Optimizing Protection: Understanding Bubble Film Stretch Wrapping Machines
Protecting long, profiled, or delicate products during handling and shipping presents a unique challenge for manufacturers and fabricators. Combining the cushioning properties of bubble film with the secure containment of stretch wrap offers an effective solution. Automated systems, specifically bubble film stretch wrapping machines, streamline this process, ensuring consistent protection and operational efficiency.
This specialized equipment, often a type of automatic horizontal stretch wrapping machine, integrates bubble film application directly into the orbital stretch wrapping cycle. It's designed for online packaging of profiles, pipes, extrusions, lumber, and other elongated items.
How Bubble Film Stretch Wrappers Work
These machines typically consist of several key stages integrated into a single automated line:
- Infeed Conveyor: Transports the product into the wrapping zone. Conveyor types (belt, roller) and lengths can often be specified based on product characteristics and line integration needs.
- Bubble Film Dispenser: Applies a layer of bubble film around the product before or concurrently with the stretch wrapping process. This provides crucial cushioning against impacts.
- Orbital Wrapping Ring: The core of the machine. A ring holding a spool of stretch film rotates around the product as it passes through the center aperture. The film is dispensed, wrapping the product securely.
- Outfeed Conveyor: Moves the fully wrapped product out of the machine, often onward to staging, palletizing, or shipping areas.
The video below demonstrates a typical orbital stretch wrapper applying film:
Key Operational Advantages
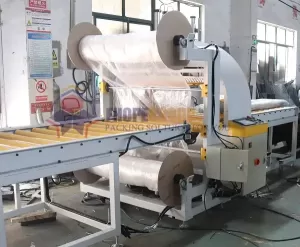
Integrating a bubble film stretch wrapping machine into a production or packaging line offers significant benefits:
- Enhanced Product Protection: The combination is highly effective. Bubble film cushions against bumps and scratches, while the stretch wrap provides tight load containment, unitization, and protection from dust and moisture.
- Improved Packaging Consistency: Automation eliminates the variability inherent in manual wrapping. Each product receives the same level of protection with consistent film tension and overlap, reducing the risk of damage due to inadequate packaging.
- Increased Throughput: These machines operate significantly faster than manual wrapping methods, allowing for higher packaging volumes and keeping pace with production output.
- Optimized Material Usage: Automated systems apply film more consistently and efficiently, potentially reducing overall material consumption compared to manual application. Precise tension control ensures optimal film stretch.
- Reduced Labor Requirements: Automating the wrapping process frees up personnel previously assigned to manual wrapping tasks, allowing them to be reallocated to more value-added activities. It can also reduce ergonomic strain associated with manual wrapping.
Customization and Key Features
To meet diverse application needs, bubble film stretch wrapping machines often offer configurable options:
- Conveyor Systems: Lengths, widths, and types (roller, belt) can be tailored to product dimensions and integration requirements.
- Wrapping Tension Control: Adjustable tension ensures the right containment force without damaging the product – crucial for delicate items.
- Variable Wrapping Speed: Allows adjustment based on product flow and desired throughput.
- Ring Speed Control: The rotational speed of the wrapping ring can often be adjusted.
- PLC Controls: Programmable Logic Controllers (PLCs) with Human-Machine Interfaces (HMIs) allow for easy setup, operation, parameter adjustments (like wrap counts, tension, speeds), and diagnostics.
- Film Carriage Systems: Pre-stretch capabilities maximize film efficiency. Different carriage types accommodate various film roll sizes and types.
- Safety Features: Light curtains, safety fencing, and emergency stops are essential for operator protection.
Here's another example illustrating the horizontal wrapping process:
Conclusion
For manufacturers dealing with profiles, extrusions, pipes, or similar elongated products requiring robust protection, a bubble film stretch wrapping machine offers a compelling solution. By automating the application of both cushioning and containment layers, these systems enhance product protection, ensure packaging consistency, increase operational efficiency, and can lead to optimized material and labor utilization. Evaluating factors like product dimensions, required throughput, and integration needs will help in selecting the most appropriate configuration for a specific industrial packaging environment.