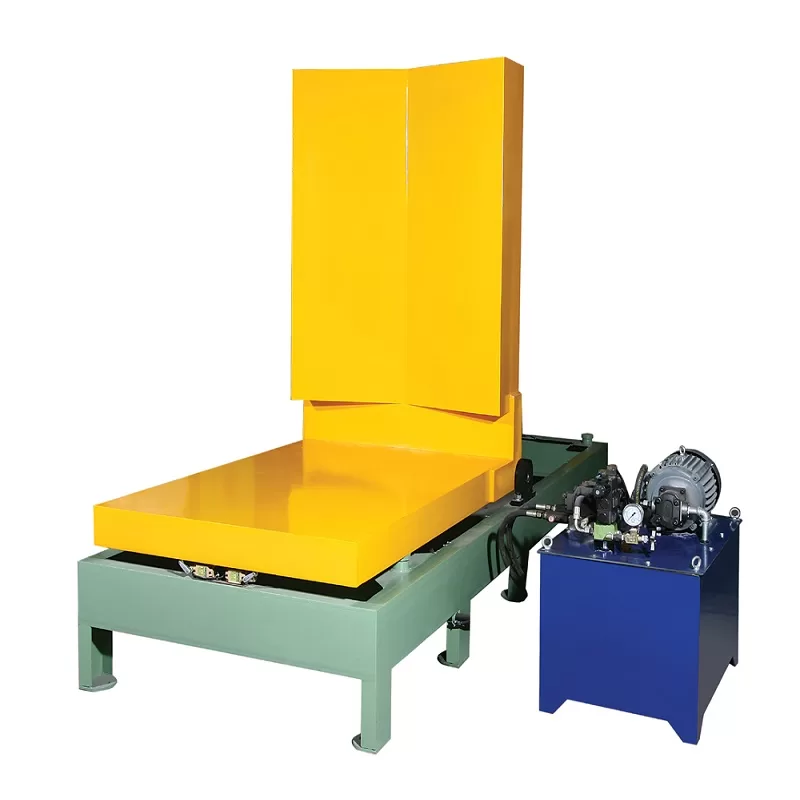
When it comes to handling heavy coils in industrial settings, coil upenders are essential. They streamline operations, minimize manual labor, and reduce the risk of workplace injuries. However, selecting the right configuration for your specific needs can be daunting. With various models, features, and capacities available, making the wrong choice could result in inefficiencies or even damage to your materials.
The decision is not as straightforward as it may seem. Each coil upender configuration is designed to cater to specific industries, coil sizes, and operational demands. What works perfectly in a steel manufacturing plant may be entirely unsuitable for a warehouse handling lightweight aluminum coils. Understanding these differences is crucial to making an informed decision.
This article explores the most common coil upender configurations, their advantages, and the factors to consider when choosing the right one for your operations. By the end, you’ll have a clear understanding of how to match your needs with the ideal configuration, ensuring optimal performance and cost efficiency.
[claim] The right coil upender configuration can significantly enhance operational efficiency, reduce downtime, and ensure the safety of workers and materials.
1. What Factors Should You Consider When Choosing a Coil Upender?
1.1 Weight Capacity and Load Compatibility
The first and most critical factor in selecting a coil upender is its weight capacity and load compatibility. Every coil upender is designed to handle a specific weight range, and exceeding this limit can result in mechanical failures or safety hazards. For example, a coil weighing 10 tons requires a machine rated for at least that weight. Choosing a model with a higher capacity ensures durability and accounts for potential future changes in operations.
Key Considerations:
- Material Type: Steel coils are denser and heavier than aluminum or copper coils, requiring robust configurations.
- Load Dimensions: Some coils have irregular shapes or larger radii, influencing the design of the cradle or platform.
Using a machine below its rated capacity can also lead to inefficiencies, as it may not grip or rotate lighter loads effectively. Ensuring compatibility between the coil weight, size, and upender design is essential to maintaining smooth operations.
1.2 Space Constraints and Machine Footprint
Industrial floor space is often a premium commodity. The size of your coil upender must align with your facility’s layout to avoid disruptions in workflow. Compact models are ideal for facilities with limited space, while larger configurations may be necessary for operations handling oversized coils.
Featured Data Table: Space Requirements for Common Coil Upender Types
Coil Upender Type | Average Footprint (sq. ft.) | Ideal Facility Type |
---|---|---|
Compact Manual | 10–15 | Small warehouses or workshops |
Hydraulic Vertical | 20–30 | Medium-sized industrial facilities |
Horizontal Heavy-Duty | 30–50 | Large-scale manufacturing plants |
Proper planning of the machine’s placement ensures that it doesn’t obstruct other equipment or create bottlenecks in the production line.
1.3 Automation vs. Manual Operation
Automation has become a major trend across industries, and coil upenders are no exception. Automated models equipped with programmable controls and sensors offer higher precision, reduced labor requirements, and increased safety. However, they come at a higher upfront cost and may require specialized training for operators.
Manual upenders, on the other hand, are more affordable and easier to maintain but depend heavily on operator expertise. They are better suited for operations with lower volumes or those that don’t require intricate handling procedures.
Benefits of Automation:
- Consistency: Reduces errors caused by manual handling.
- Safety Enhancements: Minimizes the likelihood of accidents by eliminating direct operator interaction with heavy loads.
- Efficiency Gains: Faster cycle times improve overall productivity.
The choice between automation and manual operation ultimately depends on your budget, operational demands, and the skill level of your workforce.
1.4 Comparing Initial Costs to Long-Term Savings
While the initial cost of a coil upender is a primary consideration, it’s equally important to evaluate the long-term savings it can provide. Machines with higher upfront costs often feature advanced designs and durable components that reduce maintenance needs and downtime over time.
Cost Comparison Table:
Coil Upender Type | Average Initial Cost ($) | Maintenance Cost (Annual, $) | Expected Lifespan (Years) |
---|---|---|---|
Manual Compact | 5,000–10,000 | 500–1,000 | 10–15 |
Hydraulic Vertical | 15,000–25,000 | 1,000–2,000 | 15–20 |
Fully Automated | 30,000–50,000 | 2,000–3,000 | 20+ |
For high-volume operations, the savings from reduced downtime and increased efficiency often justify the higher initial investment in automated or hydraulic systems.
1.5 Fact vs. Fiction: Are All Coil Upenders Universal?
- Fact: Coil upenders are designed for specific applications, with variations in load capacity, dimensions, and operational mechanisms. Universal models are rare and often unsuitable for specialized tasks.
- Fiction: Any coil upender can handle all coil types. For example, a machine designed for lightweight aluminum coils will struggle with heavy steel loads, leading to potential failures.
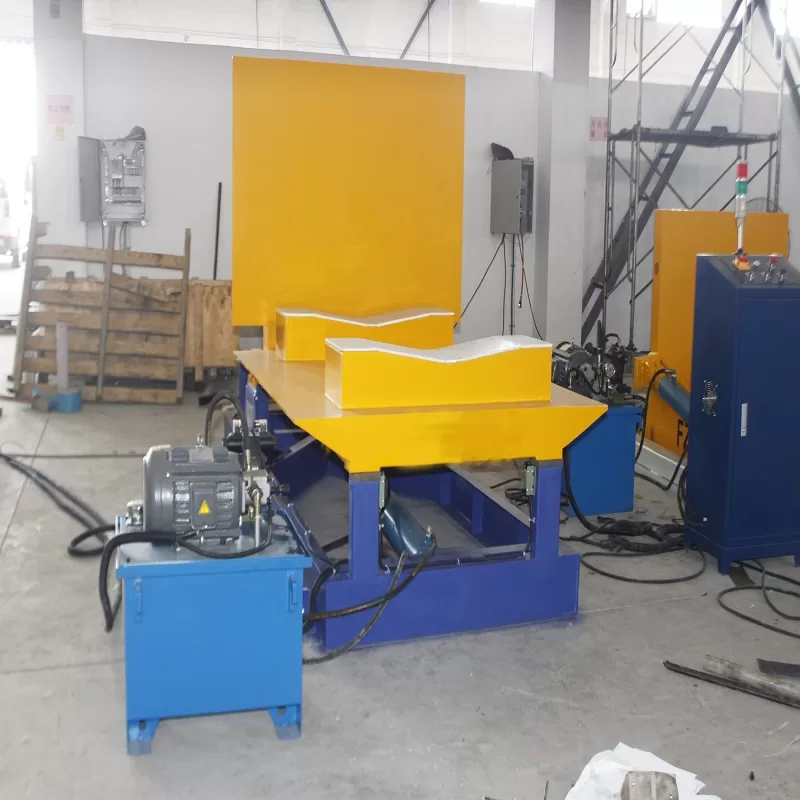
2. How Do Different Configurations Impact Efficiency?
2.1 Vertical vs. Horizontal Coil Upenders
One of the most defining characteristics of a coil upender is whether it operates vertically or horizontally. Both configurations are designed for specific workflows, and choosing between them depends on the nature of your operations.
Vertical Coil Upenders are ideal for facilities where space is limited. These machines work by rotating coils from a horizontal to a vertical position (or vice versa) in a way that minimizes the required floor space. They are commonly used in industries handling smaller or medium-sized coils and prioritize precision over speed.
Horizontal Coil Upenders, on the other hand, are designed for large-scale industrial operations. Their horizontal orientation allows them to handle heavier and larger coils, often exceeding 20 tons in weight. These machines are better suited for high-capacity workflows where speed and efficiency are paramount.
Efficiency Comparison Table:
Feature | Vertical Coil Upenders | Horizontal Coil Upenders |
---|---|---|
Space Efficiency | High (compact footprint) | Moderate (requires more space) |
Load Capacity | Up to 10 tons | Up to 50 tons or more |
Cycle Time | Moderate | Faster |
Typical Application | Medium-sized manufacturing lines | Heavy-duty industrial plants |
Selecting the right orientation ensures the best alignment with your operational needs, reducing downtime and improving overall efficiency.
2.2 Hydraulic vs. Mechanical Systems
The internal mechanics of a coil upender also play a significant role in its performance. The two most common systems used in these machines are hydraulic and mechanical.
Hydraulic Coil Upenders rely on pressurized fluids to generate the force required for lifting and rotating coils. These machines are known for their smooth and consistent performance, even when handling heavy loads. However, they require regular maintenance to prevent leaks and ensure optimal fluid pressure.
Mechanical Coil Upenders, on the other hand, use gears, motors, and chains to perform the same functions. While they may lack the smoothness of hydraulic systems, they are generally easier to maintain and have fewer components that can fail.
Featured Data Table: Hydraulic vs. Mechanical Systems
Feature | Hydraulic Systems | Mechanical Systems |
---|---|---|
Smoothness of Operation | High | Moderate |
Maintenance Requirements | Moderate (fluid checks needed) | Low |
Load Capacity | Higher (ideal for heavy loads) | Moderate |
Cost | Higher | Lower |
The choice between hydraulic and mechanical systems depends on your budget, load requirements, and willingness to invest in ongoing maintenance.
Featured Image:
(Include an image of a hydraulic coil upender lifting a heavy steel coil with precision.)
2.3 Customizable Features for Specific Industries
Many coil upender manufacturers offer customizable features to cater to the unique needs of various industries. These features can significantly enhance the machine’s efficiency and safety when used in specialized applications.
Some of the most popular customizations include:
- Variable Speed Controls: Allow operators to adjust the rotation speed based on the coil’s weight and size.
- Safety Guards: Prevent coils from shifting or falling during operation, particularly in high-speed configurations.
- IoT-Enabled Sensors: Provide real-time monitoring of load balance, hydraulic pressure, and machine performance.
For example, in the automotive industry, upenders often include advanced safety mechanisms to handle delicate materials like aluminum sheets. In contrast, the steel industry requires heavy-duty configurations capable of lifting massive coils without compromising precision.
2.4 Conclusion
The configuration of a coil upender has a direct impact on its efficiency. From vertical versus horizontal designs to hydraulic versus mechanical systems, understanding these differences ensures that you choose a machine that aligns with your operational goals. Customizable features further enhance the machine’s ability to meet specific industry requirements, improving productivity and safety.
[claim] Tailoring the configuration of your coil upender to your specific workflow is key to maximizing efficiency and minimizing downtime.
2.5 Fact vs. Fiction: Does Automation Always Improve Efficiency?
- Fact: Automation significantly improves efficiency by reducing human error and accelerating processes. For repetitive tasks, automated coil upenders outperform their manual counterparts.
- Fiction: Automation eliminates the need for operator oversight. Even automated machines require trained personnel to monitor performance and address issues promptly.
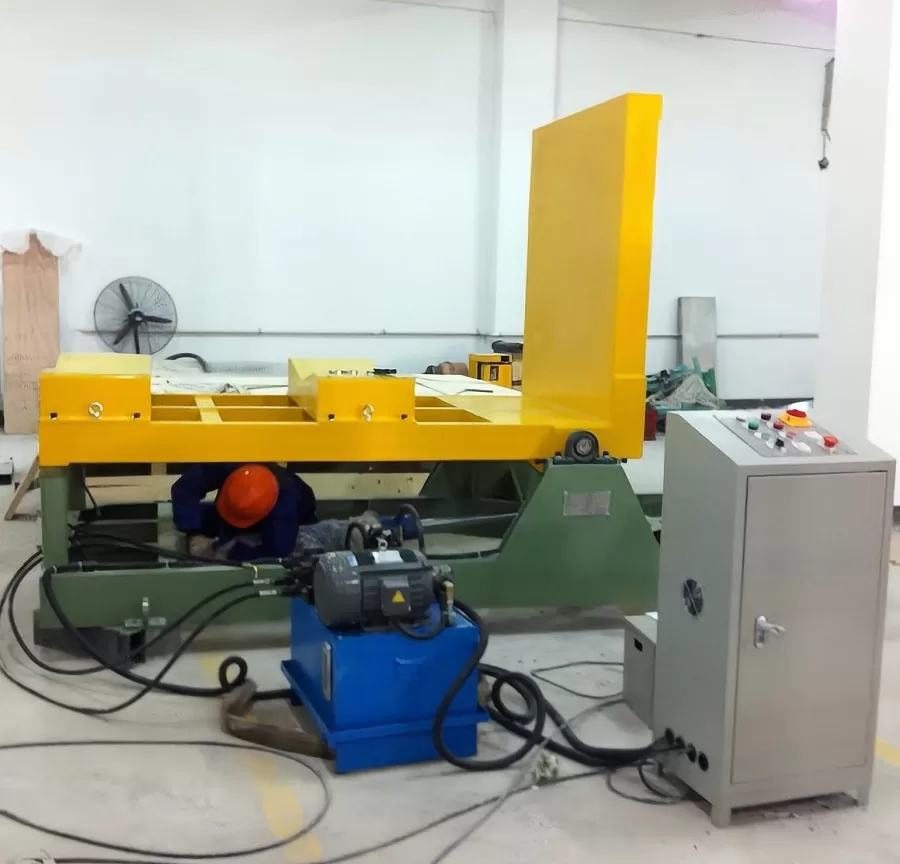
3. What Are the Maintenance Needs of Various Configurations?
3.1 Differences in Upkeep for Hydraulic vs. Manual Systems
Maintenance requirements vary greatly depending on the type of coil upender. Hydraulic systems, while efficient, require regular fluid changes, seal replacements, and pressure checks to prevent performance issues. Manual systems, conversely, have simpler mechanisms and fewer components, making them easier to maintain.
Proper lubrication is critical for both types of systems. Neglecting lubrication can lead to increased friction, overheating, and eventual component failure. For hydraulic systems, the quality of the hydraulic fluid also plays a significant role in performance.
Key Maintenance Tasks for Hydraulic Systems:
- Inspect Hydraulic Lines: Look for leaks or damage that could lead to pressure loss.
- Change Filters: Prevent contaminants from circulating in the system.
- Test Pressure: Regularly check the hydraulic pressure to ensure optimal performance.
Manual systems, on the other hand, require:
- Gear Inspections: Check for wear and tear on mechanical components.
- Adjustments: Tighten bolts and align parts to maintain smooth operation.
3.2 Common Maintenance Mistakes to Avoid
Even the most well-intentioned maintenance efforts can go wrong if not executed properly. Some common mistakes include:
- Overlooking Small Issues: Ignoring minor leaks or unusual noises can lead to larger, costlier problems.
- Using Incorrect Lubricants: Always follow the manufacturer’s recommendations for lubricants and hydraulic fluids.
- Skipping Routine Checks: Preventive maintenance is only effective if performed consistently.
Featured Image:
(Include an image of a technician performing a hydraulic fluid check on a coil upender.)
3.3 Cost Analysis of Maintenance Requirements
Understanding the cost implications of maintenance is crucial for budgeting and long-term planning. While hydraulic systems have higher maintenance costs, they often deliver better performance over time, justifying the investment.
Maintenance Cost Analysis Table:
System Type | Average Maintenance Cost (Annual, $) | Common Repairs |
---|---|---|
Hydraulic Systems | 1,000–2,500 | Fluid replacement, seal repairs, pressure tests |
Manual/Mechanical | 500–1,000 | Gear adjustments, lubrication |
Automated Systems | 2,000–3,000 | Sensor calibration, software updates |
3.4 Advanced Tools for Preventive Maintenance
Modern tools like thermal imaging cameras and vibration analysis systems are transforming how maintenance is performed. These tools can detect potential issues, like overheating or misalignment, before they lead to major failures.
Investing in these advanced diagnostic tools ensures a more proactive approach to maintenance, reducing downtime and improving the machine’s lifespan.
Two Fact Statement with Explanation: One True, One False
- True: Hydraulic coil upenders require regular fluid changes to maintain performance.
Explanation: Hydraulic fluid degrades over time, and contaminants can affect the system’s efficiency. - False: Manual coil upenders do not require lubrication.
Explanation: Even manual systems rely on moving parts that need regular lubrication to prevent friction and wear.
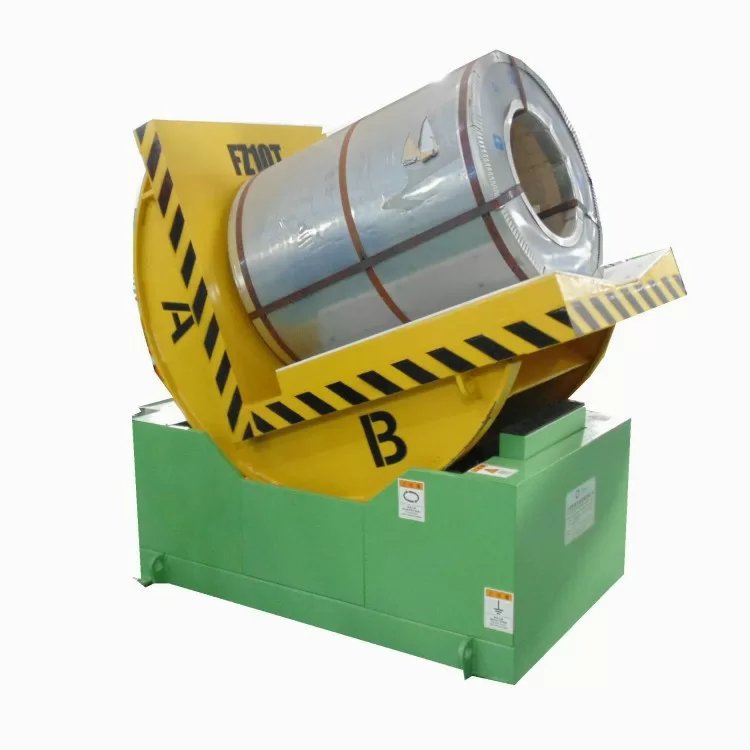
4. How to Future-Proof Your Investment in Coil Upenders?
4.1 Assessing Scalability and Adaptability
Future-proofing your investment in a coil upender starts with assessing its scalability and adaptability. Industrial demands often change over time, and choosing a machine that can grow with your operations is critical. Consider whether the upender can handle larger or heavier coils if production requirements increase. Additionally, evaluate its compatibility with new technologies, such as IoT integrations or automation upgrades.
For instance, a facility that primarily handles 5-ton coils today might transition to heavier 10-ton coils in the future. Investing in an upender with a higher load capacity or modular components ensures you won’t need to replace the machine prematurely.
Key Features to Look for in a Future-Ready Upender:
- Modular Design: Allows for easy upgrades or modifications.
- Load Capacity Flexibility: Supports a wider range of coil weights and sizes.
- Technology Integration: Compatible with IoT sensors and automation systems.
By choosing a scalable solution, you can minimize the risk of obsolescence and reduce future capital expenditures.
4.2 The Role of IoT-Enabled Coil Upenders
The industrial Internet of Things (IoT) is transforming how machinery operates and is maintained. IoT-enabled coil upenders come equipped with sensors that monitor performance metrics in real-time, such as hydraulic pressure, vibration levels, and temperature. These systems can send alerts to operators when irregularities are detected, allowing for preventive action before issues escalate.
For example, an IoT-enabled upender can flag a 10% drop in hydraulic pressure, prompting a technician to inspect the system before a complete failure occurs. This predictive approach not only minimizes downtime but also extends the lifespan of the machine.
Benefits of IoT-Enabled Coil Upenders:
- Real-Time Monitoring: Operators can detect and resolve issues immediately.
- Data-Driven Insights: Historical performance data helps optimize operations.
- Remote Accessibility: Managers can oversee multiple machines from a centralized dashboard.
Featured Image:
(Include an image of an IoT dashboard displaying real-time performance metrics of a coil upender.)
4.3 Comparing Long-Term ROI of Different Configurations
The return on investment (ROI) of a coil upender depends on its initial cost, efficiency, maintenance requirements, and lifespan. While advanced configurations like IoT-enabled or automated upenders may have a higher upfront cost, they often deliver superior long-term value through reduced downtime, lower maintenance costs, and enhanced productivity.
ROI Analysis Table:
Configuration Type | Initial Cost ($) | Annual Savings ($) | ROI (5 Years) |
---|---|---|---|
Manual Coil Upender | 5,000–10,000 | 1,000 | Moderate |
Hydraulic Coil Upender | 15,000–25,000 | 2,500 | High |
IoT-Enabled Upender | 30,000–50,000 | 5,000 | Very High |
For companies prioritizing long-term efficiency and scalability, investing in advanced configurations provides the highest ROI and positions them for future growth.
4.4 Conclusion
Future-proofing your investment in coil upenders requires a forward-thinking approach. By selecting scalable, IoT-enabled machines and focusing on long-term ROI, businesses can ensure their equipment remains relevant and efficient for years to come. This not only reduces costs but also positions companies to adapt to evolving industry demands.
[claim] Investing in scalable and technology-driven coil upenders ensures operational flexibility, reduced downtime, and long-term cost savings.
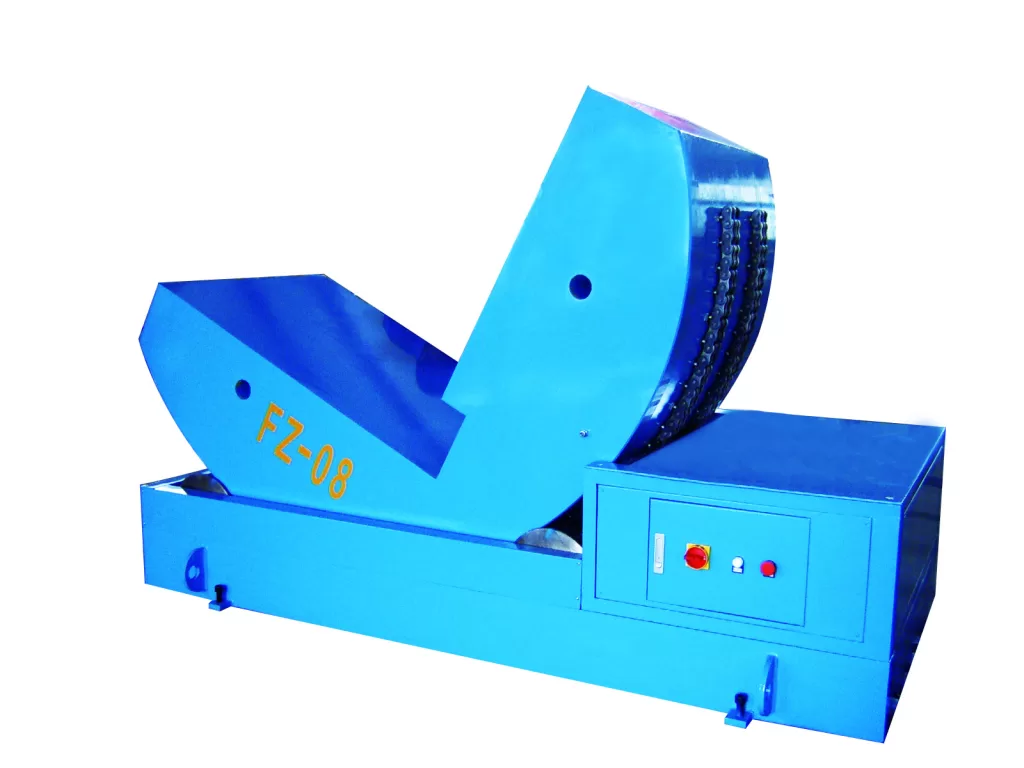
Two Fact Statement with Explanation: One True, One False
- True: IoT-enabled coil upenders can alert operators to potential issues in real-time, reducing downtime.
Explanation: Sensors continuously monitor the machine and send alerts when irregular performance metrics are detected. - False: A coil upender with a higher load capacity will always consume more energy.
Explanation: Energy consumption depends on the system design and operational efficiency, not just load capacity.
Conclusion
Choosing the right coil upender configuration is a critical decision that impacts operational efficiency, safety, and cost management. By understanding the factors that influence performance—such as weight capacity, space requirements, and automation—you can select a machine that aligns with your current and future needs. Additionally, investing in IoT-enabled systems and scalable configurations ensures your upender remains an asset as your business evolves.