Optimizing Load Security: A Guide to Automatic Turntable Pallet Wrapping Machines
Ensuring palletized goods are stable and secure during transit and storage is crucial in modern logistics and manufacturing. Damage during shipping can lead to significant costs and customer dissatisfaction. Automatic turntable pallet wrapping machines provide an efficient, consistent, and reliable solution for applying stretch film to pallet loads, enhancing stability and protection.
Automatic turntable pallet wrapping machine
Understanding the Core Mechanics
Automatic turntable wrappers operate on a simple yet effective principle:
- Loading: A pallet loaded with goods is placed onto the machine's turntable.
- Film Attachment: The leading edge of the stretch film is typically attached manually to the load or using an automatic clamping system.
- Wrapping Cycle: The machine initiates the wrap cycle. The turntable rotates the pallet at a controlled speed. Simultaneously, the film carriage, holding the roll of stretch film, travels vertically up and down a mast alongside the load. Most modern machines incorporate a powered pre-stretch unit within the carriage, stretching the film before application. This maximizes film yield and ensures tighter load containment.
- Completion: Once the programmed number of wraps is complete, the cycle stops. Depending on the machine's level of automation, the film may be automatically cut and sealed to the load.
Essential Features for Optimal Pallet Wrapping
These machines come equipped with various features designed to optimize the wrapping process for different load types and operational needs:
Programmable Wrap Cycles
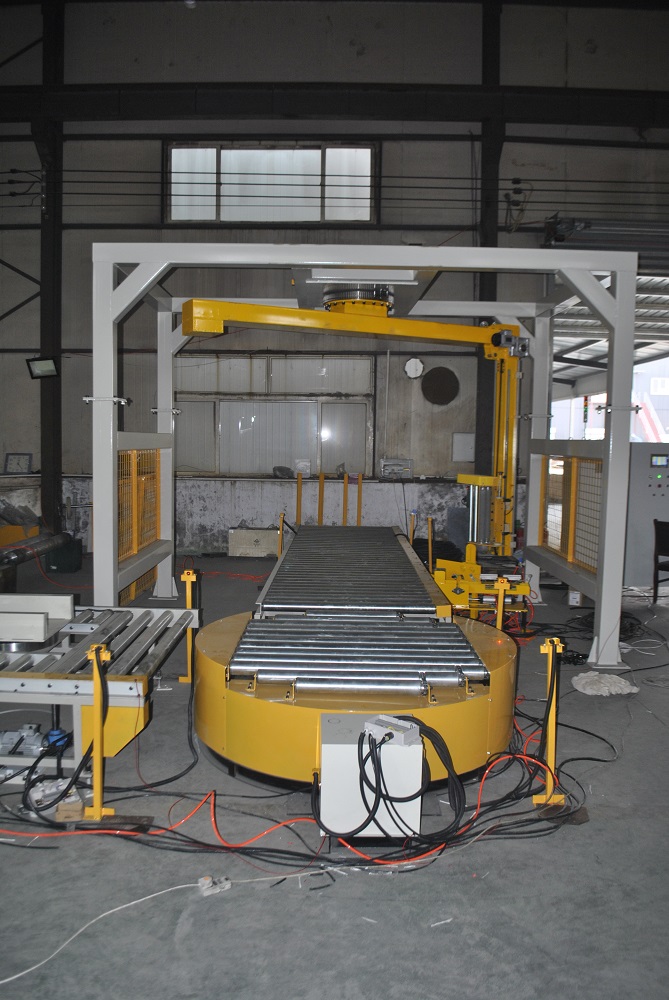
Flexibility in programming the wrap cycle is key. This includes:
- Separate Top and Bottom Wraps: Allows operators to set a different number of film layers (typically from 1 to 9) for the top and bottom sections of the load compared to the main body. This reinforces crucial stability points without wasting film on the entire height.
- Variable Cycle Parameters: Settings for parameters like turntable speed, carriage speed (up/down), and film tension can be adjusted and saved for specific load types.
Independent Speed Controls
The ability to independently control the turntable rotation speed and the film carriage's vertical travel speed is critical.
- Load Stability: Lighter or less stable loads may require slower rotation speeds to prevent shifting.
- Throughput: Stable, uniform loads can often be wrapped at higher speeds, increasing throughput.
- Wrap Pattern: Varying the ratio of turntable speed to carriage speed affects the film overlap and overall wrap pattern.
Automated Load Sensing
- Automatic Load Height Detection: A photo-eye sensor detects the top of the load automatically. This ensures the film carriage travels to the correct height for each pallet, regardless of variations, providing consistent wraps and preventing film waste or incomplete coverage.
User Interface and Control
- Electronic Control Panel: Modern machines feature intuitive control panels, often with membrane keypads or touchscreens. This allows for easy cycle selection, parameter adjustment, and diagnostics.
- Safety Features: Essential controls like an emergency stop button, pause mode, and jog mode (for manual positioning) enhance operator safety and control.
Film Management Features
- Film Break/End Alert: The system notifies the operator if the film roll runs out or breaks during a cycle, minimizing downtime and ensuring pallets aren't left partially wrapped.
- Carriage Memory Function: If the cycle is interrupted (e.g., for a film change), the carriage often remembers its last position, allowing the wrap cycle to resume correctly without needing to restart from the beginning.
- Reinforcement Wraps: Some systems allow operators to manually pause and apply additional film layers to specific areas during the cycle if extra reinforcement is needed.
Safety and Reliability
- Safety Guarding: Protective guarding around moving parts like the turntable and mast is essential for operator safety in an industrial environment.
- Robust Construction: Designed for industrial use, these machines typically feature heavy-duty steel construction and reliable components to ensure long service life and maximum uptime.
Advantages of Implementing an Automatic Turntable Wrapper
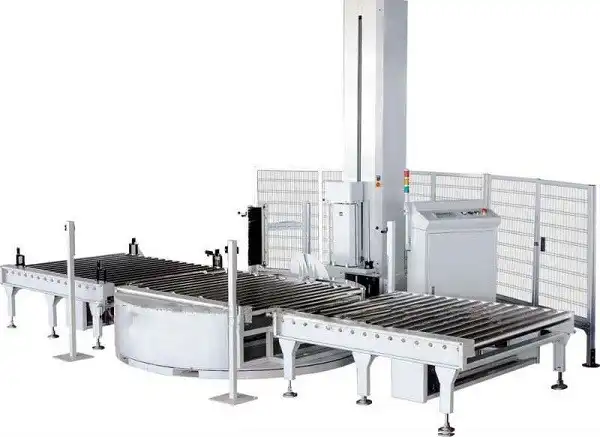
Integrating an automatic turntable stretch wrapper into your packaging line offers significant benefits:
- Consistency: Automated wrapping ensures every pallet receives the same programmed wrap pattern and tension, leading to predictable load containment.
- Efficiency: Significantly faster than manual wrapping, increasing throughput at the end of the packaging line.
- Load Security: Properly applied stretch film stabilizes the load, reducing product shifting and damage during handling and transit.
- Material Savings: Powered pre-stretch systems can stretch film by 150% to over 300%, drastically reducing film consumption compared to manual or less sophisticated wrapping methods.
- Labor Optimization: Frees up personnel previously assigned to manual wrapping for other value-added tasks.
- Improved Professionalism: Consistently wrapped pallets present a more professional image to customers.
Factors to Consider
When selecting an automatic turntable wrapper, consider:
- Load Characteristics: Weight, dimensions (L x W x H), stability, and uniformity of your typical pallet loads.
- Throughput Requirements: How many pallets per hour/shift need to be wrapped?
- Film Type: Ensure compatibility with the stretch film types you intend to use.
- Automation Level: Decide between semi-automatic (operator initiates cycle, attaches/cuts film) and fully automatic systems (integrated into a conveyor line).
In conclusion, automatic turntable pallet wrapping machines are indispensable tools for operations seeking to improve packaging efficiency, enhance load protection, and reduce costs associated with shipping damage and film consumption. By understanding their mechanics and features, businesses can select and implement the right solution to meet their specific end-of-line packaging needs.