Guide for Automatic Coil Stacking Solution in the Packing Line.
When it comes to coil stacking, selecting the right method is crucial for ensuring efficiency, safety, and product integrity in your production process. Each stacking method—whether it be mechanical systems, magnet lifters, vacuum lifters, or robotic systems—offers unique advantages tailored to specific needs and coil types. Mechanical systems are ideal for handling heavy coils with robust stability, while magnet lifters provide a secure, non-contact grip for steel coils. Vacuum lifters excel in gently handling light, delicate materials like copper and aluminum, and robotic systems offer a highly automated, adaptable solution, perfect for light coils requiring precision and flexibility. Understanding the characteristics and limitations of each stacking method is key to optimizing your coil handling operations and achieving seamless integration within your facility.
There are following 4 main types coil stacking solution.
1. Mechanical Type
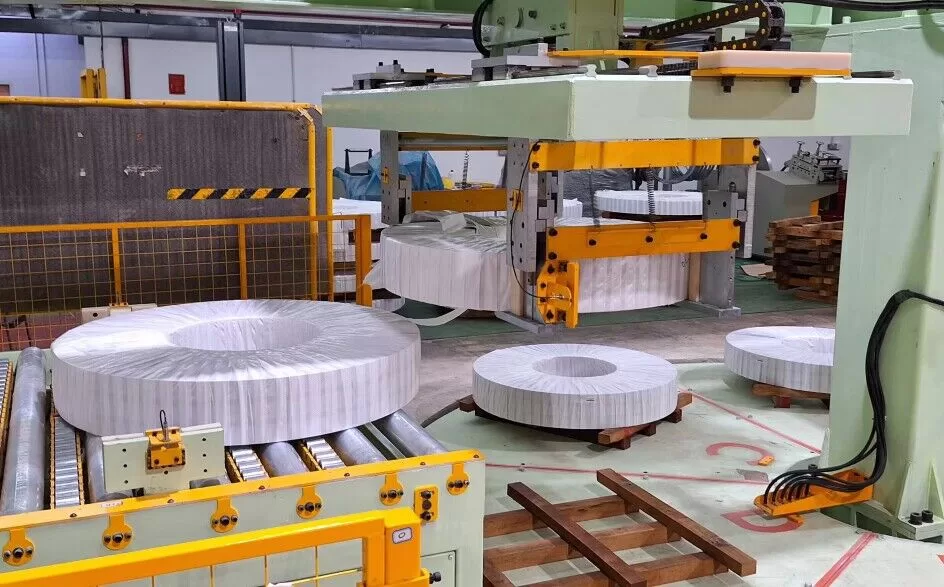
The mechanical type is the most widely used coil stacking method in packing lines, known for its robust handling and versatility. This system employs fork arms that securely hold and lift the coils from the bottom, ensuring exceptional stability during handling and stacking. The fork arms are mounted on a hydraulic lifter that allows precise up-and-down movement, facilitating smooth stacking operations. Additionally, the system is designed with a center expanding holder that grips the coil from the inside diameter, which is particularly useful for lighter coils, enabling stacking without the use of timber spacers. For moving coils between different stations, a crane system is often integrated into the design, enhancing the system’s capability to handle coils of varying sizes and weights. This mechanical stacking system can manage coils weighing up to 10 tons and is widely recognized for its safety, reliability, and adaptability across various industrial applications.
Advantages:
A. Heavy Loading up to 10 Tons: The mechanical stacking system is capable of handling heavy coils, making it suitable for industrial settings where large, bulky coils are common.、
B. Safety: The use of hydraulic lifters and crane integration ensures safe handling of coils, minimizing the risk of accidents during stacking operations. The secure grip from the fork arms and center expanding holder further enhances safety by preventing coil movement during stacking.
C. Easy Maintenance: The mechanical nature of the system allows for straightforward maintenance. Hydraulic lifters and fork arms are designed for durability, and regular servicing is relatively simple, ensuring long-term operational efficiency with minimal downtime.
Disadvantages:
A. Timber Spacer Required Between Coils: While the mechanical system is effective for stacking, it often requires the use of timber spacers between coils to prevent direct contact and potential damage. This adds an extra step to the stacking process and may increase material costs.
B. Fork Arm Thickness: The thickness of the fork arms is directly related to the maximum weight they can support. For extremely heavy coils, thicker fork arms are necessary, which might limit the ability to fit between closely spaced coils or accommodate smaller coil sizes. This limitation can pose challenges when stacking a wide range of coil sizes and weights.
2. Magnet Lifter

Magnet lifters use electric magnet suckers to handle coils, offering a secure grip without direct physical contact. This system is designed with a safety system that ensures the magnets remain engaged even in the event of a power failure, providing reliable power shutdown protection. This feature is crucial for safely handling heavy steel coils, especially in scenarios where unexpected power outages could pose a risk. The structure of the system typically consists of a crane equipped with a magnet sucker, allowing for versatile coil movement and stacking.
The magnet lifters provide consistent holding pressure and clamping force, ensuring that the coil is held securely throughout the handling process without variation in tightness. This guarantees a firm grip on the workpiece, reducing the risk of accidents and coil slippage. Magnet lifters can manage steel coils weighing up to 20 tons and offer the flexibility to stack coils both with or without the use of timber spacers. Additionally, the system minimizes the risk of magnetizing the coil, with efficient demagnetization protocols in place to maintain the coil’s quality and integrity throughout the process.
Advantages:
D. One Fit for All Size Coils and Heavy Loading: Magnet lifters are highly versatile, capable of handling a wide range of coil sizes and shapes, including extremely heavy loads up to 20 tons. This adaptability makes them an excellent choice for facilities that deal with varying coil dimensions.
E. Safety: The system’s design includes power shutdown protection, ensuring that the magnetic hold is maintained even during power outages. This safety feature prevents accidental coil drops, enhancing workplace safety, especially when handling large and heavy coils.
F. Easy Maintenance: Magnet lifters have relatively simple mechanical structures, requiring minimal maintenance. Routine checks on the electrical components and the crane system are sufficient to keep the lifter operational, ensuring consistent performance with minimal downtime.
G. Works for Stacking With or Without Timber: Unlike some mechanical stacking methods, magnet lifters can stack coils either with or without timber spacers. This flexibility allows for more efficient use of storage space and eliminates the need for additional materials in certain stacking configurations.
Disadvantages:
A. Limited to Steel Coils: Magnet lifters are suitable only for handling magnetic materials like steel coils. They are not effective for non-magnetic materials such as stainless steel, copper coils, or other non-ferrous metals, limiting their applicability in facilities handling a diverse range of coil types.
B. Potential Magnetization of Steel Coils: While magnet lifters minimize the risk of magnetizing the coils, some degree of magnetization can still occur. This may necessitate demagnetization processes for certain customers, especially those with stringent requirements for coil processing or applications where residual magnetism could be problematic.
3. Vacuum Lifter

Vacuum lifters are highly effective for handling light coils, especially those made from delicate materials like copper or aluminum, with a maximum load capacity of up to 1000 kg. These lifters rely on the principle of vacuum suction, which requires the coil surfaces to be smooth and clean to ensure a secure grip. Vacuum technology offers a gentle handling approach, significantly reducing the risk of damaging sensitive or delicate materials. This method is particularly advantageous for maintaining the aesthetic quality and structural integrity of coils, making it a preferred choice in industries where surface appearance and precision are critical.
Vacuum lifters come equipped with several safety and functional features to ensure optimal performance and operator safety. These include a vacuum leakage sensor and warning system, which continuously monitors the vacuum level and alerts operators to any loss of suction. This early warning system is crucial for preventing accidental drops or mishandling of coils. Additionally, the lifters feature an attach/release slide valve with a safety lock that controls the attachment and release of the coil, preventing unintentional detachment during handling. The lifter’s design also includes locking hand knobs on the adjustable vacuum pad, slide assemblies, and crossarms, allowing for precise adjustments to fit various coil sizes and shapes securely.
Advantages:
H. Good for Light Coil Handling: Vacuum lifters are ideally suited for handling light coils, especially those made from non-ferrous materials like copper and aluminum. Their gentle handling minimizes the risk of scratches, dents, or surface imperfections, making them an excellent choice for applications where maintaining the coil’s aesthetic and structural integrity is important.
I. Works for Stacking With or Without Timber: These lifters offer flexibility in stacking operations. Coils can be stacked directly on top of each other or with timber spacers, depending on the storage requirements. This versatility makes vacuum lifters a valuable asset in various production and storage environments where different stacking methods are employed.
Disadvantages:
A. Not for Heavy Loading: Vacuum lifters are not suitable for handling heavy coils, as their maximum load capacity is limited to around 1000 kg. This limitation makes them less appropriate for industries dealing with large, heavy coils, where more robust lifting solutions like mechanical or magnetic lifters are required.
B. Coil Surface Must Be Smooth and Clean: For vacuum lifters to function effectively, the coil surface must be smooth, neat, and free of contaminants. Rough or uneven surfaces can compromise the vacuum grip, increasing the risk of slippage during handling. Therefore, vacuum lifters are less suitable for coils with irregular or textured surfaces.
In summary, vacuum lifters offer a precise and gentle solution for handling light, delicate coils, ensuring minimal risk of damage and maintaining the quality of sensitive surfaces. With built-in safety features like vacuum leakage sensors and adjustable vacuum pads, these lifters provide a secure and flexible handling method. However, their use is limited to lighter loads and smooth-surfaced coils, making them less versatile in applications involving heavy or rough-textured materials.
4. Robot

Robotic systems provide a cutting-edge and automated approach to coil stacking, particularly effective for light coils weighing up to 1 ton. These systems utilize advanced robotics technology, equipped with specialized work fixtures explicitly designed for coil handling, ensuring a high degree of efficiency, accuracy, and precision in stacking operations. The robots can be programmed to perform a variety of tasks, making them a highly adaptable solution for facilities looking to increase automation and minimize labor-intensive processes.
The integration of a PC-supported control system via Ethernet allows seamless communication with the robot controller, enabling real-time adjustments, monitoring, and programming of complex stacking operations. This not only optimizes performance but also provides a flexible interface for configuring the robot to handle different coil sizes and stacking patterns as production needs evolve.
The robotic system enhances safety by reducing human involvement in potentially hazardous tasks. It operates within a predefined workspace, minimizing the risk of accidents associated with manual coil handling. The system can work continuously without fatigue, ensuring consistent stacking quality and productivity. Furthermore, the use of robots significantly reduces the likelihood of damage to the coils during handling, as the precise movements and controlled grip prevent unnecessary contact and force application.
Advantages:
J. 360-Degree Handling: Robotic systems offer complete 360-degree handling capability, allowing for versatile and precise coil manipulation from any angle. This flexibility is particularly useful in complex stacking operations, where coils may need to be rotated, tilted, or positioned at specific angles for optimal storage or subsequent processing.
K. Stacking Fixture Changeable: The robot’s stacking fixture can be easily changed to suit different handling requirements, including forkarms, magnet attachments, or vacuum pads. This adaptability allows the robotic system to handle various types of coils and packaging scenarios, from stacking with timber spacers to direct placement on pallets, making it a versatile tool for diverse industrial applications.
Disadvantages:
C. Suitable for Light Coil Handling: While robotic systems excel at handling light coils, they may not be suitable for heavier loads, particularly those exceeding 1 ton. This limitation restricts their application in industries dealing with large, heavy-duty coils, where more robust handling solutions are required.
Professional Maintenance: Robotic systems require professional maintenance and technical support to ensure optimal performance. Regular servicing by skilled technicians is necessary to address mechanical wear, software updates, and system calibration. This dependency on specialized service can result in higher maintenance costs and the need for ongoing training for in-house personnel.