Does Shape of the Coil Matter for Coil Upender Operation?
I have seen many overlooked details in my years of working with coil upenders. People often ignore coil shape, but this aspect can change the entire operation and final outcomes.
Coil shape does matter because it influences how the upender grips and rotates the load. If the coil is not round, we may need different supports or safety features. This can prevent slippage and ensure a smooth flip. I have learned that each variation in coil shape creates handling demands.
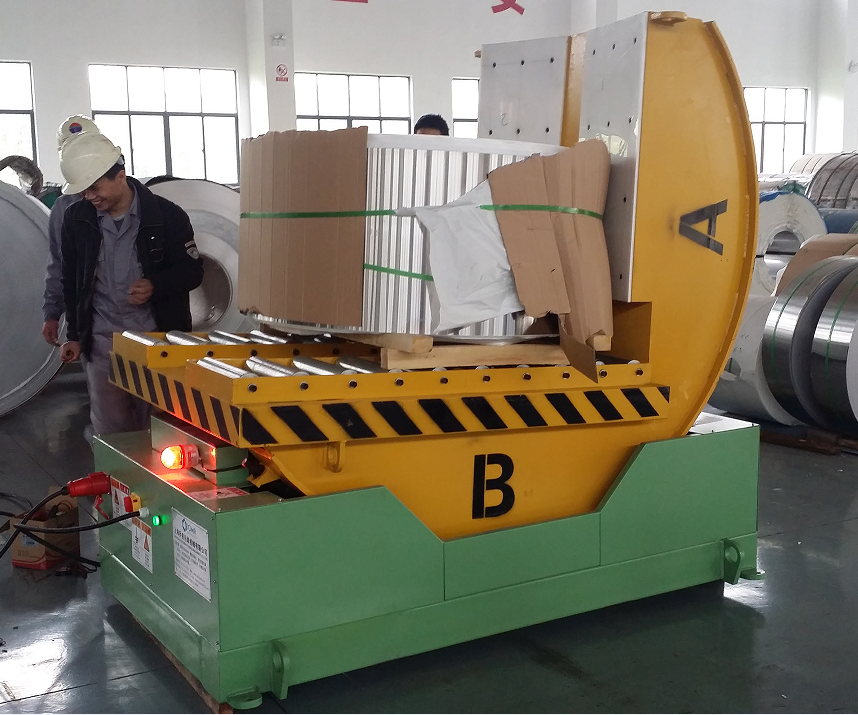
I have worked with various coil shapes, and each one tells a different story. Some are flatter, some are slightly oval, and others have edges that are not uniform. My goal has always been to find a safe and effective way to flip these coils. When I first started in coil handling, I focused only on the weight. Over time, I realized that shape also adds complexity. I now believe that shape is just as critical as size and mass. This realization has helped me reduce downtime and avoid accidents in our packaging line. I often tell others that shape can disrupt the flipping process in unexpected ways.
How Does Coil Shape Influence the Efficiency of Upender Operations?
I notice that efficiency can drop when a coil is not perfectly round. The upender may need extra setup time, which slows production. I also see that shape affects positioning.
Coil shape impacts alignment, gripping angles, and support placement. If the coil has irregular contours, the upender might need customized cradles or clamps. This can affect cycle times and labor involvement. I have found that a consistent, well-planned approach to coil shape can boost efficiency and significantly reduce operational issues.
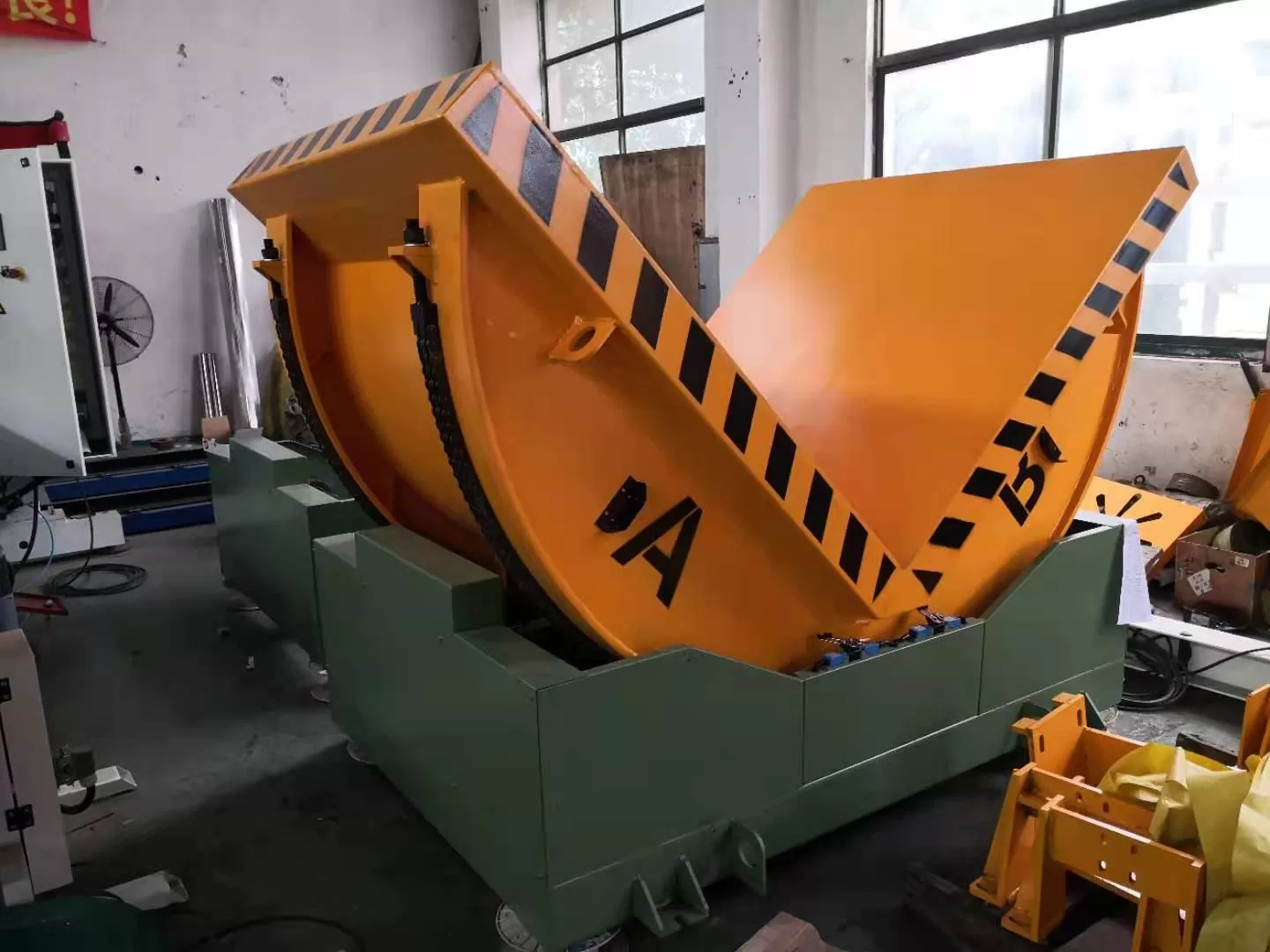
Understanding Coil Shape in Upender Efficiency
Coil shape is more than just a visual detail. I have learned that even slight deviations from perfect roundness can alter how the upender grips and lifts the load. When the coil is conical or has an uneven winding pattern, it can shift during the flipping process. This shift might lead to extra strain on the upender's motor or hydraulics. It can also require additional handling steps to keep everything stable.
I divide coil shape considerations into three main categories:
- Round or near-round coils: These are generally simpler to handle because the contact points are more predictable.
- Elliptical or oval coils: These shapes need specialized supports and a more careful approach to avoid rolling or unexpected movements.
- Irregular profiles: These might have protrusions or uneven edges that create a challenge for consistent flipping.
Coil Shape | Key Challenge | Potential Solution |
---|---|---|
Round | Consistent contact | Standard cradle or clamp |
Oval | Risk of rolling | Custom supports or adjustable arms |
Irregular | Unstable edges | Tailored fixtures and sensors |
I always try to remind others that a coil with an unusual shape does not have to be a headache. Proper planning and the right design features can solve most problems. In some cases, adding sensors or upgrading to a more powerful upender can help. I have also seen how automated control systems adjust speeds and angles to match the shape. This helps create a safer and more efficient process. In the end, the shape of the coil sets the stage for our entire operation.
What Role Does Coil Geometry Play in Ensuring Upender Stability?
I always pay attention to stability because an unbalanced coil can cause the upender to wobble. When geometry is off, the entire flipping sequence can become risky. I take precautions.
Coil geometry affects weight distribution. If the coil is not centered, the upender may shift or tilt. I have seen minor geometry issues lead to major system strain. Simple solutions include repositioning the load or installing adjustable clamps. This helps keep the upender balanced, which lowers the risk of accidents.
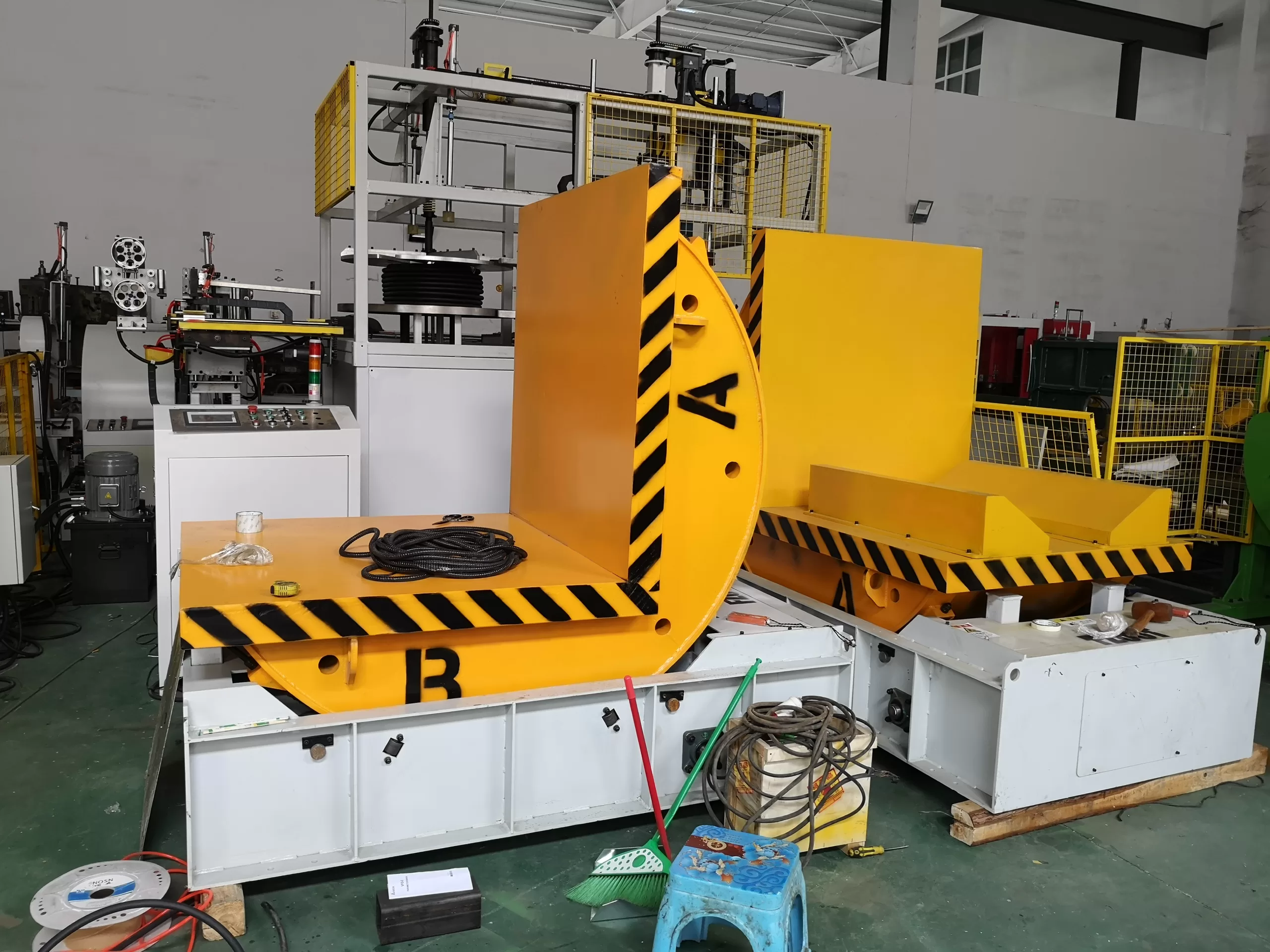
Balancing Weight and Form for Safe Upending
I have learned that stability depends on how the coil's weight is distributed. When the coil is uniform, the upender can flip it smoothly. But when there is a discrepancy in thickness, diameter, or overall form, things can get tricky. One side might be heavier than the other. That can cause the upender to rock during rotation. I have tried several methods to address this issue.
First, I evaluate the coil's geometry to see if it has a thicker core or an uneven wrap. If so, I adjust the positioning points on the upender bed. Sometimes, that means moving the coil a few inches to one side. That small shift can keep the center of gravity lined up with the upender's pivot. I also check if the coil has any dents or flattened areas that can affect stability.
Second, I consider using support beams or adjustable brackets. These devices help secure odd shapes so the coil will not roll or shift in mid-flip. I once worked with a coil that was slightly deformed. We attached removable braces to stabilize the coil, and it flipped without a hitch.
Finally, I am a fan of integrated safety sensors. These sensors can detect when the coil is off balance. The system can pause the flip or adjust the angle to prevent tipping. This extra layer of security is especially helpful when handling expensive or fragile materials. In my experience, the right combination of geometry assessment, manual adjustments, and automatic monitoring can turn a potentially wobbly flip into a smooth operation that keeps everyone safe.
Which Upender Design is Best Suited for Various Coil Shapes?
I have experimented with different upender designs, from basic mechanical systems to more advanced hydraulic models. Each design has strengths and limitations, especially when it comes to handling coil shapes.
Some upenders use a simple pivot. Others rely on hydraulic cylinders for better control. My experience suggests that heavier, irregular coils do best with hydraulic models, since they can adjust force and speed. Mechanical units work well for standard shapes and moderate loads. Both can be effective when configured properly.
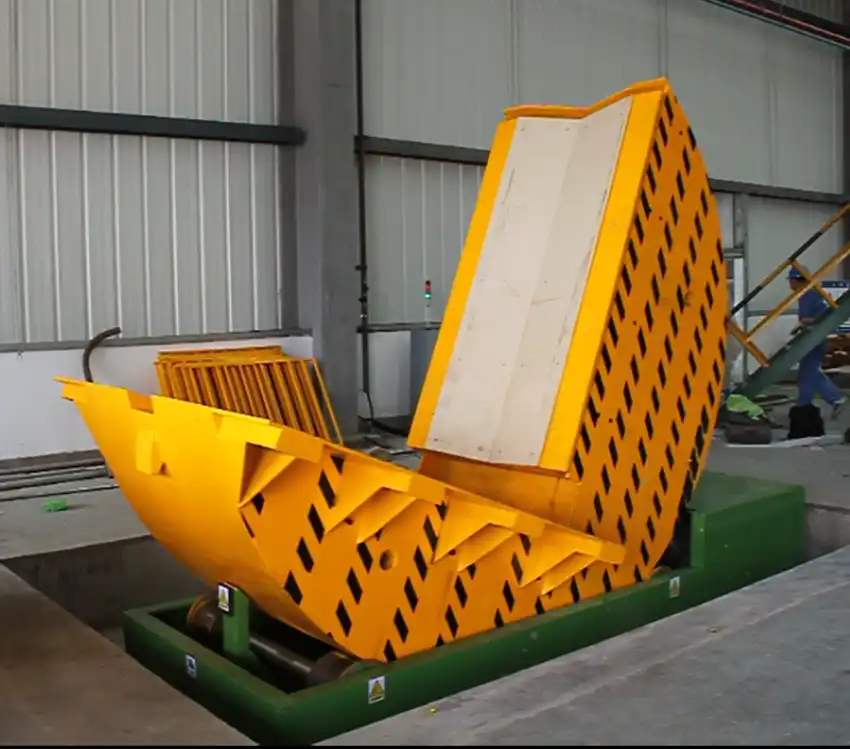
Matching Upender Design to Coil Profiles
I have seen many operations try to use one type of upender for every coil shape. That can work temporarily, but it often leads to inefficiency. In my view, choosing the right upender design starts with identifying the coil's dimensions, weight, and shape complexity. For lighter, fairly uniform coils, a mechanical upender can be a cost-effective choice. The mechanical approach often uses a gearbox or chain drive that can handle moderate loads. It flips the coil at a set speed, which is fine for smaller or standard shapes.
When I deal with heavier or more irregular coils, I usually turn to hydraulic upenders. These machines let me control the tilt angle and speed more precisely. That is especially helpful if the coil is large or has off-balance sections. With hydraulic cylinders, I can pause halfway if I sense any shifting. I can also apply more force if the coil has stuck edges or needs an initial push. This flexibility allows me to adapt on the fly.
I also think about additional features. Some upenders have rotating platforms that let me reposition the coil after flipping. Others have built-in sensors that detect unbalanced loads. I once worked on a project that required flipping coils with protruding sections. The chosen upender had adjustable clamps that could accommodate these protrusions. That small feature prevented surface damage and made the flipping smoother.
In the end, I choose the design by balancing cost, reliability, and coil shape requirements. If I need simple flips with minimal variations, I pick a mechanical option. If I handle a range of shapes and weights, I invest in a hydraulic model with extra safety measures. This approach helps me avoid downtime and keep each flip predictable, no matter the coil's profile.
Conclusion
In my experience, coil shape matters a lot in every aspect of upender operation. When we address geometry, weight distribution, and the right upender design, we improve safety and efficiency. A deliberate plan makes flipping easier. That is the key to smoother workflows and a more reliable packaging process.