Coil upenders are indispensable in industries that handle heavy metal coils, offering a safe and efficient way to transition coils between horizontal and vertical orientations. However, like any industrial machinery, they are prone to maintenance issues that can disrupt operations, increase downtime, and inflate costs. Understanding these common problems and implementing preventive maintenance strategies can save companies time and money while extending the lifespan of these machines.
Coil upenders operate under high stress, often lifting and rotating several tons of material. As such, even minor issues can escalate into significant problems if left unaddressed. From mechanical wear to electrical malfunctions, each component’s health is critical for optimal performance. To avoid these setbacks, companies must adopt a proactive approach, balancing regular inspections with detailed troubleshooting.
By analyzing the most frequent maintenance challenges associated with coil upenders, this article provides actionable solutions to mitigate risks. Whether you’re an industry veteran or a newcomer managing these machines, the insights below will help you maintain high operational standards while minimizing unexpected breakdowns.
[claim] Maintenance issues in coil upenders can be effectively mitigated through a combination of routine inspections, operator training, and adherence to manufacturer guidelines.

1. What Are the Most Common Issues in Coil Upender Maintenance?
1.1 Mechanical Wear and Tear
Mechanical wear is one of the most prevalent challenges faced by coil upenders. These machines are constantly subjected to high levels of stress as they lift and rotate heavy loads, causing components like bearings, gears, and lift arms to degrade over time. Without timely intervention, this wear can lead to breakdowns, disrupting production schedules.
One key indicator of mechanical wear is unusual noise during operation. For instance, grinding or squealing sounds often point to worn-out bearings or misaligned gears. Regular lubrication can help mitigate wear, but if left unchecked, damaged components may require costly replacements.
1.2 Hydraulic System Failures
Hydraulic systems are the backbone of coil upenders, providing the power needed to lift and rotate heavy coils. However, these systems are prone to issues such as fluid leaks, pressure loss, or clogged filters. According to industry studies, nearly 40% of coil upender downtime is attributed to hydraulic failures.
Hydraulic System Data Table:
Issue | Cause | Solution |
---|---|---|
Fluid leaks | Damaged seals or hoses | Replace seals, inspect hoses |
Pressure loss | Faulty valves or pumps | Test and repair components |
Clogged filters | Lack of routine maintenance | Clean or replace filters |
To avoid hydraulic failures, operators should schedule regular inspections, monitor fluid levels, and replace worn seals promptly.
1.3 Electrical Malfunctions
Electrical issues, while less frequent than mechanical or hydraulic problems, can still cause significant operational disruptions. Faulty wiring, damaged control panels, and sensor errors are common culprits. These issues often manifest as erratic movements, failure to start, or sudden stoppages.
For example, a damaged limit switch might prevent the coil upender from stopping at the correct position, creating safety hazards. Routine checks of electrical connections and testing control systems can help reduce the likelihood of such failures.
1.4 Operator-Related Errors
While the machine itself is often the focus of maintenance efforts, operator-related errors are an equally significant factor. Improper loading, failure to follow safety protocols, or neglecting maintenance schedules can lead to both minor and major issues. In fact, studies suggest that up to 25% of coil upender malfunctions are due to human error.
Training programs tailored to operators can address these challenges by ensuring they understand the machine’s operational limits and maintenance requirements. Additionally, providing clear documentation and checklists can further reduce the risk of errors.
1.5 Fact vs. Fiction: Do Coil Upenders Require Weekly Maintenance?
- Fact: Regular maintenance, including lubrication and basic inspections, is critical for preventing wear and tear. While weekly maintenance may not always be necessary, monthly checkups are highly recommended.
- Fiction: Coil upenders need daily maintenance. Unless operating under extreme conditions, daily maintenance is excessive and can lead to unnecessary downtime.
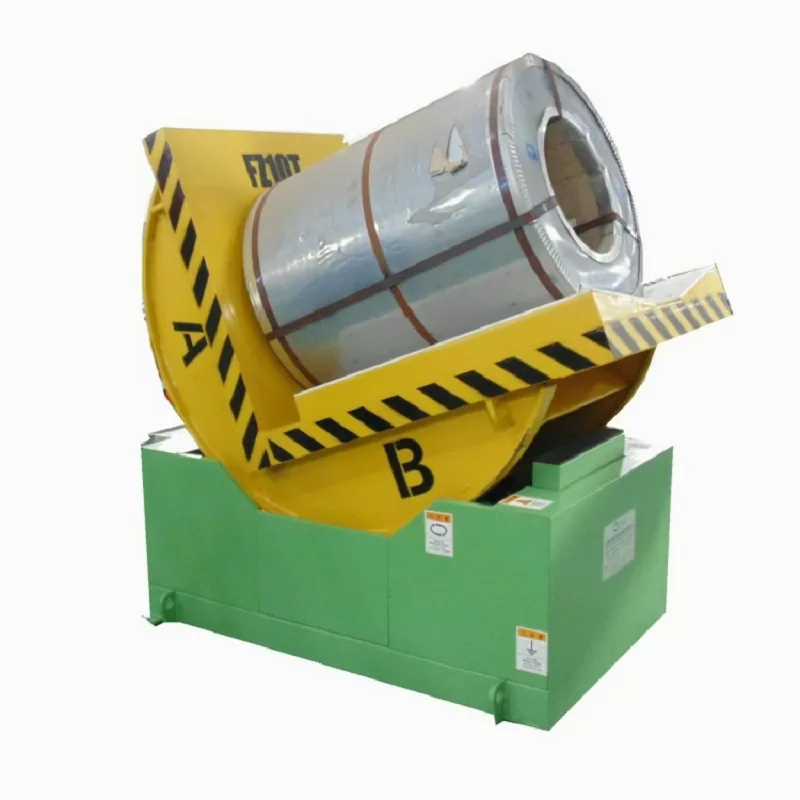
2. How Can Regular Maintenance Improve Coil Upender Performance?
2.1 Benefits of Preventive Maintenance
Preventive maintenance is the cornerstone of ensuring coil upender longevity and optimal performance. By addressing minor issues before they escalate, companies can avoid expensive repairs and extended downtime. For example, regularly lubricating mechanical components reduces friction, which helps prevent excessive wear and overheating.
Moreover, preventive maintenance enhances workplace safety. A malfunctioning coil upender can pose significant risks to operators, including dropped loads or sudden, unpredictable movements. Routine inspections ensure all safety mechanisms, such as limit switches and emergency stops, are functioning properly.
In addition, preventive maintenance contributes to better cost management. According to industry reports, companies that implement routine maintenance save up to 30% on repair costs compared to those that rely solely on reactive repairs.
2.2 Cost Analysis of Maintenance vs. Repairs
The financial benefits of regular maintenance are undeniable when compared to the high costs of unexpected breakdowns. Below is a cost analysis to highlight the savings:
Maintenance vs. Repair Costs Table:
Cost Type | Preventive Maintenance | Reactive Repairs |
---|---|---|
Labor Costs | Low (scheduled inspections) | High (emergency repairs) |
Replacement Parts | Minimal (routine upgrades) | Significant (major components) |
Downtime | Short | Long (days or weeks) |
Total Cost Per Year | $50–$100 | $800–$2,000 |
As shown, preventive maintenance is not only more cost-effective but also minimizes operational disruptions, leading to higher overall productivity.
2.3 The Role of Predictive Analytics in Maintenance
Predictive analytics is revolutionizing industrial maintenance by allowing companies to anticipate problems before they occur. By using sensors and data analysis tools, operators can monitor coil upender performance in real time, identifying irregularities such as increased vibration, temperature fluctuations, or hydraulic pressure drops.
For instance, vibration analysis can detect misaligned gears or worn bearings long before they fail. Companies that adopt predictive maintenance strategies report a 25% reduction in downtime and increased asset reliability.
Key Metrics Monitored in Predictive Maintenance:
- Temperature: Overheating indicates potential lubrication or mechanical issues.
- Pressure: Abnormal hydraulic pressure may signal valve or pump problems.
- Vibration: Irregular patterns suggest imbalances or misalignments.
By combining predictive analytics with a traditional maintenance schedule, companies can achieve a proactive approach that minimizes risks and maximizes efficiency.
2.4 Conclusion
Regular maintenance is integral to the smooth operation of coil upenders, enhancing performance, safety, and cost efficiency. Whether through routine inspections or advanced predictive analytics, investing in maintenance ensures that these machines remain reliable and productive.
[claim] Companies that embrace preventive and predictive maintenance strategies experience fewer breakdowns, lower costs, and improved operational safety.
2.5 Fact vs. Fiction: Does Predictive Maintenance Eliminate Downtime Entirely?
- Fact: Predictive maintenance significantly reduces the likelihood of unexpected downtime by identifying potential issues early.
- Fiction: Predictive maintenance completely eliminates downtime. While it minimizes risks, regular inspections and occasional repairs are still necessary.
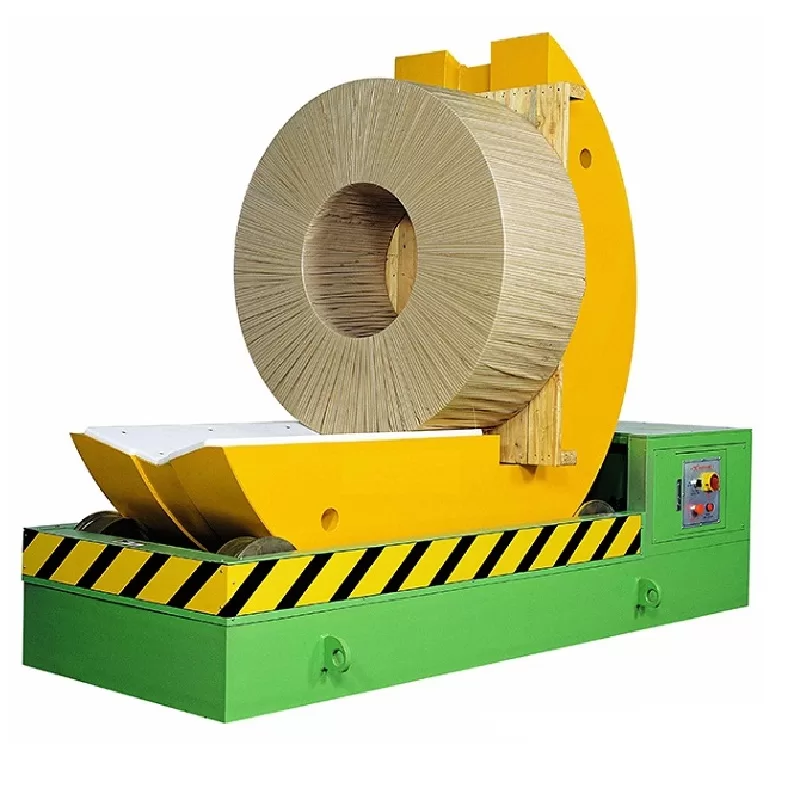
3. What Tools and Techniques Are Essential for Coil Upender Maintenance?
3.1 Essential Tools for Maintenance
Proper maintenance of coil upenders requires a well-equipped toolbox and knowledge of the machine’s specific requirements. Essential tools include torque wrenches, hydraulic test kits, and diagnostic software for monitoring electrical and mechanical systems.
Common Maintenance Tools List:
Tool | Purpose |
---|---|
Torque Wrench | Ensures proper tightening of bolts and screws. |
Hydraulic Test Kit | Measures fluid pressure and identifies leaks. |
Vibration Analyzer | Detects misalignment or worn bearings. |
Multimeter | Tests electrical circuits for faults. |
Having these tools readily available ensures maintenance tasks are completed efficiently, reducing downtime.
3.2 Training Programs for Operators
Operators play a critical role in maintaining coil upenders. Comprehensive training programs should cover proper usage, basic troubleshooting, and routine maintenance steps. According to industry research, companies that invest in operator training report a 15% reduction in machinery malfunctions.
Featured Image:
(Include an image of a trained operator performing maintenance on a coil upender.)
In addition, refresher courses should be conducted annually to keep operators updated on best practices and new technologies.
3.3 Commonly Overlooked Maintenance Practices
While most companies focus on major components like hydraulics and gears, some maintenance tasks are often overlooked, leading to long-term damage. For example, failing to clean the machine’s exterior can result in debris buildup, which may affect moving parts or clog vents.
Overlooked Maintenance Checklist:
- Lubrication Points: Ensure all moving parts are properly greased.
- Debris Removal: Regularly clean the machine to prevent dust accumulation.
- Inspection of Safety Features: Test emergency stop buttons and limit switches frequently.
By addressing these overlooked areas, companies can further enhance the reliability of their coil upenders.
3.4 Advanced Diagnostic Tools
Advanced diagnostic tools, such as thermal imaging cameras and IoT-enabled sensors, are becoming increasingly popular in coil upender maintenance. These tools provide real-time insights into machine performance, allowing operators to pinpoint issues with precision.
For example, thermal imaging can help identify overheating components, while IoT sensors provide continuous data on hydraulic pressure and electrical performance. Integrating these tools into a maintenance plan ensures a higher level of operational efficiency and safety.
Two Fact Statement with Explanation: One True, One False
- True: Vibration analysis can detect misaligned gears or worn bearings, preventing major failures.
Explanation: Vibration sensors identify irregular patterns, which indicate potential issues before they escalate. - False: Hydraulic fluid in coil upenders never needs replacement if the system is sealed.
Explanation: Hydraulic fluid degrades over time due to contaminants and heat, requiring regular replacement for optimal performance.
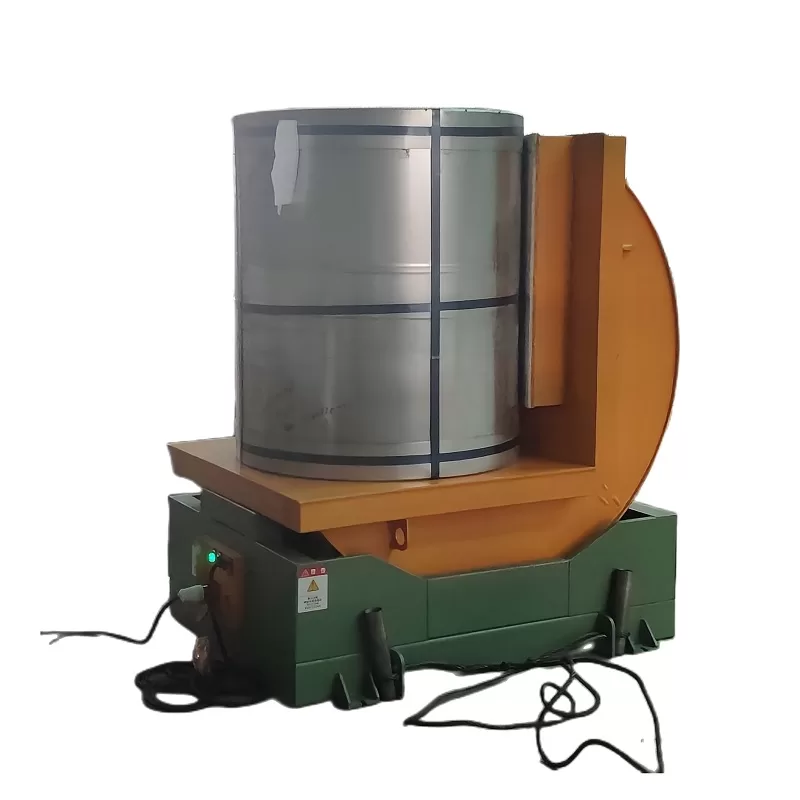
4. How to Choose the Right Maintenance Plan for Your Coil Upender?
4.1 Factors Influencing Maintenance Schedules
Choosing the right maintenance plan for your coil upender depends on several factors, including machine usage, operating environment, and load capacity. For instance, a coil upender used in a high-volume manufacturing plant will require more frequent inspections compared to one in a low-demand setting. Similarly, environmental conditions like humidity, dust, or temperature fluctuations can accelerate wear and tear.
Key considerations for determining maintenance schedules include:
- Frequency of Use: Machines operating 24/7 are more prone to wear and require shorter intervals between maintenance tasks.
- Load Size: Heavier loads put more strain on mechanical and hydraulic components, necessitating closer monitoring.
- Environment: Dusty or corrosive environments increase the risk of component damage, requiring additional cleaning and protective measures.
By evaluating these factors, companies can tailor a maintenance plan that balances cost efficiency with machine reliability.
4.2 Comparing Maintenance Plans
Maintenance plans can range from basic preventive strategies to comprehensive predictive solutions. Below is a comparison of common maintenance plans:
Maintenance Plans Comparison Table:
Plan Type | Features | Pros | Cons |
---|---|---|---|
Basic Preventive | Regular inspections, lubrication | Low cost, easy to implement | May miss hidden issues |
Predictive | IoT sensors, real-time monitoring | Minimizes downtime, accurate | Higher upfront cost |
Reactive | Repairs only after failure | No initial investment | High risk of costly downtime |
Comprehensive | Preventive + predictive | Maximum reliability | Expensive to implement |
For most businesses, a combination of preventive and predictive maintenance offers the best balance, ensuring cost savings while reducing the risk of unexpected failures.
4.3 Manufacturer-Recommended Guidelines
Manufacturers of coil upenders provide detailed maintenance guidelines tailored to their machines’ design and capabilities. These recommendations often include:
- Inspection Intervals: Most manufacturers suggest monthly or quarterly checks for mechanical, hydraulic, and electrical systems.
- Lubrication Schedules: Lubricating key components like bearings and gears every 500–1,000 operating hours is typically advised.
- Replacement Timelines: Parts like hydraulic seals and filters often have a specific lifespan and should be replaced according to the manufacturer’s schedule.
Adhering to these guidelines ensures the machine operates as intended, reducing the likelihood of warranty voids or premature failures.
4.4 Conclusion
Selecting the right maintenance plan requires a thorough understanding of your coil upender’s usage patterns and environmental conditions. Whether through basic preventive measures or advanced predictive analytics, a well-structured maintenance plan can significantly improve machine reliability and reduce costs.
[claim] Following manufacturer-recommended guidelines and tailoring maintenance plans to specific operational needs ensures optimal performance and longevity for your coil upender.
Two Fact Statement, One True, One False
- True: Coil upenders operating in dusty environments require more frequent maintenance to prevent debris-related damage.
Explanation: Dust can accumulate on moving parts, increasing friction and causing premature wear. - False: All coil upenders can operate efficiently without lubrication for up to a year.
Explanation: Without proper lubrication, components like bearings and gears will wear out quickly, leading to machine failure.

Conclusion
Coil upenders play a critical role in industrial operations, but their efficiency and longevity depend heavily on proper maintenance. From mechanical wear to hydraulic and electrical issues, understanding common challenges and implementing the right solutions can save companies significant time and money. Regular inspections, adherence to manufacturer guidelines, and leveraging predictive maintenance technologies are key to ensuring these machines remain reliable and safe.