil positioning, vertical wrapping machines allow coils to be stacked vertically, significantly reducing the machine’s footprint. In facilities with constrained space, this compact setup provides an efficient solution that doesn’t compromise on wrapping quality.
The vertical design allows operators to wrap coils upright, providing easier access to controls and enabling the use of a smaller, streamlined wrapping area. For facilities where maximizing floor space is crucial, a vertical coil wrapping machine is a smart choice that aligns with space management strategies without sacrificing performance.
2.2 Precision in Wrapping Smaller Coils
Vertical coil wrapping machines are especially advantageous when it comes to handling smaller, lighter coils. These machines can precisely control wrap tension and layering, ensuring that even delicate or narrow-diameter coils receive consistent coverage. This level of control prevents overwrapping or underwrapping, which can be common in manual or less specialized machines. By offering precision, vertical machines ensure product protection without overusing wrapping materials.
For industries that handle delicate materials or coils with smaller dimensions, the accuracy provided by a vertical machine is a distinct advantage. The machine’s settings can be adjusted easily for different coil sizes, allowing for smooth transitions between products and eliminating the need for manual recalibrations, which are often time-consuming.
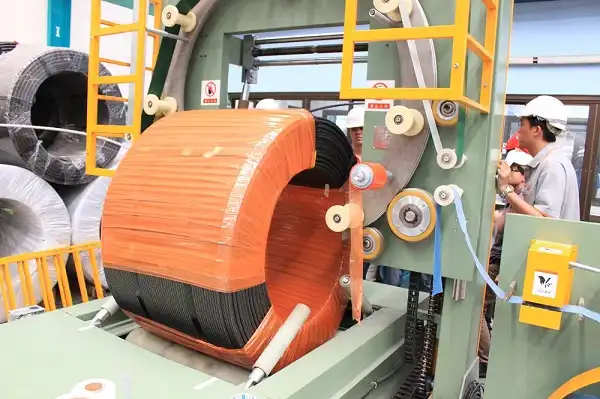
2.3 Adaptability and Versatility for Varied Coil Types
Vertical coil wrapping machines are designed to be highly adaptable, with settings that can be customized based on coil size, material, and packaging requirements. This versatility makes them suitable for facilities that package a variety of coil types, from small electrical wire coils to medium-sized copper coils. The ease of adjusting settings enables operators to handle different coils efficiently, maintaining productivity even when transitioning between products.
The adaptability of vertical machines is particularly useful in industries with diverse packaging needs, such as electrical manufacturing or plumbing supply. By quickly adjusting for different products, the machine reduces downtime and supports a flexible production line. Vertical machines provide a seamless solution for businesses that need to wrap multiple coil sizes without extensive reconfiguration.
3. How Do Space and Facility Layout Affect the Choice?
3.1 Maximizing Layout Efficiency with Horizontal Machines
When considering a horizontal coil wrapping machine, facility layout plays a crucial role. Horizontal machines require ample space for both the machine itself and the horizontally positioned coils. Facilities with spacious layouts can accommodate these machines more comfortably, allowing operators to work efficiently around them. The horizontal configuration provides stability, making it ideal for environments where heavy or large coils are standard.
In a well-planned layout, a horizontal machine can support streamlined operations, where coils are smoothly transferred from one station to another without space limitations. By dedicating specific areas to wrapping, storage, and loading, I can create a cohesive flow that maximizes productivity. For facilities that prioritize high throughput and have the space to support it, a horizontal machine seamlessly integrates into the layout, ensuring consistent output.
3.2 Efficient Use of Limited Space with Vertical Machines
For facilities where space is at a premium, vertical coil wrapping machines offer a more compact alternative. Vertical machines allow coils to be wrapped in an upright position, saving valuable floor space and fitting more easily into constrained environments. This layout flexibility is essential for smaller operations or facilities where multiple machines need to share space, allowing production to continue smoothly without overcrowding.
Vertical machines also enable more efficient organization in the production line, as they can be positioned in tighter spaces or along walls, maximizing layout efficiency. For operations that need to prioritize space without compromising on wrapping quality, vertical machines provide the functionality of larger equipment in a more compact design, making them an ideal choice.
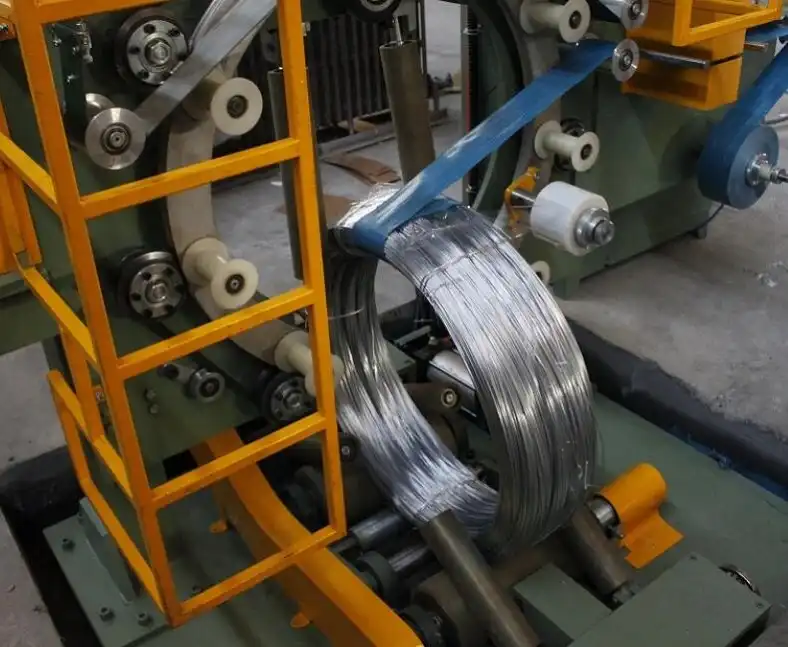
3.3 Choosing Based on Facility Workflow Needs
The facility’s workflow requirements are just as important as space considerations. For high-speed, high-volume production, a horizontal wrapping machine might be preferable, as it aligns with larger operational demands. However, for more varied workflows that handle different coil sizes and materials, the flexibility and smaller footprint of a vertical machine may be more advantageous. By assessing layout and workflow in tandem, I can determine which machine best suits the facility’s unique needs.
Ultimately, choosing between horizontal and vertical machines should involve a balance of layout, production goals, and daily workflow. Each machine type offers distinct advantages, and the right choice depends on how well it integrates into the facility’s overall operations, contributing to a more efficient and productive environment.
4. What Impact Does Coil Size and Weight Have on Machine Selection?
4.1 Handling Large, Heavy Coils with Horizontal Machines
Horizontal coil wrapping machines are designed with large, heavy coils in mind. When working with sizable coils, such as steel or thick cables, stability is essential during the wrapping process. The horizontal position ensures that the coil remains secure, preventing movement that could lead to inconsistencies in wrapping. With the coil’s weight evenly distributed, a horizontal machine can apply uniform layers without the risk of tipping or shifting, which is especially important for heavy-duty applications.
This setup is crucial for industries where coil integrity must be preserved during handling and transportation. By choosing a horizontal machine, I’m ensuring that each coil, regardless of size, receives stable, consistent wrapping, reducing the likelihood of damage and enhancing product protection.
4.2 Wrapping Smaller or Lighter Coils Efficiently with Vertical Machines
For smaller or lighter coils, a vertical coil wrapping machine provides the precision needed without requiring extensive support or space. These machines allow operators to wrap narrow-diameter coils securely, applying wrap with consistent tension and alignment. Vertical machines are ideal for materials like wiring, tubing, or copper coils, which may not require the heavy-duty support that larger coils demand.
With a vertical configuration, operators can quickly adjust settings for different coil types, making the machine versatile enough to handle a variety of lighter coils. This efficiency is beneficial in facilities where multiple coil sizes need to be wrapped throughout the day, as it supports seamless transitions and flexible production without excessive reconfiguration.
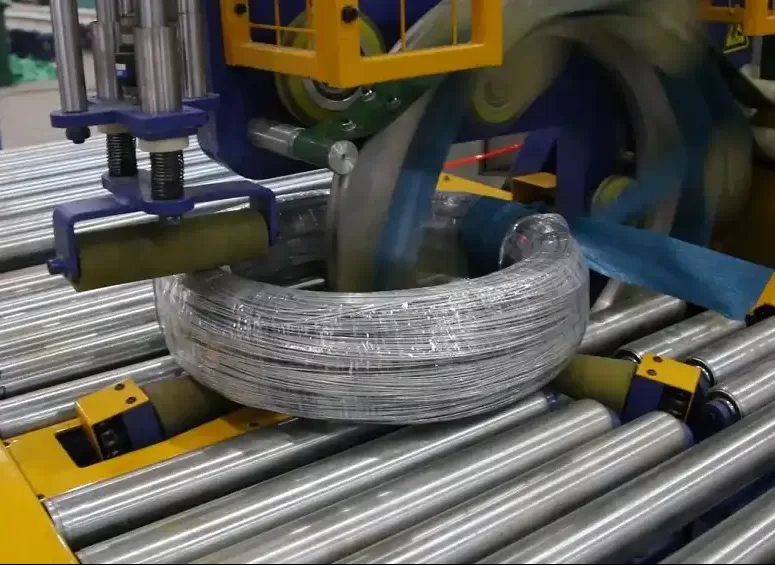
4.3 Matching Machine Type to Product Requirements
Choosing the right machine ultimately depends on the specific requirements of the coils being wrapped. For operations that primarily handle heavy, large-diameter coils, a horizontal machine offers stability and the strength needed for secure wrapping. For facilities managing lighter or more varied coil types, a vertical machine’s adaptability and compact design may be the ideal fit. By aligning the machine selection with product needs, I can ensure a smoother workflow and higher-quality packaging across the board.
Matching machine type to product requirements is a strategic decision that supports both operational goals and product quality. With the right machine in place, my facility can handle its unique demands efficiently, ensuring that every coil is wrapped safely and to specification, whether it’s a heavy-duty industrial coil or a lighter, more delicate product.
Conclusion: Making the Right Choice for Optimal Efficiency and Quality
Selecting between a horizontal and vertical coil wrapping machine involves more than just assessing space or cost; it’s about understanding how each machine aligns with production needs, coil specifications, and facility layout. Horizontal machines offer robust support for larger coils and high-throughput operations, while vertical machines provide compact, adaptable solutions ideal for space-constrained environments and varied coil sizes. Each machine type brings unique advantages to the table, and the best choice depends on a careful assessment of operational priorities.
Investing in the right coil wrapping machine means committing to improved efficiency, consistent quality, and streamlined operations. By choosing a machine that meets my facility’s needs, I can enhance productivity, reduce errors, and maintain product integrity, ensuring that every coil is wrapped securely and ready for transport or storage.
[claim] Whether opting for a horizontal or vertical coil wrapping machine, the decision impacts efficiency, quality, and operational flow. Selecting the right machine enhances productivity and ensures reliable, high-quality packaging for every coil.

Get Your Best Solution !