Optimizing Tube Handling: A Guide to Automatic Steel Tube Stacking and Packing Systems
Handling steel tubes efficiently and safely after production presents a significant challenge for manufacturers. Manual methods are often labor-intensive, pose safety risks, and can lead to inconsistencies in bundle quality. Automatic steel tube stacking and packing systems offer a robust solution, streamlining this critical phase of the manufacturing process. These automated solutions enhance productivity, improve worker safety, and ensure tubes reach their destination in optimal condition.
The Limitations of Manual Tube Handling
Traditional manual stacking and packing processes often involve:
- Significant Labor Requirements: Requiring multiple workers to lift, carry, arrange, and bundle heavy tubes.
- Safety Hazards: High risk of musculoskeletal injuries (back strain, repetitive stress) and accidents associated with handling heavy, potentially sharp-edged materials.
- Inconsistent Bundle Quality: Variations in bundle shape, tightness, and tube arrangement can occur, potentially leading to transport issues or damage.
- Potential for Product Damage: Manual handling increases the likelihood of scratches, dents, or end damage to the tubes.
- Process Bottlenecks: Manual packing can limit overall production throughput, especially in high-volume operations.
steel tube packing line3 How Automatic Stacking and Packing Systems Operate
While designs vary based on specific requirements, most automatic steel tube stacking and packing systems follow a general process flow:
- Tube Infeed: Tubes arrive from the cutting line or finishing process, typically via roller conveyors.
- Counting and Layer Formation: Sensors count the tubes, and mechanisms (e.g., electromagnetic lifters, mechanical forks, robotic arms) arrange them into predetermined layers.
- Stacking/Bundling: Layers are sequentially stacked to form a complete bundle of the desired shape (hexagonal, square, or rectangular) and size.
- Bundling/Strapping: Once the bundle is formed, automated strapping machines apply steel or plastic straps at specified intervals to secure the tubes tightly. Some systems may incorporate wrapping functions for added protection.
- Discharge: The completed, secured bundle is transferred via conveyors or other mechanisms to a storage area or loading bay.
These systems rely on PLCs (Programmable Logic Controllers) for precise control, coordination between different components, and integration with upstream and downstream equipment.
Core Benefits of Automation in Tube Handling
Implementing an automatic steel tube stacking and packing solution yields substantial operational advantages:
- Enhanced Productivity and Throughput: Automation significantly increases the speed and efficiency of the stacking and packing process compared to manual methods, reducing cycle times and boosting overall output.
- Improved Workplace Safety: By eliminating manual lifting and handling of heavy tubes, these systems drastically reduce the risk of worker injuries, contributing to a safer work environment and lower workers' compensation costs.
- Consistent Product Quality and Reduced Damage: Automated handling is gentler and more controlled, minimizing scratches, dents, and end damage. It also ensures consistently shaped and secured bundles, improving stability during transport and storage.
- Labor Optimization and Cost Reduction: Automation reduces the need for manual labor in the packing area, allowing personnel to be reassigned to higher-value tasks. This leads to significant long-term savings in labor costs.
- Better Space Utilization: Automated systems can often be designed with a more compact footprint compared to the space required for manual operations and staging.
steel tube packing line2 Key Considerations When Selecting a System
Choosing the right automatic steel tube stacking and packing solution requires careful evaluation of several factors:
- Tube Specifications:
- Diameter Range (Minimum and Maximum)
- Length Range (Minimum and Maximum)
- Wall Thickness
- Tube Shape (Round, square, rectangular, other profiles)
- Material Type and Surface Finish
- Required Throughput:
- Tubes per minute or hour from the production line
- Desired bundles per hour
- Bundle Configuration:
- Bundle Shape (Hexagonal, square, rectangular)
- Bundle Dimensions (Width, height, length)
- Maximum Bundle Weight
- Level of Automation:
- Semi-automatic (requiring some operator intervention) vs. Fully automatic operation.
- Integration Needs:
- Compatibility with existing mill exit conveyors and downstream processes (e.g., weighing stations, marking systems, storage logistics).
- Facility Constraints:
- Available floor space and ceiling height.
- Power supply and compressed air availability.
- Control Systems:
- User interface requirements.
- Data logging capabilities (for traceability, performance monitoring).
- Potential for integration with plant-wide MES or ERP systems (Industry 4.0).
- Maintenance and Support:
- Supplier reputation, warranty, availability of spare parts, and technical support.
Integration and Implementation
Successful implementation involves thorough planning, including site preparation, seamless integration with existing production lines, and comprehensive operator and maintenance training. Working closely with the equipment supplier throughout this process is crucial.
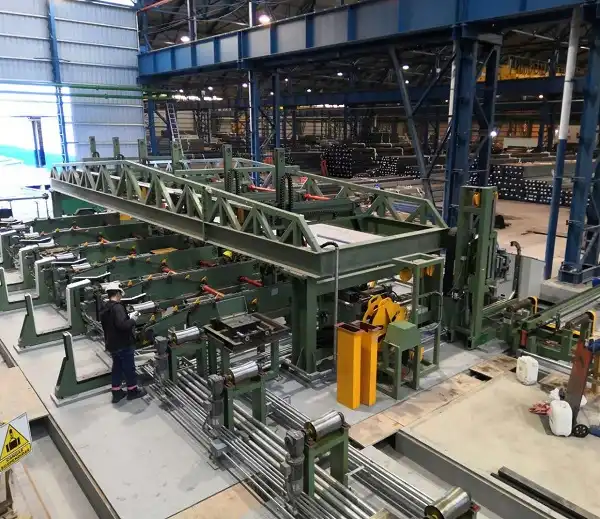
Conclusion
Automatic steel tube stacking and packing systems represent a significant advancement over manual methods. By automating this critical end-of-line process, manufacturers can achieve greater efficiency, enhance worker safety, ensure consistent bundle quality, and reduce operational costs. Carefully evaluating specific production needs and selecting the appropriate system are key steps toward optimizing tube handling operations.
For more insights into automated solutions:
More information on Automatic Steel Tube Stacking and Packing Lines