Coil Tilter Materials and Build Quality: A Guide to Choosing Durable Industrial Equipment
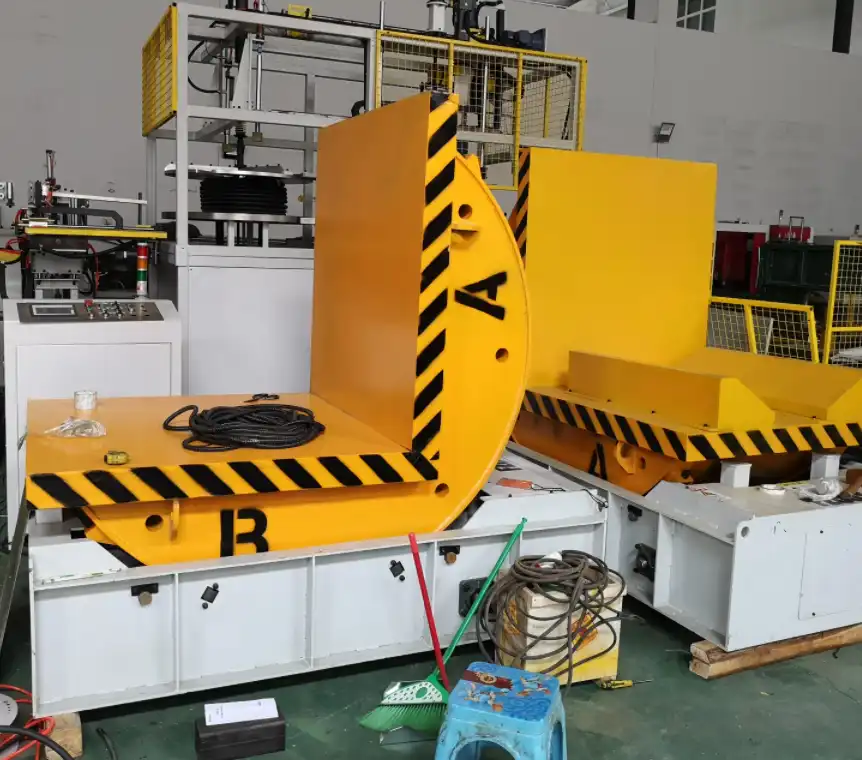
When investing in critical industrial machinery like a coil tilter (also known as a coil upender), ensuring durability and long-lasting performance is paramount. The reliability of your coil handling equipment directly impacts operational efficiency and safety, significantly depending on its materials and build quality. A poorly constructed machine can lead to frequent, costly maintenance, unexpected downtime, and potential safety hazards. This guide explores the essential factors to consider when selecting a durable coil tilter, focusing on material selection, construction techniques, and key performance indicators.
1. The Crucial Role of Coil Tilters in Metal Processing
Coil tilters are indispensable in industries involved in steel, aluminum, and other metal coil processing and handling. Their primary function is to safely and efficiently rotate heavy coils between horizontal and vertical orientations, simplifying subsequent handling, storage, and transportation tasks. This process enhances workflow speed, improves logistical efficiency, and crucially, minimizes the risks associated with manually handling heavy, unwieldy loads.
Given that these machines must consistently manage substantial weights and endure the demands of frequent industrial use, the quality of their construction and the materials used are non-negotiable aspects. Equipment built with substandard materials or poor craftsmanship is susceptible to accelerated wear and tear, potentially causing operational failures, costly production halts, and escalating repair expenses. Therefore, a thorough understanding of coil tilter materials and build quality is the foundation for making a sound investment.
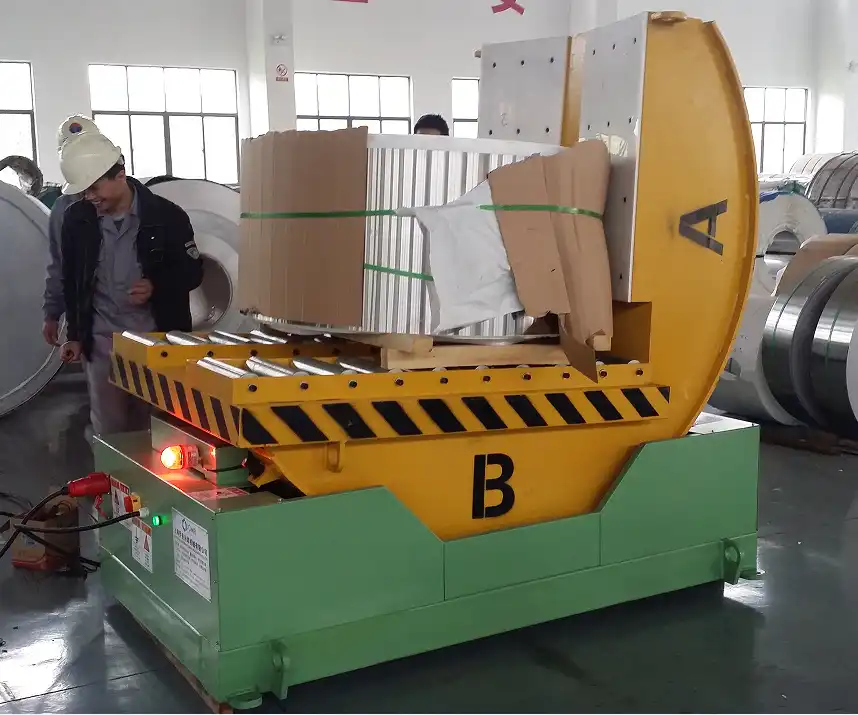
2. Key Materials Shaping Coil Tilter Durability
Material selection is arguably the most critical factor influencing a coil tilter's longevity and performance. The materials used for the frame, tilting mechanism, contact surfaces, and other vital components dictate the machine’s overall strength, resistance to wear, and ability to withstand demanding operational conditions.
Common materials used in high-quality coil tilters include:
- High-Grade Steel: This is the cornerstone material for most coil tilters due to its exceptional strength, toughness, and resistance to deformation under heavy loads. Machines built with robust, high-quality steel frames and structural components can handle significant weight capacities without buckling or structural failure. For environments with moisture or corrosive agents, stainless steel or properly coated carbon steel is often employed for critical parts to enhance corrosion resistance.
- Aluminum: While less common for primary structural components due to lower strength compared to steel, aluminum alloys are sometimes used for specific parts like guards or covers to reduce overall machine weight. Its natural corrosion resistance is an advantage. However, any aluminum components in load-bearing areas must be engineered appropriately to ensure sufficient strength for industrial applications.
- Cast Iron: Renowned for its excellent compressive strength and vibration damping properties, cast iron is frequently used for base components or counterweights in coil tilters. Its weight and rigidity contribute to the machine's stability during operation.
- Polyurethane, Nylon, and Rubber: These durable polymers and elastomers are typically used for contact pads, rollers, or protective linings – surfaces that directly interact with the coil. They provide essential functions like protecting the coil surface from scratches or damage, offering grip, and reducing friction during the tilting process. The quality and type of these materials impact both coil protection and component lifespan.
Selecting a coil tilter constructed with the optimal combination of these materials ensures a longer operational life and reduces the frequency of repairs and component replacements.
3. Assessing Build Quality: What Defines a Robust Coil Tilter?
Beyond the raw materials, the build quality – the precision and care taken during manufacturing and assembly – is crucial for a coil tilter's performance and durability. Superior construction techniques translate into greater structural integrity, smoother operation, and enhanced safety. Key indicators of build quality include:
a. Welding and Joint Integrity
Welds are critical points in the structure. They must be expertly executed to handle the immense and repetitive stresses involved in lifting and tilting heavy coils. Poor quality welds (e.g., incomplete penetration, porosity, cracks) create weak points that can compromise the frame's integrity and lead to premature failure. Look for machines with clean, consistent, and full-penetration welds, often indicative of adherence to recognized welding standards (like AWS).
b. Precision Machining and Assembly
Components like bearings, pivot points, and drive mechanisms require precise machining and alignment for smooth, efficient, and low-wear operation. Tight tolerances ensure parts fit together perfectly, minimizing friction, vibration, and uneven load distribution. High-precision manufacturing contributes significantly to operational reliability and extends the machine's service life.
c. Reinforced Structural Components
For equipment designed to handle heavy coils (often weighing many tons), strategic reinforcement of key structural elements is vital. This may involve thicker steel plates, gussets at stress points, or specially designed profiles for lifting arms, the base frame, and pivot mechanisms. These reinforcements provide the extra strength needed to withstand peak loads and fatigue over years of service.
d. Corrosion Protection and Surface Finish
Industrial environments can be harsh, exposing machinery to moisture, chemicals, dust, and temperature fluctuations, all of which can lead to corrosion. Durable coil tilters feature effective corrosion protection measures. This typically includes high-quality industrial paint, powder coating, or galvanizing applied over properly prepared surfaces. Stainless steel components may also be used where necessary. A resilient finish not only protects the underlying metal but also makes cleaning easier.
4. Evaluating Key Components for Longevity
While overall build quality is important, the durability of specific key components significantly impacts the machine's reliability:
a. Frame and Structure
The frame is the literal backbone of the coil tilter, bearing the entire load and providing structural stability. A robust heavy-duty steel frame, designed using sound engineering principles (like Finite Element Analysis - FEA), is essential. Look for thick steel sections, strong welds (as mentioned above), and a design that distributes stress effectively to prevent bending, twisting, or warping under load.
b. Hydraulic or Electromechanical System
Most industrial coil tilters use either a hydraulic system or an electromechanical system (using motors and gearboxes/actuators) for the tilting motion.
- Hydraulics: Must feature high-quality cylinders, seals, pumps, valves, and hoses rated for industrial duty cycles. Reliable seals prevent leaks, while robust pumps and valves ensure consistent power and control. Look for systems designed for ease of maintenance (e.g., accessible filters, pressure gauges).
- Electromechanical: Requires industrial-grade motors (often TEFC - Totally Enclosed Fan Cooled), durable gearboxes, and robust actuators capable of handling the required torque and frequent starts/stops without overheating or premature wear.
c. Motors, Gearboxes, and Bearings
The drive motor(s) and associated gear reducers are the heart of the movement system. They must be appropriately sized for the load capacity and duty cycle. Look for reputable motor/gearbox brands known for reliability in industrial settings. High-quality, properly sealed bearings at all pivot points are critical for smooth movement and longevity, minimizing friction and wear.
d. Control System and Electrics
Modern coil tilters feature electrical control systems for operation, safety interlocks, and potentially automation. The reliability of components like PLCs (Programmable Logic Controllers), sensors (limit switches, proximity sensors), contactors, wiring, and operator interfaces (buttons, HMI screens) is crucial. Look for robust, well-protected enclosures (e.g., NEMA rated), neatly organized wiring, and intuitive, reliable controls. Poorly designed or implemented electrical systems can be a major source of downtime.
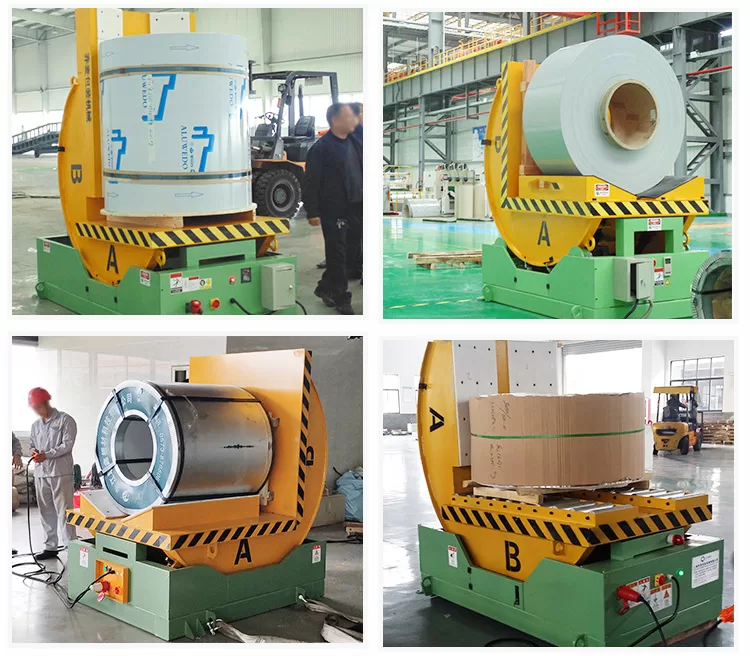
5. Maintenance Considerations for Lasting Durability
Even the best-built coil tilter requires consistent preventive maintenance to ensure its long-term durability and safe operation. When evaluating a machine, consider its maintainability:
- Accessibility: Are lubrication points, filters, hydraulic components, and electrical panels easily accessible for inspection and service? Poor access increases maintenance time and cost.
- Documentation: Does the manufacturer provide clear and comprehensive maintenance manuals, including schedules, procedures, and parts lists?
- Standard Components: Does the machine utilize readily available standard components (bearings, seals, hydraulic parts, electrical components), or does it rely heavily on proprietary parts that might be expensive or hard to source?
Adhering to a disciplined maintenance schedule is vital:
- Follow Manufacturer’s Guidelines: Strictly adhere to the recommended lubrication, inspection, and service intervals outlined in the manual.
- Address Wear Promptly: Replace components like hydraulic seals, hoses, contact pads, bearings, or filters as soon as they show signs of wear or damage. Delaying replacement can lead to cascading failures and more significant repairs.
- Conduct Regular Inspections: Implement routine visual inspections (daily or weekly) to check for leaks, loose fasteners, unusual noises, structural damage, or control system issues. Early detection prevents major problems.
6. Selecting a Reputable Coil Tilter Manufacturer
The manufacturer's reputation and experience are strong indicators of the likely quality and durability of their equipment. Choosing a well-established manufacturer specializing in heavy-duty industrial machinery offers several advantages:
- Proven Engineering: Experienced manufacturers typically have refined designs based on years of field experience and customer feedback.
- Quality Control: Reputable companies usually have robust quality control processes throughout manufacturing.
- After-Sales Support: Look for manufacturers offering solid warranty terms, responsive technical support, and reliable spare parts availability. This support is crucial for minimizing downtime if issues arise.
- Industry Standards: Established manufacturers are more likely to build equipment compliant with relevant safety and industry standards (e.g., OSHA, ANSI, CE).
- Customer References: Positive testimonials and a strong track record within your industry provide confidence in the manufacturer's capabilities.
7. Balancing Cost and Durability: Total Cost of Ownership (TCO)
While the initial purchase price is a significant factor, opting for the cheapest coil tilter can be a costly mistake in the long run. Low-cost machines often achieve their price point by compromising on material quality, component robustness, or manufacturing precision.
Consider the Total Cost of Ownership (TCO), which includes:
- Initial purchase price
- Installation and commissioning costs
- Ongoing maintenance and repair costs
- Spare parts costs
- Energy consumption
- Cost of downtime (lost production, labor costs during standstill)
Investing in a higher-quality, more durable coil tilter may involve a higher upfront cost, but it typically leads to lower TCO over the machine's lifespan due to:
- Reduced frequency and severity of breakdowns
- Lower maintenance requirements
- Longer operational life
- Improved safety and reliability
- Higher operational efficiency
upender & tilter Conclusion: Investing Wisely in Coil Tilter Durability
Choosing the right coil tilter demands a careful evaluation of materials, build quality, key components, and long-term operational factors. A machine constructed from high-grade steel, featuring precision engineering, robust hydraulics or electromechanical systems, and built by a reputable manufacturer represents a sound investment.
Prioritizing durability might require a larger initial outlay, but the long-term benefits – including enhanced safety, reduced downtime, lower maintenance expenditures, and greater overall operational efficiency – far outweigh the savings from choosing a lower-quality alternative. By focusing on the factors outlined in this guide and committing to proper preventive maintenance, you can ensure your coil tilter provides reliable, efficient service for many years, supporting your critical production and handling needs.

Get Your Best Solution !