Complying with OSHA Guidelines Using Automated Steel Coil Packaging Equipment
- Complying with OSHA Guidelines Using Automated Steel Coil Packaging Equipment
- Introduction
- 1. Understanding OSHA Guidelines for Steel Coil Packaging
- 2. The Risks of Manual Steel Coil Packaging
- 3. How Automation Addresses OSHA Guidelines
- 4. Increasing Workplace Safety with Automated Systems
- 5. OSHA Compliance Through Consistent Machine Operation
- 6. The Role of Automation in Reducing Slip, Trip, and Fall Hazards
- 7. Reducing the Risk of Machine-Related Injuries
- 8. Improving Ergonomics with Automation
- 9. Training and Safety Education with Automated Systems
- 10. Achieving Long-Term OSHA Compliance with Automation
- Conclusion

Introduction
The Occupational Safety and Health Administration (OSHA) sets strict guidelines to protect workers from hazards in various industries, including manufacturing and steel production. In an environment where steel coil packaging plays a critical role in the supply chain, the risk of injury due to manual handling, heavy lifting, and hazardous machinery is significant. For companies looking to enhance their safety protocols and remain compliant with OSHA regulations, the integration of automated steel coil packaging equipment offers an ideal solution.
This article will explore how the use of automated systems can help businesses not only comply with OSHA guidelines but also enhance workplace safety, reduce operational risks, and increase overall productivity. By eliminating many of the risks associated with manual operations, automated packaging equipment serves as a crucial tool for modernizing steel coil packaging while maintaining compliance with regulatory standards.
1. Understanding OSHA Guidelines for Steel Coil Packaging
Overview of OSHA’s Role
OSHA is responsible for establishing and enforcing workplace safety standards across various industries, including steel manufacturing. When it comes to steel coil packaging, OSHA guidelines focus on minimizing risks such as:
- Lifting injuries: Steel coils are heavy and require careful handling. OSHA emphasizes the importance of reducing manual lifting to prevent musculoskeletal injuries.
- Pinching and crushing hazards: The use of machinery for wrapping, strapping, and handling coils presents risks of workers getting caught in or between machinery.
- Slip and fall risks: Packing environments may have cluttered floors or debris, creating slip hazards, especially when manual work is involved.
- Ergonomics: OSHA advocates for the reduction of repetitive movements that could lead to worker fatigue and injury.
Understanding OSHA’s general guidelines provides a framework for ensuring that steel coil packaging processes are safe for workers. However, achieving full compliance is often challenging with manual processes, making automation a valuable investment.
2. The Risks of Manual Steel Coil Packaging
Common Injuries in Manual Operations
Manual handling of steel coils presents numerous risks, including:
- Back Injuries: Workers are often required to lift, push, or maneuver heavy steel coils, which can strain the back and lead to chronic pain or more severe injuries like herniated discs.
- Hand and Arm Injuries: Manually operating machinery or handling sharp steel bands and materials can cause cuts, pinches, and crush injuries to the hands and arms.
- Fatigue: Repetitive tasks such as wrapping or strapping steel coils can result in fatigue, which increases the likelihood of accidents and injuries.
These hazards make it difficult for companies to remain OSHA-compliant while relying solely on manual operations. Automation mitigates these risks by reducing the need for direct physical interaction with heavy coils and hazardous machinery.
3. How Automation Addresses OSHA Guidelines
Key Safety Features of Automated Packaging Systems
Automated steel coil packaging equipment is designed with safety features that directly address OSHA’s guidelines for injury prevention. These systems minimize worker interaction with the most dangerous aspects of the packaging process. Key safety features include:
- Automated Wrapping and Strapping: By automating the wrapping and strapping process, workers no longer need to manually position steel bands or secure materials around heavy coils. This eliminates the risk of hand injuries and reduces the need for manual lifting.
- Safety Sensors and Guarding: Modern automated systems are equipped with sensors and guards that detect the presence of workers near machinery. If a worker is too close, the system automatically stops to prevent accidents. These safety features are fully aligned with OSHA’s emphasis on machine guarding to protect workers from moving parts.
- Ergonomic Designs: Automated systems can be programmed to handle various coil sizes and weights without the need for worker intervention. By removing the need for manual adjustments, these systems support OSHA’s guidelines on ergonomics by reducing repetitive movements that could lead to injury.
Reducing Human Error
Human error is a leading cause of workplace accidents, especially in environments where manual work is the norm. With automation, machine-controlled processes eliminate the chance of mistakes related to improper handling or misjudged coil placements. Automated equipment operates with precision, ensuring that each coil is packaged correctly and safely, all while reducing the potential for human error.
4. Increasing Workplace Safety with Automated Systems
Minimizing Direct Interaction with Heavy Loads
One of OSHA’s top priorities is to reduce the risk of injuries caused by heavy lifting and manual handling. Automated steel coil packaging systems address this by using machinery to lift, position, wrap, and strap steel coils. By automating these tasks, workers no longer need to manually engage with heavy objects, significantly reducing the risk of musculoskeletal disorders and injuries.
Benefits of Reducing Manual Labor
- Fewer Lifting Injuries: Since machines handle the physical labor, the risk of injuries associated with lifting heavy loads is virtually eliminated.
- Decreased Worker Fatigue: Automated systems allow workers to focus on monitoring equipment rather than performing repetitive manual tasks, which reduces overall fatigue and the likelihood of accidents.
- Improved Morale: Workers in environments where automation reduces physical strain report higher job satisfaction, knowing that they are less likely to be injured on the job.
Enhancing Safety Through Automation
Automated systems are often designed with built-in safety protocols that help companies comply with OSHA’s guidelines. These systems include:
- Emergency Stops: Automated steel coil packaging equipment comes with emergency stop buttons that workers can easily access in case of a malfunction or safety concern.
- Automated Alerts: Many systems are equipped with automated alert systems that notify operators of any irregularities in the packaging process, such as improper coil alignment or material issues, enabling swift corrective actions before accidents occur.
5. OSHA Compliance Through Consistent Machine Operation
Consistency in Operations
OSHA’s guidelines stress the importance of consistent safety practices. One of the challenges in manual operations is ensuring that workers consistently follow the same safety protocols. Variations in how tasks are performed can lead to safety lapses, injuries, or equipment malfunctions.
With automation, consistency is built into the system. Machines perform the same tasks repetitively and accurately, ensuring that every coil is packaged using the same procedures and safety measures. This adherence to consistent processes ensures that OSHA’s guidelines for safe operation are followed without the variability associated with human workers.
Reduced Training Requirements
Manual operations require workers to be fully trained in various safety procedures, machine operation, and best practices for handling steel coils. This training must be ongoing to ensure that workers remain aware of OSHA requirements and company-specific safety protocols. However, with the integration of automated systems, the need for extensive training is reduced. Workers primarily need to be trained on system monitoring and maintenance, rather than engaging in potentially dangerous manual tasks.
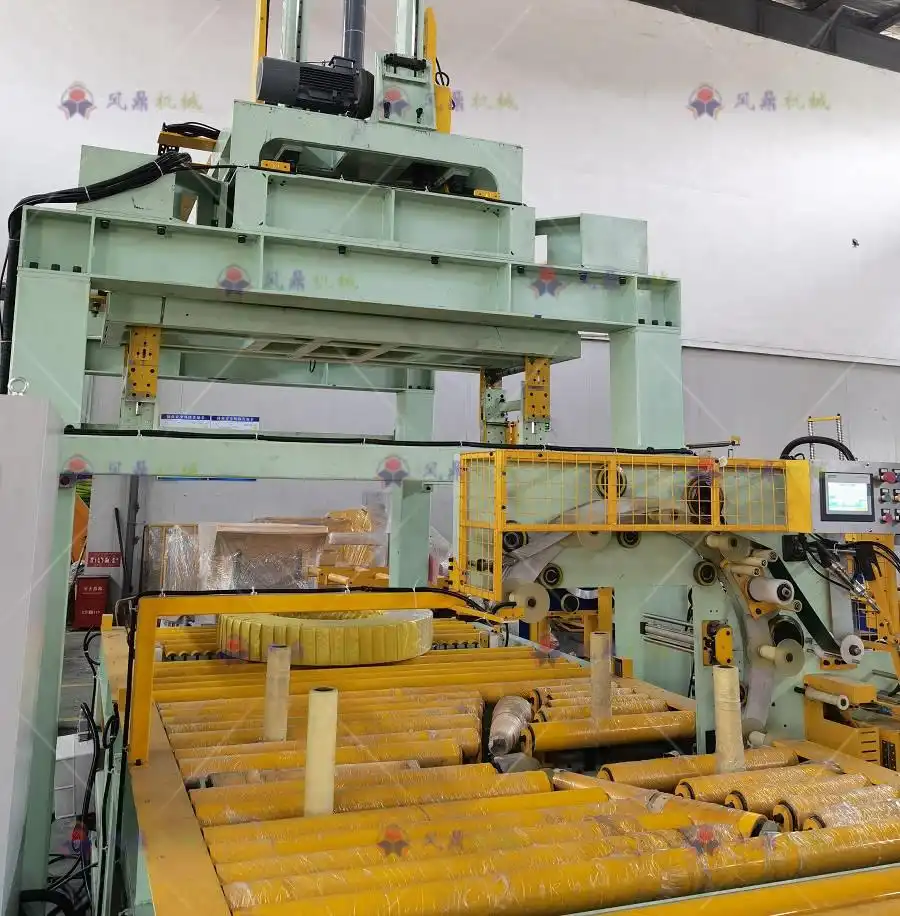
6. The Role of Automation in Reducing Slip, Trip, and Fall Hazards
Maintaining a Clean and Organized Work Environment
One of OSHA’s key guidelines is the reduction of slip, trip, and fall hazards in the workplace. In a manual steel coil packaging environment, workers often have to move between stations, handle various materials, and navigate around equipment, which increases the chances of slips or trips. Additionally, packaging materials such as strapping or loose film can clutter the floor, leading to safety risks.
Automated steel coil packaging systems help mitigate these hazards by reducing the need for workers to move around the workspace. Automated conveyors transport coils from one station to the next, minimizing the need for human intervention and creating a more organized, streamlined workspace. By limiting the physical presence of workers near moving coils and hazardous areas, the risk of workplace accidents is significantly decreased.
Benefits of a Cleaner Work Environment with Automation
- Reduced Clutter: Automated systems often include storage areas for materials, reducing the amount of loose packaging materials on the floor.
- Minimized Worker Movement: With machines handling most of the operations, workers spend less time moving between stations, which reduces the likelihood of tripping or slipping.
- Enhanced Floor Safety: A well-organized workspace is not only safer but also more efficient, as there are fewer obstacles for workers to navigate during their shifts.
Integrated Safety Features for Fall Prevention
Automated packaging systems can also be equipped with integrated fall prevention technologies, such as anti-slip flooring near high-traffic areas or automated floor cleaners that ensure the workspace remains clear of debris. These features further support OSHA’s goal of reducing slip, trip, and fall hazards in industrial environments.
7. Reducing the Risk of Machine-Related Injuries
Machine Guarding and Lockout/Tagout Procedures
One of OSHA’s primary concerns in manufacturing environments is the risk of workers getting injured by machinery. In manual packaging operations, workers are often required to interact directly with dangerous equipment, increasing the risk of accidents. OSHA mandates that all machinery be equipped with proper machine guarding and that lockout/tagout (LOTO) procedures are in place to prevent accidental startup during maintenance.
Automated steel coil packaging equipment is designed with built-in safety features that comply with OSHA’s machine guarding standards. These systems use:
- Physical Guards: Machines are equipped with barriers that prevent workers from coming into contact with moving parts during operation.
- Lockout/Tagout Systems: Automated systems incorporate LOTO procedures that prevent machines from being activated during maintenance or cleaning. These procedures ensure that equipment cannot be started without proper clearance, protecting workers from accidental injuries.
Automated Shutdowns for Enhanced Safety
In the event of a system failure or a safety breach, automated packaging equipment is designed to shut down automatically, reducing the risk of injury. These emergency stop functions ensure that workers are not exposed to moving parts or high-risk areas when the system encounters a malfunction. This automated response further enhances compliance with OSHA guidelines, ensuring that all safety precautions are in place even in unforeseen circumstances.
8. Improving Ergonomics with Automation
Addressing Ergonomic Hazards
In manual steel coil packaging, workers are often required to perform repetitive movements, such as bending, reaching, and lifting, which can lead to ergonomic injuries over time. OSHA emphasizes the importance of reducing these risks through better workplace ergonomics. Repetitive strain injuries, musculoskeletal disorders, and long-term physical wear are all common problems associated with manual coil handling.
Automated systems reduce these ergonomic hazards by taking over the most physically demanding tasks. Machines are designed to lift, wrap, and strap heavy coils without human intervention, reducing the need for workers to engage in activities that strain the body.
Benefits of Improved Ergonomics
- Reduced Repetitive Movements: Automation eliminates the need for repetitive manual tasks, such as wrapping coils or strapping them in place, which greatly reduces the risk of strain injuries.
- Safer Lifting Practices: Automated lifting mechanisms remove the need for workers to physically handle heavy steel coils, reducing the risk of back injuries and other lifting-related injuries.
- Customizable Workstations: For tasks that still require human interaction, automated systems can be designed to adjust to the worker’s height and reach, ensuring that their workstation is ergonomic and safe.
By addressing these ergonomic challenges, automated systems help companies comply with OSHA’s ergonomic guidelines, ultimately leading to a healthier and safer workforce.
9. Training and Safety Education with Automated Systems
Simplified Training Requirements
One of the challenges with manual operations is the extensive training required to ensure that workers understand all aspects of machine operation, safety protocols, and OSHA compliance. With automation, the need for intensive training is reduced, as workers are not required to interact with machinery in the same way.
Automated systems typically require operators to monitor equipment and manage its overall functionality, which simplifies the training process. Instead of learning how to safely operate each piece of machinery manually, workers are trained on how to oversee the system, respond to alerts, and perform basic maintenance.
Ongoing Safety Education
Despite the reduced training needs, it is still essential for companies to provide ongoing safety education that covers:
- System Monitoring: Workers should be trained on how to monitor the automated system and recognize potential safety risks or irregularities in its operation.
- Emergency Procedures: Workers must know how to respond to system alerts, shutdowns, and safety breaches to ensure the proper handling of emergencies.
- Maintenance Protocols: Proper maintenance and cleaning procedures should be taught to minimize the risk of injury during routine maintenance.
10. Achieving Long-Term OSHA Compliance with Automation
The Benefits of Continuous Compliance
Achieving OSHA compliance is not a one-time task but a continuous process that requires regular system assessments, safety audits, and employee training. Automated steel coil packaging systems are built with OSHA compliance in mind, ensuring that key safety guidelines are met consistently. However, companies must remain vigilant in maintaining compliance through regular system checks, updates, and adherence to new OSHA standards as they evolve.
How Automation Supports Long-Term Compliance
- Consistency: Automation ensures that the same safety procedures are followed for every coil packaged, reducing the risk of inconsistent safety practices.
- Adaptability: Modern automated systems can be updated or modified to meet new OSHA guidelines or accommodate changes in workplace safety needs.
- Reduced Risk of Violations: By automating key processes, companies minimize the likelihood of OSHA violations due to human error or negligence.
By implementing automated steel coil packaging equipment, companies can ensure long-term OSHA compliance while benefiting from enhanced productivity, reduced operational risks, and a safer work environment.
Conclusion
Integrating automated steel coil packaging equipment into your operations is a powerful way to ensure compliance with OSHA guidelines. Automation not only addresses the specific safety risks associated with manual steel coil handling but also enhances overall workplace safety by reducing physical strain, eliminating repetitive tasks, and improving ergonomic conditions. From minimizing heavy lifting to incorporating machine guarding and emergency shutdown systems, automated equipment significantly lowers the risk of workplace injuries.
By investing in automation, companies can achieve a safer, more efficient operation, ensuring long-term OSHA compliance while boosting productivity and worker morale. With continuous advancements in technology, automated systems are becoming increasingly essential for companies looking to modernize their operations while prioritizing worker safety and regulatory adherence.