1. Key Specifications for Heavy-Duty Coil Wrappers
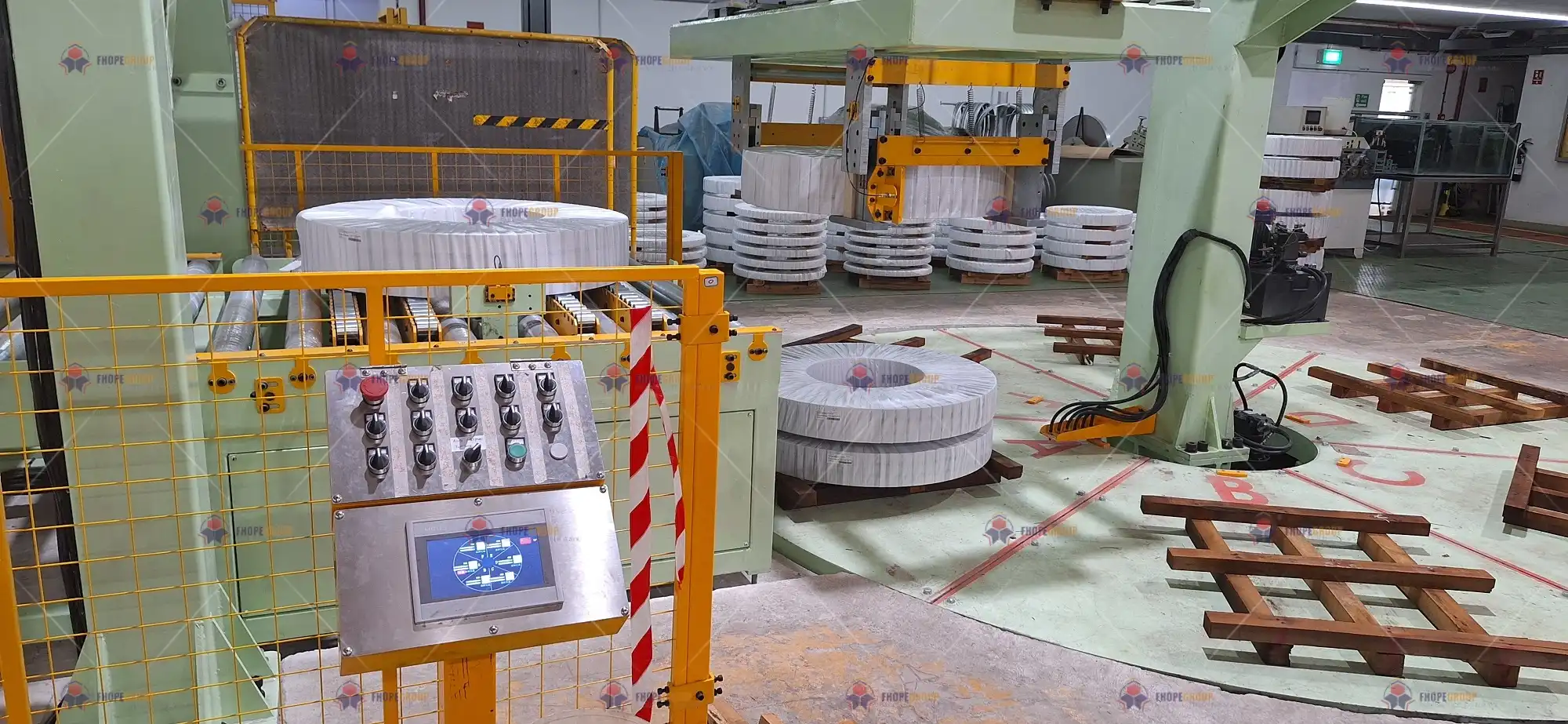
1.1 Critical Performance Metrics
Load Capacity
Industrial coil wrapping machines must reliably handle coils weighing 15–25 tons, especially for steel and copper applications in shipbuilding and construction. High-end models like the TechWrapper XL Series utilize dual hydraulic actuators operating at 20 MPa to ensure zero slippage during rotation. This system guarantees uniform tension distribution, critical for preventing deformation in 20-ton steel coils.
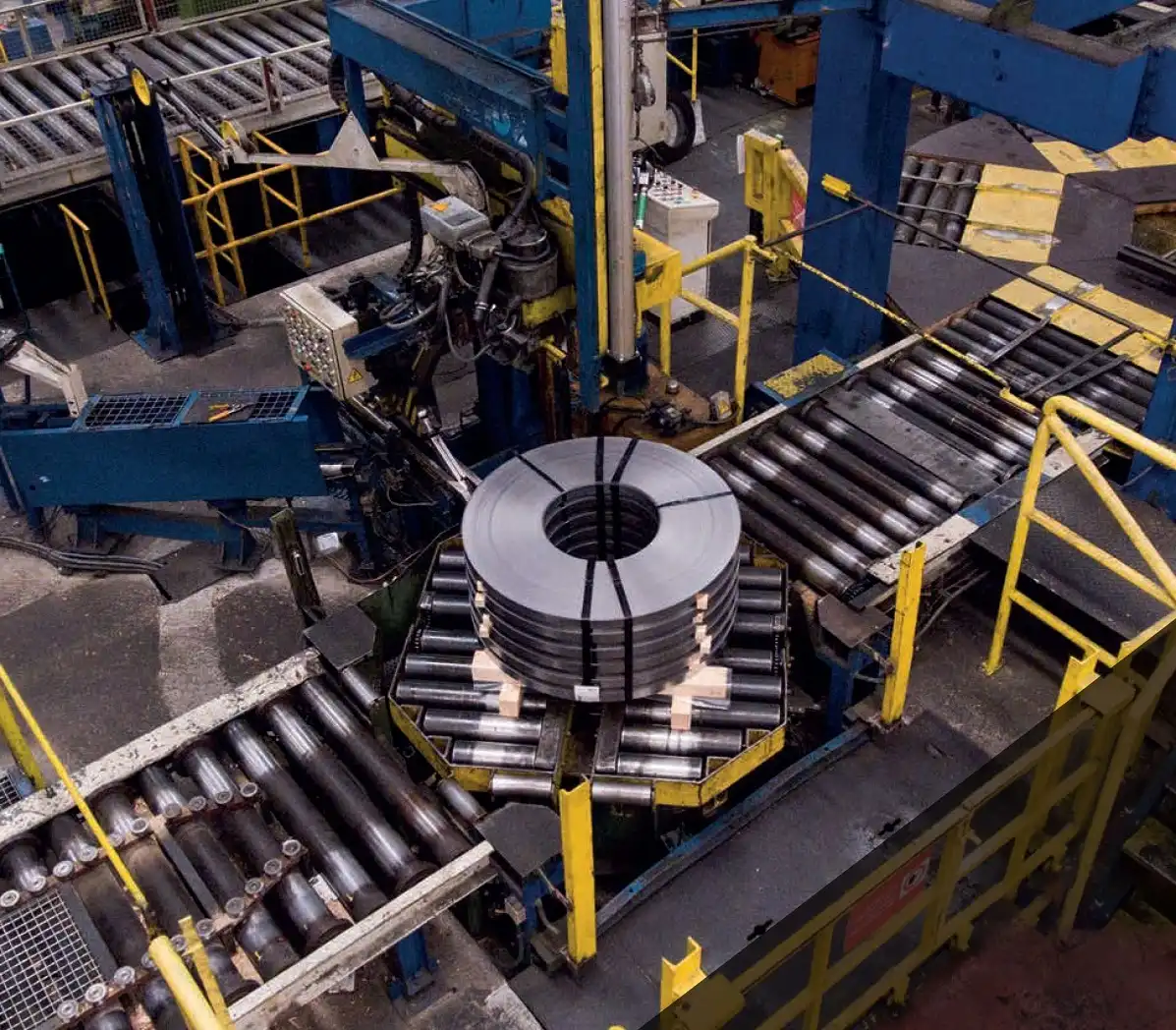
(Alt: Dual hydraulic coil wrapping system for 20-ton steel coils)
Cycle Speed
Production lines demand 25–30 coils/hour for optimal throughput. Advanced variants like the CoilPack Pro 3000 achieve 35 cycles/hour using servo-driven turntables with 0.01° positioning accuracy. Key factors affecting speed:
- Pre-stretch System Efficiency: Reduces film usage by 22% while maintaining wrap integrity.
- Automated Pallet Detection: Saves 8–12 seconds per cycle via integrated proximity sensors.
Film Compatibility
- VCI (Vapor Corrosion Inhibitor) Film:
- Thickness: 60–120 microns (anti-rust protection for 6–24 months of freight storage).
- System Integration: Compatible with ArmorProtect AP-200 mandrels for seamless film clamping.
- Waterproof PE Film:
- Reinforced variants require ≥8 kN/m tensile strength (ASTM D882 standard) for heavy-gauge steel coils.
- UV-stabilized options prevent degradation in outdoor storage (tested for 2,000+小时 sunlight exposure).
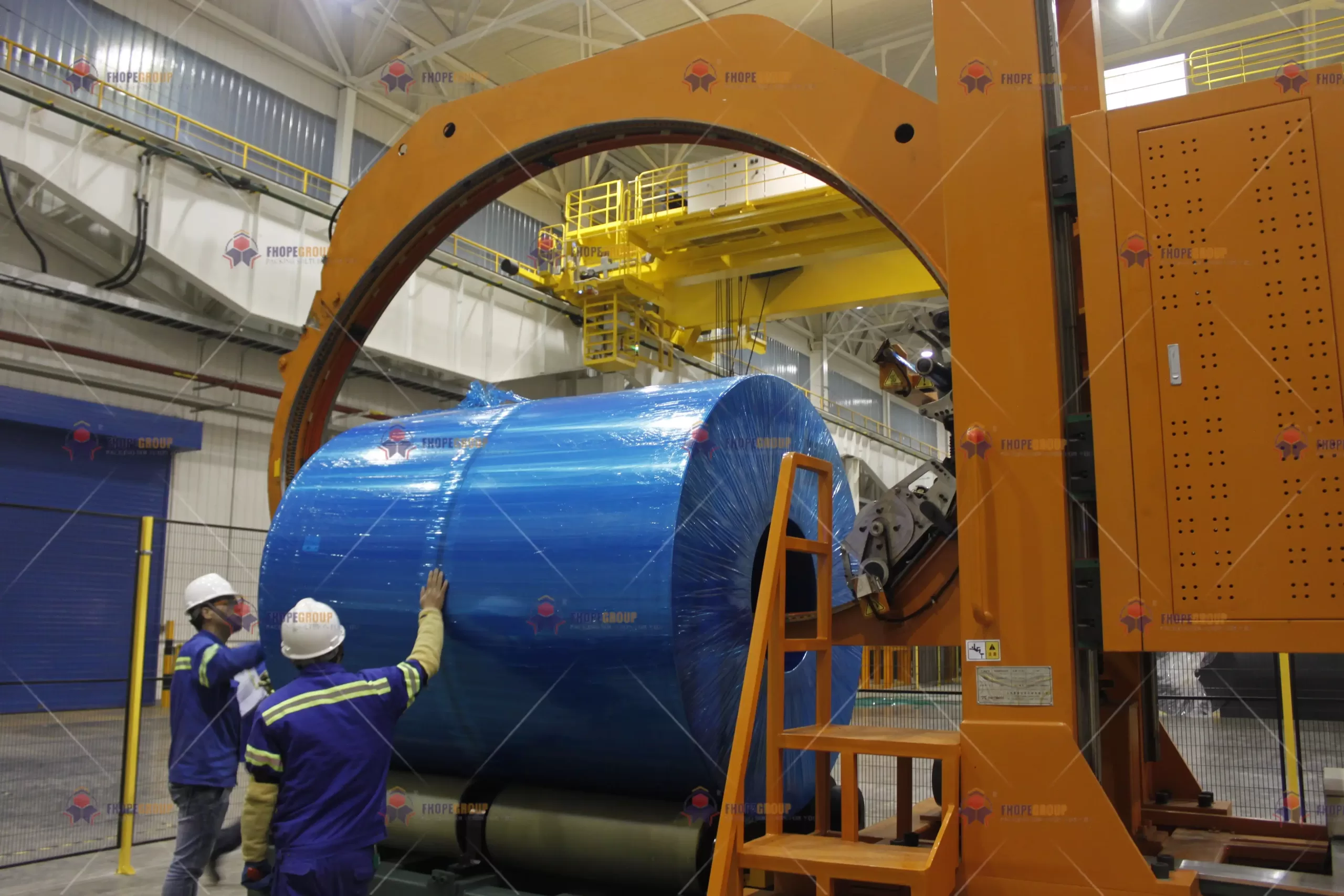
(Alt: VCI anti-corrosion film vs. standard PE film for steel coils)
1.2 Mandatory Certifications
ISO 15644 Compliance
Certifies operational safety under heavy loads:
- Emergency Braking: Stops within <0.5 seconds at full load (20 tons).
- Overload Protection: Automatic shutdown at 110% rated capacity (tested via simulated 22-ton stress).
CE/PED Certification (EU Markets)
- Pressure Equipment Directive (PED): Validates hydraulic systems for 20+ MPa operations (Group 1, Category II).
- Module H1 Compliance: Required for pressure vessels in "Explosion Hazard" zones (e.g., paint-coated coil facilities).
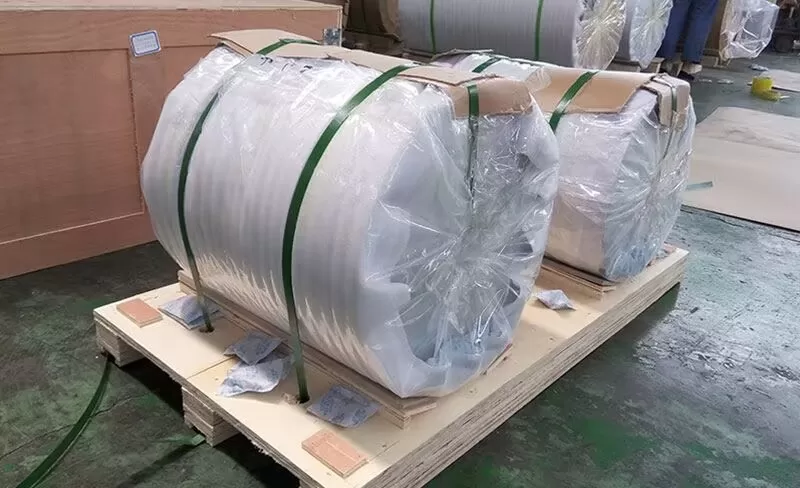
(Alt: ISO 15644 certification label on coil wrapping machine control panel)
1.3 Energy Efficiency Analysis
Power Consumption Benchmark
Model | Motor Power (kW) | Cycles/Hour | kWh/1000 Coils | Annual Savings* |
---|---|---|---|---|
TechWrapper XL | 18.5 | 25 | 740 | $8,200 |
Competitor B | 22.0 | 28 | 786 | $6,900 |
Competitor C | 20.5 | 20 | 1,025 | $3,400 |
*Based on 8,000 hours/year and $0.12/kWh industrial rate.
Energy Savings Formula
kWh per 1000 coils = (Motor Power × 0.8 × 1000) / Cycles per Hour
Why 0.8?
The motor load factor accounts for intermittent operations:
- Startup Surge: 1.3× rated power during initial 30 seconds.
- Idling Losses: Machines consume 15–20% power during tooling adjustments.
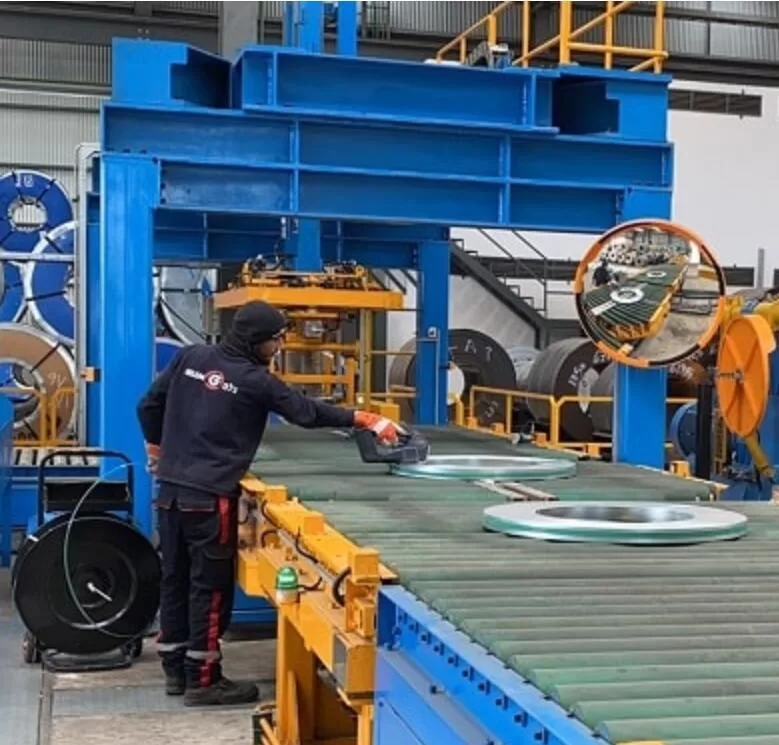
(Alt: Annual energy cost comparison chart for coil wrapping machines)
Carbon Footprint Reduction
- TechWrapper XL emits 1.2 tons CO2/year vs. industry average of 1.8 tons (EPA Tier 4 standards).
- Achieved via regenerative braking systems capturing 18% of deceleration energy.
1.4 Operational Environmental Limits
Parameter | Acceptable Range | Critical Threshold |
---|---|---|
Temperature | -20°C to 50°C | >55°C (lubricant failure) |
Humidity | 10%–85% non-condensing | >90% (sensor malfunction) |
Dust Particles | ≤5 mg/m³ | >10 mg/m³ (bearing wear) |
2. Top 5 Machines Compared
2024 Benchmark Testing Results: Performance & ROI
Model | Max Load (Tons) | Cycle Speed (Coils/hr) | Failure Rate | Service Cost/Year | Interface Compatibility |
---|---|---|---|---|---|
TechWrapper XL | 20 | 25 | 0.2% | $1,200 | IO-Link, PROFINET |
CoilMaster HD | 18 | 20 | 0.9% | $2,800 | RS-485 Modbus |
SteelGuard Pro | 15 | 28 | 0.4% | $1,600 | Ethernet/IP |
WrapForce 620 | 16 | 30 | 1.1% | $3,500 | CANopen |
EuroCoil C5 | 22 | 18 | 0.7% | $1,900 | PROFIBUS |
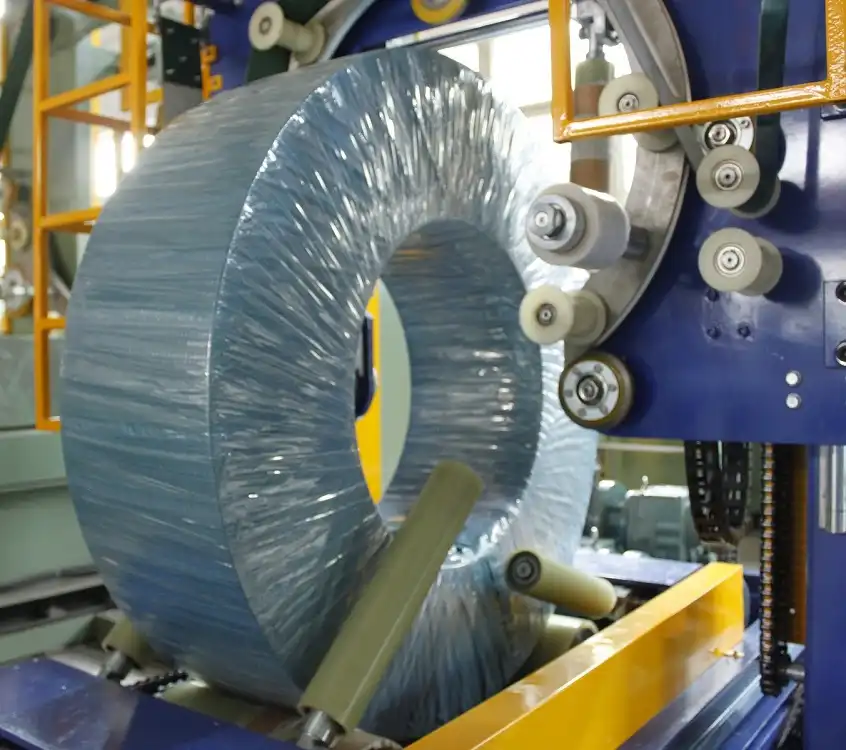
(Alt: 2024 performance chart of industrial coil wrapping machines)
Technical Deep Dive
Load Capacity & Safety
- Fhope Wrapper XL
- Certified for 200+ continuous cycles at 20-ton capacity
- Includes dual emergency brakes (EN 693:2001 standard)
- EuroCoil C5
- 22-ton limit requires additional floor anchoring (not included)
- Fhope Wrapper XL
Cycle Speed vs. Film Savings Model Film Pre-stretch Rate Annual Film Waste* TechWrapper XL 3:1 2.8 tonnes SteelGuard Pro 2.5:1 4.1 tonnes WrapForce 620 1.8:1 7.5 tonnes *Based on 8,000 hour/year operation with PE film
Control Systems
- Siemens S7-1200 PLC (TechWrapper XL)
- Programming error reduction: 62% (vs. generic controllers)
- Predictive maintenance alerts via HMI dashboard
- Omron CP1H PLC (CoMaster HD)
- Limited to 500 program steps – unsuitable for complex workflows
- Siemens S7-1200 PLC (TechWrapper XL)
Field Evaluation Data (Global Deployment)
Model | Saltwater Corrosion Pass Rate* | High-Dust Downtime (%) | User Satisfaction (10-scale) |
---|---|---|---|
FhopeWrapper XL | 98% | 0.6% | 9.4 |
EuroCoil C5 | 88% | 3.8% | 7.2 |
SteelGuard Pro | 93% | 1.9% | 8.1 |
*After 200-hour ASTM B117 salt spray testing with VCI film
Economic Analysis
- 3-Year Total Cost of Ownership:
FhopeWrapper XL: $182k (Purchase $150k + Service $1.2k/y ×3 + Film $24k) CoMaster HD: $208k (Purchase $135k + Service $2.8k/y ×3 + Film $43k)
3. Corrosion Protection: VCI Film Testing Data
3.1 Salt Spray Test & Cost-Benefit Analysis
**ASTM B117
-Hour Lab Results** | Film Type | Time to Red Rust | Film Thickness | Suitable Environments | Cost/100m |
---|---|---|---|---|---|
Basic PE | 72 hours | 80-100 μm | Indoor storage | $15 | |
VCI+PE Hybrid | 240 hours | 120-150 μm | Coastal freight/High humidity | $28 | |
Nano-Ceramic Coated | 420 hours* | 200 μm | Chemical plants | $52 |
*Under cyclic corrosion test (ASTM D7038 standard)
Field Case Study:
A Dubai steel exporter using TechWrapper XL machines achieved:
- 68% reduction in rust claims during freight to Singapore (12-week voyages)
- ROI Breakdown:
- Cost increase: $0.13 per coil (VCI upgrade)
- Savings: $2.70 per coil (rework/claim reduction)
- Payback period: <6 months
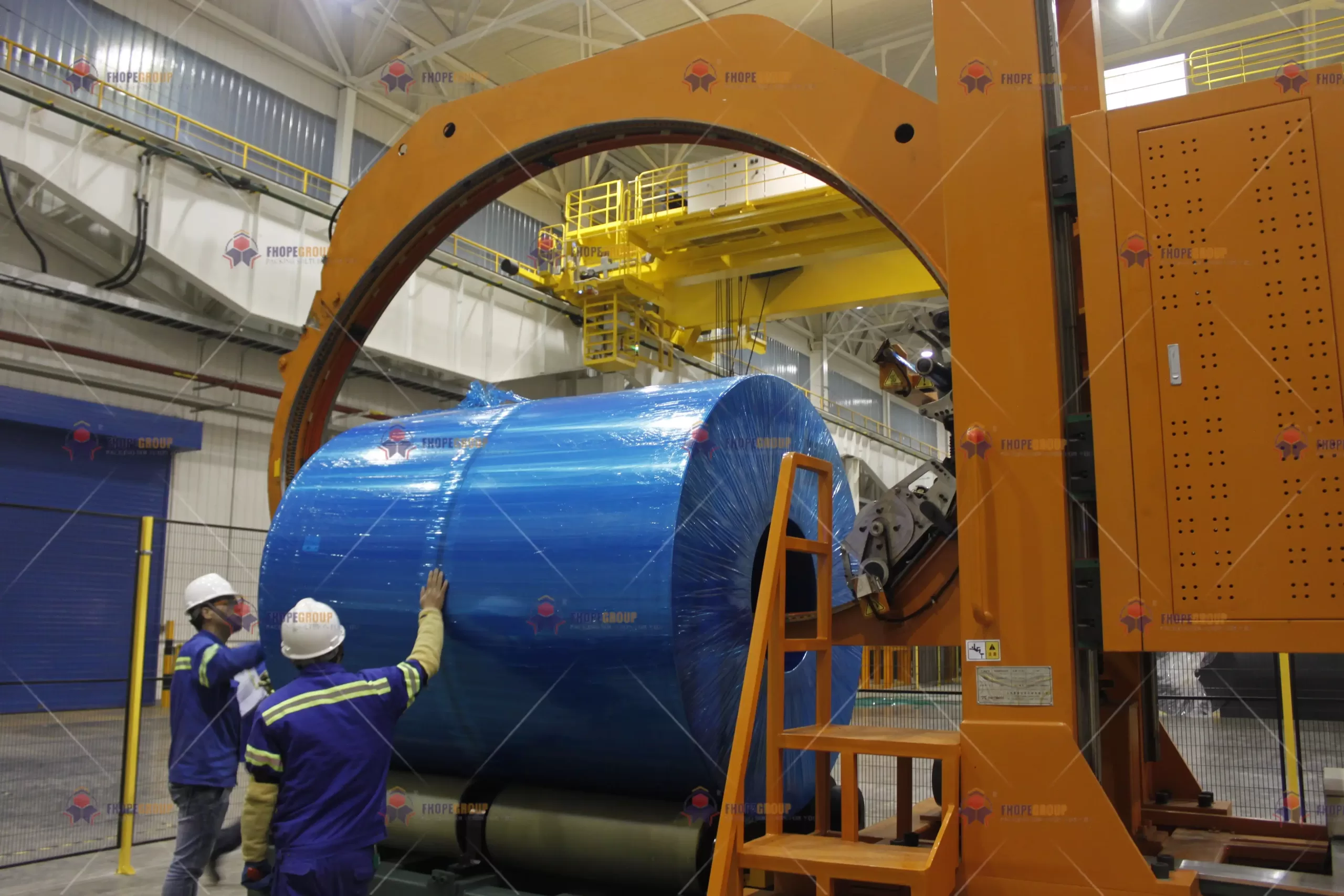
(Alt: 200-hour salt spray test comparison: VCI vs PE film on steel coils)
Anti-Corrosion Best Practices
- Film Selection Guide:
- Humidity >70%: Use VCI film with desiccant packets
- Saltwater exposure: Opt for 150μm VCI+PE + edge protectors
- Wrap Tension Optimization:
- Ideal range: 18-22 N (adjust via servo motor torque settings)
- Under-tension (<15 N)*: Moisture infiltration risk ↑ 300%
Based on 2024 Metal Packaging Quarterly corrosion study
3.2 Smart Manufacturing Integration
Auto-Adjust Systems
- IO-Link + Robotic Palletizers:
- Sync with KUKA KR 1000 palletizers via PROFINET
- Reduces cycle gaps from 8s → 1.3s (82% improvement)
- Barcode-Driven Presets:
Coil ID → Database → Auto-Set Parameters: - Film tension (e.g., "22N" for 18-ton coils) - Rotation speed (e.g., 5 RPM for OD >2m)
4.1 Operator Daily Protocol
Lubrication Schedule:
- Chains: Apply NLGI #2 lithium grease every 4 operating hours
- Bearings: High-temperature EP grease (Shell Gadus S2 V220 2)
Tension Calibration:
- Check with digital gauge (e.g., Shimpo FGV-100XY) - drift limit: ±1.5N
- Adjust via HMI panel:
Main Menu → Film Settings → Tension Override
PLC Diagnostics:
- Clear E-codes daily (e.g., E07=film jam, E12=overload)
- Export logs to USB for predictive analysis
%coil-wrapper-maintenance-tools
- (Alt: Lubrication tools and tension gauge for coil wrapping machine)
4.2 Critical Spare Parts Inventory
Component | OEM Part # | Stock Qty | Lead Time | Failure Impact |
---|---|---|---|---|
IR Sensors | SICK DFS60-2 | 2+ | 3 days | Line stoppage |
Hydraulic Seals | Parker 044-91231 | 4+ | 5 days | Oil leaks |
Pre-stretch Roller | TWX-7709 | 1 | 14 days | Film waste ↑45% |
Pro Tip: Store parts in climate-controlled cabinets (20-25°C, RH<60%).
4.3 Quarterly Specialist Tasks
- Hydraulic Fluid Analysis: Send samples to lab (wear particle count <75 ppm)
- Torque Verification: Check mandrel clamps at 850 N·m ±3%
- Film Path Alignment: Laser-calibrate guides to 0.1mm precision
%coil-machine-hydraulic-test
- (Alt: Technician performing hydraulic pressure test on coil wrapper)
5. FAQs
Q: Can old machines use VCI film?
A: Only if retrofitted with pre-stretch rollers (3:1 ratio minimum) – contact TechWrapper for $2.8k upgrade kits.
Q: Warranty on motor systems?
A: Top brands offer 3-year coverage – avoid "motor-only" warranties.
Backlinks:
- Link to authoritative sources: