Coil Upenders: Comparing Key Features Across Different Models
Table Of Contents
- Coil Upenders: Comparing Key Features Across Different Models
- 1. Importance of Coil Upenders in Industrial Applications
- 2. Weight Capacity: Ensuring the Right Fit for Your Operation
- 3. Automation: Streamlining the Coil Handling Process
- 4. Rotation Speed and Efficiency
- 5. Safety Features: Protecting Workers and Equipment
- 6. Ease of Operation: Comparing User Interfaces
- 7. Maintenance: Durability and Longevity Comparison
- 8. Customization: Tailoring Features to Meet Specific Needs
- Conclusion
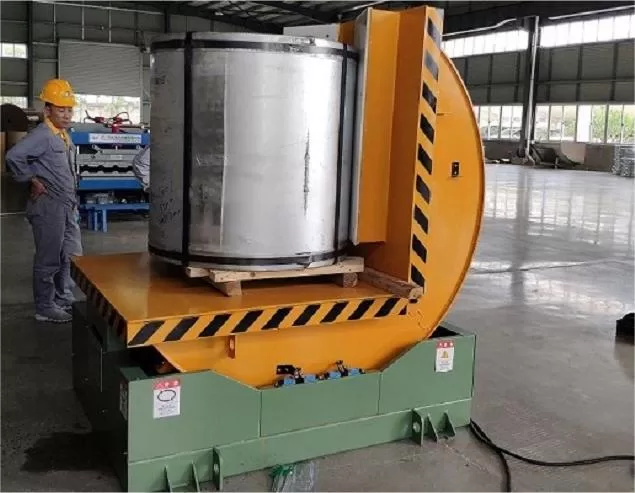
Coil upenders play a critical role in industries that handle large, heavy coils—whether they are made of steel, aluminum, or other materials. These machines are designed to rotate coils from a horizontal to a vertical position or vice versa, making them easier and safer to handle during various stages of production, storage, and shipping. Choosing the right coil upender is essential for ensuring efficiency, safety, and reliability in your operation. However, with the wide range of models available, it can be challenging to determine which features best meet your needs.
In this article, we will explore the key features that differentiate coil upenders across various models, helping you make an informed decision. We’ll examine factors such as capacity, automation, safety features, and other critical specifications that impact the performance of these machines.
1. Importance of Coil Upenders in Industrial Applications
Before diving into the specific features of different models, it’s essential to understand why coil upenders are so important. Industries that handle large coils, such as steel manufacturers, rely on upenders to safely flip coils during different stages of production. These machines reduce the risk of worker injury, minimize product damage, and enhance the efficiency of material handling.
Without the use of coil upenders, companies would have to rely on manual methods or basic equipment, which can increase safety risks and slow down operations. Investing in the right coil upender can streamline the handling process, reduce operational downtime, and improve the overall productivity of the facility.
2. Weight Capacity: Ensuring the Right Fit for Your Operation
One of the most important features to consider when selecting a coil upender is its weight capacity. Coil upenders come in various sizes and are designed to handle different weights, ranging from a few hundred kilograms to several tons. The weight capacity you choose should be aligned with the maximum weight of the coils your facility handles.
a) Standard Capacity vs. Heavy-Duty Models
Smaller, standard capacity models can handle coils weighing between 500 kg and 2 tons. These models are ideal for lighter operations or industries that don’t regularly deal with extremely heavy coils. On the other hand, heavy-duty models can manage loads of up to 50 tons or more. These are more suitable for large-scale industrial environments where coils are significantly heavier.
When evaluating different models, it’s crucial to consider both the present and future demands of your operation. Investing in a machine with a slightly higher capacity than you currently need can provide flexibility as your business grows.
3. Automation: Streamlining the Coil Handling Process
Automation is a key differentiator between basic coil upender models and more advanced, state-of-the-art options. In recent years, the integration of automation in coil upenders has significantly enhanced safety, precision, and efficiency.
a) Manual vs. Automated Upenders
Manual coil upenders require direct operator intervention for loading, flipping, and unloading coils. While these models are more cost-effective, they require more labor and carry a higher risk of human error.
Automated models, on the other hand, use programmable logic controllers (PLCs) and sensor-based systems to perform the flipping process with minimal human input. These upenders can be programmed for specific tasks, reducing the likelihood of mistakes and speeding up the coil handling process. Automation also improves workplace safety by limiting the direct involvement of workers in dangerous operations.
b) Semi-Automatic Options
For businesses that want the best of both worlds, there are semi-automatic coil upenders that offer a mix of manual and automated functions. These machines allow operators to control certain aspects of the process while automating others, offering flexibility without fully committing to a fully automated system.
4. Rotation Speed and Efficiency
The speed at which an upender can rotate a coil plays a significant role in the overall efficiency of the handling process. Some models are designed for faster rotations, allowing for high throughput in busy production environments, while others may prioritize safety over speed, rotating coils more slowly to reduce the risk of damage or accidents.
a) High-Speed Models
For facilities that need to handle large volumes of coils in a short time, high-speed coil upenders are the ideal choice. These models are designed to flip coils quickly, ensuring that the workflow remains uninterrupted. However, it’s essential to balance speed with safety, as faster machines may require additional safety measures to prevent accidents.
b) Variable Speed Control
Some coil upenders feature variable speed control, which allows operators to adjust the rotation speed depending on the coil's size and weight. This flexibility is especially useful for facilities that handle coils of different dimensions, as it ensures that each coil is flipped at the optimal speed, reducing the risk of damage.
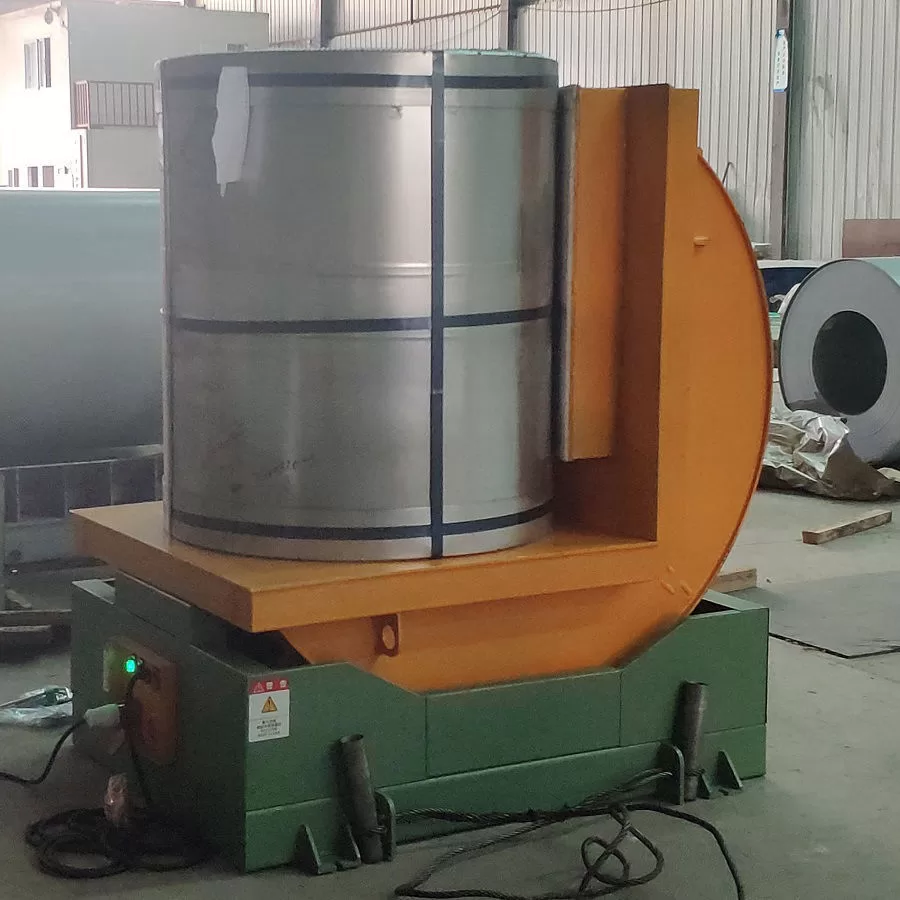
5. Safety Features: Protecting Workers and Equipment
Safety features are a key consideration when comparing different coil upender models. The level of safety that a machine offers can vary significantly based on the design and technology integrated into it. While basic models may come with standard safety guards, more advanced versions offer sophisticated safety mechanisms to reduce risks in busy industrial environments.
a) Basic Models: Essential Safety Protections
In simpler coil upenders, the most common safety feature is the emergency stop button, which allows operators to halt the machine immediately in case of malfunction. Some basic models also come with protective barriers, ensuring that workers are shielded from moving parts during the upending process. These features provide essential protection but may not offer the advanced prevention mechanisms found in more high-end models.
b) Advanced Models: Cutting-Edge Safety Innovations
Higher-end models are equipped with automated safety sensors and additional protective barriers. These sensors can detect obstructions in the machine’s path and automatically stop operations if a worker or object is too close, significantly reducing the risk of accidents. Advanced models may also come with lock-out/tag-out systems that prevent the machine from being operated during maintenance or repair work.
6. Ease of Operation: Comparing User Interfaces
Another critical comparison between different coil upender models lies in their ease of operation. The usability of a machine can have a direct impact on productivity and safety, so it’s important to evaluate how user-friendly each model is.
a) Manual Models: Basic Operation with Higher Labor Needs
Manual coil upenders often feature simple control panels with basic levers or switches. While these machines are typically more affordable, they require more manual input and higher labor to operate effectively. The learning curve for new operators might be steeper, and the potential for operator fatigue is higher, especially in busy production lines.
b) Automated Models: Intuitive and Efficient Controls
Automated upenders, on the other hand, offer more intuitive control panels, often featuring touchscreen interfaces that allow operators to monitor and control operations with ease. These machines often include pre-programmed settings, which reduce the need for manual input, making the entire process more efficient. For companies looking to reduce human error and improve operational speed, automated models present a clear advantage.
7. Maintenance: Durability and Longevity Comparison
The maintenance requirements of coil upenders can vary significantly depending on the model. Some machines are designed for heavy-duty use with minimal maintenance, while others may require more frequent checks and part replacements.
a) Low-Maintenance Models
For businesses that prioritize uptime, some low-maintenance models are built with long-lasting components and easy access points for repairs. These machines may feature self-lubricating parts and simplified maintenance schedules, making them ideal for operations that cannot afford prolonged downtime.
b) Heavy-Duty Models with Advanced Durability
Heavy-duty models are often built with reinforced steel and high-strength components, offering greater durability over time. These models, while more expensive, are built to withstand more intensive use and heavier loads without frequent maintenance. Facilities handling larger or heavier coils may prefer these models for their long-term durability and reduced likelihood of breakdowns.
8. Customization: Tailoring Features to Meet Specific Needs
Another aspect where coil upenders can differ is the level of customization they offer. Businesses that handle specialized coils or have unique operational workflows may require upenders that can be tailored to their specific needs.
a) Standard Models: Off-the-Shelf Solutions
Basic coil upenders are typically off-the-shelf products with standard features and sizes. These models are suitable for most general applications but may not fit perfectly into facilities with more specialized needs. They are typically quicker to install and more budget-friendly.
b) Custom-Built Models: Tailored to Precision
For industries that handle non-standard coil sizes or have specific space constraints, custom-built coil upenders offer a significant advantage. These machines can be designed to accommodate unusual coil dimensions or to integrate seamlessly into an existing production line. Customization options might include modified coil cradles, specialized safety features, or unique automation capabilities.
Conclusion
Choosing the right coil upender requires careful consideration of key features across different models. From weight capacity and automation to safety and customization options, each feature plays a role in determining which machine best suits your operational needs. Basic models offer cost-effective solutions for smaller operations, while advanced, automated upenders provide superior efficiency, safety, and ease of use for larger industrial environments.
By understanding the comparative advantages of each type of coil upender, businesses can make informed decisions that enhance productivity, improve safety, and reduce downtime. Whether you are opting for a more manual machine or investing in a high-end automated model, ensuring the machine meets both current and future demands is crucial for long-term success in coil handling operations.