Understanding Highly Efficient Automated Pallet Wrapping Machines
Automated pallet wrapping machines, also known as stretch wrappers, are essential equipment in modern manufacturing and distribution centers. These systems are specifically engineered to wrap and secure palletized loads using stretch film, preparing them for safe and stable transportation or storage. By automating the wrapping process, businesses can achieve significant improvements in efficiency, load integrity, and operational safety compared to manual methods.
Key Benefits of Automated Pallet Wrapping
Investing in automated pallet wrapping technology offers several advantages:
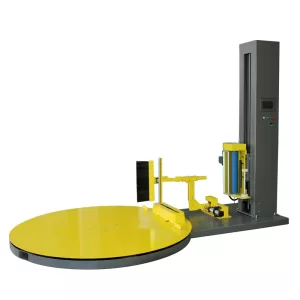
- Enhanced Load Stability and Security: Consistent and correctly tensioned film application unitizes the load, preventing shifting, damage, or product loss during transit.
- Improved Packaging Efficiency: Automated systems wrap pallets significantly faster than manual methods, increasing throughput at the end of your production or packaging line. Features like pre-set wrapping parameters ensure consistent cycle times.
- Optimized Stretch Film Consumption: Modern machines often feature powered pre-stretch systems that stretch the film before application (often 200-300%). This maximizes film yield, significantly reducing material costs and environmental impact.
- Increased Worker Safety: Automating the wrapping process eliminates the physically demanding and potentially hazardous task of manually walking around a pallet with heavy film rolls, reducing risks of back injuries and repetitive strain.
- Consistent Wrap Quality: Machines apply film with consistent tension and overlap, regardless of the operator, ensuring every pallet meets predefined security standards.
Selecting the Right Automated Pallet Wrapper
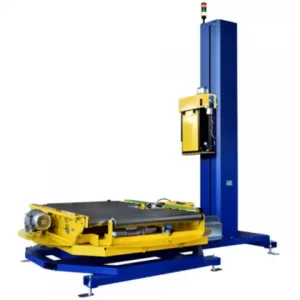
Choosing the appropriate packaging machine requires careful consideration of your specific operational needs. Key factors include:
1. Load Characteristics:
- Size and Weight: Ensure the machine's turntable or rotary arm capacity can handle your typical and maximum pallet dimensions and weight.
- Load Stability: Unstable or very light loads might require specific features like top pressure plates or specialized wrapping patterns.
2. Throughput Requirements:
- Estimate the number of pallets per hour or per shift that need wrapping. This will determine whether a semi-automatic or fully automatic system is necessary and the required wrapping speed.
3. Machine Type and Automation Level:
- Turntable Wrappers: The pallet rotates on a turntable. Suitable for many standard applications.
- Rotary Arm Wrappers: The load remains stationary while a wrapping arm rotates around it. Ideal for very heavy, unstable, or oversized loads.
- Automation: Semi-automatic machines require an operator to attach and cut the film, while fully automatic systems integrate into conveyor lines, performing the entire process without manual intervention.
4. Critical Machine Features:
- Film Pre-Stretch: Essential for cost savings. Look for powered pre-stretch systems and understand the percentage they offer.
- Wrap Settings Control: The ability to customize parameters like film tension, top/bottom wrap counts, wrapping speed, and film overlap is crucial for optimizing load containment for different product types.
- User Interface and Programmability: An intuitive control panel, potentially with password protection and saved wrap programs for different load types, improves ease of use and consistency.
- Safety Features: Look for adequate guarding, emergency stops, and sensors to protect operators.
5. Operational Considerations:
- Durability and Reliability: Choose machines built for industrial environments with a reputation for longevity.
- Maintenance and Support: Consider ease of maintenance, availability of spare parts, and manufacturer support.
Maximizing Your Investment
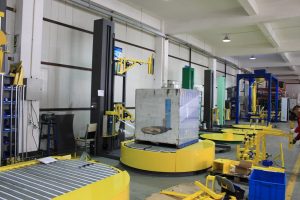
To get the most from your automated pallet wrapper:
- Use Quality Stretch Film: Select film appropriate for your machine's pre-stretch capabilities and load requirements.
- Perform Regular Maintenance: Follow the manufacturer's recommended maintenance schedule to ensure optimal performance and longevity.
- Train Operators: Ensure personnel are properly trained on machine operation, safety procedures, and basic troubleshooting.
By carefully evaluating your needs and selecting a machine with the right features, you can significantly improve the efficiency, safety, and cost-effectiveness of your end-of-line packaging operations. An automated pallet wrapper is a valuable investment for any facility looking to optimize its logistics and protect its products during transit.