Optimizing Cable Handling: An In-Depth Look at Automatic Coiling and Wrapping Packing Lines
Automated systems are revolutionizing manufacturing and logistics, and cable handling is no exception. An automatic cable coiling and wrapping packing line represents a significant step forward, streamlining the process of preparing cables for storage or shipment. This technology enhances efficiency, ensures consistency, and improves overall operational workflow.
(Video showcasing an automatic cable coiling and wrapping packing line in operation)
Let's delve into the components, benefits, and considerations surrounding these sophisticated systems.
Understanding the Core Components and Process Flow
An automatic cable coiling and wrapping packing line integrates several key stages into a seamless, automated sequence. The typical workflow involves:
1. The Cable Coiling Stage
This initial phase utilizes a specialized cable coiling machine.
- Function: Draws cable from a larger spool or source.
- Operation: Automatically winds the cable into precise, uniform coils.
- Customization: Can be programmed for specific coil lengths, diameters, and winding patterns based on application requirements. This ensures consistency across production batches.
![Placeholder: Image of an automatic cable coiling machine in action. Alt text: Automated cable coiling machine precisely winding a black cable into a neat coil.]
2. The Cable Wrapping Stage
Once coiled, the bundle moves to the cable wrapping machine.
- Function: Applies a protective layer around the coiled cable.
- Materials: Common wrapping materials include stretch film (LLDPE), PVC, paper, or other specialized protective coverings.
- Purpose: Safeguards the cable against dust, moisture, abrasion, and potential damage during handling, transit, and storage. The wrap also helps maintain the coil's shape.
![Placeholder: Image showing a coiled cable being wrapped in protective film. Alt text: Close-up of a cable wrapping machine applying clear stretch film tightly around a coiled cable.]
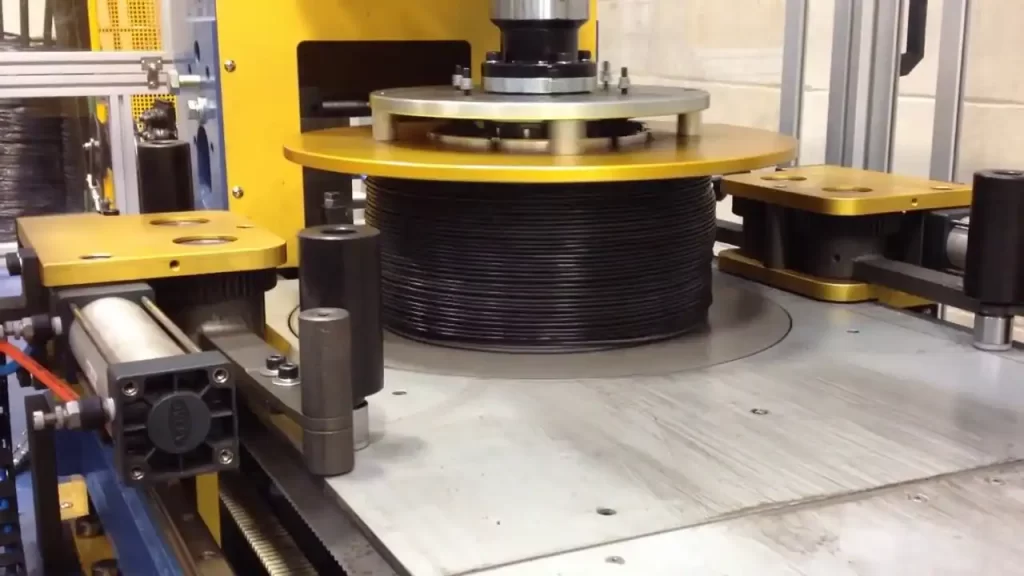
3. The Final Packaging Stage
After wrapping, the protected coil proceeds to the packaging machine.
- Function: Prepares the wrapped coil for final shipment or storage.
- Methods: This can vary widely depending on needs:
- Placing coils into cartons or boxes.
- Applying labels or identification tags.
- Shrink-wrapping individual or multiple coils for added security and stability.
- Stacking and palletizing coils for bulk handling.
Explore options for cable packing machines to understand the variety of end-of-line solutions available.
Key Benefits of Automating Cable Packaging
Implementing an automatic cable coiling and wrapping packing line offers substantial advantages over manual methods:
- Enhanced Efficiency and Throughput: Automation drastically reduces the time required per coil, significantly boosting overall production rates and shortening lead times. Machines operate continuously with consistent speed.
- Improved Consistency and Quality Control: Programmed settings guarantee uniformity in coil length, diameter, and wrap tightness, meeting precise specifications every time. This eliminates variations inherent in manual coiling and wrapping.
- Reduced Labor Costs and Operator Strain: Automating repetitive tasks frees up skilled labor for more complex duties. It also significantly reduces the risk of repetitive strain injuries (RSIs) associated with manual coiling and lifting heavy bundles.
- Minimized Material Waste: Precise control over cable length per coil and the amount of wrapping material applied reduces scrap and excess usage, leading to cost savings and more sustainable operations.
- Improved Safety: Enclosed automated systems reduce direct human interaction with moving machinery and heavy materials, creating a safer working environment.
Considerations for Implementation
Choosing and integrating an automated cable handling system requires careful planning:
- Cable Types and Sizes: Ensure the system can handle the specific range of cable diameters, flexibility, and materials you process.
- Coil Specifications: Define your required coil lengths, inside/outside diameters, and maximum coil weights.
- Wrapping Material Requirements: Specify the type, thickness, and application method for the protective wrap.
- Throughput Needs: Match the machine's processing speed (coils per hour) to your production targets.
- Integration: Consider how the line will integrate with upstream (extrusion, spooling) and downstream (palletizing, warehousing) processes.
- Footprint and Layout: Ensure adequate space and an efficient layout within your facility.
cable coil wrapping machine Maintaining Optimal Performance
Like any industrial equipment, automated cable lines require proper care:
- Regular Maintenance: Adhere to the manufacturer's recommended maintenance schedule for cleaning, lubrication, and inspection of critical components.
- Operator Training: Ensure operators are thoroughly trained on machine operation, safety procedures, basic troubleshooting, and quality checks.
- Software Updates: Keep the machine's control software updated to benefit from performance improvements or new features.
Conclusion
Automatic cable coiling and wrapping packing lines are indispensable tools for modern cable manufacturers and distributors aiming for higher efficiency, consistent quality, and improved operational safety. By automating these critical processes, companies can reduce costs, enhance product protection, and better meet the demands of a competitive marketplace. Evaluating your specific needs against the capabilities and considerations outlined above will help in selecting and implementing a system that delivers tangible benefits to your operation.