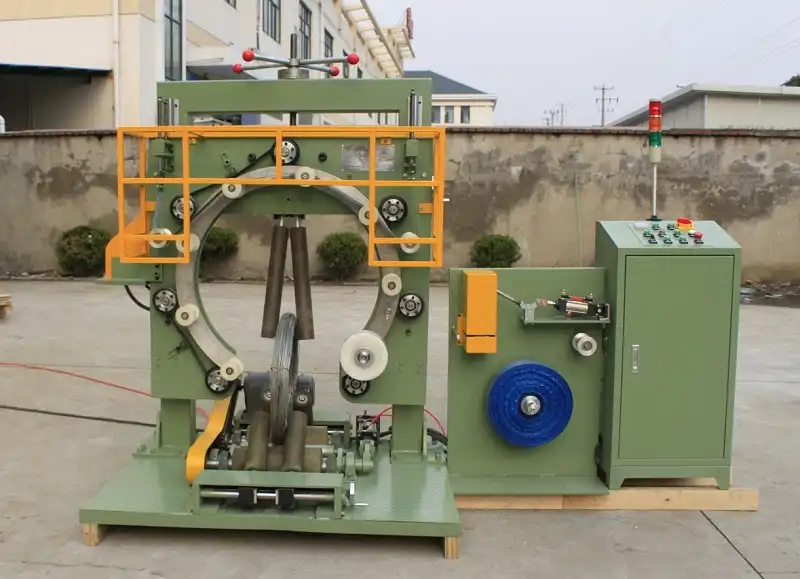
In modern manufacturing, where efficiency is king and precision is vital, the role of coil wrapping machines has become increasingly significant. These machines simplify the process of packaging industrial coils like steel, aluminum, and copper, ensuring durability during transport and storage. But as industries evolve, one question looms large: can these machines be tailored to meet specific production requirements?
When exploring the potential for customization, the possibilities seem endless. From adapting dimensions to match varying coil sizes to integrating advanced software for better control, manufacturers are often faced with a multitude of options. Customization not only enhances functionality but also aligns the machine's capabilities with unique production demands, saving time, reducing costs, and improving efficiency.
As someone deeply invested in understanding industrial innovations, I delved into this topic. Here’s what I found.
1. How Does Customization Impact Efficiency?
1.1 Tailoring Machine Dimensions
Efficiency starts with compatibility. One of the most common customizations is resizing a coil wrapping machine to fit specific coil dimensions. Manufacturers dealing with unusually large or small coils often find standard machines inadequate.
When I visited a factory specializing in steel coils, the production manager explained how resizing their wrapping machine eliminated manual adjustments. Their machine now automatically aligns with the exact width and diameter of each coil, cutting setup time by 30%. This change alone saved them significant labor hours and increased their output.
But it's not just about size. Adjusting the machine's tensioning mechanisms or roller configurations ensures that delicate materials like aluminum coils are handled gently while maintaining a snug wrap.
1.2 Integrating Advanced Control Systems
Technology plays a key role in making coil wrapping machines more efficient. Modern systems allow for software-driven adjustments, remote monitoring, and even integration with existing production lines.
For instance, programmable logic controllers (PLCs) are widely used in customized machines. These controllers allow operators to define precise wrapping parameters, including wrap speed, material overlap, and tension. Once programmed, the system can apply these settings across different product lines with minimal human intervention.
Imagine being able to track every coil wrapped by your machine in real-time. With IoT-enabled systems, this is not just a dream—it’s a reality many manufacturers have already embraced. By incorporating such features, companies reduce errors, improve consistency, and gain valuable data insights.
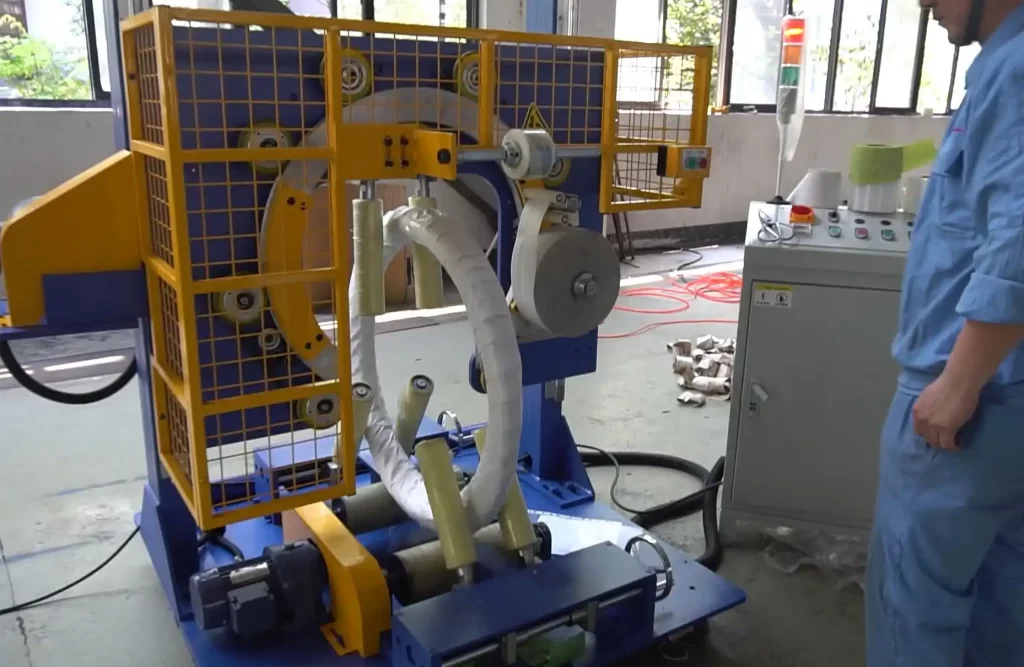
1.3 Balancing Cost vs. Benefits
Customization often comes with a hefty price tag, making it crucial to evaluate whether the investment will deliver long-term advantages. Manufacturers need to weigh upfront costs against potential savings in operational efficiency, labor reduction, and enhanced product quality.
Consider a mid-sized factory that processes both steel and aluminum coils. By customizing their coil wrapping machine to handle both materials seamlessly, they avoided the expense of purchasing a second machine. Over a year, the company saved thousands in operational costs, proving the financial wisdom of targeted customization.
However, over-customizing can lead to diminishing returns. A machine loaded with unnecessary features can become complex to operate and maintain. Striking the right balance is essential to ensure that every dollar invested directly benefits production efficiency.
2. What Factors Should Be Considered Before Customizing?
2.1 Assessing Production Requirements
The first step in customization is a thorough analysis of your production needs. Start by identifying key parameters such as coil sizes, packaging materials, and production volumes. A machine tailored to these factors can address inefficiencies and minimize downtime.
For instance, if your production line handles fragile aluminum coils, you’ll need a machine with soft tensioning capabilities and protective wrapping layers. Alternatively, high-volume steel coil operations may require a robust system capable of rapid, continuous wrapping.
Consulting with in-house teams, including engineers and operators, provides practical insights into what’s missing in the current setup. Gathering feedback ensures the customizations align with real-world requirements rather than theoretical possibilities.
2.2 Collaborating with Manufacturers
Partnering with the right machine manufacturer is critical when exploring customization. Established manufacturers often have experience tailoring machines to meet diverse industry needs. Their expertise can guide you through selecting relevant features and avoiding unnecessary modifications.
During this stage, transparency is key. Sharing detailed production data, including challenges and expectations, helps the manufacturer design a machine that precisely fits your workflow. Additionally, many companies offer prototypes or digital simulations to visualize how the customized machine will function.
Building a strong relationship with the manufacturer also facilitates future upgrades or troubleshooting. A collaborative approach ensures that your machine remains adaptable as production demands evolve.
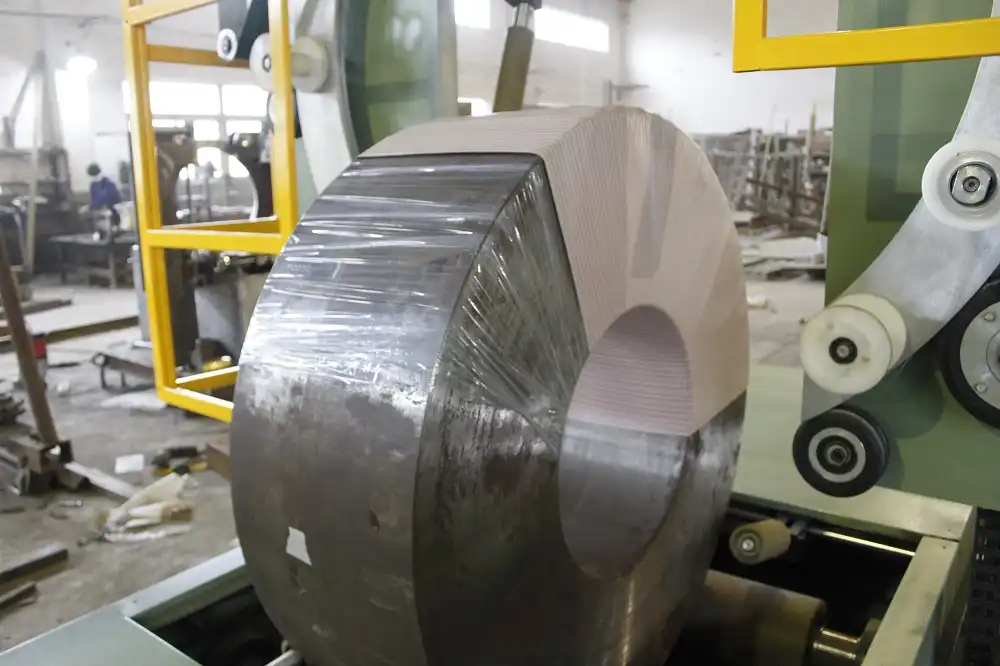
2.3 Testing and Quality Assurance
Once the customization process is complete, rigorous testing is necessary to confirm that the machine performs as intended. Testing should cover all operational scenarios, from handling varying coil sizes to maintaining consistent wrap quality at different speeds.
Quality assurance is equally important. Machines must meet safety and compliance standards, especially if they handle hazardous materials or operate in high-pressure environments. For example, automated wrapping machines in chemical plants often require specialized seals and coatings to prevent contamination.
Regularly scheduled maintenance and operator training ensure the machine continues to deliver optimal performance. Investing in quality control upfront minimizes the risk of breakdowns or costly repairs later.
3. Are There Limitations to Customizing Coil Wrapping Machines?
3.1 Identifying Technological Boundaries
While customization offers tremendous benefits, it’s essential to recognize its limits. Some features may not be feasible due to technological constraints or operational risks. For example, a machine that wraps coils at ultra-high speeds might compromise safety or product quality.
Technological advancements are closing these gaps, but not every innovation is suitable for all production environments. Before committing to complex upgrades, ensure that your existing infrastructure can support the changes.
3.2 Overcoming Practical Challenges
Customizing a machine isn’t always a straightforward process. Logistical hurdles, such as lengthy manufacturing timelines or supply chain delays, can complicate implementation. Furthermore, highly specialized machines may require unique spare parts, making repairs time-consuming and expensive.
Effective project management is key to overcoming these challenges. Setting realistic timelines, budgets, and contingency plans ensures a smoother transition to customized operations.
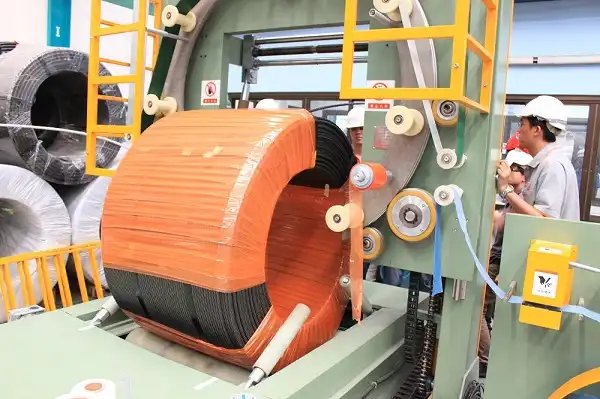
3.3 Balancing Innovation with Feasibility
Innovation is exciting, but practicality should always take precedence. Focus on features that directly address your production bottlenecks rather than adopting unnecessary technologies. For example, a machine equipped with advanced AI may be impressive, but it won’t add value if simpler software solutions can achieve the same results.
Customization is most effective when it balances cutting-edge technology with everyday usability. By aligning the machine’s features with your team’s capabilities, you create a system that enhances productivity without overcomplicating operations.
4. How to Choose the Right Customizations for Your Needs?
4.1 Analyzing Operational Goals
Before diving into customization, take a hard look at your operational goals. Are you aiming to increase productivity? Improve wrapping precision? Reduce material costs? Clear objectives will guide you toward the most beneficial upgrades.
Consider a facility producing steel and copper coils. Their primary goal was to streamline operations for faster output. Customizing the machine’s motorized rollers and wrapping speed controls helped them double their production capacity. For another factory dealing with fragile materials, adding advanced tension control mechanisms reduced damage rates.
When goals are well-defined, customization becomes a targeted investment rather than an unnecessary expense.
4.2 Exploring Available Technologies
The market is brimming with technological solutions designed to elevate coil wrapping machines. From AI-driven automation to advanced material sensors, manufacturers can pick and choose innovations that align with their requirements.
For example, integrating RFID tags during the wrapping process allows for seamless inventory management. IoT-enabled devices can monitor machine performance and send alerts for maintenance, reducing unexpected downtime. Additionally, adopting eco-friendly wrapping materials and recycling systems helps manufacturers meet sustainability goals while staying competitive.
Exploring these technologies with an eye on your specific needs ensures that you stay ahead without adopting every trend.
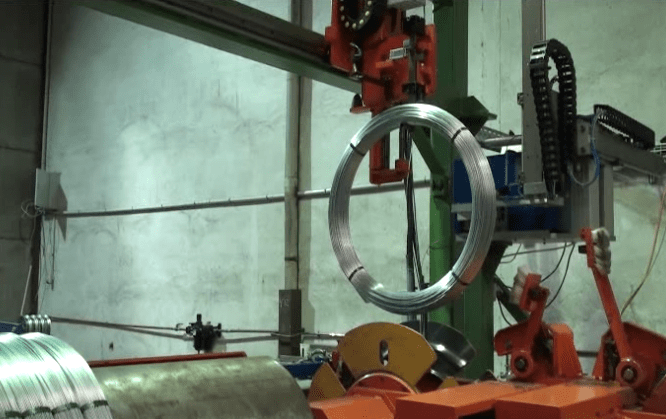
4.3 Setting a Realistic Budget
Customization is only as effective as the budget that supports it. While it’s tempting to go all-in on upgrades, prioritizing based on ROI ensures the best results.
A small-scale manufacturer might focus on cost-effective solutions like resizing machine components or upgrading software for better automation. Larger companies with robust budgets may invest in more complex features like integrated AI systems or modular designs for multi-coil operations.
Always account for long-term savings when budgeting. A higher upfront cost for energy-efficient motors or reduced material waste might yield substantial savings over time. Transparency with suppliers about financial limits also helps in crafting tailored solutions that fit your budget without compromising performance.
Conclusion
Coil wrapping machines play a pivotal role in industrial packaging, and customization takes their utility to the next level. From enhancing efficiency and productivity to addressing specific production challenges, tailored solutions provide immense value. However, the key to successful customization lies in balancing innovation, practicality, and budget considerations. By focusing on clear operational goals and collaborating closely with manufacturers, businesses can unlock the full potential of their coil wrapping systems.
Claim
Customization is not a one-size-fits-all approach. It requires careful planning, informed decision-making, and collaboration to create machines that truly meet unique production needs.

Get Your Best Solution !