Customizable Die and Mold Turners: What Options Are Available?

Innovation thrives on flexibility, and in the realm of die and mold turners, customization is no longer a luxury—it’s a necessity. Manufacturers today are seeking solutions tailored to their unique needs, combining efficiency, safety, and precision. As someone deeply entrenched in this industry, I’ve seen firsthand how businesses leverage customization to maximize their operational potential.
Customization isn’t just about having more options; it’s about addressing specific challenges. Whether it’s adapting to diverse mold sizes, increasing automation levels, or meeting stringent safety standards, customizable die and mold turners hold the key to unlocking improved performance.
When I first started researching customizable turners, I was overwhelmed by the sheer variety of options available. From advanced rotational mechanisms to integrated digital controls, these machines cater to industries that demand both flexibility and robustness. I realized that understanding the available options required breaking down the features, applications, and benefits into digestible insights.
[Claim]
Customizable die and mold turners offer solutions for diverse industrial challenges, enhancing efficiency, safety, and precision through tailored designs.
1. What Are the Primary Customization Options for Die and Mold Turners?
1.1 Tailored Rotational Capacities
Every operation has unique requirements, and one size doesn’t fit all. Customizable die and mold turners allow manufacturers to define rotational capacities to suit their processes. For example, industries handling larger molds often need devices with higher load-bearing capabilities. Adjustable rotation angles and speeds ensure precision during flipping, safeguarding against mold damage.
1.2 Enhanced Load Capacities with Modular Designs
When it comes to heavy-duty molds, load capacity is paramount. Modern die and mold turners can be customized with modular designs that support loads ranging from 500 kg to 50 tons. Below is a table comparing standard and advanced capacities for various industries:
Industry | Standard Capacity (kg) | Advanced Capacity (kg) |
---|---|---|
Automotive | 1,000 | 20,000 |
Aerospace | 2,500 | 30,000 |
Heavy Machinery | 5,000 | 50,000 |
These modular solutions also integrate seamlessly into existing production lines, minimizing downtime.
1.3 Control System Integration for Precision
Precision is non-negotiable in industries such as automotive and aerospace manufacturing. Custom turners offer integration with control systems like PLCs (Programmable Logic Controllers) or HMI (Human-Machine Interfaces). These systems provide real-time feedback and allow for programmable operations, ensuring repeatability and accuracy across batches.
1.4 Durability and Longevity Through Material Selection
Customizable die and mold turners can be built using specific materials to withstand wear and tear. For example, industries with corrosive environments often opt for stainless steel components, while high-load industries prefer reinforced alloy steel. Below is a table showing the benefits of material customization:
Material | Key Benefits | Common Use Cases |
---|---|---|
Stainless Steel | Corrosion resistance | Chemical manufacturing |
Reinforced Alloy Steel | High load tolerance | Heavy machinery production |
Aluminum Alloys | Lightweight and durable | Aerospace components |
By customizing materials, manufacturers can ensure their machines perform optimally under specific conditions.
1.5 Fact or Fiction?
- True: Modular designs in die and mold turners allow manufacturers to expand load capacities as needed.
- False: All die and mold turners are equipped with standardized control systems, leaving no room for customization.
Let me know if you’re ready for the next sections!

2. How Can Advanced Automation Enhance Operational Efficiency?
2.1 Integration of Smart Sensors
Advanced automation begins with smart sensors that monitor every aspect of the turning process. Customizable die and mold turners can include load sensors, angle detectors, and temperature monitors, all of which contribute to seamless operations. By leveraging this data, manufacturers can identify inefficiencies and improve overall productivity.
Smart sensors also minimize human intervention, reducing the risk of errors and ensuring that even the most intricate processes are executed with precision.
2.2 Automated Positioning Systems for Accuracy
Incorporating automated positioning systems ensures that molds are precisely aligned for downstream processes. Below is a comparison of manual vs. automated positioning:
Feature | Manual Systems | Automated Systems |
---|---|---|
Positioning Time | 10–15 minutes | Under 5 minutes |
Error Rate | Higher due to manual input | Minimal with automated input |
Consistency Across Cycles | Varies | Uniform |
This level of accuracy is especially critical in industries like injection molding, where a small misalignment can lead to significant defects.
2.3 Workflow Optimization through AI Integration
Artificial intelligence (AI) takes automation to the next level by analyzing data and predicting maintenance needs. Predictive maintenance enabled by AI ensures fewer disruptions, longer machine life, and reduced operational costs.
Consider this: a mold turner integrated with AI can predict motor wear two weeks in advance, allowing teams to schedule repairs without halting production. Over time, this reduces maintenance costs by up to 30%.
2.4 Streamlined Productivity in Multi-Shift Operations
For facilities running multiple shifts, automation significantly boosts productivity. Below is a data comparison of traditional and automated setups in multi-shift operations:
Metric | Traditional Setup | Automated Setup |
---|---|---|
Daily Output (Units) | 500 | 850 |
Downtime (Minutes) | 90 | 30 |
Energy Consumption (kWh) | 1,200 | 950 |
The data highlights how automation doesn’t just increase output but also optimizes energy usage, making it a sustainable choice.
2.5 Fact or Fiction?
- True: AI-enabled mold turners can predict and prevent breakdowns, significantly reducing downtime.
- False: Automation in mold turners is only suitable for small-scale production facilities.
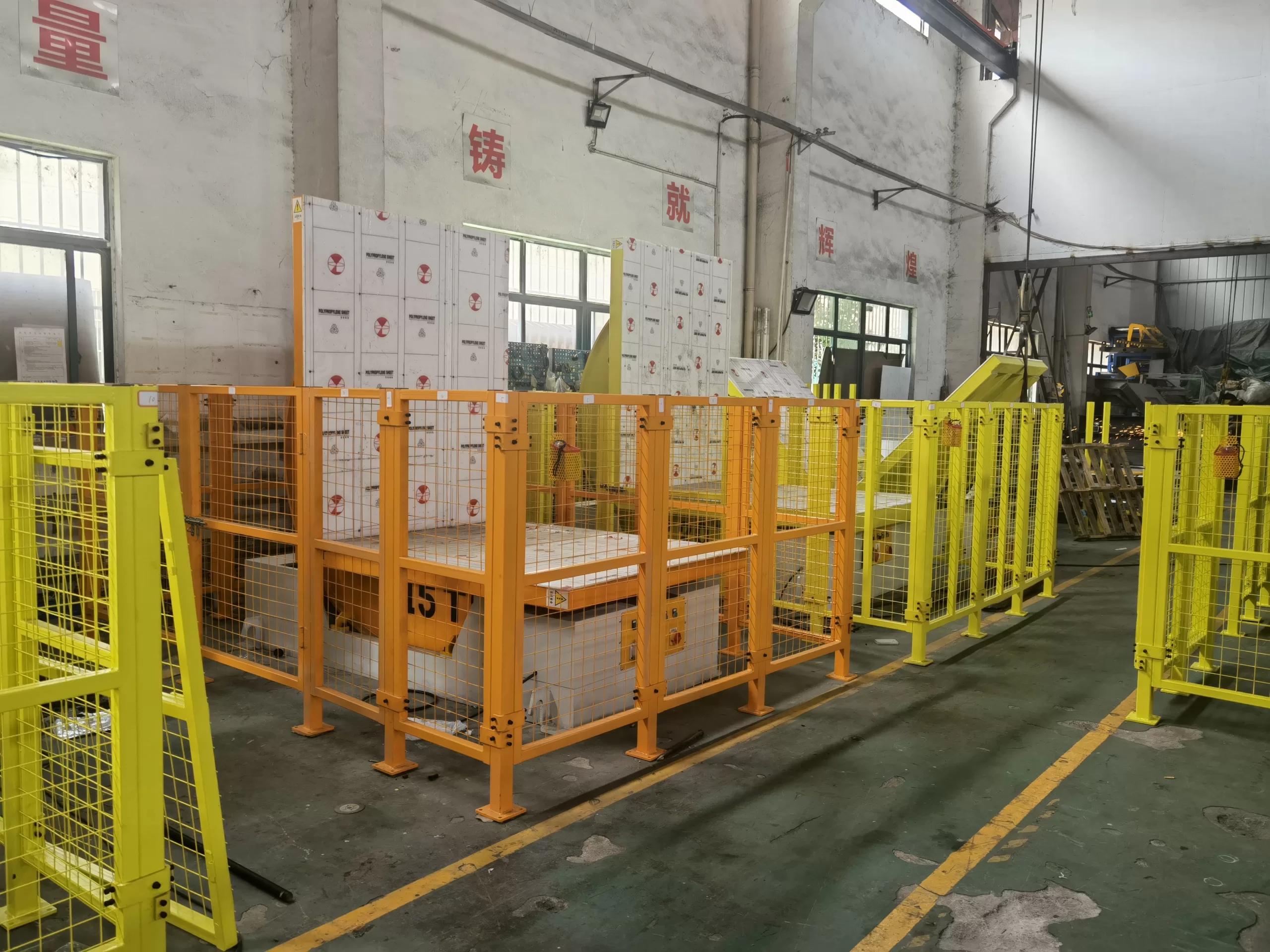
3. What Safety Features Should You Prioritize in Customizable Turners?
3.1 Safety Sensors for Collision Prevention
Safety is paramount in heavy equipment. Customizable mold turners often come equipped with safety sensors that detect potential obstructions and halt operations instantly. This feature is particularly valuable in environments where space is limited, ensuring personnel and equipment remain unharmed.
Beyond safety, these sensors help maintain operational efficiency by preventing damage to molds or the machine itself.
3.2 Emergency Stop Mechanisms for Quick Intervention
Emergency stop mechanisms are a non-negotiable feature for modern mold turners. Below is a list of essential emergency mechanisms found in customizable models:
Mechanism | Functionality |
---|---|
Manual Stop Buttons | Allows quick halting during emergencies |
Automated Halt Systems | Automatically stops upon sensor trigger |
Multi-Layer Lock Mechanisms | Prevents accidental restarts |
3.3 Compliance with Industry Standards
To ensure worker safety, customizable turners adhere to global safety standards such as ISO 13849 or OSHA regulations. Compliance doesn’t just protect workers—it also safeguards manufacturers from legal liabilities. Here’s a quick overview of common standards:
Standard | Focus Area |
---|---|
ISO 13849 | Safety-related machine control systems |
OSHA Guidelines | Worker safety in industrial setups |
CE Certification | European safety and quality assurance |
3.4 Dive Deeper into Training and Safe Operations
Even with the most advanced safety features, operator training remains crucial. Below is a snapshot of training benefits:
Training Area | Impact |
---|---|
Emergency Protocols | Faster and effective incident response |
Machine Handling Practices | Reduces wear and tear on equipment |
Maintenance Best Practices | Prolongs machine lifespan |
Operators who are well-versed in safe practices contribute significantly to operational continuity and workplace safety.
3.5 Fact or Fiction?
- True: ISO 13849 compliance ensures that a machine’s control systems are safety certified.
- False: Safety features in mold turners eliminate the need for operator training.

4. How Does Customization Impact Long-Term Cost Savings?
4.1 Tailored Designs Reduce Maintenance Costs
One of the key advantages of customizable die and mold turners is the ability to adapt designs to specific operational needs. By aligning the machine’s capabilities with the workload, wear and tear are minimized, significantly reducing maintenance costs over time.
For instance, if a manufacturer frequently handles high-weight molds, incorporating reinforced components prevents frequent part replacements. This tailored approach ensures the machine’s longevity while keeping costs under control.
4.2 Energy-Efficient Systems Minimize Operational Expenses
Energy-efficient mold turners are another customization option that delivers long-term savings. Below is a comparison of traditional systems versus energy-optimized models:
Feature | Traditional Systems | Energy-Efficient Systems |
---|---|---|
Average Energy Use (kWh) | 1,500 | 1,000 |
Monthly Energy Cost ($) | 4,500 | 3,000 |
Annual Savings ($) | – | 18,000 |
These savings add up significantly over the lifespan of the machine, making energy-efficient designs a valuable investment.
4.3 Lifecycle Cost Analysis: A Deeper Look
Customizable machines often come with a higher initial cost, but their long-term financial benefits outweigh this investment. Lifecycle cost analysis highlights how customization impacts overall expenditure:
Cost Component | Standard Machine | Customized Machine |
---|---|---|
Initial Purchase Cost ($) | 50,000 | 70,000 |
Maintenance Cost ($/year) | 10,000 | 5,000 |
Total Cost Over 10 Years ($) | 150,000 | 120,000 |
By tailoring features to specific needs, businesses can reduce recurring costs and enhance ROI over the machine’s lifespan.
4.4 Dive Deeper into ROI of Customization
Return on investment (ROI) from customized mold turners goes beyond monetary savings. Enhanced productivity, minimized downtime, and improved safety contribute to indirect cost reductions. Here’s how ROI typically breaks down:
Benefit | Financial Impact ($) |
---|---|
Reduced Downtime | 10,000/year |
Improved Efficiency | 8,000/year |
Fewer Repairs | 5,000/year |
Total Annual ROI | 23,000/year |
By calculating these factors, manufacturers can make informed decisions about the value of investing in customized solutions.
4.5 Fact or Fiction?
- True: Customizable machines typically result in reduced maintenance and operational costs over time.
- False: The upfront cost of a standard machine is always lower than a customized one.
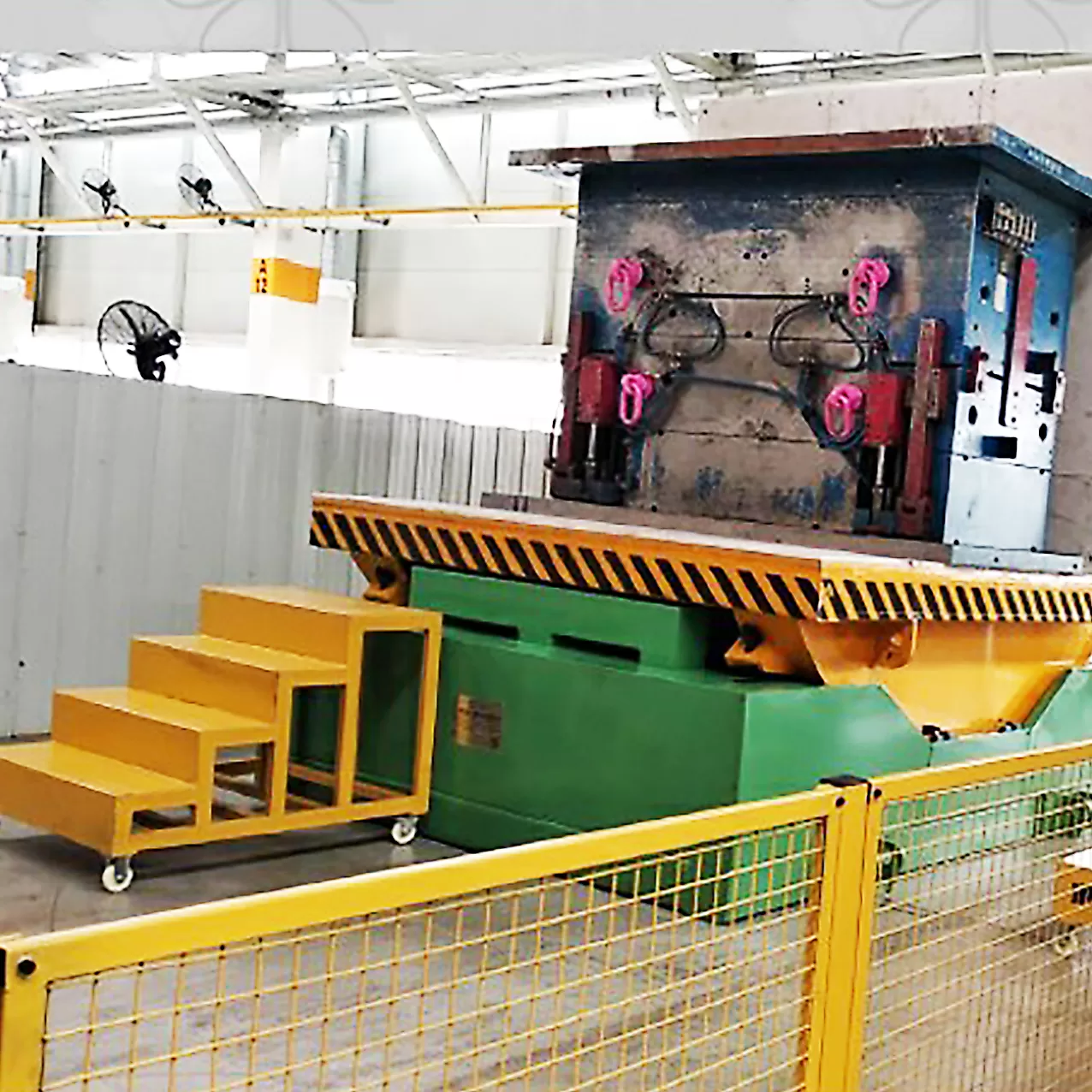
Conclusion
Customizable die and mold turners provide the flexibility manufacturers need to address diverse challenges, from precision handling to safety and cost-efficiency. By tailoring features like load capacity, energy optimization, and control systems, businesses can achieve greater productivity while reducing long-term expenses.
[Claim]
Investing in a customized die and mold turner is not just about meeting today’s operational needs—it’s a forward-looking strategy that drives efficiency, safety, and profitability for years to come.

Get Your Best Solution !