Optimizing Your Pallet Wrapping: Automatic Wrappers With vs. Without Film Cut-Off Devices
In modern logistics and manufacturing environments, efficient and secure pallet wrapping is non-negotiable. The adoption of automated solutions has streamlined this process significantly. A key decision point involves choosing between automatic pallet wrappers equipped with film cut-off devices and those without. This guide delves into the distinctions to help you determine the optimal choice for your operational needs.
What are Automatic Pallet Wrappers?
Automatic pallet wrappers are sophisticated machines engineered to apply stretch film securely around palletized goods. This automated process enhances load stability for transport and storage, critically reducing the risk of product damage and associated losses. They represent a significant upgrade from manual or semi-automatic methods in terms of consistency and throughput.
Understanding the Film Cut-Off Feature
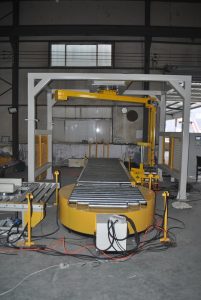
A film cut-off device integrated into an automatic pallet wrapper automates the final step of the wrapping cycle: severing the stretch film. This mechanism enhances the overall automation, boosts efficiency, and improves operator safety by removing the need for manual cutting.
Core Benefits of Investing in Automatic Pallet Wrappers
Automating your wrapping process yields several key advantages:
Enhanced Efficiency and Throughput
Automatic wrappers drastically increase operational speed and efficiency. By automating the entire cycle, they ensure consistent, rapid wrapping, significantly reducing the time spent per pallet compared to manual methods.
Superior Load Consistency and Stability
Machine-controlled wrapping guarantees consistent film application and tension. This uniformity results in highly stable and secure loads, minimizing the likelihood of product shifting or damage during transit and handling.
Reduced Labor Requirements and Costs
Automation directly translates to lower labor costs. Fewer personnel are needed for the wrapping task, freeing up valuable human resources for more complex or strategic activities within the facility.
Advantages Specific to Film Cut-Off Devices
Adding an automatic film cut-off mechanism provides further benefits:
Significant Time Savings
The primary advantage is eliminating the manual film cutting step, saving valuable seconds on every cycle. In high-volume operations, this translates to substantial gains in throughput and allows for truly continuous, operator-free wrapping sequences.
Improved Workplace Safety
Automating the cut removes the need for operators to approach the machine with cutting tools while it may still be in motion or reaching awkward angles. This significantly reduces the risk of cuts or strains, contributing to a safer work environment.
Optimized Material Usage
Precise, automated cutting minimizes film tails and waste associated with manual cutting. This optimization of film consumption leads to direct material cost savings and supports more sustainable packaging practices.
Head-to-Head Comparison: Wrappers With vs. Without Film Cut-Off
Let's compare the two configurations across key operational factors:
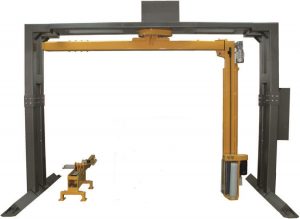
Operational Efficiency
- With Cut-Off: Generally offers superior operational efficiency. The fully automated cycle reduces bottlenecks and allows for smoother integration into automated conveyor lines. Cycle times are minimized.
- Without Cut-Off: Requires operator intervention at the end of each cycle to cut the film, adding time and potentially creating pauses in workflow, especially in high-speed environments.
Cost Considerations
- With Cut-Off: Typically involves a higher initial investment due to the additional mechanism. However, the long-term ROI can be favorable through reduced labor, faster throughput, and film savings.
- Without Cut-Off: Lower upfront cost, which might be appealing for lower-volume operations or tighter budgets. Requires factoring in the ongoing labor cost associated with manual cutting.
Maintenance and Reliability
- With Cut-Off: Introduces an additional mechanical component (the cutter) that requires periodic maintenance (e.g., blade sharpening/replacement). However, reputable manufacturers design these systems for high reliability and durability with appropriate maintenance schedules.
- Without Cut-Off: Simpler mechanical design, potentially leading to slightly lower maintenance requirements related to the cutting function itself. Overall machine reliability depends heavily on build quality.
Operational Flexibility
- Both types generally offer good flexibility for handling various load sizes and types. Machines with cut-off devices might be part of more advanced systems offering greater programming capabilities for complex wrapping patterns.
Key Technological Advancements in Pallet Wrapping
Modern pallet wrappers often incorporate cutting-edge features:
Smart Sensing and Automation
Advanced sensors monitor load dimensions and stability, automatically adjusting wrapping parameters (like tension and film overlap) for optimal results, enhancing precision and reducing film waste.
IoT Connectivity and Remote Monitoring
Integration with the Internet of Things (IoT) enables remote performance monitoring, predictive maintenance alerts, and diagnostics. This helps maximize uptime and streamline troubleshooting.
Environmental and Sustainability Aspects
Choosing the right wrapper can impact your environmental footprint:
Reducing Material Waste
Automatic wrappers, particularly those with precise film application and cut-off features, contribute significantly to sustainability by minimizing stretch film consumption and waste, aligning with corporate green initiatives.
Energy Efficiency Focus
Manufacturers are increasingly designing energy-efficient machines, utilizing advanced motors and control systems to reduce power consumption during operation, further supporting sustainability goals.
Common Industry Applications
Automatic pallet wrappers are vital across various sectors:
Manufacturing and Logistics Hubs
In high-volume manufacturing plants and distribution centers, speed, reliability, and load security are paramount. Wrappers with film cut-off devices excel in these demanding environments, often integrated into fully automated end-of-line systems.
Food and Beverage Sector
The food and beverage industry relies on secure wrapping to maintain product integrity and hygiene. Automated systems, especially those minimizing manual contact via film cut-off, help meet stringent quality and safety standards.
Making the Right Choice for Your Operation
The decision between an automatic pallet wrapper with or without a film cut-off device hinges on your specific circumstances:
- High-Volume Operations: Facilities processing a large number of pallets daily will likely see the best ROI from a machine with a film cut-off device due to significant gains in speed, efficiency, and labor savings.
- Moderate to Low Volume: Operations with lower throughput might find the higher initial cost of a cut-off device harder to justify. A standard automatic wrapper without cut-off could be sufficient, provided the manual cutting step doesn't create a significant bottleneck.
- Emphasis on Safety: If minimizing operator interaction and injury risk is a top priority, the film cut-off feature offers a clear advantage.
- Budget Constraints: The initial purchase price will be lower for machines without the cut-off feature.
- Automation Integration: For integration into fully automated lines, a wrapper with film cut-off is practically essential for seamless flow.
Conclusion: Investing in Future-Ready Wrapping
Selecting the right automatic pallet wrapper is a strategic investment. While machines with film cut-off devices offer compelling advantages in efficiency, safety, and material savings—particularly beneficial for high-throughput environments—the optimal choice requires careful consideration of your unique operational volume, budget, labor availability, and long-term automation goals. By evaluating these factors thoroughly, you can implement a pallet wrapping solution that not only boosts current productivity but also enhances safety, promotes sustainability, and positions your operation for continued success in a competitive landscape.