Enhancing Steel Coil Integrity with Automated Wrapping Systems
Protecting steel coils during handling, storage, and transit is critical in the metals industry. Bare or improperly packaged coils are susceptible to costly damage from moisture, contaminants, and physical impacts. Automated coil wrapping systems provide a robust solution, ensuring consistent and effective protection while optimizing packaging line efficiency.
The Importance of Effective Coil Packaging
Steel coils, whether hot-rolled, cold-rolled, galvanized, or coated, represent significant value. Without adequate protection, they face numerous risks:
- Corrosion: Exposure to humidity and moisture can quickly lead to rust, degrading the steel's quality and appearance.
- Surface Damage: Scratches, dents, and edge damage can occur during handling and transportation if the coil is not properly secured and cushioned.
- Contamination: Dust, dirt, and other environmental contaminants can mar the surface or interfere with subsequent processing.
Effective packaging, particularly using automated systems, mitigates these risks, preserving the coil's value and ensuring it meets end-user specifications.
Understanding Automated Steel Coil Wrapping Technology
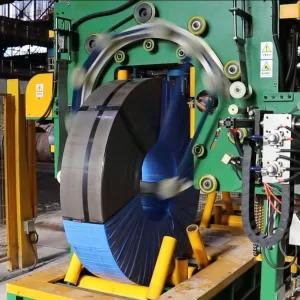
Modern coil wrapping machines are sophisticated systems designed to apply protective materials efficiently and consistently around the circumference and through the eye of the coil. Key components and capabilities often include:
- Through-the-Eye Wrapping: The core function, where wrapping material (like stretch film or paper) is passed through the coil's inner diameter and around the outer diameter, ensuring full coverage.
- Material Dispensing: Systems precisely control the application of various materials:
- Stretch Film: Provides a tight, moisture-resistant barrier and load stability.
- Paper/Cardboard/Hardboard: Offers puncture resistance and can incorporate VCI (Volatile Corrosion Inhibitors) for enhanced rust prevention.
- Combination Wraps: Applying multiple layers (e.g., VCI paper followed by stretch film) for comprehensive protection.
- Peripheral Integration: Wrapping is often part of a larger packaging line incorporating:
- Conveying Systems: Automating coil movement to and from the wrapping station.
- Edge Protection: Automatic application of edge protectors (cardboard, plastic, or metal) to prevent handling damage.
- Palletizing/Skidding: Placing coils onto appropriate bases for transport.
- Strapping: Circumferential or through-eye strapping to further secure the coil and packaging.
- Weighing Systems: Integrated scales for accurate weight documentation.
- Marking and Labeling: Automated application of labels with essential product information, tracking codes, or handling instructions.
- Robotics: Utilized for tasks like label application, pallet handling, or complex manipulation.
- Automation and Control: Advanced systems feature programmable logic controllers (PLCs), human-machine interfaces (HMIs) for operation and visualization, and connectivity to plant-level manufacturing control systems (MES/ERP) for seamless integration into production workflows. Remote diagnostics and support capabilities are also increasingly common.
Key Benefits of Automated Coil Wrapping
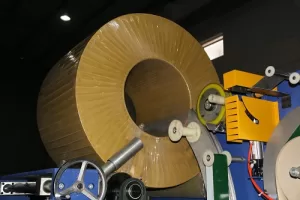
Transitioning from manual or semi-automatic methods to a full-automatic steel coil wrapping machine offers significant advantages:
- Consistency and Quality: Automation ensures repeatable wrap tension, overlap, and material placement, providing uniform protection for every coil, superior to manual application variability.
- Increased Throughput: Automated systems operate significantly faster than manual methods, reducing bottlenecks and increasing overall packaging line capacity.
- Enhanced Coil Protection: Precise material application, including options for multi-layer wrapping and VCI integration, offers superior defense against environmental factors and handling stresses.
- Improved Worker Safety: Reduces the need for manual handling of heavy coils and wrapping materials, minimizing risks of strains, sprains, and other injuries.
- Reduced Material Waste: Optimized control over material stretch (for film) and application minimizes waste compared to manual wrapping.
- Labor Optimization: Frees up personnel from repetitive wrapping tasks to focus on higher-value activities within the plant.
Selecting the Right Automated System
Choosing an appropriate automated wrapping system requires careful consideration of several factors:
- Coil Specifications: Minimum/maximum inner and outer diameters, width, and weight are primary inputs.
- Required Throughput: The number of coils per hour or shift the system must handle.
- Packaging Materials: The specific types of wrapping materials required (stretch film, VCI paper, barrier films, etc.).
- Level of Automation: Degree of integration needed with upstream and downstream equipment (conveyors, strapping, labeling).
- Operating Environment: Space constraints, environmental conditions (temperature, humidity).
- Control System Requirements: Need for integration with existing plant networks and data systems.
- Supplier Expertise and Support: Availability of technical support, spare parts, and maintenance services.
Conclusion
Automated steel coil wrapping systems are indispensable tools for modern steel producers and processors. By providing consistent, high-quality protection against environmental hazards and handling damage, these systems safeguard product value, enhance operational efficiency, and improve workplace safety. Investing in the right automated solution, tailored to specific operational needs, is a critical step in maintaining competitiveness and ensuring customer satisfaction in the demanding steel market.