Digital Transformation: The Future of Automated Packaging in the Steel Industry
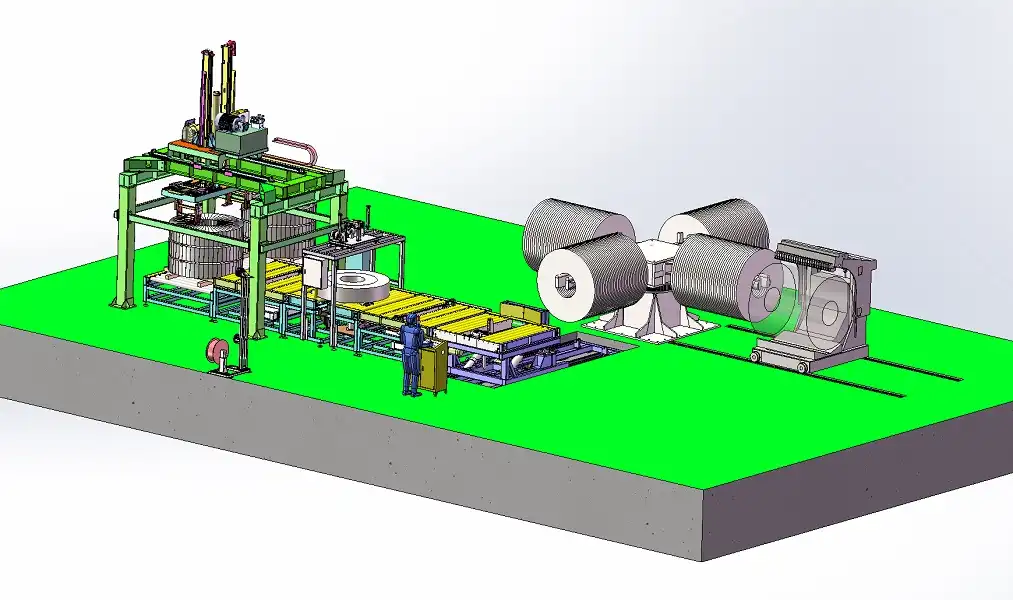
In a world driven by digital innovation, the steel industry is undergoing a significant transformation. Steel companies are increasingly adopting automation to navigate the complex demands of modern manufacturing. Among the most impactful advancements is automated packaging, a critical solution for boosting efficiency, minimizing waste, and enhancing worker safety. In an industry where precision, speed, and safety are non-negotiable, transitioning from manual packaging to automated steel packaging systems represents a vital investment in the future resilience and competitiveness of steel production.
This article explores the core elements of digital transformation within automated packaging for steel products, detailing the substantial benefits, addressing implementation challenges, and examining the role of cutting-edge technology in shaping the future of this essential industrial process.
1. Introduction to Digital Transformation in the Steel Industry
Digital transformation involves integrating digital technologies to fundamentally change how businesses operate and deliver value. Within the steel sector, this transformation encompasses everything from advanced data analytics and predictive maintenance for production lines to sophisticated automated packaging systems designed to streamline the handling, packaging, and shipping of heavy, high-value products like steel coils, sheets, and long products.
Automated steel packaging leverages technologies such as machine learning (ML), artificial intelligence (AI), the Internet of Things (IoT), and advanced robotics to create highly efficient, reliable workflows. For steel manufacturers, adopting these technologies translates into reduced bottlenecks, optimized labor allocation, improved safety records, and the ability to meet customer demands with greater speed and accuracy. Implementing these systems requires a strategic approach, understanding the unique requirements of steel products, and a commitment to continuous improvement and long-term efficiency gains.
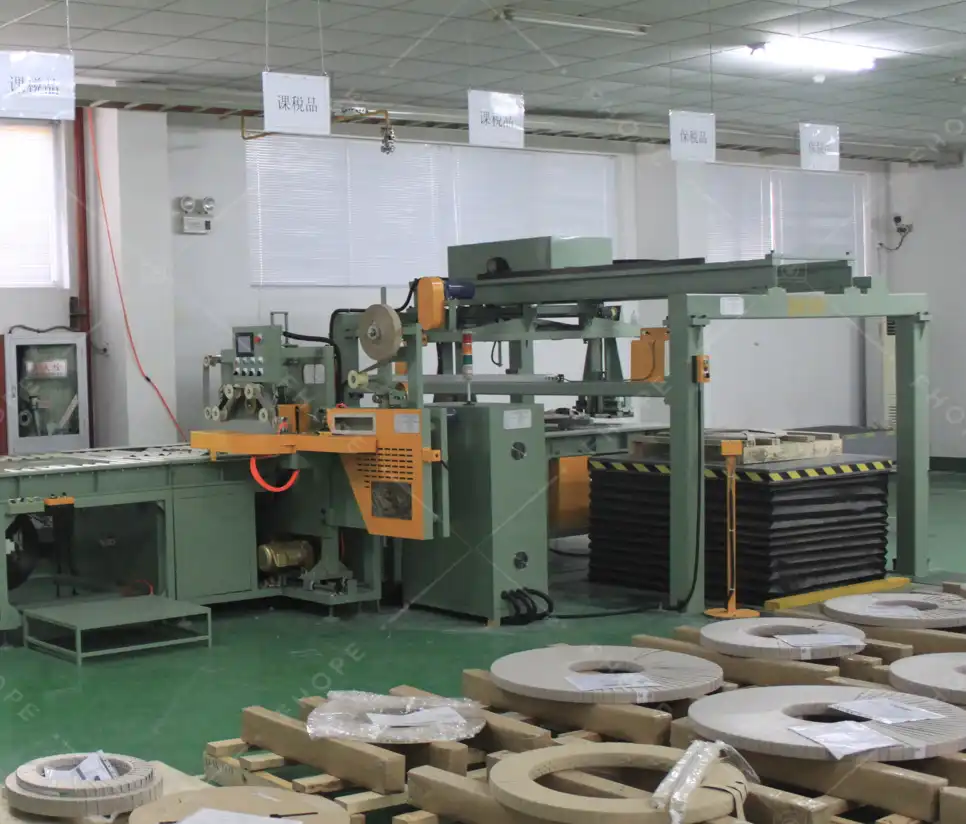
2. Why Automation is Essential in Steel Packaging
In today's competitive landscape, maximizing productivity and operational efficiency is paramount. The need for automation in steel packaging has become increasingly critical. Traditional manual packaging methods for steel products are often:
- Labor-intensive: Requiring significant manpower for physically demanding tasks.
- Hazardous: Exposing workers to risks associated with heavy lifting and repetitive motion.
- Inconsistent: Prone to human error, leading to variations in package quality and potential product damage.
- Slow: Creating bottlenecks that delay shipments and impact overall plant throughput.
Automated packaging systems provide a robust solution to these challenges. They are engineered to handle the specific demands of heavy, often irregularly shaped steel products (like coils, plates, bars, and tubes) safely and efficiently.
Key advantages include:
- Consistent Quality: Automation ensures uniform application of protective materials (e.g., VCI film, wrapping) and secure strapping or banding, minimizing transit damage.
- Reduced Errors: Automated processes significantly decrease handling mistakes and packaging inconsistencies common in manual operations.
- High Throughput: Systems operate continuously at high speeds, managing large volumes effectively and reducing lead times.
- Enhanced Flexibility: Modern systems can often adapt to various product dimensions and packaging specifications with minimal downtime.
As steel companies strive for a competitive edge, automation in packaging is an indispensable asset, transforming a traditionally challenging process into a streamlined, efficient operation aligned with modern manufacturing best practices.
3. Key Technologies Driving Digital Transformation in Packaging
The digital revolution in steel packaging is powered by a convergence of AI, IoT, and advanced robotics. These technologies work synergistically to enhance efficiency, safety, and data-driven decision-making.
3.1 Artificial Intelligence (AI) and Machine Learning (ML)
AI and ML algorithms analyze operational data to optimize packaging processes. Key applications include:
- Predictive Maintenance: Anticipating equipment failures before they occur, minimizing costly downtime.
- Process Optimization: Adjusting machine parameters in real-time (e.g., wrapping tension, strapping placement) based on product type and sensor feedback for optimal material usage and package integrity.
- Quality Control: Utilizing vision systems powered by AI to detect packaging defects or inconsistencies automatically.
3.2 Internet of Things (IoT)
IoT sensors embedded within packaging machinery enable real-time monitoring and data collection. This provides visibility into:
- Operational Performance: Tracking key metrics like cycle times, material consumption, and throughput.
- Equipment Health: Monitoring parameters such as temperature, vibration, and pressure to identify potential issues proactively.
- Remote Management: Allowing supervisors to monitor and manage packaging lines remotely, enhancing operational flexibility.
3.3 Advanced Robotics
Robotics forms the core of physical automated packaging tasks, handling heavy and cumbersome steel products with precision and reliability. Applications include:
- Material Handling: Robots safely lift, orient, and transport coils, sheets, or bundles to and from the packaging line.
- Wrapping and Strapping: Robotic arms precisely apply protective wrapping materials and secure steel strapping or banding.
- Labeling and Palletizing: Automating the application of labels and the stacking of finished packages onto pallets for shipment. Robotics significantly enhances safety by removing personnel from hazardous tasks and dramatically increases packaging speed and consistency.
4. The Benefits of Automated Packaging in Steel Manufacturing
Implementing automated packaging systems yields numerous benefits for steel manufacturers, directly impacting the bottom line and operational excellence.
4.1 Enhanced Worker Safety
Manual packaging of heavy steel products poses significant ergonomic and safety risks. Automation removes workers from strenuous lifting, repetitive motions, and potentially hazardous areas around moving equipment, drastically reducing the risk of injuries and creating a safer work environment.
4.2 Reduced Operational Costs
Automation drives cost savings through:
- Labor Optimization: Reducing the need for manual labor in repetitive packaging tasks allows staff to focus on oversight, quality control, and maintenance.
- Material Efficiency: Precise application of packaging materials (like stretch film or VCI paper) minimizes waste compared to manual methods.
- Reduced Product Damage: Consistent, secure packaging lowers the incidence of damage during handling and transit, reducing costs associated with returns and replacements.
4.3 Consistent and Improved Product Quality
Automated systems execute packaging tasks with high precision and repeatability, ensuring every product is packaged according to predefined standards. This uniformity enhances product protection, meets customer expectations consistently, and upholds the manufacturer's quality reputation.
5. Addressing Industry Challenges Through Automation
The steel industry faces specific packaging and logistics challenges that automation is uniquely positioned to solve.
5.1 Handling Irregular Shapes and Sizes
Steel products come in diverse forms – coils of varying widths and diameters, long structural beams, large plates, bundles of tubes. Manual packaging struggles to adapt efficiently. Automated systems, often equipped with sensors and adaptable programming, can dynamically adjust to different product dimensions, applying custom-fit packaging solutions efficiently and consistently.
5.2 Minimizing Damage During Transit
Secure packaging is crucial to prevent damage to heavy steel products during shipping and handling. Automated packaging lines utilize techniques like high-tension strapping, robust wrapping, and the application of edge protectors or other reinforcements with precision, ensuring load stability and significantly reducing the risk of costly transit damage.
5.3 Boosting Speed and Productivity
Meeting tight production schedules and customer delivery deadlines requires high packaging throughput. Automated packaging machines operate faster and more continuously than manual processes, significantly increasing the volume of products packaged per shift. This boost in speed alleviates bottlenecks and shortens overall order fulfillment times.
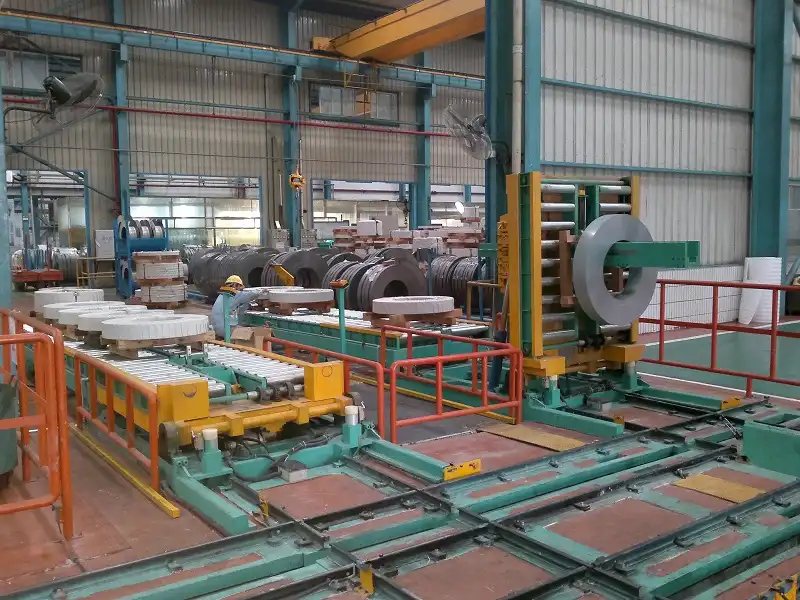
6. The Role of Data Analytics in Optimizing Automated Packaging
The digital transformation of packaging generates vast amounts of data. Leveraging data analytics is key to unlocking the full potential of automated systems.
6.1 Predictive Maintenance
Analyzing sensor data (vibration, temperature, cycle counts) allows maintenance teams to predict potential equipment failures and schedule preventative maintenance proactively. This minimizes unplanned downtime, extends machinery lifespan, and reduces overall maintenance costs.
6.2 Operational Efficiency Insights
Real-time data on cycle times, material consumption per package, and equipment uptime provides managers with actionable insights. Identifying bottlenecks, optimizing machine settings, and tracking performance trends allow for continuous improvement and maximization of packaging line efficiency.
6.3 Enhanced Quality Control
Data analytics enables continuous monitoring of packaging quality parameters. Tracking metrics like strap tension consistency, wrap integrity, or label placement accuracy helps ensure that every package meets stringent quality standards, improving customer satisfaction and reducing quality-related issues.
These data-driven practices elevate automated packaging from a simple operational function to a strategic tool for enhancing overall manufacturing performance.
7. How Digital Transformation Enhances Supply Chain Management in Steel Packaging
Automated packaging systems integrate seamlessly into the broader supply chain, enhancing visibility, efficiency, and responsiveness.
7.1 Improved Inventory Tracking
Automated lines can integrate with Warehouse Management Systems (WMS) or Enterprise Resource Planning (ERP) systems. This allows for real-time tracking of packaging material consumption and finished goods output, improving inventory accuracy, preventing material stockouts, and optimizing procurement.
7.2 Optimized Distribution Logistics
Accurate, consistent packaging and automated labeling (including barcodes or RFID tags) improve traceability throughout the distribution process. Standardized package dimensions can optimize truck or container loading. This leads to faster loading/unloading times, fewer shipping errors, and smoother logistics operations.
7.3 Cost-Effective Logistics
Efficient packaging directly impacts logistics costs. Reduced product damage minimizes returns and replacements. Optimized packaging can sometimes allow for better space utilization in transport, potentially lowering freight costs. Overall, automation contributes to a more streamlined and cost-effective supply chain from the plant floor to the end customer.
8. Sustainability Through Automated Steel Packaging
Sustainability is a growing focus for the steel industry. Digital transformation in automated packaging provides significant opportunities to implement more environmentally responsible practices.
8.1 Reduction in Material Waste
Automated systems apply packaging materials like stretch film, VCI paper, and strapping with high precision, using only the necessary amount for secure packaging. This minimizes material consumption and waste compared to less controlled manual methods. Some systems are also compatible with thinner gauge, high-performance films or recyclable materials.
8.2 Energy-Efficient Operations
Modern automated packaging equipment is often designed with energy efficiency in mind, incorporating features like variable speed drives and optimized motor controls. Data analytics can further identify opportunities to optimize energy usage during operation, reducing the overall carbon footprint of the packaging process.
8.3 Supporting Circular Economy Goals
By optimizing material use and enabling the potential use of recyclable packaging materials, automation supports the move towards a circular economy. Data on material performance can help select durable and recyclable options, minimizing landfill waste.
9. Challenges and Considerations in Implementing Automated Packaging
While highly beneficial, transitioning to automated packaging involves considerations and potential challenges:
9.1 Initial Investment Costs
The purchase and installation of sophisticated automated packaging systems represent a significant capital investment. Steel companies need to conduct thorough ROI analyses, considering long-term savings in labor, materials, safety improvements, and increased throughput to justify the upfront cost.
9.2 Employee Training and Skill Development
Operating and maintaining automated equipment requires new skill sets. Companies must invest in comprehensive training programs to upskill their workforce in areas like machine operation, troubleshooting, basic maintenance, and understanding automation software interfaces. Change management is crucial for smooth adoption.
9.3 Integration with Existing Infrastructure and Systems
Integrating new automated lines with existing plant layouts, upstream processes, and IT systems (like MES or ERP) can be complex. Careful planning, potentially involving phased implementation, is essential to ensure seamless integration without disrupting ongoing production. Collaboration between equipment suppliers, system integrators, and internal teams is key.
10. The Future of Automated Packaging in the Steel Industry
The trajectory for automated packaging in the steel industry points towards even greater sophistication and integration, driven by ongoing technological advancements.
10.1 Enhanced Predictive Analytics and AI Optimization
Future systems will leverage AI not just for maintenance but for holistic process optimization. Self-adjusting machines will fine-tune parameters based on real-time sensor feedback, material properties, and even downstream logistics data for optimal performance and minimal waste.
10.2 Greater Customization and Flexibility
Advancements in robotics and software will enable systems to handle an even wider range of product variations and complex packaging requirements with minimal changeover time. Smart packaging features, like embedded sensors for tracking environmental conditions during transit, may become more integrated.
10.3 Collaborative Robotics (Cobots)
Cobots, designed to work safely alongside humans, will likely see increased adoption. They can automate specific physically demanding or repetitive tasks within a semi-automated line, offering a flexible automation solution for operations not requiring full automation.
10.4 Integration with Digital Twins
Creating virtual replicas (digital twins) of packaging lines will allow for simulation, optimization, and remote troubleshooting before implementing changes in the physical world, speeding up commissioning and improvement cycles.

11. Conclusion: Embracing Digital Transformation for a Competitive Edge
The adoption of automated packaging is a cornerstone of digital transformation in the modern steel industry. Offering tangible benefits in safety, operational efficiency, cost reduction, quality consistency, and sustainability, automation provides a clear competitive advantage in a demanding global market. As technologies like AI, IoT, and robotics continue to mature, their integration into packaging processes will unlock further potential for innovation and optimization.
Steel manufacturers that proactively embrace automation and navigate the implementation challenges position themselves for future success. By leveraging data and advanced technology, they can achieve new levels of productivity, reliability, and environmental stewardship, ensuring they remain leaders in an industry constantly being reshaped by digital innovation. Automated packaging is no longer just an option; it's a strategic imperative for a resilient and competitive future in steel manufacturing.

Get Your Best Solution !