From Manual to Automated: Upgrading Your Coil Handling Process for Efficiency and Safety
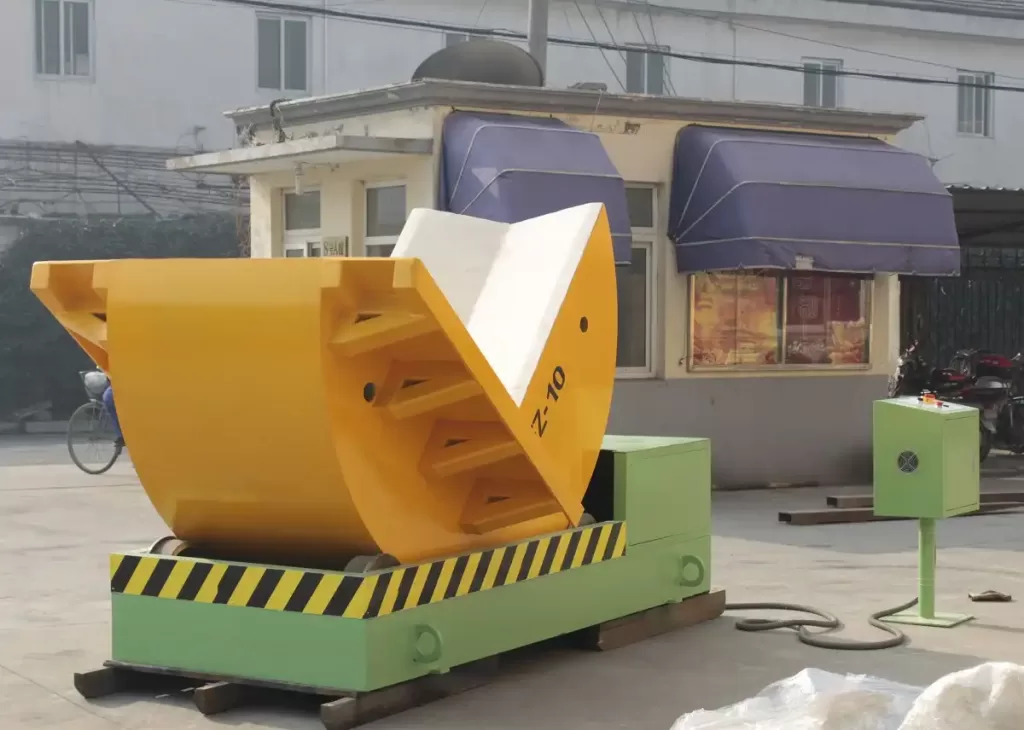
In today's competitive metal fabrication and manufacturing landscape, optimizing every stage of production is crucial. Handling heavy metal coils efficiently and safely remains a significant operational challenge. Transitioning from traditional manual methods to modern automated coil handling systems represents a major upgrade, boosting productivity, enhancing workplace safety, and improving overall process control. This guide explores the limitations of manual coil handling and details the compelling reasons and steps involved in upgrading to an automated solution.
1. The Challenges of Manual Coil Handling in Metal Fabrication
For decades, many facilities have relied on manual or semi-manual methods for moving, tilting, and positioning metal coils. This typically involves forklifts, overhead cranes, C-hooks, and manual upenders, operated directly by personnel. While functional, these methods present substantial drawbacks:
- Significant Safety Risks: Manual handling of heavy, bulky coils exposes workers to high risks of musculoskeletal injuries (strains, sprains), crush injuries, and accidents involving moving equipment. Repetitive lifting and awkward postures exacerbate these ergonomic hazards.
- Process Inefficiencies: Manual operations are inherently slower and less consistent than automated alternatives. Time is lost during loading/unloading, positioning adjustments, and waiting for equipment or operators, creating bottlenecks in the production flow.
- Material Damage Potential: Improper handling with forks, hooks, or manual positioning can easily lead to scratches, dents, or edge damage on coils. This waste impacts material costs and potentially downstream quality.
- High Labor Dependency and Costs: Manual processes require a significant number of skilled operators. Labor costs, including training, wages, benefits, and potential injury-related expenses (workers' compensation, lost time), contribute substantially to operational overhead.
- Inconsistency and Errors: Human variability can lead to inconsistent placement of coils, potentially causing issues with feeding machinery like presses, slitters, or roll formers, leading to downtime or further material damage.
Despite these issues, concerns about the initial investment cost often delay the transition to automation. However, a thorough analysis usually reveals that the long-term return on investment (ROI) from automated coil handling equipment significantly justifies the expenditure.
2. Why Upgrade to Automated Coil Handling Systems? The Benefits Explained
Implementing automated coil handling technology transforms operations by leveraging machinery to perform tasks faster, more reliably, and with unparalleled safety. The advantages extend across multiple facets of the business:
- Enhanced Workplace Safety: Automation drastically reduces the need for direct human interaction with heavy coils during lifting, tilting, and transport. Features like sensors, interlocks, emergency stops, and physical guarding minimize exposure to hazardous situations, aligning with crucial safety standards like those from OSHA (Occupational Safety and Health Administration).
- Increased Productivity and Throughput: Automated systems operate consistently and can run 24/7 with minimal supervision. Faster cycle times for handling operations eliminate bottlenecks, allowing downstream processes (stamping, slitting, etc.) to run at their optimal capacity, significantly boosting overall plant throughput.
- Improved Material Quality: Gentle, precise handling by automated equipment minimizes the risk of damage to sensitive coil surfaces and edges. Consistent positioning ensures proper feeding into machinery, reducing scrap rates and improving the quality of finished parts.
- Significant Cost Reduction: While requiring upfront investment, automation yields substantial long-term savings through:
- Reduced direct labor costs.
- Lower expenses related to workplace injuries and insurance premiums.
- Minimized material scrap and waste.
- Increased machine uptime and overall equipment effectiveness (OEE).
- Optimized use of floor space (especially with automated storage).
- Consistency and Precision: Automated systems perform tasks identically every time, ensuring coils are positioned accurately for subsequent operations. This predictability improves process stability and simplifies integration with other automated machinery.
Automation empowers the workforce by shifting focus from strenuous, hazardous manual labor to higher-value tasks like system monitoring, quality control, and process optimization.
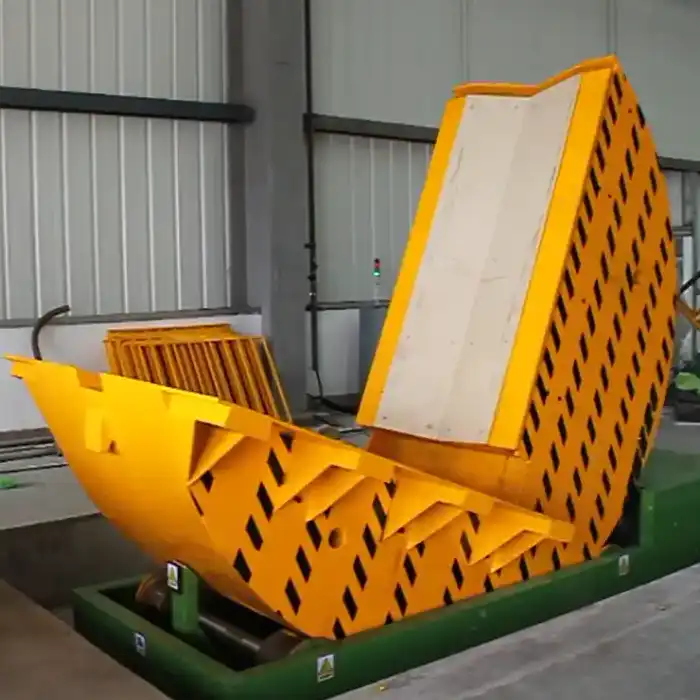
3. Key Technologies in Automated Coil Handling
A comprehensive automated coil handling system integrates various specialized equipment components designed for specific tasks within the coil lifecycle:
3.1 Coil Upenders and Tilters
Essential for changing coil orientation (e.g., from eye-to-sky for storage to eye-horizontal for processing), coil upenders (also known as coil tilters) are a cornerstone of automation.
- Functionality: They securely grip and rotate coils through 90 or 180 degrees. Types include mechanical screw-driven and hydraulic models, chosen based on capacity, speed, and duty cycle requirements.
- Integration: Often integrated with conveyors, coil cars, or automated guided vehicles (AGVs) for seamless transfer between processes.
- Features: Modern units include robust construction, smooth rotation control, load capacity sensors, and safety interlocks. Fhopepack provides more details on coil upenders.
3.2 Automated Coil Cars and Transfer Systems
These systems transport coils horizontally between locations, such as receiving docks, storage areas, and production lines.
- Types: Common options include rail-bound transfer cars (ideal for fixed paths and heavy loads) and more flexible AGVs or autonomous mobile robots (AMRs) for dynamic routing.
- Specifications: Designed for specific payload capacities (often up to 50 tons or more), travel speeds, and positioning accuracy.
- Integration: Interface with loading/unloading stations, upenders, and production machinery controls for coordinated movement.
3.3 Coil Storage and Retrieval Systems (AS/RS)
For facilities handling numerous coils, Automated Storage and Retrieval Systems (AS/RS) offer high-density, efficient storage solutions.
- Configurations: Can be vertical (utilizing overhead space effectively) or horizontal rack-based systems, managed by stacker cranes or specialized vehicles.
- Benefits: Maximize storage density, reduce retrieval times, improve inventory accuracy, and minimize damage from excessive handling.
- Integration: Typically linked with Warehouse Management Systems (WMS) or Manufacturing Execution Systems (MES) for real-time inventory tracking and automated order fulfillment.
3.4 Robotic Handling and Packaging
Robots add flexibility and precision to specific handling tasks and end-of-line packaging.
- Applications: Robots equipped with specialized end-effectors can load/unload coils onto mandrels, palletize smaller coils, or assist in inspection tasks.
- Packaging Automation: Automated coil wrapping (stretch film) and strapping machines ensure consistent, secure packaging for shipment or internal transfer, protecting coils and ensuring load stability.
upender 4. Implementing Automated Coil Handling: A Step-by-Step Guide
Transitioning to automation requires careful planning and execution. Following a structured approach ensures a successful implementation:
4.1 Needs Assessment and Process Analysis
- Map Current Workflow: Document the existing manual coil handling process, including steps, times, personnel involved, and equipment used.
- Identify Bottlenecks and Risks: Pinpoint areas with the lowest efficiency, highest safety risks, and most frequent material damage incidents.
- Define Goals and Requirements: Clearly state the objectives for automation (e.g., increase throughput by X%, reduce injuries by Y%, handle coils up to Z weight/size).
- Calculate Potential ROI: Estimate the expected financial benefits (cost savings, productivity gains) versus the projected investment cost to build a business case.
4.2 Selecting the Right Automation Partner and Equipment
- Vendor Evaluation: Research and vet potential automation suppliers based on experience, technical expertise, support capabilities, and references within the metal fabrication industry.
- Solution Design: Work with chosen partners to design a system tailored to your specific needs. Consider factors like:
- Coil specifications: Weight range, diameters (ID/OD), widths, material types.
- Throughput requirements: Coils per hour/shift.
- Facility layout and space constraints.
- Integration with existing machinery and control systems.
- Custom vs. Standard: Evaluate whether standard equipment modules suffice or if custom-engineered solutions are necessary.
4.3 Integration and Installation
- Phased Approach: Consider implementing automation in stages (e.g., starting with an automated tilter, then adding transport) to manage disruption and investment.
- Coordination: Ensure seamless integration of mechanical components, electrical wiring, control systems (PLCs), and safety systems.
- Factory Acceptance Test (FAT) & Site Acceptance Test (SAT): Conduct thorough testing at the vendor's facility and upon installation to verify performance against specifications.
- Safety During Install: Adhere strictly to safety protocols during the installation and commissioning phases.
4.4 Workforce Training and Change Management
- Operator Training: Provide comprehensive training on operating the new automated system, including user interfaces, standard procedures, and basic troubleshooting.
- Maintenance Training: Equip maintenance staff with the skills needed for preventative maintenance (PM), diagnostics, and repairs.
- Communication: Address workforce concerns proactively, emphasizing how automation enhances safety and enables employees to focus on less strenuous, more skilled tasks.
5. Safety Considerations for Automated Coil Handling Systems
While automation inherently improves safety, designing and maintaining these systems requires adherence to rigorous safety standards:
- Compliance: Ensure the system complies with relevant regulations and standards (e.g., OSHA machine guarding, ANSI/RIA robot safety standards).
- Safety Features: Incorporate multiple layers of protection:
- Physical Guarding: Fencing or barriers to restrict access to hazardous areas.
- Presence Sensing: Light curtains, safety mats, or laser scanners to detect personnel intrusion and stop motion.
- Emergency Stops (E-stops): Easily accessible buttons to halt all system movement immediately.
- Load Monitoring: Sensors to prevent overloading equipment.
- Interlocks: Safety switches on access gates that stop machinery when opened.
- Risk Assessment: Conduct a thorough risk assessment during the design phase to identify and mitigate potential hazards.
- Regular Maintenance and Inspection: Implement a robust PM program and conduct regular safety inspections to ensure all features remain functional.
steel coil upender 6. The Future Outlook: Trends in Coil Handling Automation
The evolution of automated coil handling continues, driven by advancements in technology:
- Industrial Internet of Things (IIoT): Increased use of sensors to collect real-time data on equipment performance, coil status, and energy consumption for better monitoring and diagnostics.
- Artificial Intelligence (AI) and Machine Learning (ML): AI algorithms for predictive maintenance (anticipating failures before they occur), process optimization (dynamically adjusting parameters), and enhanced vision systems for quality inspection.
- Advanced Robotics: More collaborative robots (cobots) working alongside humans, increased payload capacities, and improved dexterity for complex handling tasks.
- Data Integration: Tighter integration between handling systems and higher-level MES/ERP systems for full process visibility and control.
- Sustainability: Focus on energy-efficient designs and optimized operations to reduce the environmental footprint.
Companies embracing these cutting-edge automation technologies will be well-positioned to lead in efficiency, safety, and overall operational excellence.
Conclusion
Upgrading from manual to automated coil handling systems is a strategic imperative for modern metal fabricators seeking to enhance competitiveness. The benefits—improved safety, increased productivity, reduced costs, and better material quality—provide a compelling case for investment. By carefully planning the transition, selecting appropriate technologies, prioritizing safety, and training the workforce, manufacturers can successfully implement automation and unlock significant long-term operational advantages. In an industry where precision, speed, and safety are paramount, investing in robust coil handling automation is key to future success.

Get Your Best Solution !