Understanding Full-Automatic Tyre Wrapping Machines for Enhanced Packaging Efficiency
In the demanding environment of tire manufacturing and distribution, efficient and protective packaging is paramount. Handling diverse tire sizes while ensuring product integrity during transit and storage presents significant logistical challenges. Full-automatic tyre wrapping machines offer a robust solution, streamlining the packaging process through automation.
The Challenge of Modern Tire Packaging
Tires, ranging from small bicycle types to large passenger car or truck tires, require secure packaging to prevent damage and maintain cleanliness. Manual or semi-automatic methods can be labor-intensive, inconsistent, and struggle to keep pace with high-volume production lines. Key challenges include:

- Ensuring consistent wrap tension and coverage for adequate protection.
- Handling a wide variety of tire diameters and widths efficiently.
- Minimizing packaging material waste.
- Reducing manual handling risks and associated labor costs.
- Integrating packaging seamlessly into the overall production flow.
Introducing Full-Automatic Tyre Wrapping Systems
Full-automatic tyre wrapping systems are designed to address these challenges by automating the entire wrapping process with minimal operator intervention. These machines typically utilize stretch film to encase tires securely, offering protection against dust, moisture, and abrasions.
How Automated Tyre Wrapping Works: A Step-by-Step Overview
While specific designs may vary, the core operation of a full-automatic tyre wrapping machine generally follows these steps:
1. Tire Loading and Positioning
Tires are fed into the machine, often via conveyors. Sensors detect the tire's presence and dimensions, automatically positioning it within the wrapping station, frequently using locating wheels or similar mechanisms.
2. The Automated Wrapping Cycle
Once the tire is correctly positioned, the wrapping cycle begins. A rotating ring or arm dispenses stretch film, wrapping it around the tire's circumference and often through its center bore for complete coverage. The machine controls film tension and overlap for optimal security and material usage. Operators typically select pre-set parameters or speed settings via a control interface before initiating the automatic process.
3. Automatic Adjustments and Sizing
A key feature is the system's ability to adapt. The wrapping mechanism (often referred to as a flywheel or rotating ring) automatically adjusts its clearance or position based on the detected tire size. This ensures proper film application regardless of whether it's handling bicycle, motorcycle, or passenger car tires sequentially.
4. Unloading the Wrapped Tire
After the cycle completes, the film is automatically cut and secured. The wrapped tire is then discharged from the machine, typically onto an exit conveyor, ready for palletizing or shipping. The system resets for the next tire.
Key Features and Technological Aspects
Modern automated tire wrappers incorporate several features to enhance performance and usability:
- Versatility Across Tire Types: Engineered to handle a broad spectrum of tire sizes and weights, accommodating products from bicycle and motorcycle tires up to passenger car and sometimes light truck tires.
- Advanced Automation and Control: PLC-based control systems with touchscreen interfaces allow for easy operation, parameter adjustments (wrap counts, tension, speed), and diagnostics. Fully automatic processing minimizes the need for manual input once the cycle starts.
- Efficient Packaging Material Management: Precise tension control and optimized wrapping patterns reduce stretch film consumption. Many designs feature easy-to-load film carriages and simplified tension adjustment mechanisms, minimizing downtime during roll changes. The structure is often designed to save time during replacement without needing part changes.
- Operator Safety Considerations: Machines are equipped with safety guards, emergency stop buttons, and sensors to protect operators during operation, adhering to relevant industrial safety standards like those outlined by organizations such as the Packaging Machinery Manufacturers Institute (PMMI).
Operational Benefits of Automated Tyre Wrapping
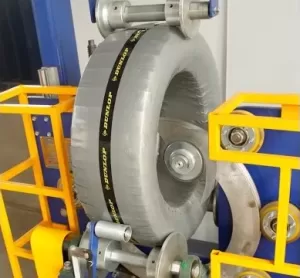
Implementing full-automatic tyre wrapping machines can yield significant operational advantages:
- Improved Packaging Consistency: Automated control ensures every tire is wrapped to the same standard, enhancing product protection and appearance.
- Increased Throughput: Significantly faster than manual methods, these machines can keep pace with high-speed production lines, reducing bottlenecks.
- Reduced Labor Requirements: Automation minimizes the need for manual labor in the packaging stage, freeing up personnel for other tasks and lowering operational costs.
- Enhanced Product Protection: Secure stretch film wrapping protects tires from environmental factors and handling damage throughout the supply chain.
- Optimized Material Usage: Precise control over film application leads to less waste compared to manual wrapping.
Conclusion: Streamlining Tire Logistics with Automation
Full-automatic tyre wrapping machines represent a critical technology for optimizing packaging operations within the tire industry. By providing consistent, efficient, and protective wrapping for a diverse range of tire types, these systems help manufacturers and distributors improve throughput, reduce costs, and ensure their products reach customers in excellent condition. As automation continues to reshape manufacturing, automated tire wrapping stands out as a valuable investment for enhancing competitiveness.
For related automated wrapping solutions, see this Full-automatic Tyre Wrapping Machine.