Guide for Customized Solution for Mold Flipper
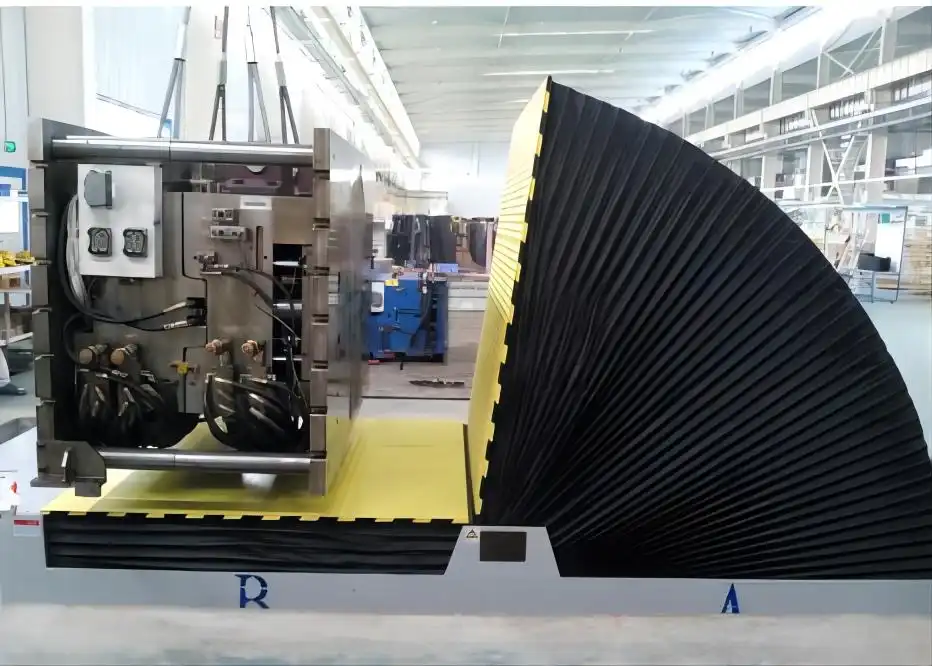
Problem Facing for Mold Using and Production
In many industries, handling molds presents a range of challenges during production, maintenance, and repair. One of the most common problems is the sheer weight of the molds, which can range from a few tons to over 100 tons. This makes manual handling impractical and time-consuming. Cranes or forklifts, often used to move molds, are slow and pose a significant safety risk. The lifting process can be dangerous, with potential hazards for workers if the mold slips or tips unexpectedly. Additionally, the molds require regular maintenance, repair, and cleaning, which further complicates their handling. Improper handling not only increases the risk of accidents but also leads to production delays. These issues create the need for a more efficient and safer solution for flipping and positioning molds in an industrial setting.
The Function of a Mold Flipper
A mold flipper is a specially designed machine that addresses the challenges associated with heavy mold handling. Its primary function is to flip molds by 90 or 180 degrees, depending on the production needs. This flipping mechanism allows for easy access to the mold for cleaning, maintenance, or repair, without the need for cranes or forklifts.
Mold flippers are engineered to handle heavy loads safely, reducing the risk of accidents in the workplace. With the ability to automate the flipping process, these machines offer faster handling times, improving production efficiency. Their precision design ensures that molds are handled with care, preventing damage during the flipping process, which is especially important in industries where molds are expensive and delicate.
1. Hydraulic Driving Mold Flipper
The hydraulic driving mold flipper is designed for heavy-duty applications, capable of handling molds weighing between 1 to 100 tons. Powered by a robust hydraulic system, this mold flipper provides smooth and controlled flipping, allowing for precise 90 or 180-degree rotations. The hydraulic system ensures that the flipper can handle the heaviest molds with ease, while also offering flexibility in terms of the speed and angle of rotation.
The machine is ideal for use in environments where large molds need to be flipped frequently for maintenance, repair, or cleaning. Its strong hydraulic power reduces manual labor and increases the safety of the mold handling process. Additionally, the hydraulic driving system is durable and requires minimal maintenance, making it a reliable option for long-term use in industrial settings.
2. Mechanical Driving Mold Flipper
The mechanical driving mold flipper is a cost-effective and reliable solution for handling molds that weigh between 1 to 80 tons. This type of flipper operates through a mechanical system that ensures steady and controlled flipping. Its simplicity makes it easy to maintain, offering lower operational costs over time.
The mechanical flipper is known for its durability and efficiency, providing an excellent option for companies seeking a robust solution for mold handling. The design is user-friendly and requires minimal training for operators, making it an accessible and practical solution for many production environments.
3. Working Table Size Customized Solution
Mold flippers can be customized to suit the specific dimensions of the molds being handled. The working table sizes range from 1000x1000mm to 3000x3000mm, ensuring that molds of various shapes and sizes can be safely flipped and manipulated. For molds with irregular or complex shapes, special working tables can be equipped with clamping devices that secure the mold during the flipping process.
These customized solutions ensure that the mold remains stable and secure throughout the operation, preventing damage and ensuring safety. The customization options allow industries to optimize their mold handling processes, improving efficiency and reducing the risk of accidents during mold maintenance or production.
4. Mold Opening Machine
A mold opening machine is an essential tool for efficiently separating molds after production. This machine is designed to open heavy molds quickly and safely, reducing the time and effort required in manual opening processes. The mold opening machine can be customized to fit different mold sizes and shapes, ensuring precise alignment during the opening procedure.
With hydraulic or mechanical systems in place, the machine ensures that the mold halves are separated smoothly, preventing damage to the mold or the product inside. By integrating this machine into the production line, companies can significantly improve productivity and reduce the labor required for mold handling, ensuring a safer and more efficient workflow.
5. Safety System
Safety is a top priority in the design and operation of mold flippers. Advanced safety systems are integrated to protect both workers and equipment. A light beam system can be installed to detect any interference in the operating area, immediately stopping the machine if an object or person enters the danger zone.
Additionally, interlock systems ensure that the machine cannot operate unless all safety conditions are met, preventing accidental operation. These safety features help to minimize the risk of accidents, ensuring a secure environment for operators working with heavy molds. With these systems in place, mold flipping can be done safely, efficiently, and with minimal risk.
SHOWCASE
1. MOLD Side 2000x2000mm 20T, USA, for Aircraft (Seattle)
In Seattle, USA, a customer in the aerospace industry faced significant challenges with handling a large 2000x2000mm, 20-ton mold for aircraft production. The mold was not only heavy but also posed safety risks during the manual opening and handling processes. Using cranes and forklifts for mold manipulation was slow, inefficient, and introduced potential hazards to workers. The customer sought a solution that would improve safety and speed up their operations.
To address this issue, we designed and implemented a hydraulic mold flipper equipped with two robust working tables and two hydraulic cylinders for each side. This configuration allowed for controlled and efficient flipping of the mold, significantly reducing the handling time. The dual-cylinder design provided smooth operation and enhanced safety during mold opening and flipping. After implementation, the customer was extremely satisfied with the solution. It not only improved safety by minimizing manual intervention but also increased operational efficiency, ensuring that molds could be flipped and handled quickly and safely in their production line.
2. Mold with Irregular Shape and Prominent Part
An Thailand customer at Bangkok, Pathum Thani, approached us with a unique challenge: handling a large mold with an irregular shape and prominent parts that made traditional flipping methods unsuitable. The surface of the mold was not square, which required a customized solution for flipping and handling. Additionally, the customer needed the mold to be easily loaded into a container for transport, making it essential that the flipper’s design accommodated this requirement.
Our solution involved the design of a 2400x2500mm working table with reinforced structural components that could be dismantled for easier transport. This customized table included two strategically placed holes to accommodate the prominent parts of the mold, ensuring that the mold could be flipped without damaging its surface.
The reinforced structure provided the stability needed to handle the mold’s weight and size, while the dismantling feature allowed the flipper to be broken down and easily loaded into containers. This tailored solution met the customer’s needs perfectly, enabling safe, efficient handling of the irregular mold while ensuring the equipment could be transported without difficulty.
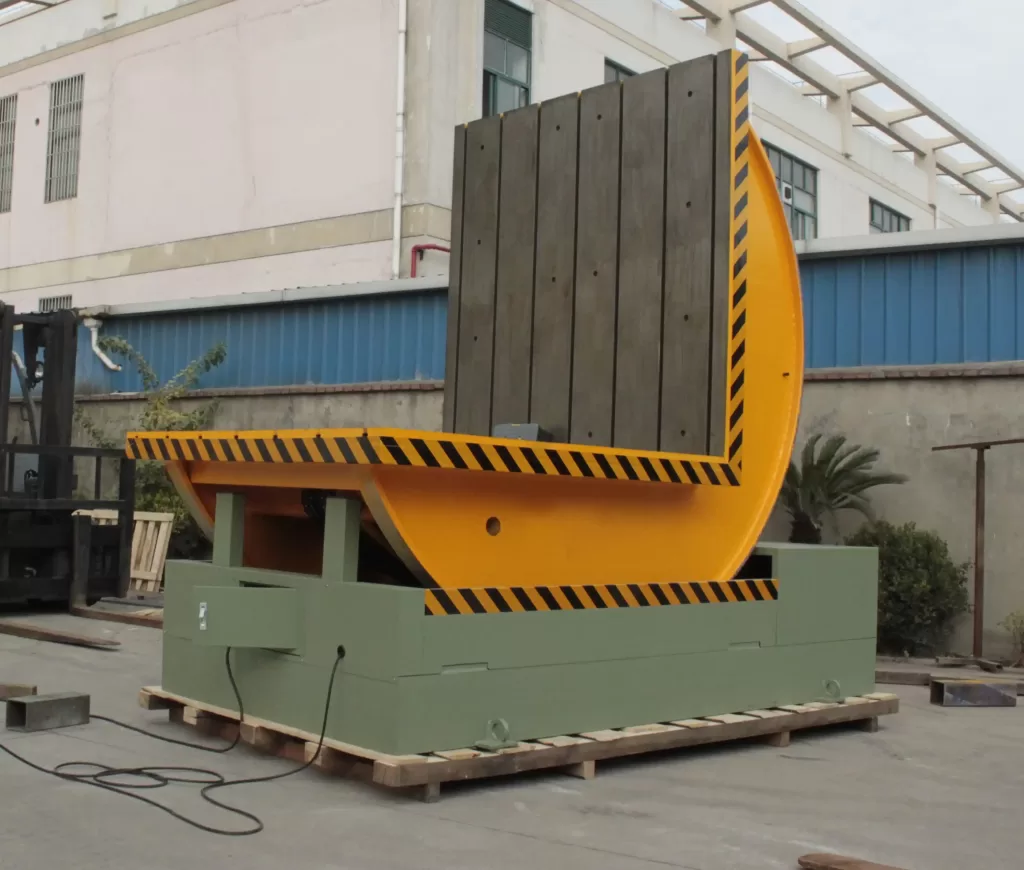