Understanding Orbital Wrappers and Bar Wrapping Machines for Industrial Packaging
Packaging long, heavy, or irregularly shaped products like metal bars, extrusions, lumber, or pipes presents unique challenges in industrial settings. Ensuring these items are securely bundled, protected from damage and environmental factors, and stabilized for transport requires specialized equipment. Two key solutions often employed are orbital wrappers and bar wrapping machines. This guide explores their functions, benefits, and applications to help you understand how they streamline packaging operations.
What is an Orbital Wrapper?
Orbital stretch wrappers, also known as horizontal wrappers or ring wrappers, are designed to apply stretch film around products that are often too long or cumbersome for traditional turntable pallet wrappers.
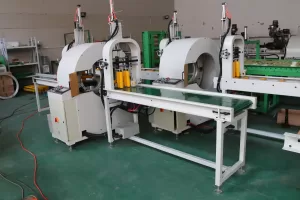
How it Works:
Instead of the load rotating, the product typically moves horizontally through the machine on conveyors. A ring or rotating arm carrying the stretch film roll revolves around the stationary or slow-moving product, applying the film in a spiral pattern. This method ensures complete coverage along the length of the item.
Key Components Often Include:
- Rotating Ring/Arm: Holds and dispenses the stretch film.
- Film Carriage: Contains the film roll and pre-stretch mechanism (if applicable) to optimize film usage.
- Conveyor System: Transports the product through the wrapping zone.
- Clamping and Cutting Unit: Automatically grips the film at the start and cuts it at the end of the cycle.
- Control Panel: Allows operators to set parameters like wrap counts, tension, and conveyor speed.
Core Benefits of Using Orbital Stretch Wrappers
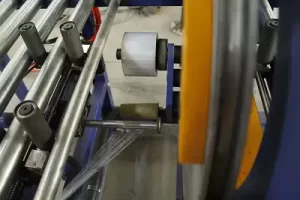
Implementing orbital wrapping technology offers several advantages for packaging long products:
- Enhanced Load Security: Provides tight, consistent containment, stabilizing bundles of bars, pipes, or extrusions, reducing movement during handling and shipping.
- Product Protection: Shields items from dust, moisture, scratches, and other potential damage. Opaque or UV-inhibitor films can offer additional protection.
- Increased Efficiency: Significantly faster than manual wrapping methods, boosting throughput and reducing labor costs.
- Consistent Application: Ensures uniform film tension and overlap, leading to reliable package integrity.
- Versatility: Capable of handling a wide variety of product lengths, shapes (round, square, irregular), and bundle configurations.
Understanding the Bar Wrapping Machine
While often used interchangeably with horizontal orbital wrappers, a bar wrapping machine typically refers to an orbital wrapper specifically configured or optimized for handling elongated products like metal bars, rods, tubes, and extrusions common in the metal fabrication industry.
These machines share the core orbital wrapping principle but may include features tailored for these specific applications:
- Heavy-Duty Construction: Built to withstand the demands of handling heavy metal products.
- Specialized Conveyors: May utilize V-rollers, flat belts, or chain conveyors designed to support and move bars or bundles smoothly.
- Profile-Specific Guides: Input and output guides may be designed to accommodate specific shapes or prevent product damage.
- Robust Clamping/Cutting: Mechanisms designed for reliable operation with potentially thicker films sometimes used for metal products.
Common Applications Across Industries
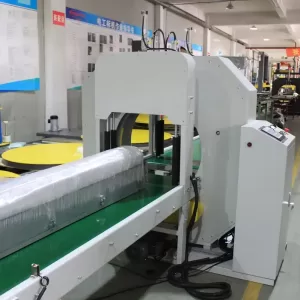
Orbital and bar wrapping machines are indispensable in various sectors:
- Metal Fabrication: Wrapping steel bars, aluminum profiles, copper pipes, and bundles of metal stock.
- Lumber and Wood Products: Bundling timber, planks, molding, and engineered wood products.
- Plastics Industry: Packaging plastic pipes, conduits, window profiles, and extrusions.
- Construction: Securing rebar, scaffolding components, and other long building materials.
- Textiles and Flooring: Wrapping rolls of carpet, fabric, or vinyl flooring.
Selecting the Right Wrapping Solution
Choosing the appropriate machine depends on several factors:
- Product Specifications: Consider the minimum and maximum length, width, height, and weight of the products to be wrapped.
- Throughput Requirements: Determine the number of packages needed per hour or shift. This influences the required level of automation. Options range from a semiauto wrapping machine requiring manual feeding and cutting to fully automated systems integrated into production lines.
- Bundle Configuration: Will you be wrapping single items or bundles? How are bundles formed?
- Film Type: Consider the necessary film thickness, pre-stretch capabilities, and any special requirements (e.g., UV protection, color).
- Operating Environment: Factor in space constraints and integration with existing material handling equipment.
- Budget: Balance initial investment cost with long-term operational savings and return on investment (ROI).
Conclusion
Orbital wrappers and specialized bar wrapping machines provide efficient, reliable solutions for packaging long and challenging products. By securely unitizing and protecting items like metal bars, extrusions, and lumber, these machines help prevent damage, reduce packaging costs, and improve overall operational efficiency in fabrication, distribution, and manufacturing environments. Evaluating your specific product characteristics, throughput needs, and operational context is key to selecting the most effective wrapping technology for your application.