Essential Quality Inspection Points for Packing Machines Before Delivery
Inspection machines testing operation before delivery is crucial for ensuring optimal performance of packaging equipment.
Key checking points include functionality tests of HMI solutions, ensuring user interfaces are intuitive and responsive, verifying the integrity of open-source innovations for flexibility and adaptability, and conducting safety assessments to meet industry standards.
FHOPEPACK looking to enhance packaging processes consider these innovative solutions to boost efficiency and reliability. Embrace the future of packaging technology by investing in robust testing protocols and cutting-edge equipment today.
The on-site machine inspection mainly includes the following specific checking points:
1. Functionality Testing
When checking Full-automatic horizontal wrapper machines, it’s essential to confirm that all functions are operating normally. This includes a thorough assessment of the start, run, and stop processes.
During the start phase, the machine should initiate without any delays or errors, ensuring that all components engage correctly. While running, FHOPE packing equipment must maintain consistent performance, with no unusual sounds or vibrations, indicating smooth operation.
Finally, the stop function should bring the machine to a complete halt without any lingering movements or malfunctions. This comprehensive evaluation ensures reliability and sets the foundation for optimal performance in production environments.

2. Safety Checks
Inspecting safety guard devices is crucial for ensuring both the safety of operators and the effective functioning of machinery. FHOPE team provide safety guards prevent accidental contact with moving parts, reducing the risk of injuries such as cuts, crushes, and entanglements.
They also serve as a vital barrier during maintenance, allowing technicians to work without the fear of unexpected equipment activation. Compliance with relevant safety standards is essential, as these regulations are designed to protect workers and create a safer work environment.
Regular inspections should confirm that guards are intact, properly positioned, and free from any obstructions or damage.
FHOPE team prioritizing the integrity of safety guard devices for packing wrapper machines, companies not only adhere to legal requirements but also foster a culture of safety, which ultimately enhances employee morale and productivity.
Investing in robust safety measures is a proactive approach that pays dividends in preventing accidents and ensuring operational efficiency.
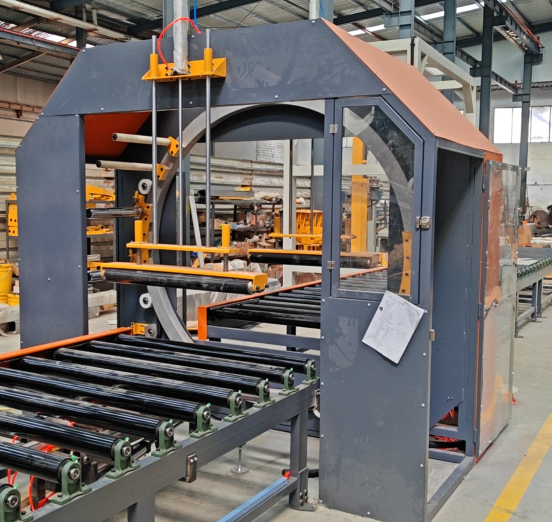
3. HMI Interface Inspection
HMI (Human-Machine Interface) interface inspection is vital for ensuring that operators can interact effectively with the machinery. Each set of FHOPE wrapping packing machine with an intuitive design allows users to navigate the system easily, reducing the learning curve and minimizing the risk of operational errors.
During the inspection, it’s essential to verify that the interface is responsive to user inputs, meaning that commands are executed promptly and accurately, which enhances workflow efficiency.
Clear labeling, logical layout, and accessible controls contribute to a seamless user experience. Additionally, testing for feedback mechanisms, such as visual or auditory signals, ensures that operators receive immediate confirmation of their actions.
A well-designed HMI not only improves usability but also enhances safety by enabling quick reactions to any issues that may arise, ultimately leading to a more productive and secure working environment. Prioritizing HMI effectiveness can significantly impact overall machine performance and operator satisfaction.

4. Performance Evaluation
Assessing equipment’s performance through rigorous testing under various loads and speeds be essential to ensure it meets design specifications and operational requirements.
This process involves simulating real-world conditions to evaluate how the machine handles different operational scenarios. By testing at varying loads, we can determine the machine’s stability, efficiency, and capacity, identifying any weaknesses or potential failure points.

Additionally, varying speeds allows for the assessment of dynamic performance, including acceleration and deceleration times, as well as the consistency of output quality. Monitoring key performance indicators, such as energy consumption and production rates during these tests, provides valuable insights into the machine’s efficiency.
This comprehensive evaluation not only helps to confirm that the equipment is capable of performing as intended but also enables early detection of issues that could lead to downtime or operational inefficiencies.
Ultimately, thorough performance testing is crucial for ensuring reliability and maximizing productivity in industrial settings. Such as wrapping tension adjustment for stretch film system…

5. Packaging Quality Inspection
Packaging quality inspection is an important step of FHOPE machines, in ensuring that products are presented effectively and securely to consumers. This process involves checking the neatness of the packaging, ensuring that it is free from wrinkles, tears, or any defects that could detract from the product’s appearance.
Proper sealing is equally important; packages must be securely sealed to protect the contents from contamination and damage during transit. Inspecting the integrity of seals helps prevent issues like leaks or spoilage, which can lead to significant financial losses.

Accuracy of labeling is crucial for compliance with regulations and consumer information. Labels should clearly display product information, including ingredients, expiration dates, and bar-codes, ensuring they are easy to read and scan.
By thoroughly assessing these aspects, companies can enhance customer satisfaction, reduce returns, and maintain brand reputation, ultimately contributing to a successful packaging process that meets both safety standards and consumer expectations.

6. Noise and Vibration Testing
Noise and vibration testing be essential for evaluating the operational integrity and comfort of machinery. During this process, precise measurement of noise levels helps identify any excessive sound emissions that could indicate mechanical issues or misalignment.
High noise levels can not only affect the workplace environment but also lead to operator fatigue and decreased productivity. Similarly, vibration analysis is critical for detecting potential problems, such as imbalances or wear in moving parts.
Excessive vibrations can result in accelerated wear and tear, ultimately shortening the equipment’s lifespan. By ensuring that both noise and vibration levels remain within acceptable limits, companies can foster a safer and more comfortable work environment.
Regular monitoring of these parameters also supports compliance with regulatory standards and helps prevent costly down times related to equipment failures.
Ultimately, thorough noise and vibration assessments contribute to the overall reliability and efficiency of machinery, enhancing operational performance and worker satisfaction.
7. Data Recording and Analysis
Checking the functionality of the data acquisition system for ensuring accurate monitoring and analysis of production processes. This system should be capable of capturing a variety of metrics, including output rates, machinery performance, and error rates, providing real-time insights into operations.
During the inspection, it is essential to verify that all sensors and data collection devices are properly calibrated and functioning as intended. Accurate data recording is vital for effective decision-making and operational improvements; it enables companies to identify trends, pinpoint inefficiencies, and implement corrective actions in a timely manner.
The system should facilitate seamless data transfer to analytical software for further processing and reporting.
By ensuring that the data acquisition system operates correctly, organizations can enhance their ability to manage production effectively, optimize resource utilization, and maintain high-quality standards, ultimately leading to improved productivity and profitability.
Regular checks of this system are key to sustaining operational excellence.
8. Maintenance and Care Inspection
Maintenance and care inspection is vital for ensuring the longevity and optimal performance of equipment. During this process, it’s important to confirm that the maintenance requirements are realistic and aligned with the equipment’s operational demands.
This includes evaluating scheduled maintenance tasks, such as lubrication, filter changes, and parts replacements, to ensure they fit within the operational schedule without causing excessive downtime.
Care plans should be practical, allowing operators to perform routine checks and minor repairs without specialized training. Effective maintenance strategies should also incorporate easy access to necessary tools and spare parts, facilitating timely interventions.
Regularly reviewing and updating these plans based on operational feedback and equipment performance can greatly enhance reliability.
By prioritizing maintenance and care, companies can prevent unexpected breakdowns, reduce repair costs, and extend the lifespan of their machinery, ultimately contributing to a more efficient and productive work environment.
A proactive approach to maintenance fosters a culture of care and responsibility among employees.
These checking points from FHOPE team are essential for guaranteeing that the equipment is in optimal condition before delivery, ultimately leading to enhanced production efficiency and product quality.
By thoroughly inspecting various aspects such as functionality, safety, HMI interfaces, performance under load, packaging quality, noise and vibration levels, data acquisition systems, and maintenance plans, companies can identify and rectify potential issues early on.
Proactive approach not only minimizes the risk of equipment failure post-delivery but also ensures that the machinery operates smoothly and reliably in a production environment. When all systems are verified and validated, operators can work with confidence, knowing that the equipment has been rigorously tested.
Reliability translates into higher output rates, reduced waste, and improved product consistency, which are critical for maintaining competitive advantages in the market. Ultimately, comprehensive pre -delivery checks foster customer satisfaction and trust, leading to long-term.