Optimizing Aluminum Profile Handling: A Guide to Automatic Stacking and Packing Lines
Efficiently handling and packaging aluminum profiles is a critical step in modern fabrication and manufacturing. Manual processes can be labor-intensive, prone to inconsistencies, and pose potential safety risks. Automatic aluminum stacking and packing lines offer a robust solution, streamlining operations, enhancing throughput, and ensuring product protection from the end of the production line to storage or shipment.
Understanding the Automated Process
An Automatic Aluminum Stacking Machine Packing Line is an integrated system designed specifically for the automated handling of aluminum sections, such as extrusions and profiles. These systems typically automate several key stages:
- Automated Loading: Profiles are received from the production line or a buffer zone onto the system's infeed conveyor.
- Precision Stacking: Robotic arms or specialized mechanical stackers carefully arrange the profiles into neat, stable bundles or stacks according to pre-set configurations. This ensures uniformity and optimizes space.
- Protective Wrapping: The formed stack is transferred to a wrapping station. Here, industrial stretch film, VCI film, or other protective materials are automatically applied to secure the bundle and shield it from environmental factors like moisture, dust, and scratches during transport and storage.
- Conveying and Offloading: The securely packaged stack is moved via conveyor to an output station, ready for storage, further processing, or shipping.
Advanced sensors and PLC (Programmable Logic Controller) systems with HMI (Human Machine Interface) panels orchestrate these stages, ensuring seamless integration, precise control, and the flexibility to handle various profile shapes and stacking patterns.
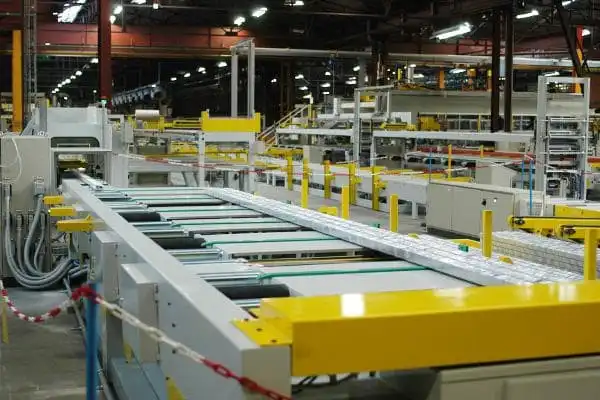
Key Features and Typical Specifications
While specific capabilities vary based on manufacturer and configuration, common features define these automated lines:
- System Type: Fully Automated Stacking and Packing Line
- Material Compatibility: Primarily designed for aluminum sections and extrusions; adaptability for similar materials may be possible.
- Stacking Capacity: Varies significantly based on design (e.g., up to 100 kg or more per stack).
- Operational Speed: Dependent on profile size, stack configuration, and wrapping requirements (e.g., capable of processing up to 30 stacks per hour).
- Wrapping Material: Compatible with various industrial films, including options for anti-corrosion or specialized protective layers.
- Control System: Advanced PLC with user-friendly HMI for operation monitoring, parameter adjustment, and diagnostics.
- Power Requirements: Typically requires industrial power supply (e.g., 380V, three-phase).
- Conveyor System: Adjustable speed conveyors (e.g., up to 15 meters per minute) for smooth material flow.
- Stacking Mechanism: Often utilizes robotic arms or servo-driven mechanical systems for high precision and gentle handling.
- Safety Features: Equipped with light curtains, safety fencing, emergency stops, and sensors to ensure operator safety and protect equipment.
- Footprint: System dimensions vary based on capacity and configuration (Example: Length: 7000mm; Width: 2400mm; Height: 2200mm).
- Construction: Built for durability and continuous operation in demanding industrial environments.
Note: The specifications listed are illustrative. Actual parameters depend on the specific machine model and application requirements. Consultation with manufacturers is recommended for precise configurations.
Core Benefits of Automation in Aluminum Handling
Implementing an automatic stacking and packing line yields significant advantages:
- Increased Throughput: Automation dramatically speeds up the stacking and packing process compared to manual methods.
- Reduced Labor Costs: Frees up personnel from repetitive, physically demanding tasks, allowing them to focus on higher-value activities.
- Improved Consistency and Quality: Ensures uniform stacking and tight, secure wrapping for every bundle, reducing variability.
- Enhanced Product Protection: Minimizes scratches, dents, and other handling-related damage to sensitive aluminum surfaces.
- Optimized Material Flow: Creates a smoother, more predictable flow from production to warehousing or shipping.
- Improved Workplace Safety: Reduces risks associated with manual lifting and handling of heavy or awkward profiles.
- Better Space Utilization: Neatly stacked bundles optimize storage space in warehouses and during transport.
Key Industry Applications
The efficiency and precision of these automated systems make them invaluable across various sectors:
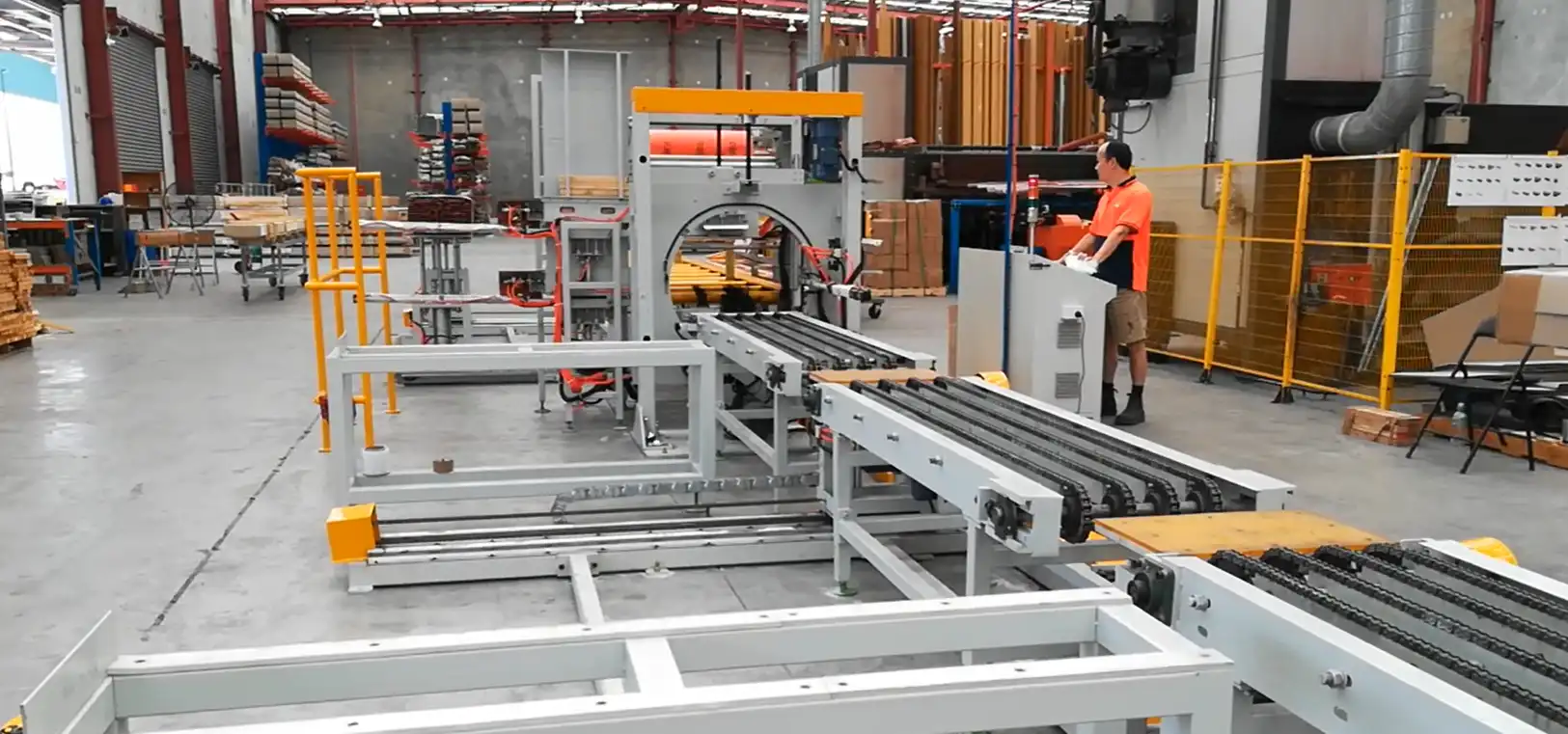
Construction Industry: Streamlining Material Flow for Building Systems
Aluminum profiles are essential for windows, doors, curtain walls, and structural components. Automated stacking lines efficiently handle long or complex extrusions, packaging them securely for transport to job sites. This reduces handling time, minimizes damage risk, and ensures materials arrive ready for installation, improving project timelines.Automotive Manufacturing: Supporting Lean Production
In automotive, where aluminum is increasingly used for lightweighting, automated systems supply neatly packed profiles and components directly to assembly lines. This supports just-in-time manufacturing, reduces line-side inventory, minimizes handling damage to critical parts, and contributes to overall production efficiency.Aerospace Industry: Meeting Stringent Handling Standards
Aerospace demands meticulous handling to protect high-value aluminum alloys from surface defects or contamination. Automated stacking and packing lines provide the required precision and gentle handling, ensuring components maintain their integrity throughout the logistical chain, meeting strict quality and safety standards.General Manufacturing and Fabrication:
Any facility processing significant volumes of aluminum extrusions—for furniture, electronics, solar panel frames, or general fabrication—can benefit from the increased speed, consistency, and labor savings provided by automated stacking and packing technology.
Considerations for Implementation
Adopting an automated stacking and packing line requires careful planning:
- Profile Variety: Assess the range of profile shapes, sizes, and lengths the system needs to handle.
- Throughput Needs: Match the system's speed and capacity to your production output.
- Footprint and Layout: Ensure sufficient space is available and consider integration with existing production lines.
- Integration: Plan for seamless communication between the packing line and upstream/downstream equipment.
- Operator Training: Factor in training requirements for operation and basic maintenance.
- Maintenance: Understand the preventative maintenance schedule to ensure long-term reliability.
By automating the stacking and packing of aluminum profiles, manufacturers and fabricators can achieve significant improvements in efficiency, quality control, and operational safety, strengthening their competitive position in the market.