Cold/ Hot Rolled Coil Automatic Packing Line Basic Specification
FHOPE team specifies that this document applies to the following types of coils:
1.Cold Rolled Coils: Suitable for cold rolled steel coils of various thicknesses and widths.
2.Hot Rolled Coils: Covers hot rolled steel coils of different specifications.
3.Galvanized Coils: Includes rust-proof and corrosion-resistant galvanized products.
4.Coated Coils: Suitable for painted or otherwise surface-treated coils.
5.Stainless Steel Coils: Suitable for stainless steel products of various thicknesses.
Adjustments can be made based on specific equipment configurations as needed.

I.A complete coil packaging line mainly consists of the following components:
- Main Unit: (1 set).
This is the central component of the wrapping machine, crucial for the packaging process. It manages several functions, including shuttle operation and packing material fixation with tension control through the coil eye. The machine offers automatic feeding and cutting of packing material and precise positioning for each coil based on its outer diameter. It is designed as an orbital wrapper, suitable for large mother coil packaging, ensuring efficient and reliable performance throughout the operation.
- Trolley: Packaging trolley (2 sets).
The packaging trolleys are designed to facilitate the movement of steel coils throughout the packaging process. Each set includes two trolleys, which are essential for efficiently transporting the coils to and from the packaging area, ensuring smooth workflow and minimizing handling time. For coil 360 degree turning.
- Equipment Operation: with HMI (1 set).
This station features a Human-Machine Interface (HMI) designed for easy operation and comprehensive monitoring of the packaging line. The HMI provides operators with an intuitive touchscreen interface, enabling them to control and adjust settings seamlessly to optimize performance. With real-time data display, operators can monitor key metrics such as speed, throughput, and error alerts, facilitating prompt decision-making. The user-friendly design minimizes the learning curve for new staff, enhancing overall productivity. .
- Electrical Control Cabinet: with air conditioning room (1 set).
This cabinet contains all the electrical components and control systems, such as the PLC, inverter, and drive, ensuring the equipment functions properly while protecting it from overheating. Built to industrial cabinet standards,IP55, it offers durability, safety, and efficient organization of electrical parts.
- Hydraulic System: (1 set).
This system delivers essential hydraulic power to the packaging machinery, ensuring safety, smooth and efficient operation. It is used for orbital locking and precise machine position fixing. The system includes a pump with a filter and 4 liters of hydraulic oil, providing the necessary force and control for the machinery’s movements.
- Spare Parts: 1 year (1 set).
A complete set of spare parts for one year of operation, ensuring that the line can be maintained and any necessary repairs can be conducted without delay. This comprehensive collection ensures that any necessary repairs can be conducted swiftly, minimizing downtime and preventing disruptions in production. By having the right parts readily available, maintenance teams can address issues proactively, enhancing the overall efficiency and reliability of the line.
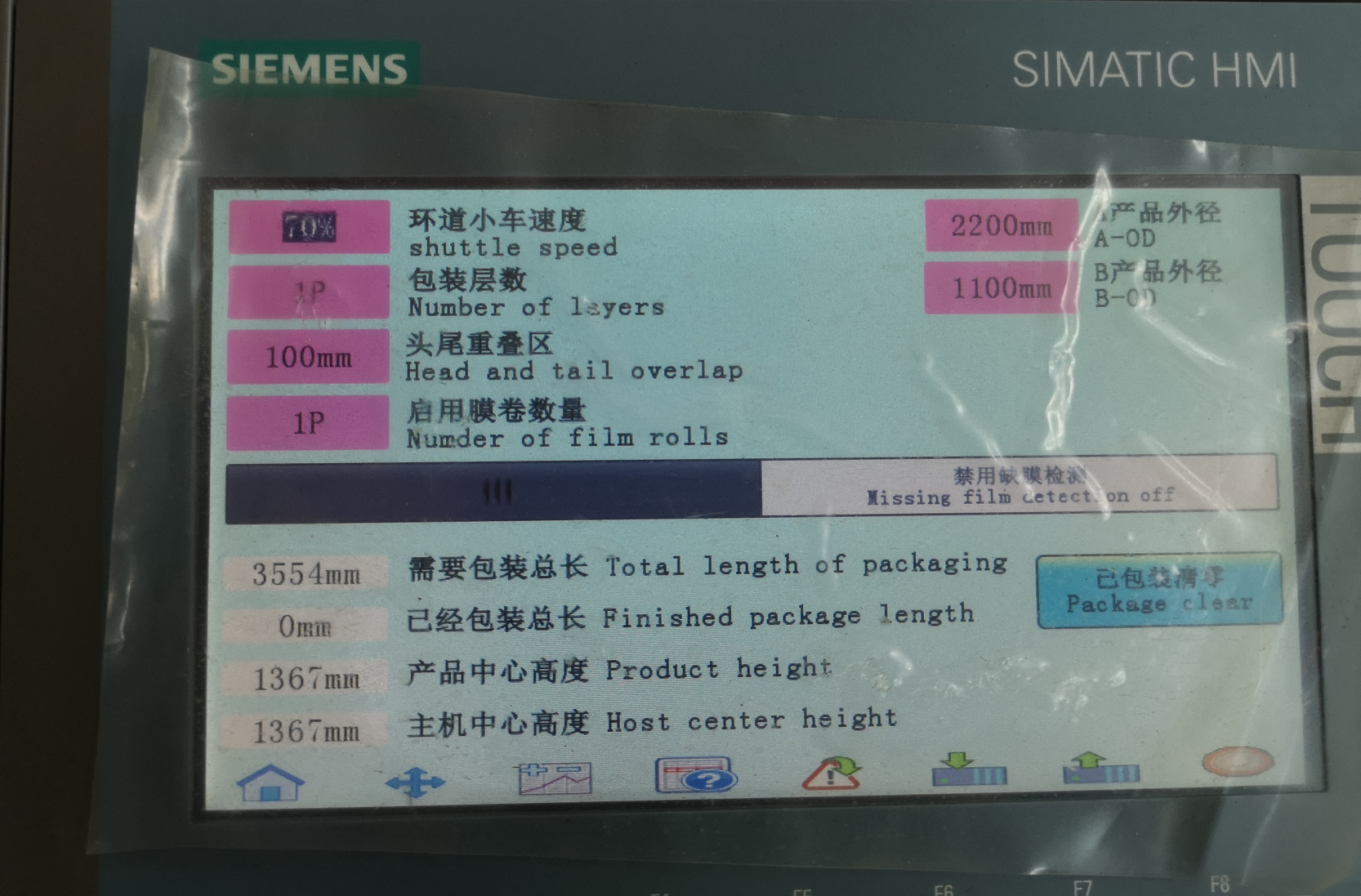
II.What are the main functions of FHOPE automatic packaging line?
Functional:
- Automatic Centering Wrapping:
The Automatic Centering Wrapping feature of the Horizontal Stretch Wrapper with Bubble Film Covering is designed for precision and ease of use. It automatically centers the item, loads the initial film, and manages film breaking, ensuring accurate alignment during wrapping. This feature also adjusts the height level according to the outer diameter of the item, providing a custom fit for each product. Moreover, it includes an inner diameter checking function and height level adjusting capability, allowing for further customization. The tension control feature ensures the right amount of tightness in the wrap, offering optimal protection for each item.
- Safety :
Safety features like a safety fence and an emergency stop switch. These tools offer enhanced protection for both operators and machinery. The interlock system and light beam add extra layers of security, while the fence’s 1800mm height ensures a safe boundary. In case of any unforeseen circumstances, the emergency stop switch allows for immediate equipment shutdown. The machine adheres to CE safety standards, thereby ensuring a secure and reliable working environment.
- Packaging Capacity :
Packaging capacity of 10 coils per hour or more (conditions as per section 6-5).
This ensures efficient production rates to meet operational demands. This capacity ensures that operational demands are met consistently, allowing for timely delivery and reducing the risk of backlog. Such efficiency helps in optimizing labor and resource utilization, ultimately contributing to increased profitability.
- Packaging Trolley :
Two packaging trolleys can achieve one packaging cycle while the other handles loading and unloading of the coil.
This arrangement maximizes efficiency by allowing continuous operation without downtime.
A setup not only accelerates the overall throughput but also enhances productivity, allowing for greater output within the same time frame.
- Covering :
Ability to use two types of packaging materials simultaneously.
This flexibility allows for different protective materials to be applied based on the product’s needs.
This flexibility enables the application of various protective materials tailored to the specific requirements of each product.
- Overlapping design:
Overlap rate adjustable to a range of at least 20-50%.
This feature allows customization of the film application for optimal protection.
By tailoring the overlap rate, operators can enhance the integrity and security of the packaged items, effectively minimizing the risk of damage from external factors such as moisture, dust, or physical impacts.
- Operation Console:
The operation station is divided into HMI control and button control panel.
This design enhances usability by providing multiple control options for operators.
HMI provides a user-friendly touchscreen interface for intuitive navigation and monitoring, while the button control panel allows for quick, tactile responses during critical tasks.
- Operation Control:
HMI and button control panel can operate independently.
This ensures flexibility in operation, allowing for both manual and automated control as needed.
This design allows operators to choose between manual and automated control based on the specific requirements of the task at hand. For example, during routine operations, the HMI can facilitate automated processes, enhancing efficiency and reducing the potential for human error.

III.Wire Rod Coil Specifications Requirements
- 3-1. Inner Diameter:
Inner diameter: 500-850 mm.
This specification ensures that the coils fit properly on the packaging equipment, facilitating efficient operation.
- 3-2. Outer Diameter
Outer Diameter: 800-1250 mm.
This specification defines the outer diameter of the wire rod coils as 1250 mm. This dimension is crucial for ensuring compatibility with packaging equipment and transport systems.
- 3-3. Width:
Width: 2000 mm (600 mm for a small amount).
The standard length of 2000 mm allows for optimal handling and storage, while the option for a shorter length accommodates specific product requirements.
- 3-4. Weight:
Weight: Below 5 tons.
This weight limit ensures that the coils can be safely handled by the packaging system, maintaining operational efficiency and safety standards.
IV.Other
- Packaging Materials:
Packaging material for testing should be provided until the equipment is accepted.
This ensures that all necessary materials are available for proper testing and validation of the packaging system before final acceptance.
Packaging material for testing must be supplied continuously until the equipment is officially accepted.
- Packaging Material Specifications:
Packaging material specifications are provided in the attachment.
specifications outline essential standards and characteristics of the packaging materials, ensuring they align with operational needs and quality requirements.
By clearly defining parameters such as durability, thickness, and moisture resistance, the specifications facilitate informed decision-making during the selection process. Adhering to these guidelines helps maintain product integrity throughout storage and transportation, reducing the risk of damage.
- Project service:
The Serive include on-site installation, commissioning by a technician, and training for equipment operation.
This ensures that the supplier provides comprehensive support, facilitating a smooth setup and effective training for operators to maximize the use of the equipment.
- PLC Program
PLC Program: All PLC program source codes must be provided.
This requirement ensures that the complete source code for the Programmable Logic Controller (PLC) is available for review, modification, and troubleshooting, allowing for future updates and maintenance.
- Operation Manual, Spare Parts List, and Circuit Diagrams
Operation Manual, Spare Parts List, and Circuit Diagrams Requirements:
Operation manual, spare parts list, and circuit diagrams should be provided in both hardcopy and PDF files.
This ensures that all necessary documentation is readily available for operators and maintenance personnel, facilitating effective operation and quick reference for repairs.
- Control Panel and Cabinet Labeling
Control Panel and Cabinet Labeling:
The operation station and cabinet labeling language should be in English, Chinese, and Vietnamese.
This multilingual requirement enhances usability for diverse operators, ensuring clear understanding of the controls and functions.
- Power Supply
Power Supply: AC 380V, 50Hz, 3-phase.
This specification outlines the necessary electrical supply for the equipment,ensuring compatibility with local power standards and safe operation.
- Indicator Light
Indicator Light Requirements:
Indicator lights should show red for operation, green for stop, and yellow for abnormal conditions.
This provides clear visual signals to operators, enhancing safety and operational awareness by indicating the system’s status at a glance.
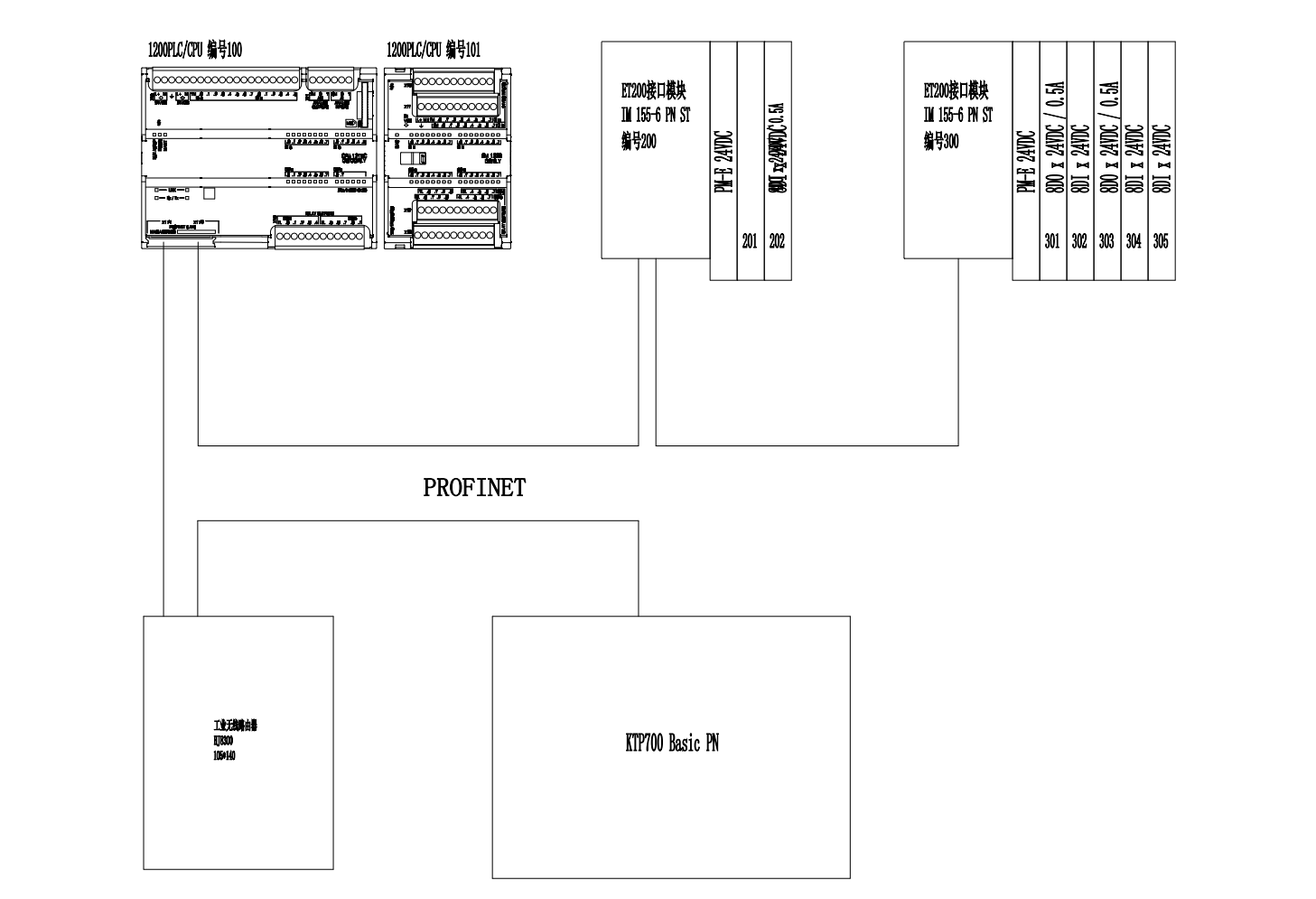
Accompanying Operation or User Manual
Provision of Documentation:
Provide the operation manual, spare parts list, and circuit diagrams in both hardcopy and PDF format to ensure accessibility and convenience for all users. Having these documents available in hard copy allows for quick reference during maintenance or operation, while the PDF versions can be easily shared and stored digitally for future access. This comprehensive documentation is crucial for training new staff, troubleshooting issues, and conducting routine maintenance.
Rejection Standard:
Operation manual, spare parts list, and circuit diagrams are not provided in both hard copy and PDF format, the goods will be subject to rejection. This requirement is essential to ensure that all operational and maintenance needs are met effectively. Without these critical documents, it becomes challenging for operators and technicians to understand the equipment fully, perform necessary repairs, or conduct proper training.
The absence of this documentation can lead to increased downtime, operational inefficiencies, and potential safety hazards.
Explanation:
All necessary documentation is included with the shipment, enabling users to operate and maintain the equipment effectively and safely. Comprehensive documentation, such as the operation manual, spare parts list, and circuit diagrams, provides critical information for troubleshooting and routine maintenance.
If these documents are missing, the shipment will not be accepted, as it could lead to operational delays and increased costs..