Common Workplace Injuries in hydraulic upender operation and How to Prevent Them
- Common Workplace Injuries in hydraulic upender operation and How to Prevent Them
- Introduction
- 1. Understanding the Basics of Hydraulic Upenders
- 2. Common Workplace Injuries in Hydraulic Upender Operations
- 3. Crushing Injuries: Causes and Prevention
- 4. Back and Muscle Strains: Overexertion and Ergonomics
- 5. Slip and Fall Incidents: Hydraulic Fluid Hazards
- 6. Hand and Finger Injuries: Operational Hazards
- 7. Eye Injuries: Fluid Spray and Debris Risks
- 8. Electrical Hazards and Shock
- 9. Hearing Damage: Noise Hazards in Hydraulic Operation
- 10. Fire Hazards: Hydraulic Fluid as a Combustion Risk
- 11. Mental and Physical Fatigue: Long-Term Operational Strain
- 12. The Importance of Regular Training and Safety Protocols
- Conclusion
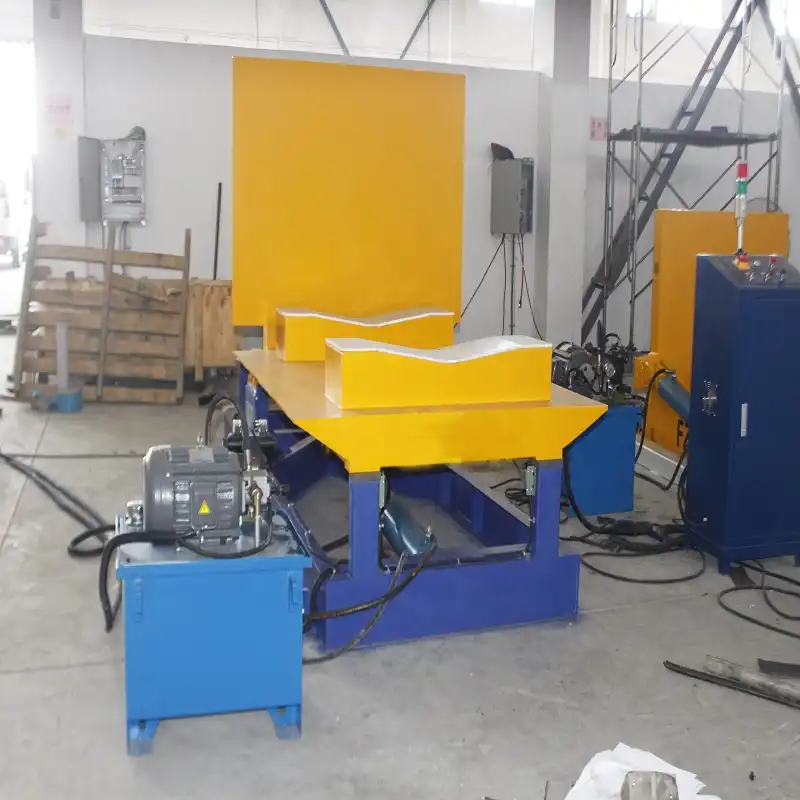
Introduction
Hydraulic upenders play a vital role in heavy industries, facilitating the movement, rotation, and positioning of large materials with ease and efficiency. However, their use also presents potential hazards that, if left unaddressed, can result in serious workplace injuries. Understanding the common injuries that occur in hydraulic upender operation and learning effective prevention strategies are essential to maintaining a safe working environment.
In this article, we will delve into the most frequent injuries associated with hydraulic upender operation and explore practical steps to prevent them. By implementing these strategies, businesses can create a safer workplace, improve operational efficiency, and ensure the well-being of their workforce.
1. Understanding the Basics of Hydraulic Upenders
Hydraulic upenders are machines used to rotate or flip large, heavy objects, making them essential in industries such as metal fabrication, automotive, and manufacturing. These machines rely on hydraulic systems to exert immense pressure, providing smooth and controlled movements that help workers handle loads with minimal physical exertion.
How They Work:
- Hydraulic systems use fluids to transmit force, enabling the upender to lift, rotate, or flip heavy materials.
- Upenders come with different load capacities, and some models can handle weights exceeding several tons.
- Operators control the hydraulic upender through a set of levers or buttons, allowing for precision movement.
While hydraulic upenders provide significant advantages, improper handling and insufficient training can lead to workplace injuries, underscoring the need for proper safety protocols.
2. Common Workplace Injuries in Hydraulic Upender Operations
Despite their advantages, hydraulic upenders can pose various risks if not handled correctly. Some common injuries among operators and workers include:
- Crushing Injuries: Caused by mishandling loads or equipment failure.
- Back and Muscle Strains: Due to overexertion when positioning or adjusting loads.
- Slip and Fall Incidents: From oil or hydraulic fluid leaks.
- Hand and Finger Injuries: Resulting from improper positioning or unexpected movement.
- Eye Injuries: Occurring from hydraulic fluid sprays or particles during operation.
By identifying these injuries, companies can implement targeted safety measures to minimize their occurrence.
3. Crushing Injuries: Causes and Prevention
Crushing injuries are among the most severe risks in hydraulic upender operation, often resulting in broken bones, internal injuries, or even fatalities. These injuries usually occur when workers are caught between the machine and the load.
Causes:
- Equipment malfunctions leading to uncontrolled movement.
- Miscommunication during operation, leading to accidental activation.
- Insufficient clearance around the machine.
Prevention Tips:
- Maintain Proper Clearance: Ensure there is ample space around the upender for safe operation.
- Regular Equipment Checks: Inspect hydraulic components, such as valves and hoses, to prevent sudden movements due to pressure loss or malfunction.
- Safety Training: Train all employees on correct load handling procedures and equipment operation to minimize the risk of crush injuries.
4. Back and Muscle Strains: Overexertion and Ergonomics
Back and muscle strains are often overlooked but can severely impact productivity. Hydraulic upenders are designed to reduce physical exertion; however, improper usage can still lead to muscle strains, particularly in the back, shoulders, and arms.
Causes:
- Poor lifting techniques when positioning loads.
- Overextending to reach controls or adjust loads.
- Standing in awkward positions during operation.
Prevention Tips:
- Ergonomic Training: Provide training on proper lifting techniques and posture to minimize strain.
- Use Lifting Aids: Encourage the use of lifting aids or support tools to reduce the physical burden on workers.
- Position Controls Appropriately: Adjust controls to a comfortable height and distance to prevent overreaching and awkward body positions.
5. Slip and Fall Incidents: Hydraulic Fluid Hazards
Hydraulic fluid leaks are a common problem, as even small leaks can create slippery surfaces. Slip and fall incidents may seem minor, but they can lead to significant injuries, such as fractures, sprains, or head trauma.
Causes:
- Hydraulic fluid or oil spills around the machine.
- Poor housekeeping, leading to wet or oily floors.
- Ineffective cleanup practices after leaks.
Prevention Tips:
- Regular Equipment Maintenance: Inspect hydraulic hoses and seals regularly to prevent leaks.
- Housekeeping Standards: Establish strict cleaning protocols to ensure that any spills are promptly cleaned.
- Non-Slip Mats and Shoes: Use non-slip mats around hydraulic upenders and encourage workers to wear slip-resistant footwear.
6. Hand and Finger Injuries: Operational Hazards
Hands and fingers are especially vulnerable during hydraulic upender operation due to the close proximity to moving parts and the machine’s powerful hydraulics. Injuries range from cuts and abrasions to serious fractures and amputations.
Causes:
- Hands getting caught between moving parts.
- Unexpected machine movement.
- Using hands to adjust loads without proper tools.
Prevention Tips:
- Machine Guards and Barriers: Install guards to protect hands from moving parts.
- Hand Protection: Provide protective gloves suited to the task at hand.
- Hands-Free Tools: Use tools or devices to adjust loads rather than hands.

Get Your Best Solution !
7. Eye Injuries: Fluid Spray and Debris Risks
Eye injuries are a significant concern due to hydraulic fluid leaks or bursts, which can spray under high pressure. The chemicals in hydraulic fluid can cause severe eye irritation or damage.
Causes:
- Sudden hydraulic fluid bursts.
- Particles or debris generated during operation.
- Lack of protective eyewear.
Prevention Tips:
- Wear Safety Goggles: Ensure all operators and nearby personnel wear safety goggles.
- Routine Hydraulic Line Checks: Regularly inspect hoses and fittings for potential leaks.
- Barrier Shields: Install barrier shields around high-pressure areas to reduce exposure risk.
8. Electrical Hazards and Shock
Many hydraulic upenders are powered by electrical systems, posing the risk of electrical shocks, especially when combined with leaking fluids. Electrical injuries can range from mild shocks to severe burns or even fatalities.
Causes:
- Faulty wiring or exposed cables.
- Leaks in hydraulic lines near electrical components.
- Improper grounding of the equipment.
Prevention Tips:
- Regular Electrical Inspections: Have a qualified electrician inspect the machinery’s wiring and grounding.
- Seal Electrical Components: Ensure all electrical parts are sealed and protected from hydraulic fluids.
- Personal Protective Equipment (PPE): Use insulated gloves and boots to reduce shock risk.
9. Hearing Damage: Noise Hazards in Hydraulic Operation
Hydraulic upenders can generate high levels of noise, especially when handling heavy loads. Prolonged exposure to this noise can result in hearing damage for operators.
Causes:
- Loud hydraulic systems.
- Noisy environments where hydraulic upenders are often used.
Prevention Tips:
- Provide Ear Protection: Equip employees with earplugs or earmuffs.
- Noise Level Monitoring: Regularly monitor noise levels to ensure they stay within safe limits.
- Maintenance to Reduce Noise: Keep equipment well-maintained to minimize excessive noise from wear and tear.
10. Fire Hazards: Hydraulic Fluid as a Combustion Risk
Hydraulic fluids are often flammable and, when exposed to heat sources, can pose a fire hazard. Fires in industrial settings can spread quickly, leading to extensive injuries and property damage.
Causes:
- Leaking hydraulic fluid near heat sources.
- Accumulated fluid on machine surfaces igniting.
- Electrical sparks near hydraulic components.
Prevention Tips:
- Routine Leak Checks: Regularly inspect for leaks, especially near heat sources.
- Fire Safety Equipment: Equip the workplace with fire extinguishers rated for oil-based fires.
- Proper Storage of Fluids: Store hydraulic fluids away from heat and open flames.
11. Mental and Physical Fatigue: Long-Term Operational Strain
Frequent, prolonged operation of hydraulic upenders can lead to mental and physical fatigue, impacting an operator’s reaction time and increasing the likelihood of mistakes or injuries.
Causes:
- Repetitive tasks over long periods.
- High-stress environment due to tight schedules.
- Insufficient rest breaks for operators.
Prevention Tips:
- Enforce Regular Breaks: Schedule rest breaks to prevent fatigue.
- Rotate Duties: Allow workers to rotate between tasks to reduce repetitive strain.
- Encourage Stress-Relief Practices: Promote stress-relieving practices to help workers manage mental strain.
12. The Importance of Regular Training and Safety Protocols
Comprehensive training is one of the most effective tools for preventing injuries in hydraulic upender operation. Training programs should be mandatory, covering machine operation, emergency procedures, and equipment maintenance.
Key Components of a Training Program:
- Equipment Handling: Teach employees how to handle loads and control the upender properly.
- Emergency Response: Provide training on what to do in case of an accident or equipment failure.
- Ongoing Refresher Courses: Regularly update training to reflect any new safety protocols or equipment updates.
Conclusion
Hydraulic upender operation, while essential for many industrial applications, comes with a set of risks that can lead to serious workplace injuries. From crushing incidents to eye injuries and electrical shocks, each potential hazard calls for specific preventive measures. By implementing regular maintenance, conducting comprehensive safety training, and fostering a culture of caution, companies can dramatically reduce the likelihood of injuries and create a safer work environment.

Get Your Best Solution !