Optimizing Pipe Handling: A Guide to Automatic Steel Pipe Packing Lines
In modern pipe mills and metal fabrication facilities handling steel, stainless steel, and aluminum pipes, efficient downstream processing is crucial. Manual packing of pipes into bundles can be labor-intensive, time-consuming, and pose safety risks. Automatic steel pipe packing lines offer a streamlined solution, automating the process from pipe collection to final bundle strapping. This guide explores the components, capabilities, and advantages of these systems.
Video demonstrating an automatic pipe packing line in operation.
What is an Automatic Steel Pipe Packing Line?
An Automatic Pipe Packing Machine is an integrated system designed to automatically collect, arrange, bundle, and strap pipes (including round and shaped profiles) produced on a mill or finishing line. By utilizing digital controls and mechanical handling, these lines create consistently shaped bundles (often hexagonal or square) tailored to specific pipe counts or weight requirements, significantly enhancing productivity and safety compared to manual methods.
Key Components and Their Functions
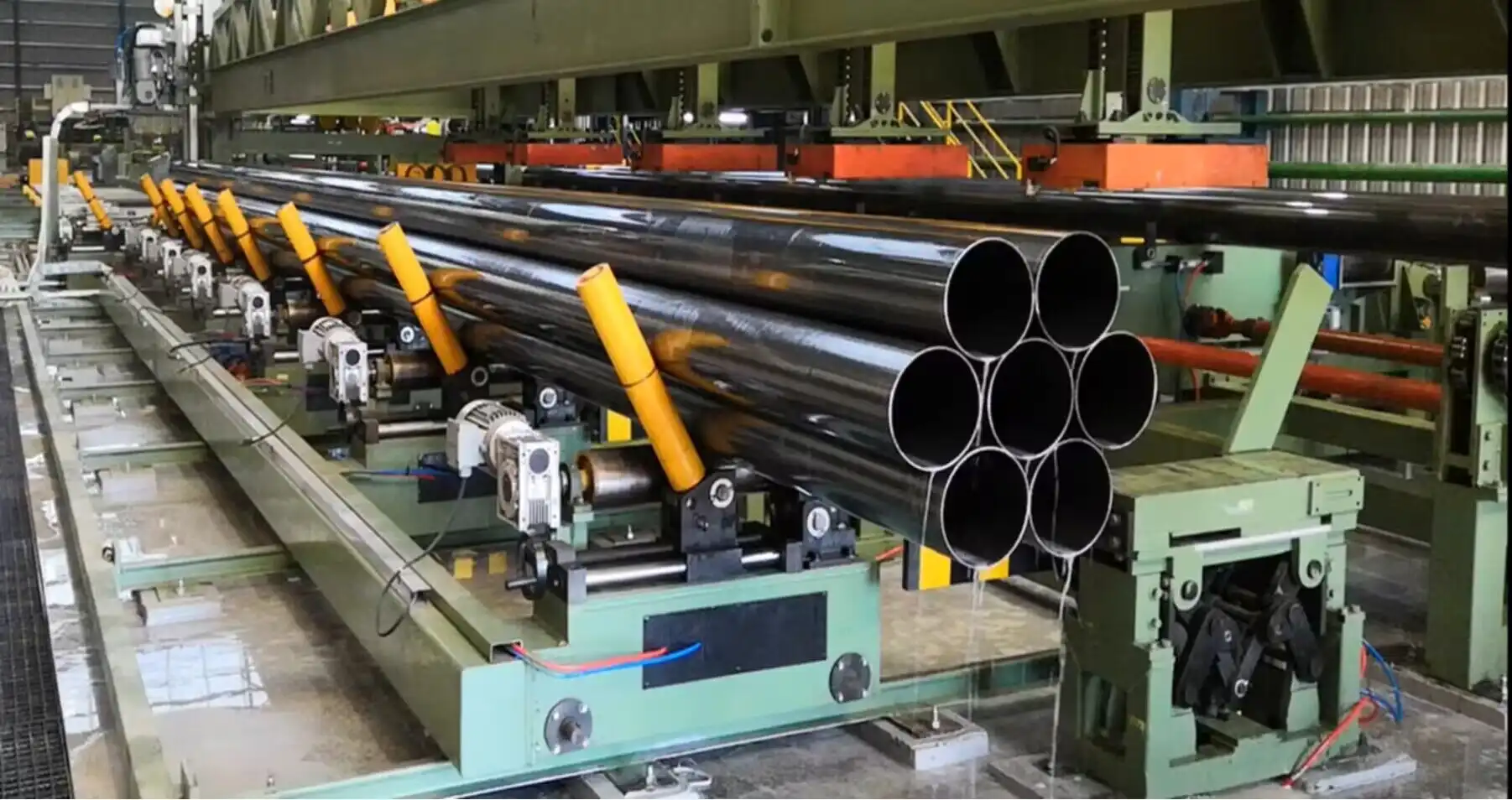
A typical automatic pipe packing line consists of several interconnected stations:
- Lifting Sequence Conveyor: Receives pipes from the production line and transports them towards the bundling area, often elevating them as needed.
- Pipe Layer Forming/Alignment: Carefully arranges individual pipes into layers, ensuring correct orientation and count before bundling. This may involve mechanisms like star wheels or chain conveyors with specific pockets.
- Tube Exchange Lever/Mechanism: Assists in manipulating pipes or layers to achieve the desired bundle shape.
- Bundling Station: Gathers the arranged layers of pipes into the final bundle configuration (e.g., hexagonal, square). This often involves forming pockets or clamps.
- Pocket (Fixed) / Transfer Pocket: Securely holds the formed bundle and facilitates its movement to the next station.
- Outlet Pack Conveyor / Package Sequence Conveyor: Transports the completed, unstrapped bundle away from the bundling station towards strapping.
- Auto Strapping Machine: Automatically applies and secures plastic or steel straps around the bundle at predetermined positions to maintain its integrity.
- Control Panel (PLC): The central processing unit (CPU) running programmable logic controller (PLC) software. It manages the entire sequence, controls motor speeds, sensor inputs, and allows operators to input parameters and select different packing recipes.
Core Capabilities and Advantages
Implementing an automatic pipe packing line offers several operational benefits:
- Increased Throughput: Significantly faster bundling cycles compared to manual packing, keeping pace with high-speed production lines.
- Consistent Bundle Quality: Produces uniform bundles with consistent shapes, pipe counts, and strap tension, improving storage and transport stability.
- Minimized Surface Damage: Automated handling is designed to be smoother and more controlled than manual methods, reducing the risk of scratches or scuffs, particularly critical for stainless steel and aluminum pipes.
- Operational Flexibility: Capable of handling various pipe diameters, lengths, wall thicknesses, and profiles (round, square, rectangular) with programmable adjustments.
- Improved Workplace Safety: Reduces the need for manual lifting and manipulation of heavy pipes, minimizing ergonomic strains and potential accidents.
- Labor Optimization: Automates repetitive tasks, allowing personnel to be reassigned to higher-value activities within the facility.
steel tube packing line Achieving Flexibility: Handling Diverse Pipe Specifications
The adaptability of an automatic steel tube bundle packing line to handle different pipe sizes and bundle requirements is a key feature, typically achieved through:
Programmable Logic Control (PLC): The PLC system is central to flexibility. Operators can program and store specific "recipes" for different pipe dimensions and customer orders. These recipes define parameters such as:
- Number of pipes per bundle.
- Arrangement pattern (e.g., hexagonal, square).
- Number and locations of straps.
- Conveyor speeds and timing sequences.
Selecting the appropriate pre-programmed recipe allows for quick changeovers between production runs.
Adjustable Bundle Size: The mechanical systems, guided by the PLC, can automatically adjust to form bundles with varying pipe counts based on the selected program.
Customizable Strapping Pitch: The automatic strapping machine can be programmed to apply straps at different intervals along the bundle length, accommodating different bundle sizes and stability requirements.
Adjustable Mechanical Guides and Supports: Components like side guides, conveyor widths, alignment tools, and bundling pockets often feature automated or manual adjustments to physically accommodate different pipe diameters and bundle dimensions.
Interchangeable Grippers/Forming Tools: Some systems may use specific grippers or forming tools tailored to certain pipe sizes or bundle shapes. While often designed for a range, significant changes might require tool swaps, which are typically designed for efficiency.
Sensor Integration and Feedback: Sensors detect pipe presence, position, and bundle characteristics, providing real-time feedback to the PLC for precise control and automatic adjustments during operation, ensuring proper handling across various sizes.
Servo-Controlled Motion: The use of servo motors for critical movements provides high precision and controlled acceleration/deceleration, enabling careful handling of pipes regardless of size and preventing damage during bundling and transfer.
Considerations for Implementation
When considering an automatic pipe packing system, factors such as line integration, available floor space, throughput requirements, the range of pipe sizes to be handled, and maintenance accessibility should be evaluated to ensure the selected system aligns with operational needs.
In summary, automatic steel pipe packing lines represent a significant advancement in optimizing the final stages of pipe production and processing. By automating the bundling and strapping process, these systems deliver enhanced efficiency, consistency, safety, and flexibility, making them a valuable asset in modern metal fabrication environments.