Streamlining Operations: An Overview of Automatic Steel Tube Packing Machine Lines
In modern manufacturing and distribution environments, efficiency, safety, and product integrity are paramount. For industries handling steel tubes, automated packing systems play a crucial role in achieving these goals. An automatic steel tube packing machine line integrates various processes to prepare tubes for storage or shipment with minimal manual intervention.
Understanding the Components and Functions
A typical automatic steel tube packing line comprises several interconnected modules designed to handle tubes efficiently:
- Tube Feeding & Counting: Systems accurately feed tubes from production or storage onto the line and count them to ensure precise bundle formation.
- Bundle Forming: Mechanisms arrange the tubes into the desired bundle shape (e.g., square, rectangular, hexagonal) based on pre-set parameters.
- Strapping/Wrapping: Automated strapping machines secure the bundle using steel or PET straps. Some lines may incorporate wrapping stations using materials like polyethylene film or woven straps for added protection against environmental factors.
- Conveying & Stacking: Conveyor systems transport the tubes through the different stages and move the finished bundles to designated collection or storage areas, sometimes including automatic stacking capabilities.
- Control System: A central control unit, often featuring a touch screen interface (HMI), manages the entire process, allowing operators to set parameters, monitor operations, and troubleshoot issues.
steel tube bundle wrapping machine Key Benefits of Automated Tube Packaging
Implementing an automatic steel tube packing line offers significant advantages:
- Increased Efficiency: Automation dramatically speeds up the packaging process compared to manual methods, leading to higher throughput and reduced cycle times.
- Improved Consistency: Machines perform repetitive tasks with high precision, ensuring uniform bundle shapes, strap tension, and overall package quality.
- Enhanced Safety: Reduces the need for manual handling of heavy tubes and bundles, minimizing the risk of workplace injuries.
- Product Protection: Secure and consistent bundling protects tubes from damage during handling, storage, and transportation.
- Labor Optimization: Frees up personnel from manual packing tasks, allowing them to focus on more value-added activities.
Example Technical Specifications
The capabilities of an automatic steel tube packing line can vary based on design and intended application. Below are example specifications to illustrate typical ranges. Note: These parameters may not exactly match the equipment shown in the video or specific models. Always consult manufacturer documentation for precise details.
Product Handling:
- Material: Carbon steel, galvanized steel tubes
- Tube Shape: Round, Square, Rectangular
- Round O.D. Range: 19 mm - 76.1 mm (Example Range)
- Square Profile Range: 15x15 mm - 60x60 mm (Example Range)
- Rectangular Profile Range: 25x10 mm - 100x20 mm (Example Range)
- Wall Thickness (W.T.): 0.8 mm - 4 mm (Example Range)
- Tube Length: 4 m - 9 m (Example Range)
- Required Straightness: Typically around 0.5mm per 1000mm
Bundle Parameters:
- Max Bundle Weight: Up to 2500 Kg (Example)
- Square Bundle Dimensions (W x H): 220x200 mm - 500x500 mm (Example Range)
- Hexagonal Bundle Dimensions (W x H): 200x200 mm - 575x500 mm (Example Range)
Performance:
- Production Rate: Can exceed 150 m/min for certain tube lengths (e.g., 6m), equating to a beat time of ~2.4 seconds per tube.
- Wrapping Material (if applicable): Polyethylene film, woven strap
Operating Requirements:
- Compressed Air: Typically around 6 bar
- Working Temperature: 5°C to 40°C
- Power Supply: e.g., 400V ± 10%, 50Hz ± 1% (Varies by region and design)
- Environmental Limits: 0°C to +40°C; Relative Humidity up to 90% at +20°C
Common Applications Across Industries
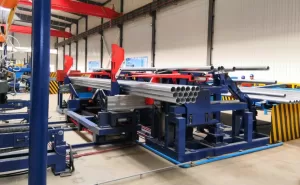
Automatic steel tube packing lines are essential in various sectors:
- Steel Mills & Tube Manufacturers: Streamlining the final packaging stage directly after production.
- Metal Service Centers: Efficiently repackaging tubes for distribution to diverse customers.
- Construction Industry Suppliers: Preparing large volumes of structural tubes for transport to job sites.
- Automotive Component Manufacturing: Packaging tubes used in vehicle frames, exhaust systems, and other components, supporting Just-in-Time (JIT) supply chains.
- Furniture Manufacturing: Bundling tubes used in frames and structures.
Selecting the Right System
Choosing an appropriate automatic steel tube packing line involves considering:
- Tube Specifications: Diameter, shape, length, and weight ranges.
- Required Throughput: The speed needed to match production or distribution demands.
- Bundle Requirements: Desired bundle size, shape, and weight.
- Level of Automation: Degree of integration required with upstream and downstream processes.
- Space Availability: Physical footprint of the machine line.
- Budget: Initial investment cost versus long-term operational savings.
By carefully evaluating these factors, businesses can implement an automated solution that significantly enhances their steel tube handling and packaging operations.
For more details on specific configurations, visit:
http://www.fhopepack.com/Automatic-steel-pipe-bundle-packing-line.html