The True Cost of Ownership: Factoring Maintenance and Downtime in Steel Coil Packing Lines
- The True Cost of Ownership: Factoring Maintenance and Downtime in Steel Coil Packing Lines
- 1. What Is the True Cost of Ownership?
- 2. Why Maintenance Matters in Steel Coil Packing Lines
- 3. The Financial Impact of Downtime
- 4. How Downtime Affects Productivity
- 5. The Role of Automation in Reducing Maintenance and Downtime
- 6. Long-Term Effects of Inadequate Maintenance
- 7. The Impact of Downtime on Customer Satisfaction and Reputation
- 8. Strategies for Reducing Downtime in Steel Coil Packing Lines
- 9. The Role of Spare Parts Management in Reducing Downtime
- 10. Cost-Benefit Analysis: Investing in Maintenance vs. Risking Downtime
- Conclusion
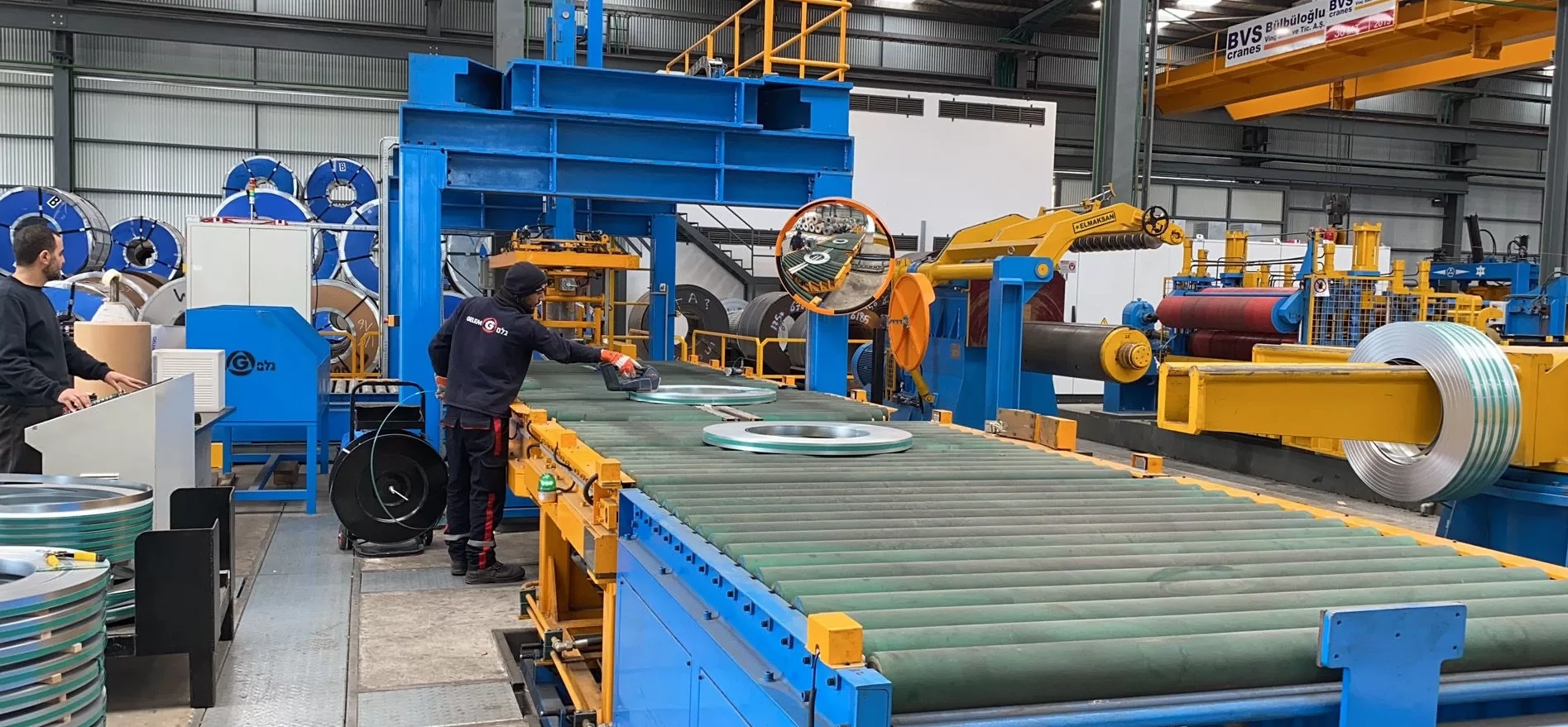
Investing in a steel coil packing line is a significant decision for any business that deals with heavy manufacturing or logistics. While the initial price tag is often the first thing that comes to mind, it’s essential to dig deeper and consider the true cost of ownership. Over the lifespan of the equipment, hidden costs such as maintenance and downtime can add up significantly, impacting both productivity and profitability.
In this article, we’ll take an in-depth look at how maintenance schedules, unexpected breakdowns, and downtime factor into the overall cost of running a steel coil packing line. By understanding these crucial elements, businesses can make more informed decisions, ensuring they get the best value from their investment.
1. What Is the True Cost of Ownership?
The true cost of ownership (TCO) refers to the total expenses incurred over the lifespan of a machine, going beyond the initial purchase price. When considering the TCO of a steel coil packing line, it’s critical to account for:
- Initial investment cost: The price of purchasing and installing the equipment.
- Maintenance costs: Routine service, part replacements, and preventive maintenance.
- Downtime costs: Lost productivity and revenue when the machine is out of service.
- Energy consumption: The ongoing costs of running the equipment.
- Operational efficiency: How well the machine integrates into the workflow and its impact on productivity.
By focusing on the lifecycle costs rather than just the upfront price, businesses can avoid unexpected financial hits and maximize the return on their investment.
2. Why Maintenance Matters in Steel Coil Packing Lines
Maintenance is one of the most significant ongoing costs for any industrial machinery. For steel coil packing lines, regular maintenance is essential to ensure that the system runs smoothly, safely, and efficiently. Without proper upkeep, even the most advanced automated packing systems can experience performance issues or breakdowns, leading to costly repairs or replacements.
a. Preventive vs. Reactive Maintenance
There are two main types of maintenance strategies businesses can adopt:
- Preventive maintenance involves regular inspections, servicing, and part replacements to prevent equipment failure. This proactive approach helps to avoid unexpected breakdowns and extends the equipment's lifespan.
- Reactive maintenance, on the other hand, focuses on fixing issues after they arise. While it may save on initial maintenance costs, the downtime and repair expenses can be far more costly in the long run.
Choosing preventive maintenance over reactive approaches can dramatically reduce the chances of catastrophic failures, saving the company both time and money.
b. Key Components Requiring Maintenance
Steel coil packing lines consist of several key components that require regular attention:
- Turnstile systems: These parts are responsible for holding and rotating the coils, and any failure here can halt the entire line.
- Coil wrapping machines: These machines need consistent lubrication, cleaning, and calibration to maintain precision.
- Strapping machines: Strapping tension and alignment must be regularly checked to ensure coils are securely strapped without overstraining the material.
- Conveyor belts: The conveyor system moves the steel coils through the packing line, so any issues with the belt can lead to bottlenecks or delays.
By addressing these components through scheduled maintenance, businesses can minimize the risk of unexpected failures and extend the overall lifespan of the equipment.
3. The Financial Impact of Downtime
When a steel coil packing line experiences downtime, the costs can quickly spiral out of control. Downtime doesn’t just mean idle machinery—it represents lost productivity, missed deadlines, and unfulfilled orders, all of which can harm your reputation and your bottom line.
a. Calculating the Cost of Downtime
To fully understand the financial impact of downtime, it’s important to look at the numbers. You can calculate the cost of downtime with a simple formula:
Downtime Cost = (Lost Production Time) x (Revenue Lost per Hour)
For example, if your steel coil packing line is down for 4 hours and the revenue generated per hour is $5,000, the total downtime cost is $20,000. This doesn’t include the additional expenses such as paying workers while the system is offline, delayed orders, and potential customer dissatisfaction.
b. Unplanned vs. Planned Downtime
Not all downtime is avoidable, but there’s a key distinction between unplanned and planned downtime:
- Planned downtime is typically scheduled for maintenance or upgrades, allowing businesses to minimize disruption by adjusting production schedules.
- Unplanned downtime, however, occurs due to unexpected equipment failures and is often more costly. Not only is the business unprepared, but the equipment repair may take longer, and the knock-on effects can impact the entire production line.
By investing in preventive maintenance and ensuring a reliable system, companies can significantly reduce unplanned downtime and its associated costs.
4. How Downtime Affects Productivity
Every minute a steel coil packing line is down, production stops, which can cause a ripple effect throughout the supply chain. If coils aren’t packed and prepared for shipping on time, the delays can affect warehousing, shipping schedules, and even the production of new coils waiting to be processed.
a. Impact on the Supply Chain
In industries like automotive or construction, where timing is critical, even short periods of downtime can cause substantial delays. These industries often work on just-in-time (JIT) inventory systems, meaning that the delays in packing and shipping steel coils can halt operations further down the chain. This creates a domino effect that increases the cost of missed deadlines and delays throughout the supply chain.
b. Operational Bottlenecks
A breakdown in the steel coil packing line can also create bottlenecks that affect other operations. For example, if the packing line is down, coils may pile up, leading to disruptions in the manufacturing process. Workers may have to stop production or reroute operations to deal with the backlog, which adds additional costs and reduces overall productivity.
By minimizing downtime, businesses can avoid these bottlenecks and ensure that production flows smoothly from start to finish.

Get Your Best Solution !
5. The Role of Automation in Reducing Maintenance and Downtime
Automation plays a crucial role in reducing maintenance requirements and minimizing downtime. Modern steel coil packing lines are equipped with automated systems that monitor performance, detect potential issues, and alert operators to the need for maintenance before problems arise.
a. Predictive Maintenance Through IoT and Sensors
With the rise of Internet of Things (IoT) technologies, steel coil packing lines can now be equipped with sensors that track performance in real-time. These sensors gather data on things like vibration levels, temperature, and operating speed. By analyzing this data, businesses can implement predictive maintenance strategies.
Predictive maintenance allows operators to address potential issues before they cause downtime, rather than waiting for a problem to occur. For example, if the sensors detect an abnormal rise in temperature in a strapping machine, maintenance can be performed before a complete failure occurs. This approach not only reduces downtime but also prolongs the lifespan of the equipment.
b. Automated Alerts and Monitoring
Modern automated systems come with built-in monitoring features that notify operators of potential maintenance needs. These systems can send real-time alerts when a part is nearing its end of life or when performance is dropping below acceptable thresholds. Automated alerts ensure that maintenance teams are aware of potential issues and can schedule repairs during planned downtime, preventing unexpected interruptions.
6. Long-Term Effects of Inadequate Maintenance
Failing to maintain a steel coil packing line properly doesn’t just result in short-term downtime—it can have long-lasting consequences that affect the overall performance and longevity of the equipment.
a. Accelerated Wear and Tear
Without regular maintenance, key components of the packing line, such as motors, belts, and strapping heads, will experience accelerated wear and tear. This can lead to more frequent breakdowns, increased repair costs, and a shorter lifespan for the machine. As components wear out faster, the cost of replacement parts and repairs will increase over time, eating into profits.
b. Decreased Efficiency Over Time
A poorly maintained steel coil packing line will gradually become less efficient. Equipment that isn’t regularly serviced may run slower, experience more errors, or produce lower-quality packaging. Over time, this decreased efficiency can reduce your overall production capacity, leading to higher operational costs and missed production targets.
By prioritizing maintenance, businesses can ensure that their equipment runs at peak efficiency throughout its lifespan, avoiding the long-term costs of neglect.

7. The Impact of Downtime on Customer Satisfaction and Reputation
Downtime doesn't only affect the bottom line—it also has a direct impact on customer satisfaction and the reputation of your business. When a steel coil packing line is down, delays in shipping and production schedules can result in missed deadlines, late deliveries, and frustrated customers.
a. Delayed Deliveries and Lost Business
In industries where on-time delivery is critical, such as automotive or construction, even a small delay can lead to lost contracts or orders. Customers who rely on your business for regular shipments of steel coils may switch to competitors if they experience frequent delays. This not only leads to lost revenue in the short term but can also damage long-term business relationships.
b. Reputation in the Marketplace
In today's digital age, reputation is everything. Word spreads quickly when businesses fail to meet deadlines or produce inconsistent results. Poor reliability can tarnish your reputation in the marketplace, leading to negative reviews and dissatisfied clients. Over time, this loss of trust can lead to a decline in new customer acquisition, as prospective clients may be wary of engaging with a company known for frequent production delays.
By minimizing downtime through effective maintenance practices, businesses can ensure they maintain a strong reputation for reliability, ensuring long-term customer satisfaction.
8. Strategies for Reducing Downtime in Steel Coil Packing Lines
Reducing downtime should be a top priority for any business relying on steel coil packing lines. There are several strategies that companies can adopt to minimize disruptions and ensure that operations run smoothly.
a. Implementing a Preventive Maintenance Schedule
As mentioned earlier, preventive maintenance is essential for keeping equipment in top condition and avoiding unexpected breakdowns. Businesses should establish a regular maintenance schedule that includes:
- Lubricating moving parts to prevent wear and tear.
- Inspecting key components, such as belts, motors, and strapping machines, for signs of damage.
- Calibrating sensors and automated systems to ensure they are functioning correctly.
- Replacing worn-out parts before they fail completely.
By sticking to a scheduled maintenance routine, businesses can prevent small issues from escalating into major breakdowns that result in extended downtime.
b. Investing in Redundant Systems
For operations that cannot afford any downtime, investing in redundant systems can provide a safety net. A redundant system is a backup line that can take over when the main packing line is undergoing maintenance or repairs. While this requires a significant upfront investment, it ensures that production can continue uninterrupted, protecting the business from costly downtime.
c. Training Employees for Quick Repairs
While automation can minimize the need for manual intervention, there will always be instances where human expertise is needed. Ensuring that employees are well-trained in basic repair and maintenance procedures can help to reduce the time it takes to get a packing line back up and running after a breakdown.
By empowering operators with the knowledge and tools to perform quick repairs, businesses can reduce downtime by addressing small issues in-house without waiting for external technicians.
d. Real-Time Monitoring and Data Analytics
Utilizing real-time monitoring systems allows businesses to track equipment performance and predict potential issues before they cause downtime. Sensors on the packing line can continuously monitor key metrics such as temperature, vibration, and operating speed. Any deviation from normal operating conditions can trigger an alert, giving the maintenance team a heads-up to investigate the issue.
Additionally, data analytics can be used to track the performance of the packing line over time. By analyzing patterns, businesses can identify inefficiencies and predict failures, allowing them to take proactive measures to prevent downtime.
9. The Role of Spare Parts Management in Reducing Downtime
Even with the best maintenance practices in place, parts will eventually wear out and need to be replaced. A key strategy for reducing downtime is to implement an effective spare parts management system. Without immediate access to spare parts, businesses may face extended delays while waiting for replacement components to arrive.
a. Stocking Critical Spare Parts
The most effective way to minimize downtime is to keep an inventory of critical spare parts on hand. These parts should include components that are prone to wear and tear, such as belts, motors, strapping heads, and sensors. By stocking these parts, businesses can quickly replace damaged components and get the packing line back in operation without significant delays.
b. Working with Reliable Suppliers
To ensure that spare parts are readily available, businesses should establish relationships with reliable suppliers who can provide fast delivery of replacement parts. In some cases, it may be beneficial to work directly with the equipment manufacturer to secure access to OEM parts that are specifically designed for the steel coil packing line.
10. Cost-Benefit Analysis: Investing in Maintenance vs. Risking Downtime
Many businesses struggle with the decision of how much to invest in preventive maintenance versus simply dealing with breakdowns as they occur. While it might seem cost-effective to minimize maintenance expenses in the short term, the long-term costs of downtime can far outweigh the savings.
a. The Hidden Costs of Downtime
When calculating the true cost of downtime, businesses should consider not only the lost production but also the secondary costs that come with it. These costs include:
- Overtime pay for workers who need to make up for lost production.
- Expedited shipping costs to meet delayed orders.
- Loss of customer trust and potential damage to reputation.
- Emergency repair costs, which are often higher than scheduled maintenance.
b. The Benefits of Regular Maintenance
In contrast, regular maintenance helps businesses avoid these hidden costs by keeping equipment in optimal condition. Over time, the money saved by reducing downtime and increasing operational efficiency will typically outweigh the costs of preventive maintenance.
By investing in maintenance, businesses can ensure that their steel coil packing line operates reliably, minimizing downtime and maximizing productivity.
Conclusion
The true cost of ownership for a steel coil packing line goes far beyond the initial purchase price. Maintenance, downtime, and spare parts management all play a significant role in determining the total expenses incurred over the lifespan of the equipment.
By implementing a preventive maintenance strategy, investing in automated monitoring systems, and ensuring quick access to spare parts, businesses can significantly reduce downtime, protect their bottom line, and maintain a competitive edge in the marketplace. Understanding and managing these costs is crucial for long-term profitability and operational success.
Ultimately, businesses that prioritize maintenance and efficiency will experience fewer disruptions, improved productivity, and greater overall value from their steel coil packing line investment.

Get Your Best Solution !