Guide Of Electrical Equipment & Facilities For Coil Packaging Line
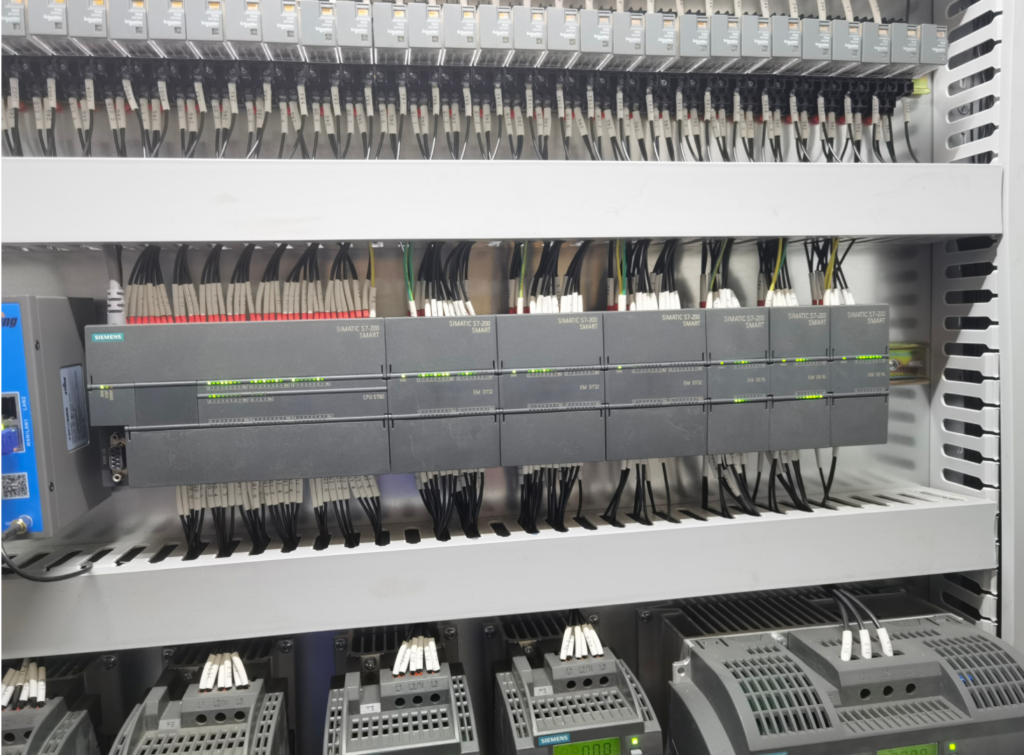
1. Electrical infrastructure
A robust electrical infrastructure is crucial to support an efficient automated packaging line. For hot rolled wide coils, FHOPE implements a customized system integrated throughout the process. At the heart is a climate-controlled motor control center housing programmable logic controllers and variable frequency drives. These interface with AC motors to precisely regulate the speed of conveyors, robotic systems, wrapping units and other key components.
Climate-Controlled Motor Control Center :
At the core of the electrical setup is a climate-controlled motor control center, designed to provide a stable environment for housing critical electrical components. This center serves as the nerve center of the automation system, orchestrating the seamless operation of various machinery and equipment.
Programmable Logic Controllers (PLCs):
The motor control center accommodates programmable logic controllers, sophisticated devices that facilitate the automation of processes by executing predefined logic and sequencing commands. PLCs play a crucial role in coordinating the actions of different components within the packaging line.
Variable Frequency Drives (VFDs) :
Integrated within the motor control center are variable frequency drives, which enable precise control over the speed and torque of AC motors. By adjusting the frequency of the electrical supply, VFDs ensure optimal performance and energy efficiency of motors powering conveyors, robotic systems, wrapping units, and other essential components.
AC Motors :
The system is designed to interface with AC motors, which serve as the workhorses driving key components of the automated packaging line. These motors are responsible for powering conveyors, robotic arms, wrapping units, and other machinery, ensuring smooth and efficient operation throughout the packaging process.
Speed Regulation and Precision Control :
Through the integration of VFDs and PLCs, the system enables precise regulation of motor speeds, allowing for seamless coordination between different components. This precision control enhances the accuracy, efficiency, and consistency of the packaging process for positioning, wrapping, stacking… ultimately leading to improved productivity and quality.
Optimized Performance of Key Components :
The system optimizes the performance of critical components such as conveyors, robotic systems, and wrapping units by providing them with the necessary power and control mechanisms. This ensures that each component operates at its peak efficiency, contributing to the overall success of the automated packaging line.
2. Local push button control
Local push button control stations strategically positioned throughout the packaging line play a crucial role in ensuring safe manual operation during setup and maintenance procedures.
During setup and maintenance tasks, operators often need to make adjustments or conduct tests on specific equipment. The presence of local push button control stations enables them to perform these tasks conveniently without needing to access a centralized control panel, saving time and enhancing operational efficiency.
By providing operators with immediate access to control stations, safety measures are heightened. In case of emergencies or unexpected situations, operators can quickly respond by using the push buttons to stop or alter operations, mitigating potential risks and ensuring the safety of personnel and equipment.
The push buttons allow for precise control over various functions such as conveyor speed, robotic movements, or wrapping processes. Operators can monitor and adjust parameters in real-time, ensuring smooth and accurate operations throughout the packaging line.
3. Local Starter Panel and Festooning Power Track Cable
Local Starter Panel is a compact control panel positioned near specific equipment or machinery within the coil packaging line. It houses essential electrical components like starters, contactors, and safety devices, providing localized control and power distribution.
It efficiently distributes power to the machinery involved in the coil packaging process, ensuring reliable operation. Operators can conveniently control and monitor equipment near the panel, facilitating quick interventions and adjustments. Incorporation of safety devices like emergency stop buttons and overload protection enhances operational safety within the packaging line.
Festooning Power Track cables are flexible systems designed to supply power and control signals to moving equipment in industrial settings. In a coil packaging line, these cables are used to power mobile machinery handling coils along the line.
Festooning Power Track cables enable the seamless movement of machinery carrying coils, ensuring flexibility and efficiency in the packaging process. They deliver electrical power and control signals to mobile equipment, allowing for continuous operation without the constraints of fixed wiring.
Durability and Protection: These cables are constructed to withstand mechanical stress, environmental conditions, and frequent movement, ensuring reliable power distribution for mobile equipment handling coils.
4. Cabling
The installation of 1.1KV grade power and control cables, along with cabling accessories, cable trays, and conduits, is vital for the efficient and safe operation of a coil packaging line. These components collectively contribute to power distribution, control signal transmission, safety, reliability, and ease of maintenance within the industrial setup, ensuring the seamless functioning of the coil packaging machinery.
1.1KV grade cables ensure efficient transmission of power to drive motors, control systems, and other electrical components critical for the operation of the coil packaging machinery. Control cables ensure effective communication between control panels, sensors, and actuators, enabling precise control over the packaging process.
Properly installed cables and accessories, along with cable trays and conduits, enhance the safety and reliability of the electrical infrastructure within the coil packaging line.
Cable trays and conduits facilitate easy access to cables for maintenance and troubleshooting, minimizing downtime and ensuring smooth operations. Cable management will employ effective cable management practices to organize and secure cables, reducing the risk of damage and simplifying maintenance tasks. Label cables and document the cable routing plan for easy identification, troubleshooting, and future modifications.
The cabling of FHOPE packaging line will adhere to,
Selecting the right size and type of cables, along with suitable cable trays and conduits, is crucial for ensuring optimal performance and safety in the coil packaging line.
Adhering to industry standards and regulations for electrical installations is essential to guarantee the safety and reliability of the electrical systems.
Designing the electrical infrastructure with scalability in mind allows for easy integration of additional equipment or upgrades to the coil packaging line in the future.
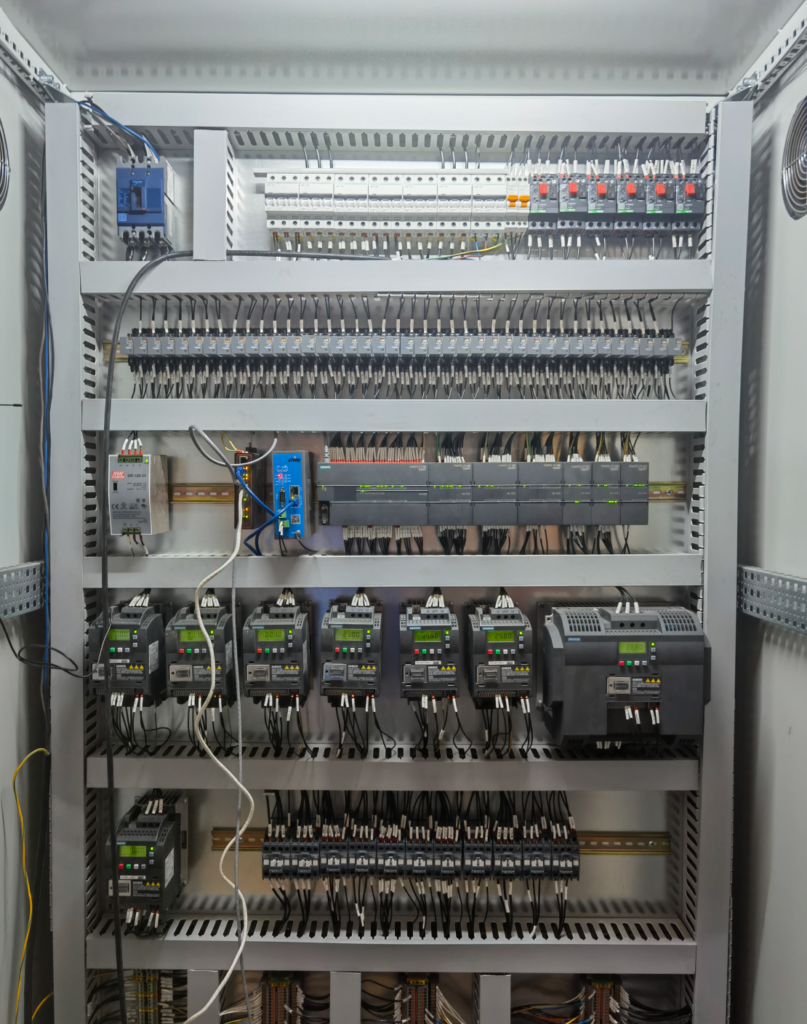
5. Grounding and Lightning Protection System
All components of the packaging line, including turning and stacking equipment, are adequately grounded to mitigate electrical risks. Grounding system provides a path for fault currents to safely dissipate, reducing the risk of electric shocks to personnel and damage to equipment.
Helps prevent damage to electrical equipment by ensuring proper grounding for fault currents. Grounding eliminates static charges that could pose safety hazards during the handling of hot rolled coils.
Correct grounding and lightning protection guards against surges that could disrupt operations. Energy efficient lighting illuminates work areas as needed. Backup batteries facilitate controlled shutdown in any scenario.
Safeguards the entire packaging line, including the turning, wrapping, strapping, stacking, and weighing equipment from lightning strikes. Minimizes the risk of damage to sensitive electronic components and machinery caused by lightning-induced power surges. Ensures a low-resistance path for lightning currents to dissipate safely into the ground.
6. Erection and Installation Materials
In a hot rolled coil packaging line, the erection and installation of electrical components such as cable glands, lugs, tags, termination kits, cable trays, and conduits are crucial for establishing a safe and efficient electrical infrastructure. These components play a vital role in ensuring the proper functioning of the electrical system within the packaging line.
Cable Glands will provide secure cable entry points, ensuring the cables are properly terminated and sealed to prevent dust and moisture ingress. Lugs can connect electrical cables to equipment or other cables securely, maintaining a reliable electrical connection.
Tags are used for cable identification and labeling, aiding in maintenance and troubleshooting tasks. Termination kits contain components necessary for terminating cables, such as connectors, insulators, and sealing materials for reliable connections.
Ensure that the cable glands, lugs, tags, termination kits, cable trays, and conduits are compatible with the specific requirements and types of cables used in the hot rolled coil packaging line.
7. Battery limit
Creating an electrical building within the battery limit of a hot rolled coil packaging line involves intricate planning and meticulous execution to ensure a safe and efficient electrical infrastructure.
Cable engineering with proper cable routing is crucial for the seamless operation of the packaging line. The design and construction of the electrical building within the battery limit of the hot rolled coil packaging line must adhere to stringent safety standards and regulations to safeguard personnel and equipment.
The coil packaging line layout of the electrical building should be optimized to efficiently accommodate the necessary equipment, machinery, and electrical components within the designated battery limit.
Essential emergency systems, such as fire alarms, emergency lighting, and backup power sources, should be incorporated to ensure uninterrupted operation during emergencies.
The cable routing design should accommodate current electrical loads and allow for future expansion within the battery limit of the packaging line.
Detailed documentation of the cable engineering design of the packaging line, installation, and maintenance activities should be maintained for future reference and operational requirements.
By implementing a well-planned approach to the design of the electrical building and cable engineering with proper routing within the battery limit of the hot rolled coil packaging line, a robust and efficient electrical infrastructure can be established to support the operational needs of the facility while upholding safety standards and compliance.