Maximizing ROI: Key Economic Benefits of Automated Aluminum Profile Packaging Lines
For manufacturers and fabricators working with aluminum extrusions, protecting profiles from damage during handling, storage, and transport is crucial. Manual packaging methods are often labor-intensive, inconsistent, and can lead to costly surface scratches or deformities. Investing in an aluminum profile bag packaging line offers a strategic solution, automating the process to deliver significant economic advantages through enhanced efficiency, reduced costs, and improved product quality. This article explores the tangible financial benefits of integrating this technology into your operations.
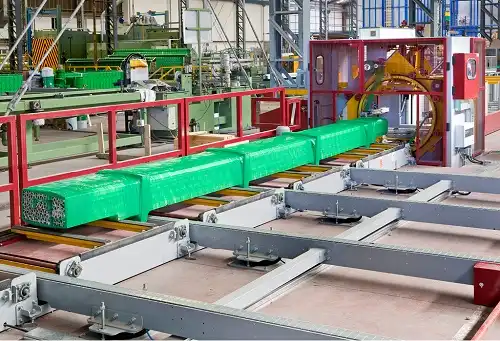
Understanding Automated Aluminum Profile Packaging
Automated aluminum profile packaging lines are designed specifically to handle the unique challenges of long, often complex-shaped extrusions. These systems typically wrap individual profiles or bundles in protective materials like polyethylene (PE) film, stretch wrap, or paper-based products. The process often involves:
- Infeed: Profiles are fed onto the line, either manually or via integrated conveyors from extrusion or finishing processes.
- Wrapping/Bagging: The machine automatically applies the chosen protective material, ensuring consistent coverage and tension. This might involve orbital stretch wrapping, side-sealed bagging, or spiral wrapping.
- Sealing/Cutting: The packaging material is automatically cut and sealed to secure the profile.
- Outfeed: Packaged profiles exit the line, ready for bundling, stacking, or direct shipment.
This automation replaces manual wrapping, taping, and handling, streamlining the end-of-line process.
Boosting Operational Efficiency and Throughput
Manual packaging is a common bottleneck. An automated line dramatically increases packaging speed and consistency.
- Increased Speed: Machines operate significantly faster than manual labor, increasing the throughput of finished profiles per hour or shift.
- Reduced Labor Dependency: Automation minimizes the need for manual wrappers, freeing up personnel for higher-value tasks and mitigating challenges related to labor shortages or repetitive strain injuries.
- Consistent Quality: Automated systems apply packaging materials uniformly every time, eliminating variations common in manual processes.
This boost in efficiency translates directly to faster order fulfillment and an increased capacity to handle larger production volumes without proportional increases in labor costs.
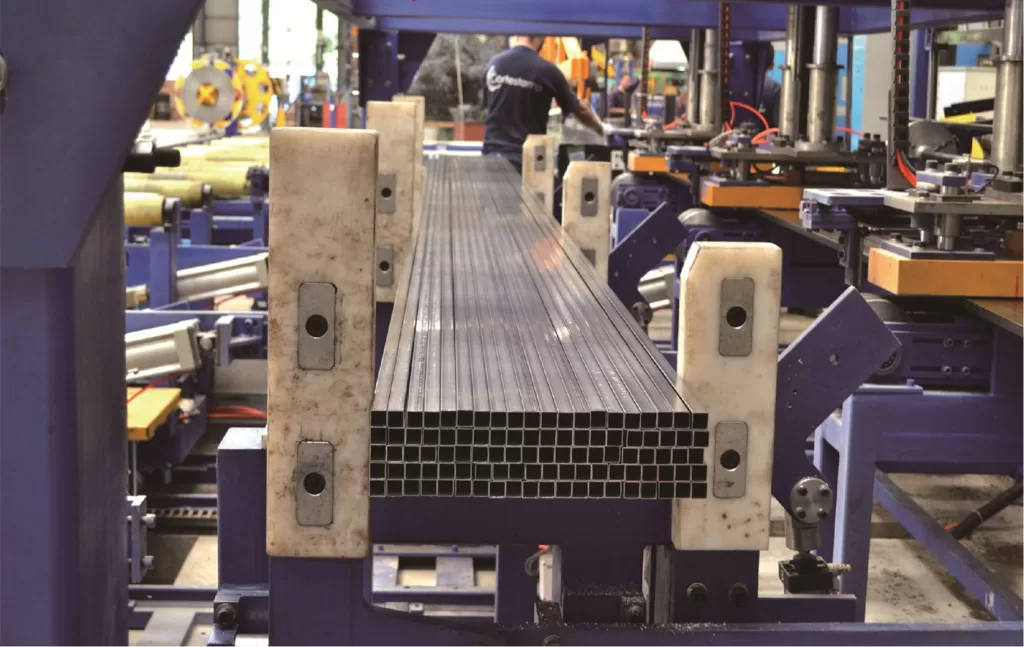
Significant Cost Reduction and Strong ROI
The financial justification for investing in automated profile packaging is compelling, primarily through direct and indirect cost savings:
- Labor Savings: Reduced manual handling directly lowers labor costs, including wages, benefits, training, and potential injury-related expenses.
- Material Optimization: Automated systems use precise amounts of film or paper, minimizing material waste compared to inconsistent manual application.
- Reduced Product Damage: Superior, consistent protection significantly lowers the incidence of scratches, dents, and contamination during handling and shipping. This reduces costs associated with scrap, rework, customer returns, and damage claims.
- Lower Overhead: Streamlined operations can lead to reduced needs for packaging floor space and potentially lower energy consumption compared to multiple manual stations.
While requiring an initial capital investment, these lines typically offer a strong Return on Investment (ROI) through accumulated savings, often realizing payback within a few years depending on volume and labor rates.
Enhancing Product Protection and Quality Preservation
Aluminum profiles, especially those with decorative or architectural finishes (like powder coating or anodizing), are highly susceptible to surface damage.
- Scratch and Dent Prevention: Consistent, tight wrapping shields surfaces from abrasion during movement and stacking.
- Contamination Control: Sealed packaging protects profiles from dust, dirt, moisture, and other contaminants during storage and transit.
- Maintaining Appearance: Delivering pristine, professionally packaged products reinforces quality perception and customer satisfaction.
Enhanced protection ensures extrusions arrive at the customer or the next manufacturing stage in optimal condition, preserving their value and function.
Sustainability and Environmental Considerations
Modern packaging lines contribute to sustainability goals:
- Material Reduction: Precise application minimizes the consumption of plastic films or paper wrap.
- Recyclability: Many packaging films used (like PE) are recyclable, supporting circular economy initiatives (check local recycling capabilities).
- Reduced Waste from Damage: Less product damage means less material waste from scrapped or rejected profiles.
Demonstrating efficient and responsible packaging practices can also enhance a company's environmental credentials.
Versatility for Diverse Profile Requirements
Automated packaging lines can often be configured to handle a wide range of profile shapes, sizes, and lengths.
- Adaptability: Systems can accommodate simple shapes to complex, multi-hollow extrusions.
- Bundling Options: Many lines can wrap individual profiles or create secure bundles for easier handling.
- Material Flexibility: Options often exist for using different types or thicknesses of protective films or papers based on specific protection needs.
This versatility ensures the investment remains valuable even as product mixes change.
Improving Supply Chain Management and Logistics
Reliable, protective packaging smooths the entire logistics process.
- Reduced Shipping Issues: Fewer damage claims simplify logistics and reduce associated administrative burdens.
- Easier Handling: Well-packaged profiles or bundles are often easier and safer to load, unload, and store.
- Predictable Output: Consistent packaging speeds contribute to more reliable production scheduling and delivery times.
This leads to a more efficient and less costly supply chain from the factory floor to the end-user.
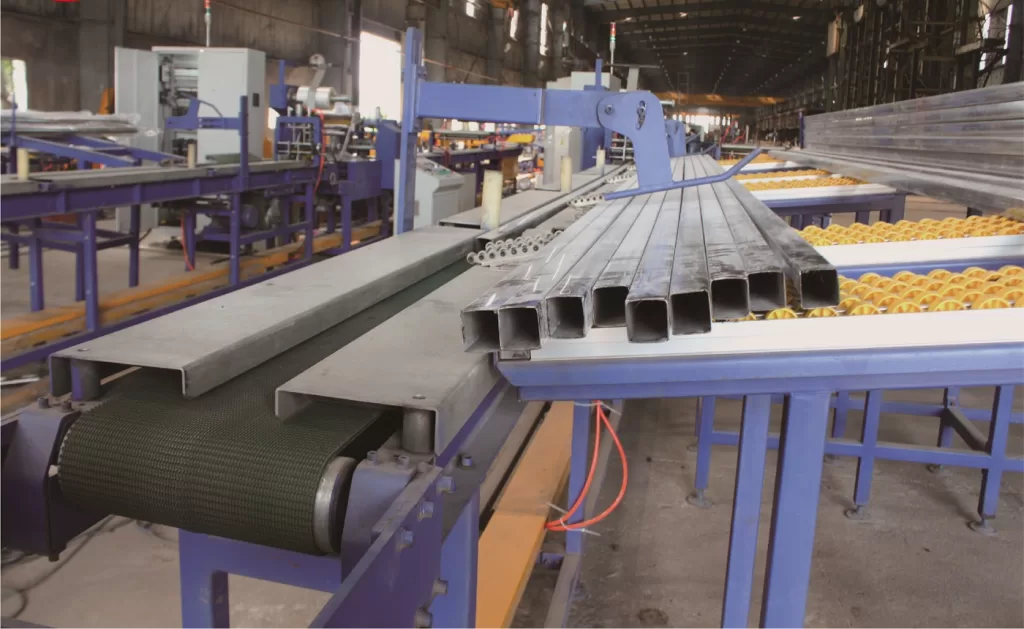
Enhancing Brand Reputation and Customer Loyalty
The way products are presented matters.
- Professionalism: High-quality packaging signals attention to detail and product care.
- Customer Satisfaction: Receiving undamaged, clean profiles builds trust and encourages repeat business.
- Competitive Differentiation: Superior packaging can be a key differentiator in markets where product quality and reliability are paramount.
Investing in packaging is an investment in brand image.
Meeting Industry Standards and Safety Goals
Automated packaging can help meet various requirements:
- Safety: Reducing manual handling lowers the risk of worker injuries associated with repetitive motion or handling long/heavy profiles.
- Quality Standards: Consistent protection helps meet customer or industry-specific standards for product condition upon arrival (e.g., standards set by organizations like the Aluminum Extruders Council - AEC).
Future-Proofing Your Operations
Automation is key to staying competitive in manufacturing.
- Scalability: Automated lines allow manufacturers to scale production up or down more easily in response to market demand.
- Technology Integration: These systems can often be integrated with upstream (extrusion, finishing) and downstream (labeling, palletizing) automation.
- Adapting to Labor Markets: Automation provides resilience against fluctuating labor availability and costs.
Investing in automation positions a company for greater efficiency and adaptability in the future.
Conclusion: A Sound Economic Decision
Investing in an aluminum profile bag packaging line transcends simple cost-cutting; it's a strategic move toward greater operational efficiency, enhanced product quality, and improved profitability. By automating this critical process, aluminum extruders and fabricators can significantly reduce labor and material costs, minimize costly damage, streamline their supply chain, and bolster their brand reputation. In a competitive global market, leveraging automation for packaging provides a clear pathway to a stronger bottom line and sustainable long-term growth.