Hidden Costs in Steel Coil Packaging and How to Avoid Them
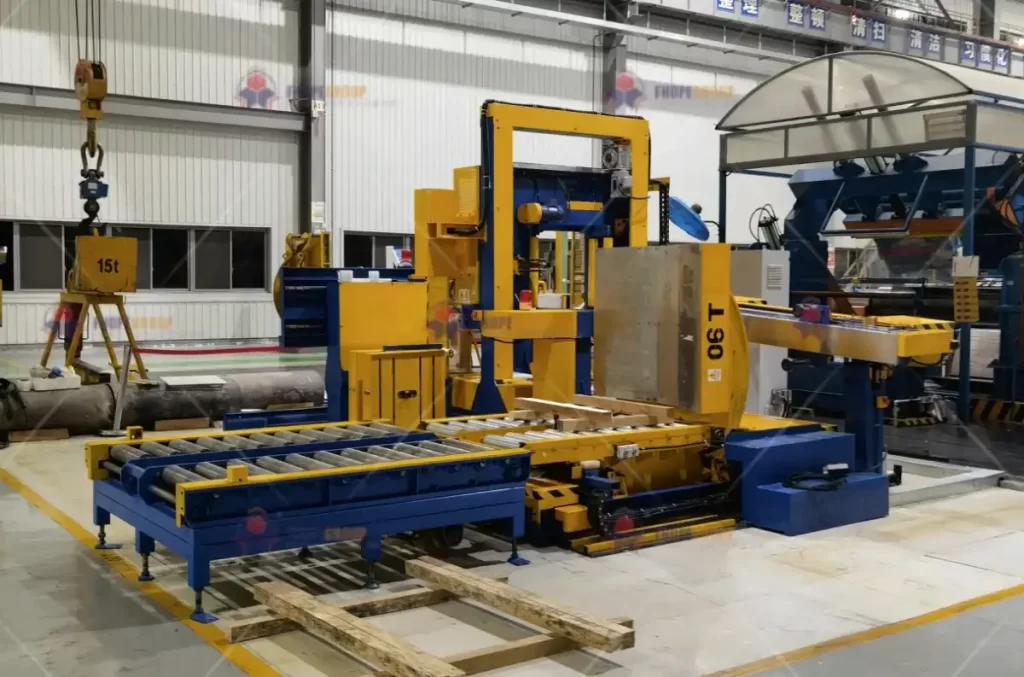
Steel coil packaging is a critical process in various industries, from construction to automotive manufacturing. While the initial costs of packaging machinery and materials are often calculated and budgeted for, there are hidden costs that can significantly impact your bottom line. These unanticipated expenses can be avoided with the right knowledge and proactive strategies. In this article, we’ll explore the various hidden costs associated with steel coil packaging and provide actionable solutions to help you mitigate them.
1. Inefficient Packaging Processes
One of the biggest hidden costs in steel coil packaging is inefficiency. Many companies rely on outdated or poorly optimized systems that slow down production, leading to longer lead times and increased labor costs. If your packaging line isn’t designed for speed and accuracy, you’ll end up paying more in the long run due to unnecessary delays and bottlenecks.
How to Avoid This: Invest in automated packaging systems that are designed for high-speed operations. Look for solutions that offer features like automatic strapping and coil wrapping, which can reduce the need for manual labor and improve overall efficiency. Implementing lean manufacturing principles can also help you streamline your processes and minimize wasted time and resources.
2. Increased Labor Costs
Manual packaging operations often require a large workforce to keep production running smoothly. While these labor costs might seem manageable on paper, they can quickly add up when you factor in overtime, employee turnover, and training expenses. Additionally, the more workers you have handling the packaging process, the greater the chance for errors, which can lead to rework or damaged products.
How to Avoid This: Consider switching to automated or semi-automated packaging systems that can handle more tasks with fewer workers. Not only will this reduce your labor costs, but it will also decrease the likelihood of human error, leading to fewer damaged goods and reduced rework costs. Additionally, automated systems can operate 24/7, allowing for round-the-clock production without needing to hire more workers for night shifts.
3. Damage to Coils During Handling
Another significant hidden cost in steel coil packaging is damage that occurs during handling. Coils that are improperly packaged or secured can shift during transport, leading to dents, scratches, or even complete product loss. This damage not only affects the appearance of the coils but also their functionality, potentially leading to customer complaints and returns.
How to Avoid This: To reduce the risk of damage, invest in high-quality protective packaging materials such as durable wraps and corner protectors. Additionally, ensure that your packaging system is designed to secure the coils tightly, preventing them from shifting during transport. Automated strapping systems can help achieve consistent tension across all coils, providing better protection than manual methods.
4. Excess Material Usage
Many companies unknowingly waste packaging materials, leading to higher-than-necessary costs. This is often due to outdated equipment that isn’t optimized for material efficiency or human error in manual packaging processes. Using more material than needed not only drives up costs but also contributes to environmental waste, which could affect your company’s sustainability goals.
How to Avoid This: Automated packaging systems can be calibrated to use just the right amount of material for each coil, minimizing waste. By ensuring that each coil is wrapped securely but without excess material, you can save money while reducing your environmental footprint. Additionally, consider using recyclable materials that are both cost-effective and eco-friendly.
5. Unplanned Downtime
Unscheduled downtime is one of the most expensive hidden costs in any packaging operation. When machines break down or require maintenance, production halts, leading to missed deadlines and delayed shipments. The longer the downtime, the more it will cost your business in terms of lost productivity and potential penalties for late deliveries.
How to Avoid This: Implement a preventive maintenance program that includes regular inspections and servicing of your packaging machinery. By catching potential issues early, you can reduce the likelihood of breakdowns and ensure that your production line runs smoothly. Additionally, consider investing in machines with built-in diagnostics that can alert you to problems before they lead to costly downtime.
6. Overlooking Energy Consumption
Many companies fail to account for the energy costs associated with running their packaging machinery. Steel coil packaging equipment can consume significant amounts of electricity, especially if it’s outdated or inefficient. High energy consumption can lead to increased utility bills, which may go unnoticed until they become a significant expense.
How to Avoid This: Upgrade to energy-efficient packaging machines that are designed to use less power without compromising performance. Look for systems with energy-saving features, such as automatic shutdown during idle times or adjustable speed settings. Regularly reviewing your energy usage can also help identify areas where you can cut down on consumption, ultimately lowering your operating costs.

Get Your Best Solution !
7. Lack of Proper Training
Inadequate training for workers who operate packaging machinery can result in costly mistakes, equipment damage, and accidents. The costs associated with improper use of machinery can include not only repairs and replacements but also potential legal liabilities if employees are injured. Moreover, improper use of equipment can lead to increased wear and tear, shortening the lifespan of your machinery.
How to Avoid This: Invest in comprehensive training programs for all employees who handle or maintain the packaging equipment. Proper training ensures that workers are familiar with the equipment's functions, safety protocols, and troubleshooting procedures. Regular refresher courses and hands-on training can help prevent accidents, reduce machine downtime, and extend the lifespan of your equipment.
8. Underestimating the Importance of Packaging Design
Packaging design might seem like a minor detail, but it can have a significant impact on your costs. Poorly designed packaging can result in inefficient space utilization during transportation and storage, leading to higher shipping and warehousing costs. Furthermore, packaging that doesn’t adequately protect the steel coils can lead to product damage, resulting in additional costs.
How to Avoid This: Work with packaging experts to design solutions that provide optimal protection for your coils while maximizing space efficiency. Consider using customized packaging solutions that are tailored to the specific dimensions of your coils, ensuring that they are secure during transport. Efficient packaging design can help you reduce storage space, minimize freight costs, and protect your products from damage.
9. Compliance and Regulatory Fines
Many industries have stringent regulations related to packaging, especially when it comes to safety standards. Failure to comply with these regulations can result in fines, legal fees, and reputational damage. Additionally, non-compliant packaging could lead to product recalls, which are both costly and time-consuming.
How to Avoid This: Stay informed about the latest industry regulations and packaging standards. Ensure that your packaging equipment and processes comply with all necessary guidelines, including safety and environmental regulations. It’s also wise to invest in packaging machinery that is designed to meet or exceed these standards, reducing the risk of non-compliance.
10. Failing to Plan for Long-Term Scalability
Many businesses fail to plan for growth when designing their packaging lines. While your current packaging system might meet today’s needs, it could quickly become outdated or inefficient as your business expands. This can lead to expensive upgrades or even the need to completely overhaul your packaging line in the future.
How to Avoid This: When investing in packaging equipment, consider future growth and scalability. Look for machinery that can be easily upgraded or expanded to handle higher volumes or different types of products. Flexible, modular systems can help you avoid the costs associated with having to replace your entire packaging line as your business grows.
Conclusion
Understanding and mitigating the hidden costs in steel coil packaging is essential for maintaining profitability and efficiency in your operations. From energy consumption and labor costs to product damage and compliance fines, these unanticipated expenses can quickly add up if left unaddressed. By investing in modern, automated systems, training your workforce, and proactively planning for scalability, you can avoid these hidden costs and improve the overall efficiency of your packaging process.
In summary, automation, efficiency, and strategic planning are key to reducing these hidden costs and ensuring that your steel coil packaging operation remains cost-effective. Don’t let these unseen expenses erode your profits—take action today to optimize your packaging processes for long-term success.

Get Your Best Solution !