Optimizing Copper Coil Packaging: Essential Features of Modern Wrapping Machines
Proper packaging is critical for safeguarding valuable copper coils throughout storage and transportation. Copper's susceptibility to surface damage, oxidation, and corrosion necessitates robust protection. Automated coil packing and wrapping machines play a vital role in ensuring coils reach their destination in optimal condition, streamlining handling processes and enhancing overall operational efficiency. Understanding the key features and capabilities of this equipment is essential for selecting the right solution.
Core Functionality: Protecting the Coil
The primary function of a copper coil packing machine is to apply protective wrapping material—such as stretch film, VCI (Vapor Corrosion Inhibitor) paper or film, or woven fabrics—securely around the coil. This shield protects against moisture, dust, physical impacts, and other environmental factors that could compromise the copper's quality.
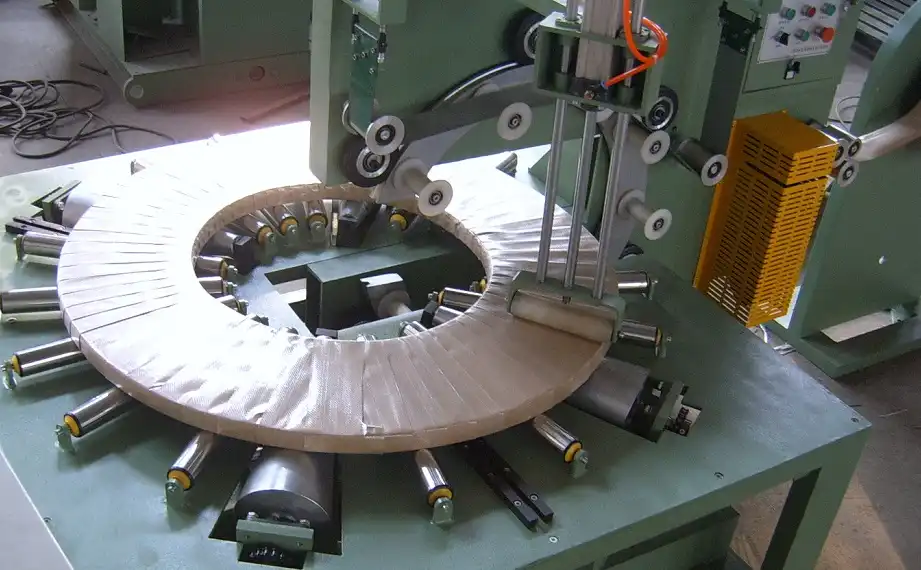
Key Considerations for Selecting a Copper Coil Packing Machine
Choosing the appropriate machinery involves evaluating several critical features against specific operational needs:
Handling Capacity: Matching Machine to Coil
The machine must be dimensionally and structurally capable of handling the specific range of copper coils used in your facility. Key specifications include:
- Maximum Weight: Ensure the machine's load capacity (e.g., up to 10 tons or as specified) exceeds the weight of your heaviest coils.
- Coil Dimensions: Verify the machine can accommodate the minimum and maximum outside diameter (OD), inside diameter (ID), and width of your coils. The support rollers, wrapping ring size, and overall machine footprint must be suitable.
Automation for Efficiency and Consistency
Modern coil wrapping machines incorporate significant automation to improve throughput and ensure repeatable quality:
- Automatic Material Feed and Cut: Systems that automatically dispense the wrapping material, maintain consistent tension during application, and precisely cut the material upon cycle completion minimize manual intervention and material waste.
- Constant Tension Control: Essential for ensuring the wrap is tight enough for security but not so tight as to damage the coil edges. This leads to a stable and consistently protected package.
Control Systems and Ease of Use
Advanced control systems enhance functionality and simplify operation:
- Programmable Logic Controller (PLC): PLCs allow for pre-programmed wrapping "recipes" tailored to different coil sizes and wrapping requirements. This enables quick changeovers between product types.
- Human-Machine Interface (HMI): An intuitive touchscreen interface simplifies machine operation, monitoring, and troubleshooting, reducing training time and potential operator errors.
copper coil wrapper1 Customization and Flexibility
Manufacturing environments often require adaptable equipment:
- Adjustable Components: Features like adjustable support rollers, guide rollers, and clamping mechanisms allow the machine to be fine-tuned for various coil dimensions within its operating range.
- Modular Design: Some machines offer modular components, allowing for easier integration into existing lines or future upgrades.
Integrated Material Handling
Efficiently moving heavy copper coils onto and off the wrapping station is crucial:
- Loading/Unloading: Options range from integrated loading trolleys (carts) for manual or semi-automated positioning to conveyor systems, tilt tables, or integration with overhead cranes for fully automated lines. The chosen method should align with plant workflow and safety protocols.
Ensuring Operator Safety
Robust safety features are non-negotiable in industrial machinery:
- Emergency Stops: Easily accessible E-stop buttons are critical.
- Safety Guarding: Physical barriers or fencing prevent access to moving parts during operation.
- Light Curtains/Safety Sensors: These detect personnel entering hazardous zones and automatically halt machine movement.
- Interlocks: Ensure guards must be in place for the machine to operate.
Optional Enhancements for Added Protection and Functionality
Depending on requirements, machines can include additional features:
- Sealing Systems: Heat sealing or adhesive applicators can be integrated to secure the wrap tail or provide a more complete environmental seal.
- Integrated Weighing/Labeling: Some systems can incorporate scales for weight verification and automated label applicators for product identification and tracking.
copper tube coil packing machine zt Selecting Appropriate Wrapping Materials
The choice of wrapping material significantly impacts the level of protection:
- Stretch Film: Provides good load containment and protection against dust and moisture.
- VCI Film/Paper: Impregnated with Vapor Corrosion Inhibitors, crucial for protecting copper from oxidation and corrosion, especially during long-term storage or sea transport.
- Woven Fabric/Polypropylene: Offers enhanced puncture and tear resistance for heavy-duty applications.
Benefits of Utilizing Specialized Coil Wrapping Equipment
Investing in a dedicated copper coil packing machine offers numerous advantages:
- Improved Product Protection: Consistent, secure wrapping minimizes damage during handling and transit.
- Enhanced Safety: Reduces manual handling risks associated with heavy coils.
- Increased Efficiency: Automation speeds up the packaging process compared to manual methods.
- Consistent Quality: Automated systems ensure every coil is wrapped to the same standard.
- Material Savings: Precise tension control and cutting can optimize material usage.
Conclusion
Selecting the right copper coil packing machine requires a thorough assessment of your specific coil dimensions, weight range, throughput requirements, handling methods, and desired level of protection. By carefully considering the features outlined above—from handling capacity and automation to safety and material compatibility—fabricators and processors can implement effective packaging solutions that protect valuable copper assets and streamline operations.