Optimizing Packaging for Long Profiles: A Guide to Automatic Stretch Film Strapping Machines
Packaging long, often unwieldy items like metal profiles, extrusions, pipes, or lumber presents unique challenges for manufacturers and fabricators. Ensuring these items are securely bundled, protected from damage during transit and storage, and handled efficiently requires specialized solutions. Automatic stretch film strapping machines offer a robust answer, streamlining the packaging process and enhancing product integrity.
Understanding the Combined Approach: Stretch Film and Strapping
These automated systems typically combine two key packaging methods:
- Stretch Wrapping: Often utilizing an orbital wrapping technique for long items, a ring dispenses stretch film, wrapping it helically around the profile or bundle as it passes through the machine. This provides containment, stability, and protection against dust, moisture, and surface scratches.
- Strapping: Plastic straps (commonly Polypropylene - PP, or Polyethylene Terephthalate - PET) are automatically applied around the stretch-wrapped bundle at predetermined intervals. Strapping adds significant reinforcement, preventing bundles from separating, securing heavier loads, and improving handling characteristics.
This dual approach leverages the strengths of both methods – the containment of film and the high tensile strength of straps – creating a secure and well-protected package.
Visualizing the Process: Machine in Action
Observing these machines operate clarifies their efficiency and function. The following video demonstrates an automatic system designed for profiles:
Key Benefits of Automated Profile Packaging
Implementing an automatic stretch film strapping system offers several advantages for fabrication and manufacturing operations:
- Improved Product Protection: The combination of film and straps shields profiles from environmental factors and physical damage during handling and shipping.
- Enhanced Load Stability: Securely unitized bundles are less likely to shift or come apart, reducing the risk of damage and improving safety.
- Increased Throughput: Automation significantly speeds up the packaging process compared to manual methods, boosting overall operational efficiency.
- Reduced Labor Costs: Automating repetitive packaging tasks frees up personnel for other value-added activities.
- Optimized Material Usage: Machines can be calibrated for consistent film stretch and strap tension, potentially reducing material consumption compared to manual application.
- Consistent Package Quality: Automation ensures every bundle is wrapped and strapped to the same standard, improving reliability and customer perception.
Operational Considerations and System Types
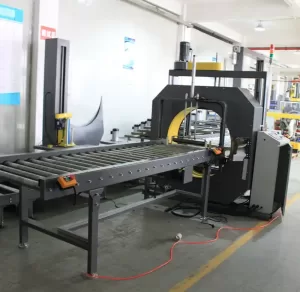
When considering an automated solution, several factors come into play:
- Profile Dimensions: Machine specifications must accommodate the length, width, height, and weight range of the products being packaged.
- Throughput Requirements: The machine's speed (bundles per hour) must align with production output.
- Level of Automation:
- Semi-Automatic: May require operator intervention to initiate cycles or position bundles.
- Fully Automatic: Integrate seamlessly into production lines, often receiving bundles via conveyors and discharging them automatically. These systems require minimal operator oversight.
- Strapping Needs: Determine the number of straps required per bundle, their placement, and the appropriate strap type (PP vs. PET) and dimensions based on load weight and security requirements.
- Integration: Consider how the machine will fit into the existing production layout and workflow, including infeed and outfeed conveyor systems.
Material Choices: Film and Straps
- Stretch Film: Available in various thicknesses (gauges) and formulations, chosen based on load shape, weight, and required puncture resistance.
- Strapping:
- PP Straps: Suitable for light to medium-duty applications, offering flexibility and cost-effectiveness.
- PET Straps: Provide higher tensile strength and retain tension better, making them ideal for heavier or less stable loads. They are often considered a viable alternative to steel strapping in many applications.
Selecting the Right System
Choosing the appropriate Automatic Stretch Film Strapping Machine for Profile involves assessing current and future packaging needs, evaluating available machine features against operational requirements, and considering factors like budget, floor space, and integration capabilities. Consulting with equipment suppliers who specialize in packaging automation can provide valuable insights tailored to specific applications.
By implementing effective automated packaging solutions like stretch film strapping machines, fabricators can ensure their products reach their destination securely and efficiently, protecting value and enhancing customer satisfaction.