How Full-Automatic Copper Coil Wrapping Lines Enhance Operational Safety in Factories
In modern manufacturing environments, particularly those handling heavy materials like copper coils, operational safety is non-negotiable. Automating processes like packaging is a key strategy to mitigate risks. Full-automatic copper coil wrapping lines offer significant advantages beyond just efficiency; they are instrumental in creating safer workplaces. Let's delve into how these automated systems contribute to enhanced factory safety.
The Critical Need for Safety in Copper Coil Handling

Copper coils, often heavy and potentially having sharp edges, present inherent risks during manual handling and packaging. Common hazards include:
- Musculoskeletal Injuries: Lifting, pushing, or pulling heavy coils can lead to strains, sprains, and long-term back problems.
- Cuts and Abrasions: Manual handling increases the risk of contact with sharp coil edges or strapping materials.
- Product Damage: Improper handling can damage coils, potentially creating unstable loads or unsafe conditions.
Prioritizing safety protocols and leveraging technology like automated coil wrapping systems is essential to protect personnel and maintain smooth operations.
How Automation Directly Reduces Manual Handling Risks
The most immediate safety benefit of full-automatic wrapping lines is the drastic reduction in manual intervention.
- Eliminating Heavy Lifting: Automation takes over the strenuous tasks of moving, positioning, and wrapping heavy copper coils, significantly reducing the ergonomic risks associated with manual labor.
- Minimizing Repetitive Strain: Automated cycles replace repetitive manual wrapping motions, lowering the incidence of repetitive strain injuries (RSIs) among workers.
- Reducing Operator Fatigue: By automating demanding tasks, operators experience less physical fatigue, which helps maintain alertness and reduces the likelihood of errors that could lead to accidents.
Built-in Machine Safety Features
Modern automatic copper coil wrapping lines are engineered with safety as a core design principle, incorporating multiple protective features:
- Physical Guarding and Barriers: Robust enclosures and safety fences restrict access to moving parts during operation, preventing accidental contact.
- Safety Interlocks: Doors and access points are often equipped with interlocks that automatically halt machine operation if opened, ensuring maintenance or adjustments are performed safely.
- Emergency Stops: Clearly marked and easily accessible emergency stop buttons allow operators to quickly halt the machine in case of an unforeseen issue.
- Compliance with Standards: Reputable systems are designed to meet or exceed relevant safety regulations and standards (e.g., OSHA requirements in the U.S. or CE marking in Europe), ensuring a baseline level of safety is built-in. For more information on general machine safety, consult resources like the Occupational Safety and Health Administration (OSHA).
Precision, Monitoring, and Error Prevention
Automation enhances safety through consistency and advanced monitoring capabilities:

- Consistent Wrapping Quality: Automated systems apply wrapping materials with consistent tension and overlap, creating secure, stable packages less prone to shifting or collapsing during subsequent handling or transport.
- Real-Time Process Monitoring: Sensors (e.g., photoelectric, proximity) monitor coil presence, material feed, and machine status. Deviations from normal parameters can trigger alerts or automatic shutdowns, preventing potential hazards before they escalate.
- Reduced Human Error: User-friendly HMIs (Human-Machine Interfaces) simplify operation. Automation eliminates variability inherent in manual processes, reducing the chance of errors caused by fatigue, inattention, or lack of training.
- Data Logging and Diagnostics: Many systems log operational data, which aids in troubleshooting and identifying potential issues (predictive maintenance), minimizing unexpected downtime and the associated pressures that can compromise safety.
Streamlining Operations for Indirect Safety Gains
Beyond direct hazard reduction, automation contributes to a safer environment indirectly:
- Optimized Workflow: Efficient automated lines often lead to smoother overall production flow, reducing congestion and hurried movements in the packaging area.
- Focus on Oversight: Operators shift from performing physically demanding tasks to overseeing the automated process, allowing them to focus more on safety checks and overall situational awareness.
- Energy Efficiency: Modern designs often incorporate energy-efficient components, which can lead to a quieter and cooler working environment, reducing ambient stressors for staff.
- Improved Morale: A demonstrably safer workplace, utilizing modern technology, can significantly boost employee morale and foster a stronger safety culture, where workers feel valued and protected.
Leveraging Advanced Technologies (IoT & AI)
The integration of newer technologies further enhances the safety profile of automatic wrapping lines:
- IoT Connectivity: Internet of Things (IoT) enabled systems allow for remote monitoring of machine status and performance, facilitating proactive maintenance and faster responses to alerts, even from off-site locations.
- Predictive Maintenance: By analyzing sensor data and operational trends (often using AI algorithms), systems can predict potential component failures before they occur, allowing maintenance to be scheduled proactively, preventing unexpected breakdowns and emergency repairs under pressure.
Conclusion: Investing in a Safer, More Productive Future
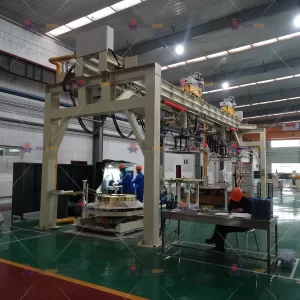
Implementing full-automatic copper coil wrapping lines is a strategic investment that pays dividends in operational safety and efficiency. By minimizing manual handling, incorporating robust safety features, ensuring process consistency, and leveraging advanced monitoring, these systems directly address key risk factors in industrial environments. Factories that embrace this automation not only protect their workforce from injury but also benefit from improved productivity, reduced errors, and enhanced overall operational excellence, positioning themselves for sustained success in a competitive landscape.