Integrating Orbital Wrapping Machines into Existing Production Lines: A Practical Guide
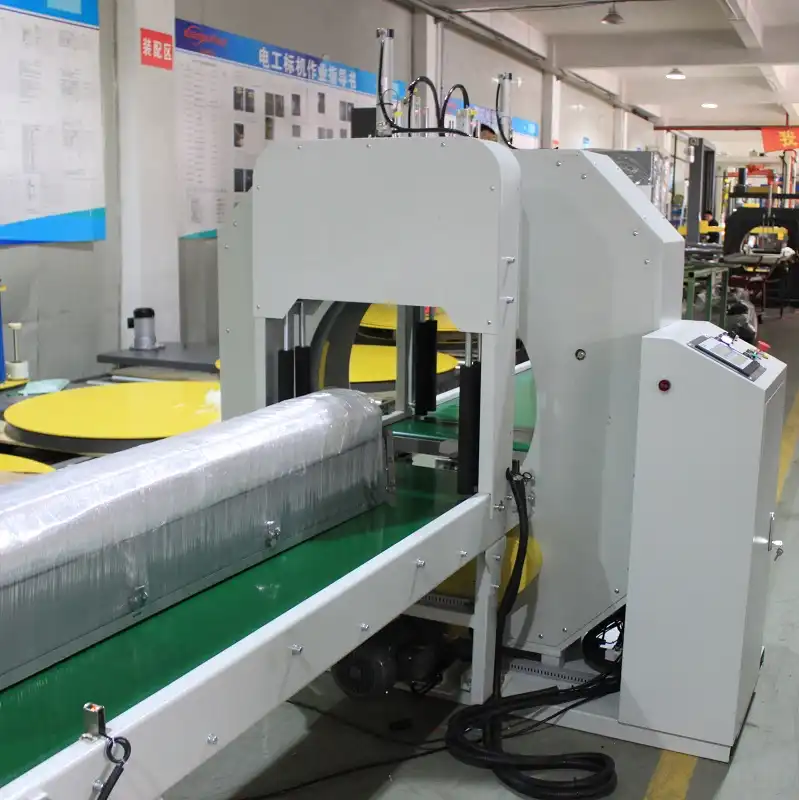
In modern manufacturing and logistics, optimizing production flow through automation is paramount for maintaining competitiveness. Integrating specialized equipment, such as an orbital wrapping machine, into an established production line presents significant opportunities for efficiency gains but also requires meticulous planning. Can such a machine be seamlessly incorporated into your existing workflow? The answer is often yes, but success hinges on careful evaluation and strategic implementation.
This guide outlines the critical factors, challenges, and solutions involved in orbital wrapping machine integration. We will explore how to assess compatibility, manage automation controls, leverage customization, and ultimately ensure the new equipment enhances, rather than disrupts, your manufacturing workflow optimization.

1. The Strategic Value of Seamless Machine Integration
Before delving into technical specifics, understanding the strategic importance of production line integration is crucial. A standalone machine that doesn't mesh with the overall system can create bottlenecks, increase downtime, and hinder productivity. Successful integration ensures new machinery acts as a catalyst for improvement.
1.1. Enhancing Overall Production Efficiency
The primary goal of integrating new machinery should be to boost overall efficiency. Proper integration allows the orbital wrapper to complement existing processes, facilitating a smoother, faster production flow. Key benefits include:
- Reduced Manual Handling: Automating the wrapping process minimizes labor-intensive tasks.
- Increased Throughput: Machines operate continuously and often faster than manual methods.
- Consistent Quality: Automated wrapping ensures uniform tension and coverage, improving load stability and protection.
For example, integrating an orbital wrapper into a packaging line can significantly cut down cycle times, eliminate inconsistencies associated with manual wrapping, and allow personnel to be redeployed to higher-value activities.
1.2. Maintaining Workflow Consistency
Production lines function as interconnected systems. Introducing new equipment must preserve the operational rhythm. A poorly integrated machine can disrupt upstream or downstream processes, leading to delays and inefficiencies. Key considerations include:
- Synchronization: Ensuring the wrapper operates at a pace compatible with conveyors and other equipment.
- Buffering: Assessing if buffer zones are needed before or after the machine to handle minor speed variations.
- Reliability: Choosing robust equipment with high uptime to avoid becoming a point of failure.
Maintaining a consistent workflow is vital for predictable output and meeting production targets.
1.3. Optimizing Labor Allocation and Safety
Automated machinery integration often leads to significant labor cost optimization. Repetitive, physically demanding tasks like manual wrapping can be automated, freeing up employees for roles requiring problem-solving, quality control, or complex machine oversight. Furthermore, automation can enhance workplace safety by reducing ergonomic risks associated with manual wrapping.
2. Assessing Machine Compatibility with Your Production Line
Thoroughly evaluating the packaging equipment compatibility is the foundational step for successful integration. This involves assessing physical fit, operational synergy, and utility requirements.
2.1. Physical Dimensions and Layout Integration
The machine's footprint and configuration must align with your facility's constraints. Consider these parameters:
- Space Availability: Measure the allocated area, including necessary clearances for operation, maintenance access, and safety zones.
- Machine Orientation: Determine the optimal infeed and outfeed directions relative to the existing product flow (e.g., left-to-right, right-to-left).
- Height Constraints: Check for overhead obstructions like pipes, ducts, or low ceilings.
- Impact on Workflow: Ensure the machine doesn't impede personnel movement, forklift traffic, or access to other critical equipment.
Manufacturers often offer compact models or modular designs that provide flexibility for facilities with limited space. A detailed layout analysis, sometimes using CAD models, is recommended.
2.2. Integration with Existing Material Handling Systems
The orbital wrapper must seamlessly interface with your current material handling equipment, primarily conveyor systems. Key compatibility points include:
- Conveyor Height and Width: Ensure the machine's conveyor matches the height and accommodates the width of your existing line conveyors for smooth product transfer.
- Conveyor Speed Synchronization: The wrapper's internal conveyors must match the line speed, often requiring variable speed control.
- Product Transfer Mechanisms: Verify how products transition onto and off the wrapper's conveyor (e.g., driven rollers, belt conveyors, chain transfers).
- Load Characteristics: Confirm the machine can handle your product dimensions (length, width, height), weight, and stability.
Discussing these parameters in detail with the equipment supplier is essential to ensure smooth, uninterrupted product flow.
2.3. Utility Requirements
Ensure your facility can meet the machine's power, compressed air, and potentially other utility needs at the installation point. Mismatched requirements can lead to costly infrastructure upgrades.

Get Your Best Solution !

3. Automation and Control System Integration Challenges
Modern production lines rely on sophisticated control systems. Ensuring the new orbital wrapper communicates effectively with your existing infrastructure, often managed by Programmable Logic Controllers (PLCs), is critical for automation in packaging.
3.1. PLC Communication and Protocol Compatibility
The wrapper's PLC must "talk" to the main line control system. Key considerations for PLC integration packaging include:
- Control Architecture: Does your line use a centralized PLC, or distributed control? The wrapper needs to fit this architecture.
- Communication Protocols: Identify the primary industrial network protocol used (e.g., EtherNet/IP, PROFINET, Modbus TCP/IP). The wrapper must support the same protocol or use a compatible gateway. ([External Link Example: PMMI - The Association for Packaging and Processing Technologies](https://www.pmmi.org/))
- Data Exchange: Define the necessary data points to be exchanged (e.g., machine status, start/stop commands, fault codes, cycle counts).
- Handshaking Signals: Establish clear physical or logical signals for product entry/exit confirmation (e.g., photo-eye signals confirming product presence or clearance).
Incompatibility here can lead to significant integration challenges, requiring custom programming or hardware interfaces. Early discussion with suppliers about your specific control environment is vital.
3.2. Centralized Monitoring and Control
Ideally, the orbital wrapper should integrate into your plant's SCADA (Supervisory Control and Data Acquisition) or HMI (Human-Machine Interface) systems. This allows:
- Unified Operation: Operators manage the line from a central point.
- Real-time Monitoring: Visibility of the wrapper's status, performance, and alarms alongside other line equipment.
- Remote Diagnostics: Potential for remote troubleshooting and support, minimizing downtime.
Integration with IoT (Internet of Things) platforms can further enhance data collection for predictive maintenance and performance analytics.
3.3. Safety System Integration
The wrapper's safety system (emergency stops, light curtains, safety interlocks) must integrate seamlessly with the overall line safety architecture. This ensures that an emergency stop triggered anywhere on the line safely halts relevant upstream and downstream equipment, including the wrapper, according to established safety standards (e.g., ISO 13849). (External Link Example: ISO - International Organization for Standardization)
4. Leveraging Customization for Optimal Fit
Standard, off-the-shelf machines may not perfectly align with unique production requirements. Stretch wrapper customization options allow tailoring the equipment for seamless integration and optimized performance.
4.1. Physical and Layout Modifications
Manufacturers can often modify machine dimensions or configurations:
- Adjustable Height/Width: Modifying conveyor heights or machine frame dimensions.
- Custom Infeed/Outfeed Conveyors: Designing non-standard conveyor lengths or types (e.g., right-angle transfers).
- Relocated Controls: Positioning the operator panel for optimal accessibility within the line layout.
4.2. Adjusting Operational Parameters and Features
Tailoring machine functions ensures compatibility with product variations and line speed:
- Wrapping Programs: Storing multiple recipes for different products with varying wrap patterns, tension settings, and rotation speeds.
- Variable Speed Control: Precisely matching the wrapper's throughput to the line's operational speed.
- Specialized Clamping/Cutting Units: Adapting film clamping and cutting mechanisms for specific film types or product shapes.
- Film Delivery System: Options for different pre-stretch levels or film widths.
4.3. Incorporating Ancillary Equipment
Integration may involve adding features or connecting to other devices:
- Top Sheet Dispensers: Adding dust or moisture protection.
- Automatic Film Splicing: Enabling continuous operation during film roll changes.
- Label Applicators: Integrating labeling post-wrapping.
- Safety Enhancements: Custom guarding or enhanced sensor packages based on risk assessment.
Collaborating closely with the machine manufacturer during the specification phase is key to identifying and implementing necessary customizations.


Conclusion: Strategic Integration for Future Growth
Integrating an orbital wrapping machine into an existing production line is a feasible and often highly beneficial project, provided it's approached strategically. Success requires a thorough assessment of compatibility (physical, operational, utility), careful planning for automation and control system integration (PLC communication, safety), and leveraging customization options to ensure a perfect fit.
By prioritizing seamless integration, businesses can unlock significant improvements in efficiency, throughput, consistency, and labor optimization. Careful evaluation, clear communication with suppliers, and attention to technical details will ensure the new equipment becomes a valuable asset, enhancing production capabilities and supporting long-term operational goals rather than creating bottlenecks.

Get Your Best Solution !