From Basic to Advanced: Comparing Automation Features in Steel Coil Packing Lines
- From Basic to Advanced: Comparing Automation Features in Steel Coil Packing Lines
- Limitations of Fully Automated Systems
- 5. Key Differences Between Basic, Semi-Automated, and Fully Automated Systems
- 6. Safety Benefits Across Different Automation Levels
- 7. Production Throughput: Speed and Efficiency Gains
- 8. Data Collection and Analytics Capabilities
- 9. Scalability: Adapting to Growing Business Needs
- 10. Cost Considerations: Balancing Investment and ROI
- Conclusion
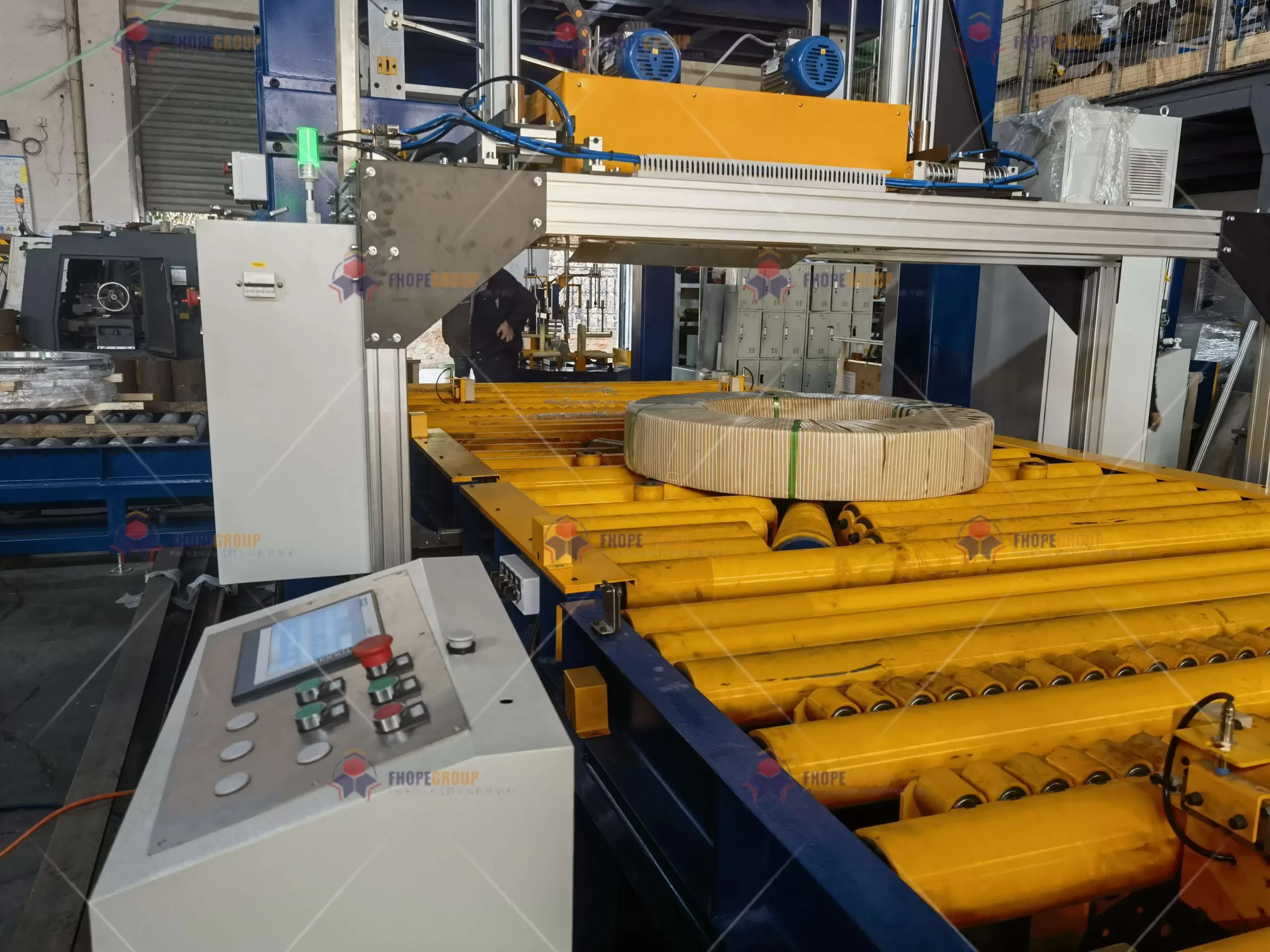
Introduction
In today’s competitive manufacturing landscape, automation is no longer just an option; it’s a necessity for companies looking to improve efficiency, enhance safety, and reduce operational costs. The steel coil packaging industry is no exception. As demand for high-volume production and faster turnaround times grows, businesses are adopting more advanced automation technologies to stay ahead. However, the level of automation can vary widely, from basic semi-automated systems to fully integrated, intelligent packaging lines.
This article will take a detailed look at the different levels of automation in steel coil packing lines—from basic systems to advanced, state-of-the-art technology. We will explore the key features, benefits, and limitations of each level, providing insight into how manufacturers can choose the right level of automation for their operations. Whether you’re considering a basic upgrade or planning to invest in cutting-edge automated systems, this guide will help you understand what’s available and how it can impact your business.
1. The Role of Automation in Steel Coil Packaging
Why Automation Matters
Steel coil packaging involves handling large, heavy products that need to be securely packed for transportation and storage. Without automation, this process can be labor-intensive, time-consuming, and prone to human error. Automation brings precision, speed, and safety to the table, making the entire process more reliable and scalable.
- Precision: Automated systems can wrap and strap steel coils with a level of consistency that is difficult to achieve manually.
- Safety: Machines handle the most hazardous tasks, reducing the risk of injuries related to manual lifting and handling.
- Speed: Automated systems can complete tasks faster than human workers, increasing throughput and productivity.
Understanding the basic and advanced features of automation helps manufacturers optimize their packing lines to meet production goals more effectively.
2. Basic Automation in Steel Coil Packing
What is Basic Automation?
Basic automation refers to the partial mechanization of manual processes. These systems are typically designed to perform specific tasks, such as wrapping or strapping, but still require significant human intervention. For many manufacturers, basic automation is the first step toward modernizing their packaging lines.
Key Features of Basic Automation
- Semi-Automated Wrapping Machines: These machines assist operators in wrapping coils with stretch film or protective materials but still require manual handling of the coils.
- Manual Strapping Tools: While some level of automation may be used to apply the straps, workers are still needed to position and secure the straps around the coil.
- Conveyor Systems: Basic conveyors may be used to move coils from one station to another, reducing the need for workers to lift and transport coils manually.
Benefits of Basic Automation
- Cost-Effective: Basic automation is more affordable than fully automated systems, making it accessible to smaller businesses or those with lower production volumes.
- Reduced Manual Labor: Even partial automation can significantly reduce the physical strain on workers, improving safety and efficiency.
- Scalability: Basic systems can often be upgraded over time, allowing businesses to gradually move toward more advanced automation as their needs grow.
Limitations of Basic Automation
- High Dependency on Manual Labor: Basic systems still require significant worker involvement, which limits the overall gains in efficiency and speed.
- Inconsistent Results: Because manual intervention is required, the quality of packaging can vary from coil to coil, especially when large production volumes are involved.
- Limited Data and Monitoring: Basic systems typically do not offer the advanced monitoring and data collection features found in more sophisticated systems.
3. Mid-Level Automation: Enhancing Efficiency with Semi-Automated Systems
The Step Up: Semi-Automated Systems
Mid-level automation, also known as semi-automated systems, offers a balance between manual intervention and automated processes. These systems are designed to handle more tasks autonomously while still allowing operators to control and adjust key settings as needed. Mid-level systems are ideal for manufacturers who are looking for more efficiency but are not ready for the full commitment of advanced automation.
Key Features of Semi-Automated Systems
- Automated Wrapping: Semi-automated systems can wrap steel coils without manual intervention, ensuring a consistent application of protective materials.
- Strapping Automation: Strapping machines automatically apply and secure straps to the coils, minimizing the need for manual handling.
- Programmable Settings: Operators can adjust settings such as wrapping tension, coil size, and strap placement through an interface, allowing for some level of customization.
Benefits of Semi-Automated Systems
- Improved Efficiency: By automating repetitive tasks like wrapping and strapping, these systems significantly reduce the time it takes to package each coil.
- Consistent Quality: Automation ensures that every coil is wrapped and strapped consistently, reducing the risk of product damage during transport.
- Reduced Physical Labor: Semi-automated systems take over the most physically demanding tasks, making the process safer for workers and reducing the risk of injuries.
Limitations of Semi-Automated Systems
- Still Requires Operator Involvement: While many tasks are automated, operators are still required to oversee the process and make adjustments, which limits the potential for full automation benefits.
- Moderate Investment: Semi-automated systems require a higher initial investment than basic systems, which may not be feasible for smaller operations.
- Less Advanced Data Capabilities: Semi-automated systems may offer some monitoring features but lack the advanced data analytics and predictive maintenance capabilities found in fully automated solutions.
4. Advanced Automation: The Future of Steel Coil Packing
Fully Automated Systems
At the highest level of automation are fully automated steel coil packaging lines, which are capable of performing every task in the packaging process with minimal to no human intervention. These systems integrate advanced technologies such as robotics, IoT connectivity, and AI-driven analytics, allowing them to optimize every aspect of the packaging process from start to finish.
Key Features of Fully Automated Systems
- Robotic Wrapping and Strapping: Robots handle the wrapping and strapping process with high precision, ensuring that every coil is packaged exactly to specification.
- Integrated Material Handling: Fully automated systems include conveyors, robotic arms, and automated storage systems that move steel coils throughout the packaging process without the need for manual handling.
- Advanced Monitoring and Diagnostics: IoT-enabled sensors monitor machine performance in real-time, providing valuable data on system health, coil quality, and material usage. AI-driven systems can even predict when maintenance is required, preventing unplanned downtime.
Benefits of Fully Automated Systems
- Maximum Efficiency: Fully automated systems can process steel coils at a much faster rate than semi-automated or basic systems, dramatically increasing throughput and reducing labor costs.
- Enhanced Safety: With minimal human intervention, fully automated systems eliminate many of the risks associated with manual coil handling, such as injuries from heavy lifting or repetitive motion.
- Data-Driven Decision Making: The data collected from IoT sensors and integrated software provides real-time insights that allow companies to make informed decisions about system performance, maintenance schedules, and material usage.
- Predictive Maintenance: Advanced automation systems use predictive analytics to forecast when components will need maintenance, reducing the likelihood of equipment failure and unplanned downtime.
Limitations of Fully Automated Systems
- High Initial Investment: Fully automated systems represent a significant financial investment, which may not be justified for smaller operations or those with lower production volumes.
- Complex Implementation: The installation and integration of fully automated systems can be complex, requiring a thorough understanding of both the technology and the production process.
- Requires Skilled Workforce: While fewer workers are needed, those who manage fully automated systems must have specialized skills in robotics, software, and maintenance to ensure smooth operation.
5. Key Differences Between Basic, Semi-Automated, and Fully Automated Systems
Manual Intervention and Labor Requirements
The most significant difference between the three levels of automation—basic, semi-automated, and fully automated systems—lies in the amount of manual intervention required. Basic systems rely heavily on human operators for tasks such as wrapping, strapping, and coil transportation. Semi-automated systems reduce this dependency by automating repetitive tasks, although operators are still needed for oversight and adjustments. Fully automated systems, however, require minimal human involvement, as machines handle almost every aspect of the packaging process.
Labor Efficiency Comparison
- Basic Systems: Operators are involved in most tasks, making labor costs higher and the process slower. The risk of injuries due to heavy lifting and manual handling is also more pronounced.
- Semi-Automated Systems: Operators are needed for system oversight and adjustments but do not handle the physical packaging process. This reduces labor costs and improves safety.
- Fully Automated Systems: Minimal human intervention is needed, which greatly reduces labor costs and increases overall efficiency.
Cost Considerations
Cost is another critical factor when comparing these systems. Basic systems are the least expensive but offer the fewest productivity gains. Semi-automated systems represent a middle ground, offering increased efficiency at a moderate cost. Fully automated systems have the highest upfront costs but deliver the greatest long-term savings due to lower labor costs and higher productivity.
Return on Investment (ROI) Comparison
- Basic Systems: Low initial investment but also limited improvements in efficiency and throughput.
- Semi-Automated Systems: Moderate investment with significant improvements in efficiency and safety, leading to faster ROI than basic systems.
- Fully Automated Systems: High initial investment but substantial long-term savings in labor and maintenance, resulting in the fastest ROI for larger-scale operations.
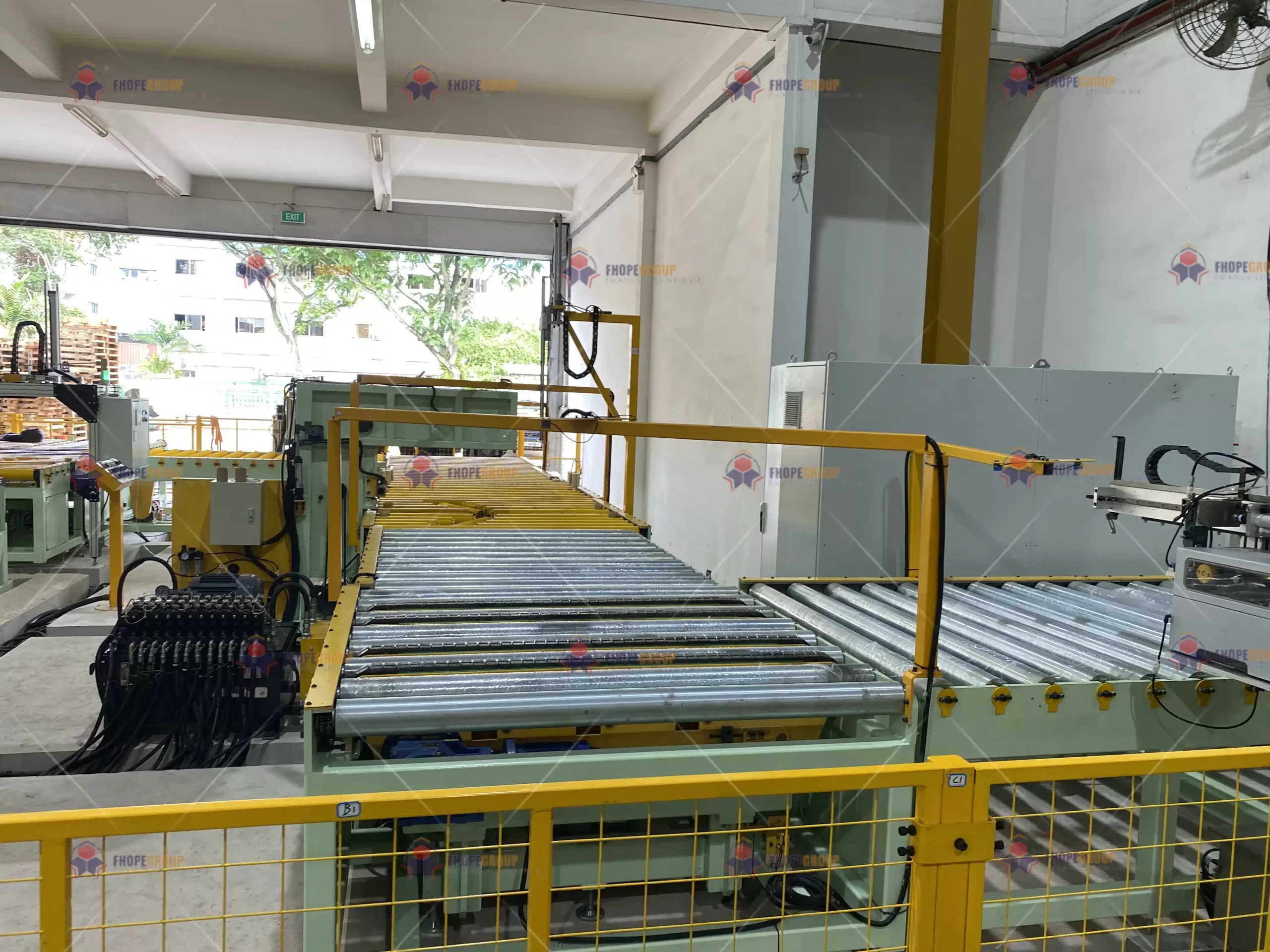
6. Safety Benefits Across Different Automation Levels
Reducing Workplace Injuries
One of the main drivers for adopting automation in steel coil packing lines is the enhanced safety it provides. Each level of automation offers safety improvements, but fully automated systems deliver the most significant reduction in workplace injuries by removing almost all manual handling of coils.
Safety Features Breakdown
- Basic Systems: While some mechanical assistance is provided, workers are still at risk of injuries from heavy lifting, repetitive motion, and operating manual strapping tools.
- Semi-Automated Systems: By automating the most physically demanding tasks, such as wrapping and strapping, semi-automated systems significantly reduce the risk of musculoskeletal injuries and accidents.
- Fully Automated Systems: Workers are no longer involved in any direct handling of coils, meaning the risk of injuries from heavy lifting, pinch points, or repetitive strain is virtually eliminated.
Machine Safety Protocols
Another important aspect of safety is the implementation of machine guarding and safety protocols. Semi-automated and fully automated systems come with built-in safety features such as emergency stop buttons, sensors that detect human proximity, and guard rails to prevent workers from coming into contact with moving parts. These safety features are essential for complying with OSHA guidelines and protecting workers from hazardous machinery.
7. Production Throughput: Speed and Efficiency Gains
Processing Speed
As automation increases, so does the speed at which steel coils are packaged. Basic systems often struggle to keep up with high-volume production demands due to their reliance on manual labor. Semi-automated systems improve speed by automating critical steps, but fully automated systems are capable of running continuously with minimal downtime, making them the ideal choice for operations that require maximum throughput.
Speed Comparison
- Basic Systems: Slower processing times due to manual tasks, which can lead to bottlenecks, especially during peak production periods.
- Semi-Automated Systems: Faster than basic systems, as key tasks such as wrapping and strapping are automated, but still require manual adjustments that may slow down the process.
- Fully Automated Systems: The fastest option, as machines work at a consistent speed without the need for human intervention. Fully automated systems can process large volumes of coils with minimal delays.
Downtime Reduction
One of the key benefits of fully automated systems is the ability to reduce unplanned downtime. By using predictive maintenance tools and IoT sensors, fully automated systems can detect when equipment needs servicing and alert operators before a breakdown occurs. This reduces the chances of unexpected machine failure, ensuring that the production line continues to operate smoothly.
8. Data Collection and Analytics Capabilities
The Importance of Data in Modern Manufacturing
In today’s data-driven world, access to real-time information is crucial for optimizing operations. Fully automated steel coil packaging lines are equipped with IoT sensors and data analytics platforms that provide detailed insights into every aspect of the process. This includes tracking material usage, machine performance, production rates, and more.
Data Capabilities by Automation Level
- Basic Systems: Minimal data collection, often limited to manual logs or basic counters.
- Semi-Automated Systems: Some level of data collection is available, often focused on operational metrics such as coil count and packaging speed. However, advanced predictive analytics and real-time monitoring are typically limited.
- Fully Automated Systems: Full data integration with real-time monitoring and analytics. Advanced systems can provide detailed reports on system performance, predict when maintenance is needed, and identify areas where efficiency can be improved.
Leveraging Predictive Maintenance
One of the biggest advantages of fully automated systems is their ability to predict maintenance needs. By analyzing data collected from IoT sensors, the system can forecast when components are likely to wear out or fail, allowing for proactive maintenance scheduling. This minimizes unplanned downtime and ensures that the system continues to run efficiently.
9. Scalability: Adapting to Growing Business Needs
Scalability Across Different Systems
When investing in automation, it’s essential to consider how scalable the system is. As your business grows, your packaging line needs to adapt to higher production demands. Basic systems are often limited in scalability, while fully automated systems are designed with growth in mind, allowing you to expand or add more capacity with minimal disruption.
Scalability Comparison
- Basic Systems: Limited scalability. These systems may struggle to keep up with increased production demands and would likely need to be replaced or significantly upgraded as the business grows.
- Semi-Automated Systems: More scalable than basic systems, as they offer some automation that can handle increased volumes. However, they may still require manual adjustments or additional labor as production expands.
- Fully Automated Systems: The most scalable option, fully automated systems can easily handle increased production volumes without the need for significant changes. They are designed to integrate additional components, such as more robotic arms or conveyors, as needed.
Preparing for Future Technology Integration
Fully automated systems are built with future technologies in mind, allowing manufacturers to integrate the latest advancements in robotics, AI, and machine learning. This adaptability ensures that your investment in automation remains relevant and can continue to support your business as technology evolves.
10. Cost Considerations: Balancing Investment and ROI
Upfront Costs vs. Long-Term Savings
The cost of automation can vary significantly depending on the level of automation being implemented. Basic systems are the least expensive, but they also offer the fewest long-term savings. Semi-automated systems provide a balance between initial cost and efficiency gains, while fully automated systems have the highest upfront costs but deliver the most substantial long-term savings through reduced labor and increased productivity.
ROI by Automation Level
- Basic Systems: Low upfront cost but limited long-term savings. ROI may be slow, especially if production volumes are high.
- Semi-Automated Systems: Moderate investment with good returns due to improved efficiency and safety. ROI is typically realized within a few years, especially in mid-sized operations.
- Fully Automated Systems: High initial investment but the fastest ROI in high-volume production environments. Long-term savings from reduced labor, improved safety, and increased throughput make fully automated systems the most cost-effective choice for large-scale operations.
Conclusion
Choosing the right level of automation for your steel coil packaging line depends on various factors, including production volume, budget, safety requirements, and long-term goals. Basic automation offers an affordable entry point but requires significant manual intervention, while semi-automated systems strike a balance between cost and efficiency. For those seeking maximum productivity, safety, and scalability, fully automated systems provide the best solution, with advanced features such as robotic handling, predictive maintenance, and data-driven decision making.
As technology continues to evolve, manufacturers must carefully evaluate their current needs and future growth potential to make the best investment in automation. By selecting the right system, companies can improve productivity, reduce operational costs, and create a safer work environment, all while staying competitive in a rapidly changing industry.