Understanding Full-Automatic Vertical Pallet Wrapping Machines
Full-automatic vertical pallet wrapping machines are essential equipment in modern logistics and manufacturing, designed to enhance packaging efficiency, ensure load stability, and reduce operational costs. Understanding their features, operation, and maintenance is crucial for maximizing productivity and workplace safety. This guide provides insights into these sophisticated packaging systems.
Core Operation and Workflow
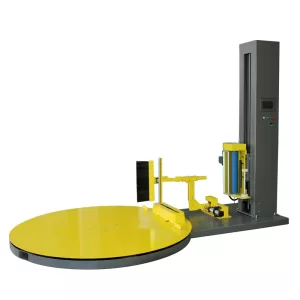
Automated vertical pallet wrappers typically operate with minimal human intervention. Once a palletized load is placed onto the turntable (often via conveyor or forklift), the machine automatically initiates the wrapping cycle. This involves:
- Load Positioning: The load is centered on the turntable. Features like Forklift Stops can assist operators in precise alignment.
- Film Attachment: The machine automatically attaches the stretch film to the base of the load.
- Wrapping Cycle: The turntable rotates while the Film Delivery System (FDS) moves vertically along a mast, applying film according to pre-set parameters (e.g., bottom wraps, top wraps, wrapping tension).
- Film Cutting and Sealing: Upon cycle completion, the film is automatically cut and often sealed to the load.
- Load Exit: The wrapped pallet is ready for removal, often integrated with outbound conveyor systems.
Key Features and Common Options
Modern pallet wrappers come with various standard features and optional upgrades to tailor performance to specific needs:
- Film Delivery System (FDS): This core electrical/mechanical assembly dispenses and stretches the film before applying it to the load. Advanced systems (G Force Plus FDS or similar) often use electric brakes or powered rollers for precise film tension control, maximizing film yield and load containment. The FDS assembly is mounted on the FDS Carrier, which moves vertically.
- Wrapping Parameter Customization:
- Bottom Wraps: Sets the number of initial wraps applied to the pallet base (typically 1-9), crucial for securing the load to the pallet.
- Top Wraps: Similar setting for the top of the load.
- Banding: Allows applying a concentrated number of wraps (1-9) to specific sections of the load for reinforcement.
- Automation Enhancements:
- Auto Film Cut-off: Automatically cuts the film at the end of the cycle, eliminating manual intervention and speeding up the process.
- Load Positioning Aids:
- Forklift Stop: A physical guide attached to the turntable skirt (often adjustable to 3 positions using pins) to help forklift operators accurately place pallets onto the machine. Installation typically involves inserting pins into skirt holes and potentially anchoring to the floor.
- Safety Features:
- Emergency Stop (E-stop): A prominent red button that, when pressed, immediately and safely halts all machine operations in an emergency.
- Safety Circuits: Integrated systems designed to protect personnel, often requiring an Initialize sequence to reset circuits and confirm components are in their safe start positions before operation can begin.
Importance of Proper Installation and Operation
Correct installation according to manufacturer guidelines is paramount for safe and efficient operation. Operator instructions detail the proper use of machine controls, loading/unloading procedures, and adherence to safety protocols. A well-understood operation minimizes errors, reduces downtime, and prevents accidents.
Maintenance and Troubleshooting
Regular maintenance ensures the pallet wrapper remains in top operating condition, preventing unexpected breakdowns and extending its service life. This includes routine checks, lubrication, and part inspections as outlined in the equipment manual. Troubleshooting guides help diagnose and resolve common issues quickly, minimizing disruptions to the packaging line.
Understanding the specific Specifications and Options of your machine is vital during installation, operation, and maintenance phases. Likewise, thorough knowledge of the Safety precautions (Warnings, Cautions, Notes) ensures a secure working environment for all personnel. Resources like Parts Lists and Drawings are invaluable for identifying and ordering replacement components.