Choosing the Best Pallet Inverter for Cold Storage vs. Dry Warehousing
- Choosing the Best Pallet Inverter for Cold Storage vs. Dry Warehousing
- Introduction
- 1. Understanding the Role of a Pallet Inverter
- 2. Key Differences Between Cold Storage and Dry Warehousing
- 3. Factors to Consider When Choosing a Pallet Inverter for Cold Storage
- 4. Factors to Consider for Dry Warehousing Inverters
- 5. Types of Pallet Inverters and Their Applications
- 6. The Advantages of Pallet Inverters in Cold Storage Operations
- 7. Benefits of Pallet Inverters in Dry Warehousing
- 8. Comparing Maintenance Requirements: Cold Storage vs. Dry Warehousing
- 9. How Automation Impacts Efficiency in Cold Storage and Dry Warehousing
- 10. Energy Efficiency Considerations
- 11. Cost Comparison: Cold Storage vs. Dry Warehousing Pallet Inverters
- 12. Choosing the Right Inverter for Your Facility
- Conclusion
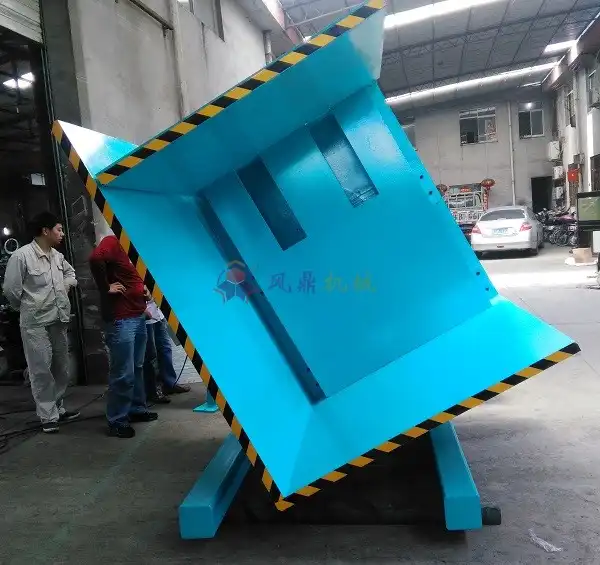
Introduction
The logistics of managing pallets is a core concern for many industries, particularly in cold storage and dry warehousing. Both environments have distinct needs when it comes to handling and rotating heavy loads, which is why pallet inverters have become essential tools in modern operations. Whether you’re working in frozen environments or maintaining a temperature-controlled dry warehouse, selecting the right pallet inverter is crucial to enhancing efficiency, safety, and reducing operational costs.
1. Understanding the Role of a Pallet Inverter
Before diving into the comparison, it’s essential to understand what a pallet inverter is and its role in material handling. A pallet inverter is a machine designed to rotate, tilt, or turn pallets to access the goods on the pallet more efficiently. They help businesses save time and labor by automating the process of rotating goods without manually handling each item.
Pallet inverters are used across various industries such as food and beverage, pharmaceuticals, and manufacturing to replace damaged pallets, switch loads from wooden to plastic pallets, or remove damaged products from the bottom of a stack. The primary goal is to increase efficiency and safety while reducing labor costs.
2. Key Differences Between Cold Storage and Dry Warehousing
When comparing cold storage and dry warehousing, there are distinct environmental and operational differences that impact the choice of pallet inverter.
Cold Storage: In cold storage, environments can range from freezing temperatures to sub-zero levels. The key concern here is preventing equipment malfunctions due to frost, condensation, and extreme temperature fluctuations. Cold storage facilities often handle perishable goods, so operational speed and equipment reliability are critical.
Dry Warehousing: On the other hand, dry warehousing operates in normal temperature conditions, primarily focusing on the storage of dry goods like electronics, textiles, and hardware. The need for speed and precision is still important, but there are fewer environmental challenges to contend with compared to cold storage.
Understanding these differences helps businesses tailor their selection of pallet inverters to the unique demands of each environment.
3. Factors to Consider When Choosing a Pallet Inverter for Cold Storage
Cold storage facilities face unique challenges that require specialized equipment. Here are the key factors to consider:
Temperature Resistance: The most critical factor for cold storage pallet inverters is their ability to operate in sub-zero temperatures. Look for models with insulated electronics and robust materials that can withstand harsh conditions without freezing or breaking down.
Anti-Corrosion Materials: Due to the humidity and condensation common in cold environments, it’s important to choose pallet inverters made from stainless steel or materials with corrosion-resistant coatings to prevent rust and extend the machine’s lifespan.
Sealed Bearings and Components: In cold storage, condensation can lead to component failure if not properly addressed. Inverters with sealed bearings and components are better suited to this environment as they resist moisture and condensation buildup.
Speed and Efficiency: Time is money, especially in cold storage where energy costs are higher. You’ll want an inverter that can perform quickly and smoothly to minimize the time that doors are open, preventing cold air loss and helping maintain optimal storage temperatures.
4. Factors to Consider for Dry Warehousing Inverters
Dry warehousing, while less environmentally demanding, still requires pallet inverters that can handle the specific needs of the operation. Key considerations include:
Versatility in Pallet Types: Dry warehouses often deal with a variety of pallet types, from wooden pallets to plastic and metal ones. Look for a pallet inverter that can accommodate different materials without requiring constant adjustments.
Durability and Load Capacity: Even though temperature isn’t a concern, the sheer volume of goods handled in a dry warehouse can be overwhelming. It’s essential to choose a pallet inverter that has a high load capacity and is durable enough to withstand continuous operation over long shifts.
Automation and Integration: Many dry warehouses are shifting towards automated material handling systems. Ensure that the pallet inverter you choose can be easily integrated into your existing workflow, whether through automated conveyors or palletizing systems.
5. Types of Pallet Inverters and Their Applications
There are several different types of pallet inverters, each suited for specific applications. Understanding these types can help you choose the best inverter for your needs.
Single Clamp Pallet Inverter: This type is great for smaller operations that need to invert loads on a frequent but not constant basis. It’s easy to use and efficient for most general warehousing applications.
Double Clamp Pallet Inverter: For more secure handling, a double clamp inverter can hold the load more securely during the inversion process, making it ideal for fragile or irregularly shaped goods, often found in cold storage.
180-Degree Inverter: A 180-degree inverter fully rotates the pallet, which is useful for situations where the goods need to be completely flipped, such as for changing out damaged pallets or accessing items at the bottom of a stack. These are commonly used in both cold and dry environments.
6. The Advantages of Pallet Inverters in Cold Storage Operations
Cold storage environments demand fast and reliable equipment to minimize the risk of spoilage. Pallet inverters offer several advantages in these operations:
Time Savings: With the high cost of refrigeration, cold storage facilities benefit from pallet inverters that reduce handling time. This minimizes door opening times, helping maintain consistent storage temperatures and reducing energy consumption.
Improved Safety: Handling heavy loads in cold environments can be hazardous due to the risk of slips and falls. A pallet inverter eliminates much of the manual labor required in pallet handling, thereby reducing the risk of injury.
Product Protection: Frozen goods are often fragile and prone to damage when manually handled. Pallet inverters automate the process, ensuring less damage to goods and better product quality control.

Get Your Best Solution !
7. Benefits of Pallet Inverters in Dry Warehousing
While dry warehousing may not have the same environmental challenges as cold storage, pallet inverters still bring several benefits to these operations:
Increased Efficiency: Automating the process of pallet inversion saves valuable time and allows warehouse workers to focus on other tasks. This can lead to a significant boost in productivity.
Labor Cost Reduction: Manual pallet handling is labor-intensive and can increase operational costs. By using a pallet inverter, dry warehouses can reduce the number of workers needed for pallet handling tasks, saving on labor costs.
Versatility: Dry warehouses often handle a wide range of products, from heavy machinery to delicate electronics. A pallet inverter allows for safe and efficient handling of a variety of goods, reducing the risk of product damage during handling.
8. Comparing Maintenance Requirements: Cold Storage vs. Dry Warehousing
Maintenance is a crucial consideration when selecting a pallet inverter, as the operational environment directly affects how often servicing will be required.
Cold Storage: In cold storage, pallet inverters must endure harsh, freezing conditions. This means that the machinery is more prone to wear and tear due to temperature fluctuations, frost, and condensation. Regular maintenance checks are essential to prevent malfunctioning caused by frozen parts or corrosion. Additionally, lubricants used in cold storage must be specially formulated for low-temperature environments, ensuring that the components function smoothly despite the cold.
Dry Warehousing: Maintenance in dry warehousing is typically less intensive, as environmental factors like temperature and humidity are more stable. However, due to the often higher volume of loads handled, there can be wear on mechanical components from frequent use. Regular maintenance should focus on preventing mechanical breakdowns and ensuring the inverter’s capacity matches the operational demand.
9. How Automation Impacts Efficiency in Cold Storage and Dry Warehousing
The rise of automation in material handling systems is transforming both cold storage and dry warehousing. The impact of automated pallet inverters can be seen in various operational improvements.
Cold Storage: In cold environments, automation offers substantial benefits in reducing the amount of time employees spend in freezing conditions. Pallet inverters equipped with automated controls reduce manual handling, allowing the machine to process loads autonomously. This not only minimizes exposure to extreme temperatures but also ensures faster turnover, which is crucial for keeping energy costs low.
Dry Warehousing: In dry warehousing, automation is equally beneficial, allowing for faster throughput and greater precision in handling. Automated pallet inverters can be integrated into broader warehouse management systems (WMS), allowing for seamless operations without the need for constant human intervention. Automation also aids in maintaining consistency, ensuring pallets are handled uniformly, which reduces errors and damage.
10. Energy Efficiency Considerations
Energy efficiency is a critical aspect of pallet inverter selection, especially for businesses looking to reduce their carbon footprint and operational costs.
Cold Storage: Cold storage facilities are notoriously energy-intensive due to the refrigeration requirements. Selecting a highly efficient pallet inverter is essential to reduce power consumption. Many cold storage pallet inverters are designed with energy-saving features such as lower idle power draw and high-efficiency motors. Additionally, the faster the inverter can perform its function, the less time the facility’s doors are open, which minimizes the loss of cold air and lowers energy usage.
Dry Warehousing: Energy efficiency is still important in dry warehouses, though less critical than in cold storage. The focus should be on inverters with minimal power consumption during operation and idle periods. Implementing pallet inverters that can integrate into energy management systems can further help reduce overall power usage.
11. Cost Comparison: Cold Storage vs. Dry Warehousing Pallet Inverters
When it comes to cost, both initial investment and long-term operational expenses should be considered.
Cold Storage: Pallet inverters for cold storage are typically more expensive due to the additional features needed to withstand freezing environments. These features include insulated components, anti-corrosion materials, and special lubricants. However, these inverters can save on long-term operational costs by reducing energy usage and minimizing the risk of product loss due to temperature fluctuations.
Dry Warehousing: Pallet inverters for dry warehouses tend to be more affordable, as they don’t require the specialized materials and components needed for cold storage. The operational costs are also generally lower, as these inverters don’t have to contend with harsh environmental conditions. However, high-volume warehouses may need to invest in more robust equipment to handle continuous use, which can raise costs.
12. Choosing the Right Inverter for Your Facility
To choose the right pallet inverter for your facility, it’s essential to weigh the specific needs of your operation. Here are some final tips to help guide your decision:
Evaluate Your Operational Needs: Consider the volume of pallets handled daily, the types of goods stored, and the specific challenges your facility faces. Cold storage facilities should prioritize inverters that can withstand freezing temperatures, while dry warehousing should focus on inverters that offer versatility and durability.
Consider Long-Term Costs: While the upfront cost of a pallet inverter is important, long-term costs such as maintenance, energy consumption, and potential productivity gains should also factor into your decision.
Seek Expert Consultation: If you’re unsure which pallet inverter is best for your needs, consulting with experts in the field can help you make an informed decision. Many manufacturers offer customization options to tailor their products to specific environments, so be sure to explore these possibilities.
Conclusion
Choosing the best pallet inverter for cold storage or dry warehousing involves a careful evaluation of your operational requirements, environmental challenges, and long-term costs. Cold storage facilities need inverters that can withstand freezing temperatures and reduce energy consumption, while dry warehouses should focus on inverters that provide versatility, speed, and efficiency. By understanding the unique needs of each environment and selecting a pallet inverter tailored to those needs, businesses can improve efficiency, reduce costs, and create a safer working environment.
This comparison highlights the importance of choosing the right pallet inverter to meet your facility's demands. Whether you are operating in cold or dry environments, the correct pallet inverter can make a significant difference in productivity, safety, and cost savings.

Get Your Best Solution !