Coil Upenders: Improving Material Handling Efficiency and Safety in Heavy Industries
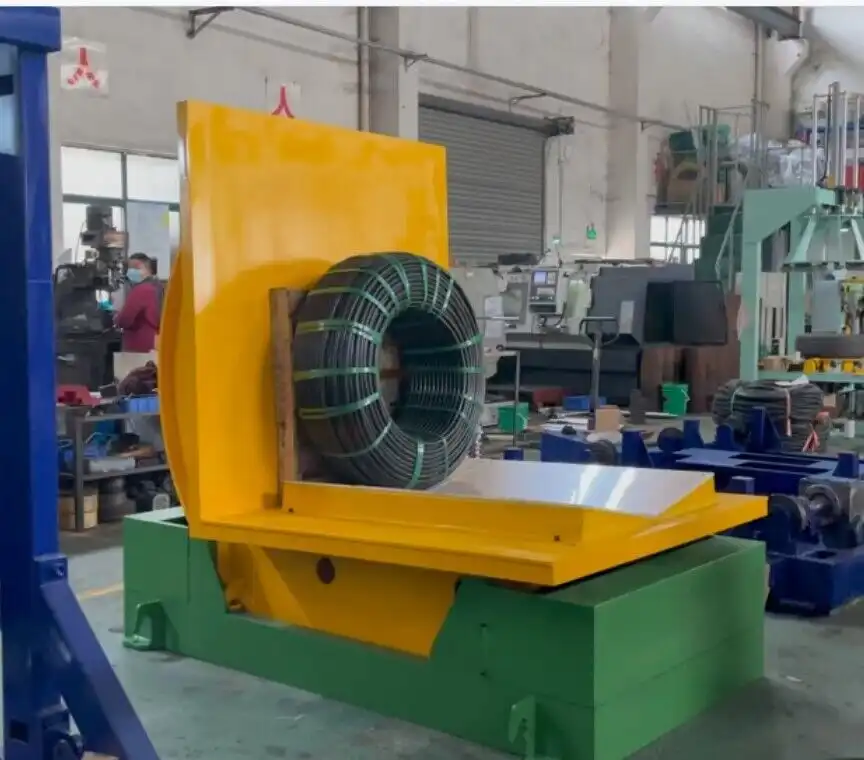
In today's demanding industrial environments, maximizing efficiency while ensuring worker safety is paramount. Automation continues to reshape operations, especially in heavy industries where handling large, bulky materials like metal coils presents significant challenges. Among the specialized material handling equipment designed to address these challenges, coil upenders (also known as coil tilters) are essential. This equipment is engineered to safely and efficiently rotate, tilt, or reposition heavy coils of steel, aluminum, copper, paper, or other materials, facilitating their movement and processing within manufacturing facilities.
This article examines the role of coil upenders in enhancing productivity, reducing operational downtime, improving workplace safety, and contributing to cost savings in heavy industrial applications. Understanding the capabilities and benefits of coil upenders can help operations managers and engineers make informed decisions about optimizing their material handling processes.
1. What is a Coil Upender?
A coil upender is a piece of industrial equipment specifically designed to reorient large, heavy coils, typically rotating them 90 degrees between horizontal and vertical positions. In many heavy industries, coils of materials like steel, aluminum, or paper arrive and are stored horizontally (eye-to-sky) but need to be tilted vertically (eye-to-wall) for processing, slitting, stamping, or shipment, or vice-versa.
Traditional methods for repositioning these coils often rely on overhead cranes with C-hooks or slings, or even manual prying and maneuvering. These methods can be time-consuming, pose significant safety risks to personnel, and potentially damage the coil edges or surfaces. Coil upenders provide a controlled, automated solution, minimizing manual intervention and reducing the associated risks and inefficiencies.
These machines are available in various designs and load capacities, utilizing mechanical or hydraulic systems to achieve smooth and secure rotation. Their primary function is consistent: to handle heavy coils safely and efficiently, integrating seamlessly into production workflows.
2. The Critical Role of Efficiency in Heavy Industry Material Handling
Operational efficiency in heavy industries directly impacts throughput, costs, and competitiveness. It involves optimizing resource utilization, minimizing waste, and ensuring smooth, uninterrupted workflows. Inefficient material handling, particularly for bulky items like metal coils, can create bottlenecks, lead to production delays, increase the risk of material damage, and inflate operational costs.
Coil upenders address these inefficiencies directly. By automating the coil tilting process, they significantly reduce the time required compared to manual or crane-based methods. A typical rotation cycle with an upender takes only a minute or two, whereas crane handling can be much slower and requires coordination between operators and ground personnel.
Key efficiency benefits include:
- Reduced Cycle Times: Faster rotation speeds up the transition of coils between storage, processing, and shipping stages.
- Minimized Downtime: Reliable, automated handling reduces delays caused by waiting for crane availability or addressing handling incidents.
- Optimized Labor Allocation: Fewer personnel are required for coil repositioning, freeing up workers for more complex or value-added tasks.
- Improved Workflow Integration: Upenders can be integrated with conveyors and other automated systems for seamless material flow.
2.1 Impact on Labor Costs
Manual or semi-manual coil rotation is labor-intensive and inherently risky. Coil upenders require minimal operator involvement – often just loading/unloading and initiating the cycle via controls. This reduction in dedicated handling labor translates directly into lower operational costs over the equipment's lifespan.
3. Enhancing Workplace Safety with Coil Tilters
Perhaps the most crucial benefit of using coil upenders is the significant improvement in workplace safety. Handling multi-ton coils inherently involves risks. Accidents related to dropped loads, crane malfunctions, or personnel being caught in pinch points during manual maneuvering can lead to severe injuries or fatalities.
Coil upenders mitigate these risks by providing a stable, controlled platform for rotation. Key safety features often include:
- Secure Clamping/Support: Robust platforms and sometimes clamping mechanisms hold the coil securely during rotation.
- Controlled Movement: Hydraulic or electro-mechanical drives ensure smooth, predictable tilting, preventing sudden shifts or drops.
- Remote Operation: Operators typically manage the upender from a safe distance using a control panel or pendant.
- Emergency Stops: Easily accessible E-stops can halt motion immediately if required.
- Limit Switches & Sensors: Prevent over-travel and ensure proper positioning.
3.1 Compliance with Safety Regulations
Implementing engineered solutions like coil upenders helps facilities comply with stringent occupational safety regulations, such as those mandated by OSHA (Occupational Safety and Health Administration) in the U.S. or equivalent bodies internationally (e.g., adhering to CE marking requirements in Europe). These regulations emphasize the need for safe material handling practices and equipment.
Beyond compliance, a safer work environment fosters better employee morale, reduces costs associated with accidents (worker compensation, insurance, downtime), and enhances the company's reputation.
4. Types of Coil Upenders and Common Applications
Coil upenders are available in several configurations, primarily differing in their drive mechanism and structure. Choosing the right type depends on factors like coil weight, size, handling frequency, and budget.
4.1 Mechanical Coil Upenders
Mechanical upenders typically use an electromechanical drive system (motor and gearbox) coupled with gears, chains, or screw jacks to achieve rotation. They are often robust and cost-effective for standard applications.
- Mechanism: Motor, gearbox, chain/sprocket or screw jack system.
- Pros: Generally lower initial cost, relatively simple maintenance.
- Cons: May offer less precise speed control compared to hydraulic systems; potentially higher wear on mechanical components under very heavy loads or high cycle rates.
- Applications: Suitable for many standard coil handling tasks in metal service centers, fabrication shops, and paper mills where extreme precision or very heavy loads aren't the primary concern.

4.2 Hydraulic Coil Upenders
Hydraulic coil upenders utilize hydraulic cylinders powered by a hydraulic power unit (HPU) to rotate the coil platform. They are known for providing smooth, highly controlled motion and handling very heavy loads.
- Mechanism: Hydraulic cylinders, hydraulic power unit (motor, pump, reservoir, valves).
- Pros: Excellent control over speed and positioning, high load capacity, smooth operation ideal for delicate materials, inherent overload protection.
- Cons: Higher initial cost, potential for hydraulic leaks (requires proper maintenance), HPU adds complexity.
- Applications: Preferred for very heavy coils (e.g., large steel or aluminum coils in mills), applications requiring precise positioning, or handling sensitive materials where smooth motion is critical.
4.3 Customized and Specialized Coil Upenders
Many manufacturers offer customization to meet specific operational needs. This can include:
- V-Saddle or Flat Platforms: To accommodate different coil shapes or protect surfaces.
- Powered Conveyors: Integrated conveyors on the loading/unloading platforms for automated integration.
- Specific Load Capacities and Sizes: Tailored dimensions and structural strength for unique coil parameters.
- 90-Degree or 180-Degree Rotation: While 90-degree tilters are most common, 180-degree inverters are also available for specific processes.
5. Integrating Coil Upenders into Automated Systems
Automation is a key driver in modern manufacturing and warehousing. Coil upenders are frequently integrated into larger automated material handling systems. They can act as crucial linking points between different stages of production or logistics, receiving coils from automated guided vehicles (AGVs) or conveyor lines, rotating them, and then feeding them onto the next process (e.g., slitting lines, stamping presses, packaging stations).
Integration typically involves:
- PLC Control: Programmable Logic Controllers (PLCs) manage the upender's operation and synchronize it with upstream and downstream equipment.
- Sensors: Photo-eyes or proximity sensors detect coil presence and position for automated loading/unloading and cycle initiation.
- Communication Protocols: Integration with Manufacturing Execution Systems (MES) or Warehouse Management Systems (WMS) for tracking and process control.
5.1 Data Acquisition and Process Monitoring
Modern coil handling equipment, including upenders, can incorporate sensors and connectivity (IIoT - Industrial Internet of Things) to provide valuable operational data. This data might include cycle counts, operating hours, fault diagnostics, and energy consumption. Analyzing this information allows for predictive maintenance scheduling, performance optimization, and better overall equipment effectiveness (OEE) tracking.
6. Analyzing Cost Savings and Return on Investment (ROI)
While investing in a coil upender requires an initial capital outlay, the long-term financial benefits often result in a favorable return on investment (ROI). Cost savings are realized through several areas:
- Reduced Labor Costs: As previously mentioned, automating the tilting process significantly cuts down on manual labor requirements for this specific task.
- Increased Throughput: Faster cycle times and reduced handling delays directly contribute to higher overall productivity and output.
- Minimized Material Damage: Controlled rotation prevents damage to coil edges and surfaces that can occur with improper crane or manual handling, reducing scrap rates and rework costs.
- Lower Accident-Related Costs: Preventing injuries reduces expenses associated with worker compensation, medical bills, insurance premium hikes, and lost workdays.
- Extended Equipment Lifespan (Cranes): Reducing the reliance on overhead cranes for routine tilting tasks can lessen wear and tear on crane components.
6.1 Durability and Maintenance Considerations
Industrial coil upenders are typically built for heavy-duty use and longevity. Constructed from robust steel frames and employing reliable drive systems, they require standard preventive maintenance. Routine checks often include lubrication of moving parts (gears, bearings), inspection of hydraulic systems (hoses, fluid levels) or electrical components, and verification of safety features. Following the manufacturer's recommended maintenance schedule ensures reliable operation and maximizes the equipment's service life, further enhancing its cost-effectiveness.
7. Selecting the Right Coil Upender for Your Application
Choosing the most suitable coil upender involves careful consideration of several factors specific to your operation:
- Coil Specifications:
- Maximum weight
- Maximum and minimum diameter
- Maximum and minimum width
- Material type (steel, aluminum, paper, etc. – impacts platform design)
- Handling Frequency: How many coils per shift or day need rotation? (Impacts choice between mechanical/hydraulic and necessary robustness)
- Operating Environment: Indoor/outdoor use, temperature, presence of corrosive elements.
- Loading/Unloading Method: How will coils be placed onto and removed from the upender? (Forklift, crane, conveyor – influences platform design and integration needs)
- Level of Automation Required: Standalone operation or integration into an automated line?
- Safety Requirements: Specific guarding, interlocks, or certifications needed.
- Budget: Balance initial cost with long-term operational benefits and total cost of ownership.
Consulting with reputable equipment manufacturers and potentially material handling consultants like those within organizations such as MHI (Material Handling Industry) can provide valuable insights during the selection process. Providing detailed application requirements will ensure the chosen coil tilter aligns perfectly with operational needs and delivers the expected improvements in efficiency and safety.
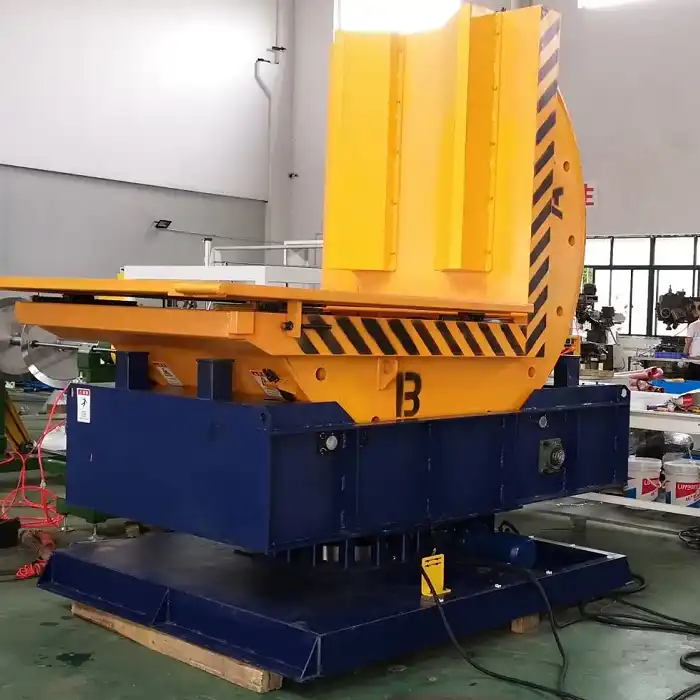
Conclusion
In heavy industries where efficient and safe handling of large coils is a daily necessity, coil upenders offer a robust and reliable engineering solution. By automating the rotation process, this equipment significantly enhances operational speed, reduces the risk of costly material damage, and drastically improves workplace safety compared to traditional methods. Furthermore, the reduction in manual labor and potential for integration into automated workflows contribute to lower operating costs and a strong return on investment.
As industries continue to prioritize automation, safety compliance, and operational efficiency, coil upenders remain a vital tool for facilities handling steel, aluminum, paper, and other coiled materials. Careful selection based on specific application parameters ensures that this equipment effectively streamlines coil handling processes, supporting competitiveness and operational excellence.