Breaking Down the Components of a Modern Steel Coil Packing Line
- Breaking Down the Components of a Modern Steel Coil Packing Line
- 1. Introduction to Steel Coil Packing Lines
- 2. Industry Standards in Steel Coil Packing
- 3. Main Components of a Steel Coil Packing Line
- 4. Practical Applications of Modern Packing Lines
- 5. Materials Used in Steel Coil Packing
- 6. Ensuring Coil Integrity with Advanced Monitoring Systems
- 7. Safety Considerations in Modern Packing Lines
- 8. Automation and Data Integration: Enhancing Productivity
- 9. Environmental Sustainability in Steel Coil Packing
- 10. The Role of Robotics in Modern Steel Coil Packing
- 11. Real-World Case Studies of Automated Steel Coil Packing Lines
- 12. Future Trends in Steel Coil Packing Lines
- Conclusion
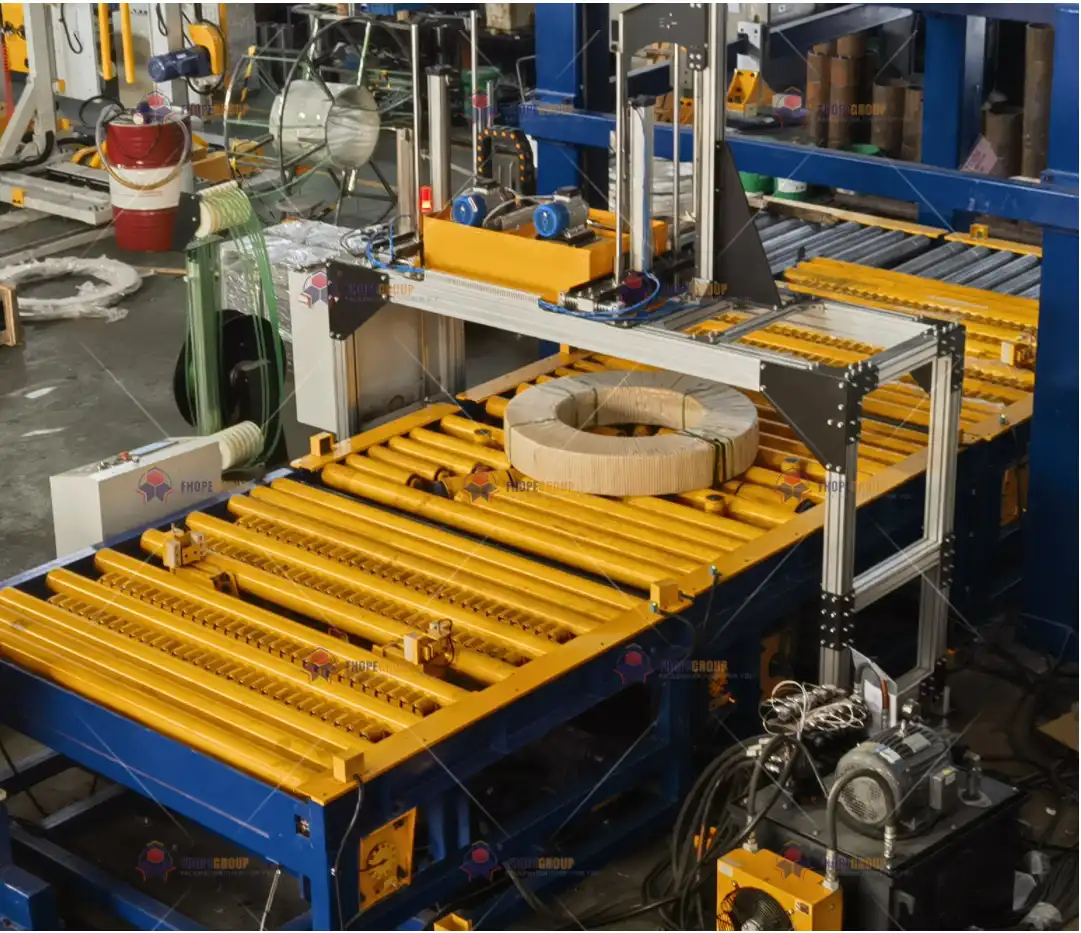
The steel manufacturing industry has seen significant advancements in recent decades, particularly in how steel coils are packed for storage and shipment. With global demand for steel continuing to rise, manufacturers must optimize every aspect of production, including the steel coil packing process, to ensure efficiency, safety, and cost-effectiveness. A modern steel coil packing line is a sophisticated, multi-component system that automates the traditionally labor-intensive process of preparing steel coils for transport. This article explores the key components of a modern steel coil packing line, detailing the technologies, industry standards, and best practices that drive operational excellence.
1. Introduction to Steel Coil Packing Lines
Steel coil packing lines are critical in the production cycle, ensuring that steel coils are securely packed and ready for transportation. Properly packed coils are less likely to sustain damage during handling or shipping, reducing the risk of product returns or claims. The packing line is responsible for ensuring that the coils are wrapped, strapped, and stacked to meet both industry standards and customer requirements.
Modern steel coil packing lines are highly automated, integrating various mechanical, electrical, and data-driven systems to deliver high throughput and consistent quality. These lines are designed to handle coils of different sizes, weights, and materials, such as cold-rolled, hot-rolled, or galvanized steel, ensuring that each product is packed securely according to its specifications.
2. Industry Standards in Steel Coil Packing
To ensure product safety and uniformity, modern steel coil packing lines must adhere to strict industry standards. These standards govern everything from material handling to packaging methods. Key standards include:
- ISO 9001: Specifies requirements for a quality management system that helps ensure consistent product quality. Packing lines designed to ISO 9001 standards prioritize uniformity in wrapping and strapping processes.
- ASTM D3951: Covers standard practices for commercial packaging, ensuring that the packed steel coils meet global transportation and handling requirements.
- ISO 780: Defines the pictorial marking for the handling of goods, ensuring that labels and packaging clearly communicate necessary handling precautions.
Compliance with these standards not only ensures product safety but also reduces costs associated with damaged goods during transportation. Automated steel coil packing lines often incorporate barcode systems and data tracking, which help manufacturers comply with standards like ISO 9001 by providing a traceable record of each packed coil.
3. Main Components of a Steel Coil Packing Line
A modern steel coil packing line typically consists of several key components, each designed to automate a specific part of the packing process. These components work in unison to provide efficient, consistent, and high-speed packaging.
3.1 Turnstile
The turnstile is the first component in most automated steel coil packing lines. This device holds multiple coils and rotates them into position for packing, reducing the need for cranes or manual labor. The turnstile allows for continuous operation, where coils are fed into the system without interruption. This not only speeds up the process but also ensures consistent throughput.
Real-world Example: A steel manufacturer in Germany reported a 30% reduction in handling time after implementing a turnstile with a 4-coil capacity, allowing for uninterrupted loading of coils into the packing system.
3.2 Coil Down-Ender
The coil down-ender is responsible for rotating the steel coils into the correct orientation for wrapping or strapping. In many cases, the coils need to be turned from an eye-horizontal position to an eye-vertical position (or vice versa), depending on how they will be stored or transported.
Technical Insight: Many down-enders are equipped with hydraulic lifting mechanisms that ensure smooth and precise movement of coils weighing up to 30 tons. These systems are typically designed with PU-coated rollers to prevent damage to the coil surface during handling.
3.3 Wrapping Machine
A crucial part of the modern packing line, the wrapping machine ensures that the steel coil is protected from environmental factors such as moisture, dust, and corrosion. Wrapping materials often include stretch film, HDPE sheets, or woven fabric, each chosen based on the customer’s requirements and the coil’s storage or shipping conditions.
Many automated wrapping machines feature programmable logic controllers (PLCs), which allow for the precise control of wrapping tension, overlap rate, and speed. This level of control ensures that coils are wrapped uniformly and securely, minimizing the risk of damage during transit.
3.4 Strapping Station
Once wrapped, the steel coil moves to the strapping station, where it is secured using high-tension steel or plastic straps. Strapping is critical for ensuring the stability of the coil during transportation. Automated strapping systems are equipped with sensors that detect the coil's size and apply the correct number of straps with uniform tension.
Technical Note: Automated strapping machines often use pneumatic or hydraulic tensioning systems, allowing them to apply up to 20,000 N of force to ensure the steel coils are tightly bound. These systems must comply with ASTM D3953 standards, which outline the specifications for steel strapping used in industrial packaging.
4. Practical Applications of Modern Packing Lines
The versatility of modern steel coil packing lines makes them suitable for a variety of industries, from automotive to construction. Each industry has specific requirements in terms of how coils are packed, transported, and stored.
Case Study: Automotive Industry
An automotive steel supplier in the U.S. implemented an automated packing line to handle high-strength steel coils used in car manufacturing. Prior to automation, the company experienced frequent damage to the coil edges due to improper manual strapping. By automating the process, the company reduced coil damage by 40% and increased packing throughput by 25%, enabling them to meet tighter production schedules.
Case Study: Construction Industry
In the construction sector, where galvanized steel is commonly used, manufacturers must ensure that coils are packed to withstand harsh outdoor conditions. A Chinese manufacturer incorporated automatic HDPE wrapping into their packing line to protect coils from moisture during long-term storage. This change led to a significant reduction in rust-related defects, enhancing the overall durability of their products.
5. Materials Used in Steel Coil Packing
The materials used in modern steel coil packing lines are selected for their strength, durability, and ability to protect the product during transportation and storage. Key materials include:
- Stretch Film: Often made from polyethylene, stretch film is used to tightly wrap the coil and prevent moisture ingress.
- HDPE Sheets: High-density polyethylene is used for wrapping coils that need extra protection against moisture and UV rays.
- Steel Straps: Manufactured according to ASTM D3953 standards, steel straps are used to bind heavy coils, ensuring they remain stable during transit.
- Plastic Straps: For lighter coils, plastic straps made from polypropylene or polyester are often used. These materials are resistant to corrosion and offer excellent durability.
Each material is chosen based on the specific needs of the coil and the conditions it will face during shipping or storage. The goal is to provide maximum protection while keeping material costs under control.
6. Ensuring Coil Integrity with Advanced Monitoring Systems
One of the critical advancements in modern packing lines is the integration of real-time monitoring and data collection systems. By using sensors and IoT-enabled devices, manufacturers can monitor the status of each coil during the packing process, ensuring that any anomalies are detected and corrected in real-time.
Real-world Example: A steel producer in South Korea installed sensor-based monitoring systems in their coil packing line, allowing them to track the tension applied during strapping and the overlap percentage during wrapping. This system reduced the rate of improperly packed coils by 15%, significantly improving product consistency.

7. Safety Considerations in Modern Packing Lines
Automation not only increases efficiency but also enhances safety by reducing the need for manual intervention in dangerous tasks. Steel coils are heavy, and improper handling can lead to serious workplace injuries. Modern packing lines are designed with safety mechanisms that include:
- Emergency stop buttons located at multiple points along the line.
- Safety sensors that detect when a human is in proximity to moving parts, immediately pausing operations.
- Enclosed strapping heads to prevent accidents during the high-tension strapping process.
Additionally, operators are trained to adhere to ISO 45001 safety management systems, ensuring a standardized approach to health and safety throughout the manufacturing process.
8. Automation and Data Integration: Enhancing Productivity
The integration of automation and data management in modern steel coil packing lines is not just about speeding up operations—it’s about creating a smart, connected production environment. In line with Industry 4.0 principles, these systems are capable of collecting and analyzing data from every stage of the packing process. This data is invaluable for identifying bottlenecks, optimizing workflows, and predicting maintenance needs.
How Data Integration Works:
- Sensors placed throughout the packing line monitor everything from coil dimensions to wrapping tension and strapping pressure. These sensors feed real-time data into a central system, which operators can access to make immediate adjustments.
- Big Data Analysis: The large volume of data collected from these lines is analyzed using big data algorithms to detect patterns that may indicate potential inefficiencies. For instance, if a certain type of steel coil consistently requires more strapping force than others, the system can flag this anomaly for further investigation.
- Predictive Maintenance: One of the key benefits of data integration is predictive maintenance. Instead of relying on scheduled maintenance, automated systems can detect signs of wear or malfunction and alert operators before a breakdown occurs. This reduces unplanned downtime and extends the lifespan of the equipment.
Illustration Suggestion: A flowchart or diagram illustrating how data flows through the different components of a steel coil packing line, highlighting where data collection and analysis occur, could help readers understand how automation and data integration work in tandem.
9. Environmental Sustainability in Steel Coil Packing
As industries worldwide shift towards more sustainable practices, steel coil packing has also evolved to reduce environmental impact. Modern automated packing lines are designed to minimize material waste, energy consumption, and emissions.
Key Sustainability Features:
- Optimized Material Usage: Automated systems ensure that the exact amount of packing material—whether it be stretch film, HDPE sheets, or strapping—is used for each coil. This prevents overuse, reducing material waste and lowering costs.
- Energy-Efficient Machinery: Modern packing equipment is often powered by energy-efficient motors, reducing the overall energy consumption of the production line. In some cases, factories are also exploring renewable energy sources to power these machines.
- Recyclable Packaging Materials: Many manufacturers are moving towards using recyclable materials such as biodegradable plastic films and recycled steel straps. This shift helps reduce the carbon footprint associated with packaging materials and aligns with global sustainability initiatives.
Real-world Example: A steel manufacturer in Italy implemented recyclable plastic straps into their coil packing line, which reduced their overall waste disposal costs by 15% while meeting ISO 14001 environmental management standards.
10. The Role of Robotics in Modern Steel Coil Packing
Another significant development in steel coil packing is the introduction of robotics. Robotic arms and automated forklifts have become integral components of packing lines, particularly in the handling and positioning of heavy steel coils.
Key Robotic Applications:
- Robotic Coil Positioning: Robotic arms equipped with end-effectors designed for steel coils can handle the positioning of coils before they enter the packing line. This reduces the need for human operators to perform dangerous lifting tasks, enhancing workplace safety.
- Automated Guided Vehicles (AGVs): AGVs are used to transport packed steel coils from the packing line to storage areas or loading docks. These vehicles are equipped with sensors and machine vision technology, allowing them to navigate factory floors autonomously, improving logistical efficiency.
Real-world Example: A steel plant in Japan integrated AGVs with their automated coil packing system, which reduced forklift-related accidents by 30% and improved overall packing line throughput by 20%.
11. Real-World Case Studies of Automated Steel Coil Packing Lines
Case Study 1: North American Steel Manufacturer
A leading steel manufacturer in North America upgraded their existing manual packing line to a fully automated system. The goal was to increase output without sacrificing the quality of the packed coils. After installing a modern packing line equipped with turnstiles, coil down-enders, and automated strapping systems, the company saw the following results:
- Throughput increased by 35%, allowing the company to meet growing demand.
- Damage claims dropped by 25%, thanks to the consistency and precision of the automated wrapping and strapping processes.
- Labor costs decreased by 15%, as fewer operators were needed to oversee the packing process.
Case Study 2: European Galvanized Steel Producer
A galvanized steel producer in Europe faced challenges with rust and corrosion during transport. By implementing automated HDPE wrapping and incorporating real-time data monitoring, the company was able to:
- Eliminate rust-related defects by 80%.
- Improve overall product quality and customer satisfaction, leading to increased repeat orders from key clients.
- Achieve a 25% reduction in material usage, lowering both operational costs and environmental impact.
12. Future Trends in Steel Coil Packing Lines
As technology continues to evolve, steel coil packing lines are likely to see even more advancements. Here are some forward-looking trends that are expected to shape the future of the industry:
- AI and Machine Learning Integration: While current systems rely on pre-programmed parameters, the next generation of packing lines will incorporate machine learning algorithms. These systems will learn from historical data to optimize packing methods, material usage, and machine settings in real-time without human intervention.
- Augmented Reality (AR) for Maintenance: AR technology will allow operators to conduct maintenance and troubleshooting remotely. Wearing AR glasses, technicians can view live data feeds from the packing line and receive real-time instructions on how to perform repairs or adjustments, reducing downtime.
- Carbon-Neutral Packing Solutions: As environmental concerns grow, manufacturers will increasingly move towards carbon-neutral packaging solutions. This may include innovations such as biodegradable strapping materials, solar-powered packing machines, and systems designed to have zero emissions.
- Blockchain for Supply Chain Transparency: Blockchain technology could be integrated into steel coil packing lines to provide an immutable record of every coil’s packing, shipping, and handling history. This would increase supply chain transparency, helping manufacturers track product movement and ensure compliance with regulatory standards.
Illustration Suggestion: A timeline or infographic showing the evolution of steel coil packing technology and predicting how future trends will shape the industry could provide readers with a clearer understanding of where the industry is headed.
Conclusion
The components of a modern steel coil packing line represent the cutting-edge of industrial automation and efficiency. From turnstiles and coil down-enders to wrapping and strapping machines, each part of the system plays a vital role in ensuring that steel coils are packed securely, consistently, and in compliance with global standards. The integration of Industry 4.0 technologies, such as real-time data monitoring, predictive maintenance, and robotics, has further enhanced the productivity, safety, and sustainability of these lines.
Looking ahead, advancements in AI, machine learning, and environmentally sustainable practices will continue to drive innovation in steel coil packing. For manufacturers, investing in modern automated systems is not just about improving operational efficiency today—it’s about future-proofing their business for the challenges and opportunities of tomorrow.