The Significant Benefits of Connecting ERP and MES for Steel Service Centers in Coil Slitting and Packing
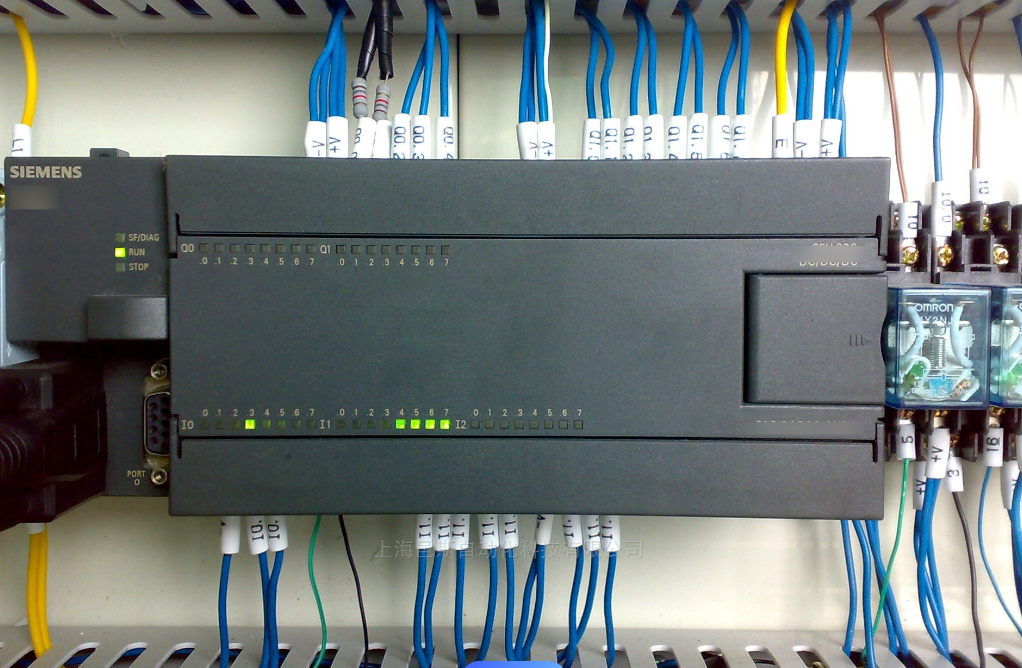
Introduction
In the steel industry, service centers play a pivotal role by processing large steel coils into specific sizes for downstream manufacturing. One of the most critical operations within these centers is coil slitting and packing. Coil slitting is the process of cutting large steel coils into narrower strips, which are then packaged and sent to various customers. This procedure is complex, requiring precision, efficiency, and effective communication between departments. Any mistakes or inefficiencies in this process can lead to costly downtime, material waste, and delayed orders.
To address these challenges, steel service centers are increasingly turning to the integration of Enterprise Resource Planning (ERP) systems and Manufacturing Execution Systems (MES). These technologies provide significant advantages by connecting the business and production sides of operations, streamlining workflows, and ensuring that coil slitting and packing processes are carried out efficiently and accurately. In this article, we will explore how ERP and MES integration can enhance productivity, reduce errors, and optimize material handling in steel service centers, particularly in the context of coil slitting and automatic packing lines.
Challenges in Coil Slitting and Packing
Before delving into the benefits of ERP and MES integration, it is important to understand the common challenges faced by steel service centers in coil slitting and packing:
Manual Processes:
In many steel service centers, manual coordination between the coil slitting and packing stages creates inefficiencies. These manual systems lead to frequent miscommunication, slow production cycles, and errors such as mislabeled coils. For instance, it can become difficult to ensure that the label information—such as PO numbers, customer names, or order details—aligns with the correct slit coils. This lack of synchronization often results in delays or incorrect deliveries, ultimately impacting customer satisfaction and operational efficiency.
Quality Control:
Maintaining precision during the slitting process is essential for product quality. Minor inaccuracies in the cut can lead to significant defects, such as coils that don’t meet the required dimensions, causing customer dissatisfaction or returns. Additionally, special packaging requirements specified by customers may not always be met, further complicating order fulfillment. Without proper data tracking, identifying the source of a quality problem becomes impossible, hampering efforts to retrospectively address or prevent similar issues in future production.
Material Tracking:
Proper real-time material tracking is essential for managing inventory and optimizing production. Without an integrated system, keeping track of coil usage becomes a manual and error-prone process. This can lead to inaccurate stock counts, causing either material shortages or overproduction, both of which are costly. The lack of a unified system also impedes effective production planning, making it challenging to coordinate material flow between departments and ensure that orders are fulfilled on time.
Labor-Intensive Packing:
The packing stage in steel service centers often involves multiple manual steps, such as wrapping, securing, and labeling each coil. This process can be labor-intensive and prone to errors, particularly when packing requirements vary from customer to customer. Some coils may need specific packaging while others do not, leading to confusion and inconsistency when the process is manual. Automating these steps is necessary to reduce human errors and ensure that each coil is packed according to order specifications.
Production Planning Gaps: When production planning is not well-integrated with real-time shop floor data, it can lead to significant scheduling gaps. Orders may be delayed due to inaccurate planning, and operational capacity can be underutilized. For example, coils stored in the warehouse that require packing may not be properly tracked or prioritized in the production plan, leading to missed deadlines and inefficient resource use. This lack of alignment between business systems and operational workflows hampers the service center’s overall efficiency.
The Role of ERP and MES
Enterprise Resource Planning (ERP) systems are primarily focused on the business side of operations, providing insights into inventory management, finance, and order processing. On the other hand, Manufacturing Execution Systems (MES) handle the production side, tracking the execution of manufacturing processes, equipment status, and work-in-progress (WIP) data in real time.
In a steel service center, connecting ERP and MES allows for an integrated approach to managing both the business and production processes. This enables more accurate planning, real-time tracking of materials and production progress, and enhanced collaboration between different teams.
When applied to coil slitting and packing, ERP-MES integration offers several key advantages:
- Real-Time Production Data: MES captures real-time data from the production floor, including information about machine status, coil consumption, and product output. This data is then shared with the ERP system, allowing for accurate inventory updates, order tracking, and production forecasts.
- Seamless Communication: By integrating ERP and MES, service centers can ensure that production plans from the ERP system are automatically communicated to the MES, which then executes these plans on the shop floor. This eliminates manual data entry and reduces the risk of errors.
- Automated Material Handling: In an automatic coil packing line, MES can monitor and control the entire packaging process, ensuring that the correct packaging materials are used, and that each coil is securely wrapped and labeled according to customer specifications. This reduces labor costs and improves packaging consistency.
Key Benefits of ERP-MES Integration
Real-Time Production Visibility
One of the most significant benefits of ERP-MES integration is real-time visibility into production processes. In a coil slitting and packing line, this means that operators, managers, and planners can monitor production in real time, enabling them to respond quickly to any issues that arise. For example, if a slitting machine experiences a malfunction, MES will immediately alert the system, and the ERP can adjust production schedules to accommodate the downtime. This helps to minimize disruptions and ensures that production continues smoothly.
Optimized Material Handling
Steel coils are valuable materials, and any waste or inefficiency in handling them can result in significant financial losses. MES provides detailed tracking of coil usage during the slitting process, ensuring that material is used efficiently. Additionally, the integration of automatic packing lines with MES ensures that coils are packed correctly and consistently, minimizing the risk of damage during transportation. By synchronizing material handling with production schedules, service centers can reduce waste and improve overall productivity.
Enhanced Quality Control
Quality control is critical in the steel industry, where even minor defects can lead to significant issues downstream. By integrating ERP and MES, service centers can ensure that quality control is embedded into every stage of the production process. MES tracks coil slitting in real-time, providing data on tolerance deviations, machine performance, and product quality. This data is then shared with the ERP system, enabling managers to identify trends, track defects, and make data-driven decisions to improve quality over time.
Inventory and Supply Chain Management
Efficient inventory management is crucial for any service center, particularly in industries like steel where raw materials are expensive and lead times are long. By connecting ERP and MES, service centers can gain better control over their inventory levels, ensuring that they have the right materials available at the right time. This is especially important for coil slitting and packing, where the availability of the correct coil sizes and packing materials can directly impact production efficiency. Moreover, this integration allows for more accurate demand forecasting, helping service centers plan their supply chain more effectively.
Reduced Downtime and Increased Machine Utilization
In any production environment, particularly in steel service centers, downtime is a major concern. Unplanned machine stoppages or extended maintenance windows can significantly disrupt production schedules, delaying shipments and increasing costs. ERP-MES integration helps minimize these disruptions by facilitating predictive maintenance. MES collects real-time data from slitting and packing machines, tracking factors such as operating hours, performance metrics, and machine wear. This information is then communicated to the ERP system, which can automatically schedule maintenance based on machine health rather than a fixed schedule.
This predictive approach to maintenance ensures that machines are serviced only when necessary, reducing unnecessary downtime while preventing catastrophic equipment failures. In addition, ERP-MES integration helps improve machine utilization by optimizing production schedules. By understanding machine availability and performance in real time, ERP can adjust production plans dynamically, ensuring that the coil slitting and packing lines are always operating at maximum efficiency.
Data-Driven Decision Making
Steel service centers are increasingly reliant on data to make informed business decisions, especially in an era where efficiency and competitiveness are key. One of the most powerful advantages of ERP-MES integration is the ability to gather and analyze large amounts of production data. This data can provide valuable insights into every aspect of the coil slitting and packing process, from machine performance and material usage to quality control and production rates.
By having access to this data in real time, managers can make data-driven decisions that improve efficiency and reduce costs. For example, they can identify bottlenecks in the slitting process, optimize material flow, or adjust production schedules based on historical performance data. The ability to analyze trends over time also enables service centers to continuously improve their operations, driving greater profitability and customer satisfaction.
Moreover, business intelligence tools integrated with ERP-MES systems can provide detailed reports and dashboards that give decision-makers a comprehensive view of their operations. This empowers them to make strategic decisions quickly, responding to changing customer demands or market conditions with agility. In a highly competitive industry like steel processing, this level of insight can provide a significant competitive advantage.
Enhanced Customer Service and Order Accuracy
In today's market, customers expect not only high-quality products but also timely delivery and transparent communication throughout the order process. ERP-MES integration plays a crucial role in improving customer service by ensuring that service centers can provide accurate, real-time information about production status, lead times, and order fulfillment.
When a customer places an order, the ERP system can immediately access data from the MES to determine the current status of production, including the availability of materials, machine capacity, and expected completion times. This level of visibility allows sales teams to provide accurate delivery estimates, improving customer satisfaction and trust. Furthermore, the integration ensures that orders are fulfilled correctly, with coils being slit to the correct specifications and packaged according to customer requirements.
ERP-MES integration also helps reduce errors in order fulfillment. By automating the flow of information between departments, it eliminates the need for manual data entry and reduces the risk of miscommunication. This not only improves the accuracy of the slitting and packing processes but also ensures that customers receive their products on time and as expected. The result is a more efficient operation that meets customer demands consistently, enhancing the reputation of the service center.
Case Example: ERP-MES Integration in Action
Consider a steel service center that specializes in providing slit coils for automotive manufacturers. This service center previously faced significant challenges in managing its production processes, particularly in coordinating between the slitting and packing departments. Manual tracking of materials and production schedules led to frequent delays, and quality control issues resulted in high levels of rework and scrap.
After implementing an integrated ERP-MES system, the service center saw immediate improvements in operational efficiency. Real-time data from the MES allowed for more accurate production planning, ensuring that coils were slit and packed according to customer specifications. Automated material handling systems, controlled by the MES, reduced the need for manual labor in the packing process, improving both speed and accuracy.
In addition, the service center was able to implement predictive maintenance for its slitting machines, reducing downtime by 30%. This increase in machine availability, combined with optimized production schedules, allowed the service center to fulfill orders faster and with fewer errors. The data collected from the integrated system also provided valuable insights into production trends, enabling the center to continuously improve its processes and reduce costs over time.
Conclusion
In conclusion, the integration of ERP and MES offers significant benefits for steel service centers, particularly those involved in coil slitting and packing. By connecting the business and production sides of operations, this integration improves real-time visibility, enhances material handling, optimizes machine utilization, and enables data-driven decision making. In addition, it ensures that orders are fulfilled accurately and efficiently, improving customer satisfaction and driving profitability.
For steel service centers looking to remain competitive in a fast-paced industry, ERP-MES integration is no longer a luxury—it is a necessity. With the ability to streamline operations, reduce costs, and improve product quality, this technology provides a clear path to success in coil slitting and packing operations.