Automated vs. Manual Pallet Inverters: Which Offers the Best ROI?
- Automated vs. Manual Pallet Inverters: Which Offers the Best ROI?
- Introduction
- 1. Understanding Pallet Inverters: A Brief Overview
- 2. Manual Pallet Inverters: Key Features and Capabilities
- 3. Automated Pallet Inverters: The Future of Material Handling
- 4. Calculating ROI for Manual Pallet Inverters
- 5. Calculating ROI for Automated Pallet Inverters
- 6. Factors Affecting ROI: Key Considerations
- 7. Long-Term Cost Savings of Automated Systems
- 8. Comparing Maintenance and Downtime
- 9. Flexibility and Customization Options
- 10. Industry Applications and Best Fits
- 11. Environmental and Safety Considerations
- 12. Conclusion: Which Pallet Inverter Offers the Best ROI?
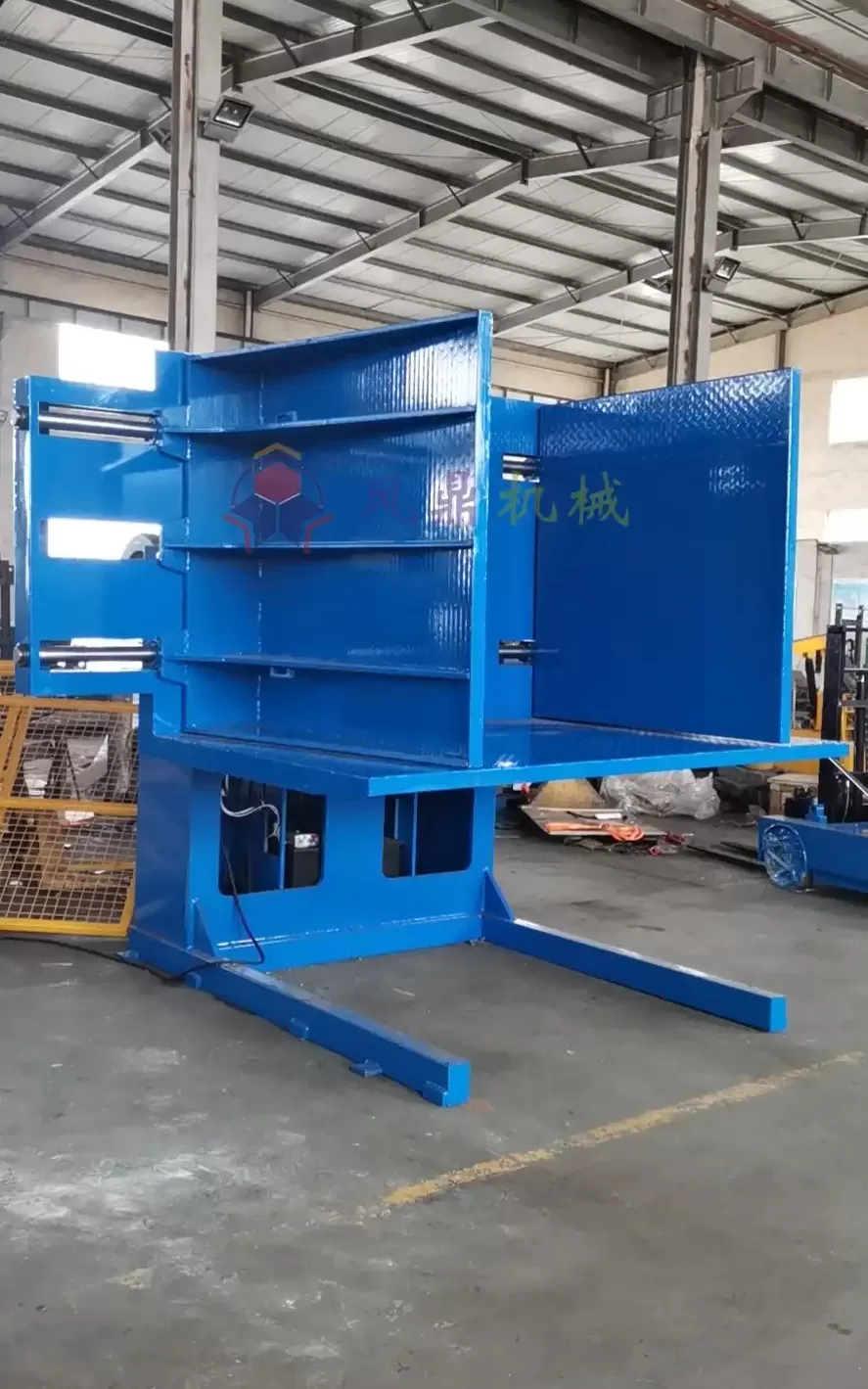
Introduction
In the world of warehousing and logistics, efficiency and cost-effectiveness are paramount. One crucial piece of equipment that plays a significant role in improving warehouse operations is the pallet inverter. These machines make it easier to handle heavy pallet loads, reduce manual labor, and maintain product safety. But with the variety of options available, companies are often faced with a critical decision: Automated pallet inverters or manual pallet inverters? Understanding which of these options offers the best return on investment (ROI) can significantly impact a business’s operational efficiency and bottom line.
In this article, we’ll dive deep into the comparison between automated and manual pallet inverters, exploring their initial costs, operational benefits, long-term savings, and how to calculate the best ROI for your business. Whether you’re operating in warehousing, food and beverage, pharmaceutical, or any other industry, the choice between manual and automated pallet inverters is one that requires careful consideration.
1. Understanding Pallet Inverters: A Brief Overview
Before we delve into the differences between automated and manual options, it’s essential to understand the primary function of a pallet inverter. Pallet inverters are machines designed to rotate or flip pallets and their loads to enable efficient loading, unloading, or replacement of damaged goods. These devices are vital for industries where speed and safety are critical, helping to minimize product damage and reduce the risk of injury during pallet exchanges.
2. Manual Pallet Inverters: Key Features and Capabilities
Manual pallet inverters are the more traditional solution. As the name suggests, these machines require manual intervention to operate, which means a worker is needed to initiate the inversion process. These inverters usually have lower upfront costs and are favored by smaller businesses or operations with lower volumes. However, they do come with some limitations.
Advantages of Manual Pallet Inverters:
- Cost-Effective for Small Operations: The upfront investment in a manual inverter is relatively low, making it an attractive option for businesses looking to minimize capital expenditure.
- Simplicity and Durability: Manual inverters tend to have fewer moving parts than automated systems, which can translate into easier maintenance and longer service life.
- Flexibility: Workers can quickly adjust the operation of manual inverters to suit various load types, providing a level of flexibility that some automated systems might lack.
Disadvantages of Manual Pallet Inverters:
- Labor-Intensive: The need for human intervention makes these systems more labor-intensive and, over time, this increases operational costs.
- Slower Productivity: The speed of manual pallet inverters is typically slower than their automated counterparts, which can create bottlenecks in high-volume environments.
- Potential for Errors: Manual handling increases the risk of operational errors, product damage, and even injuries, leading to potential hidden costs over time.
3. Automated Pallet Inverters: The Future of Material Handling
Automated pallet inverters are designed to operate with minimal to no human intervention. These systems are often integrated into broader automated workflows, which makes them ideal for high-volume environments such as large warehouses and manufacturing facilities. While they come with a higher initial cost, their long-term benefits often justify the expense.
Advantages of Automated Pallet Inverters:
- Increased Efficiency: Automated systems can handle a greater number of pallets per hour than manual systems, dramatically improving throughput.
- Labor Savings: By reducing the need for manual intervention, automated inverters can help businesses save on labor costs, particularly in industries where labor is a significant part of operational expenses.
- Consistency and Precision: Automation ensures that each load is handled with the same precision, reducing the likelihood of product damage or misalignment.
- Safety: Automated pallet inverters minimize the need for workers to handle heavy loads directly, thereby reducing the risk of workplace injuries. This leads to lower insurance premiums and fewer downtime incidents due to accidents.
Disadvantages of Automated Pallet Inverters:
- High Initial Investment: The upfront cost of an automated system is significantly higher than that of a manual system, which can be a barrier for smaller businesses or those with tighter budgets.
- Complexity in Setup: Automated systems require more complex integration into existing workflows, which might necessitate additional costs for customization, training, and maintenance.
4. Calculating ROI for Manual Pallet Inverters
When assessing the ROI of a manual pallet inverter, the primary factors to consider are the initial cost, ongoing labor costs, and the operational speed. For smaller operations with low-volume requirements, the lower upfront cost might make manual inverters a cost-effective choice.
To calculate ROI, consider the following formula: ROI (%) = (Net Profit from Investment / Initial Investment) x 100
For manual systems:
- Net Profit would be calculated based on labor costs saved by using the manual inverter instead of entirely manual pallet handling.
- Initial Investment is the cost of purchasing and installing the manual pallet inverter.
In a small warehouse operation that handles around 50 pallets per day, the ROI for a manual inverter may be more attractive, as labor costs are relatively low and the need for speed is not as critical.
5. Calculating ROI for Automated Pallet Inverters
For automated systems, the ROI calculation is more complex, as it involves several long-term savings factors. These include labor cost reductions, increased throughput, and reduced downtime due to automation. Although the initial investment is higher, the long-term savings in labor and increased productivity often result in a higher ROI over time.
Automated systems shine in high-volume operations. If a warehouse processes hundreds or thousands of pallets daily, the speed and efficiency of an automated pallet inverter can quickly offset the upfront cost. Here’s a simplified breakdown:
- Net Profit for automated systems includes savings from reduced labor, fewer errors, faster processing times, and enhanced safety.
- Initial Investment includes the cost of the automated system, installation, and any integration into existing systems.
For a large-scale warehouse handling 1,000 pallets a day, the ROI of an automated inverter might be realized within the first few years due to the dramatic increase in efficiency and the reduction in labor costs.
6. Factors Affecting ROI: Key Considerations
When comparing the ROI of manual versus automated pallet inverters, several critical factors come into play:
- Volume of Pallet Handling: For smaller operations, manual inverters may suffice, but larger-scale operations will benefit from the efficiency of automation.
- Labor Costs: In regions where labor costs are high, the savings from reducing manual labor can significantly impact the ROI of an automated system.
- Safety and Compliance: Industries with strict safety regulations may find that the safety benefits of automated systems justify the higher cost.
- Maintenance Costs: Automated systems typically require more maintenance, which can affect the overall ROI, but their consistent performance often outweighs these costs.

Get Your Best Solution !
7. Long-Term Cost Savings of Automated Systems
One of the most significant advantages of automated pallet inverters is their potential for long-term cost savings. While the initial investment might be higher compared to manual systems, the savings generated over time from increased efficiency, reduced labor, and minimized downtime can far outweigh the initial costs.
Automated systems can operate continuously, handling large volumes without the need for frequent breaks or manual intervention. This not only improves productivity but also ensures that the entire workflow is streamlined. The precision of automated systems means less product damage, leading to fewer losses or replacements. Over the course of several years, these factors combine to create a more cost-efficient operation.
Additionally, automation reduces worker fatigue and the risk of injuries, which can lead to lower workers’ compensation costs and fewer disruptions due to accidents. These savings further contribute to the overall return on investment.
8. Comparing Maintenance and Downtime
Another critical aspect when evaluating the ROI of pallet inverters is maintenance and downtime. While manual pallet inverters tend to have simpler mechanics and require less maintenance, they can still cause delays due to human error or physical limitations of workers. In contrast, automated pallet inverters, although more complex, are built to perform with consistency and precision, reducing the likelihood of downtime caused by operational errors.
That said, automated systems may require scheduled maintenance and can have higher repair costs due to their advanced technology. However, if properly maintained, these systems can operate for extended periods without significant interruptions, which offsets the occasional maintenance cost. Many automated pallet inverter manufacturers also offer support contracts that include regular servicing to ensure optimal performance.
In high-volume operations, minimizing downtime is crucial. The speed and reliability of automated pallet inverters help reduce the risk of bottlenecks in the supply chain, improving overall productivity. This improvement in operational uptime directly contributes to a higher ROI.
9. Flexibility and Customization Options
When it comes to versatility, both manual and automated pallet inverters offer a range of options, but automated systems tend to provide more customization capabilities. For example, automated pallet inverters can be integrated with existing warehouse management systems (WMS) and tailored to meet specific operational requirements, such as handling different pallet sizes, materials, and weights.
On the other hand, manual pallet inverters offer greater flexibility in terms of human control. Workers can make quick adjustments to account for irregular loads, and manual inverters can often handle a broader range of products without the need for software adjustments. This flexibility is beneficial in smaller operations where the variety of tasks is greater, but the volume is lower.
For businesses that require consistent, high-speed handling of similar pallet types, automation offers unmatched efficiency. In contrast, manual systems might be more suitable for smaller-scale operations that handle a variety of loads and need adaptability.
10. Industry Applications and Best Fits
The choice between manual and automated pallet inverters largely depends on the industry and the specific operational needs of the business. Here’s a quick breakdown of which type of pallet inverter may be best suited for different industries:
- Food and Beverage: Automation is essential for high-speed environments where hygiene and consistency are critical. Automated pallet inverters are ideal for these industries due to their ability to reduce human contact with the product.
- Pharmaceuticals: Similar to food, the pharmaceutical industry benefits from automation’s precision and the ability to maintain strict hygiene standards. Automated systems reduce the risk of contamination, ensuring products are handled safely.
- Manufacturing: Large-scale manufacturers dealing with heavy loads and requiring high throughput will see the best ROI from automated pallet inverters.
- Warehousing and Logistics: Both manual and automated systems have a place in warehousing, depending on the volume. For smaller warehouses, manual inverters may suffice, but larger distribution centers will benefit significantly from automation.
- Small Businesses: For smaller operations with a tight budget and lower volumes, manual inverters offer a cost-effective solution.
Understanding the specific needs of your industry and operations will help determine which pallet inverter offers the best ROI.
11. Environmental and Safety Considerations
Beyond operational efficiency, there’s also a growing focus on environmental sustainability and workplace safety. Automated pallet inverters contribute to both areas. By reducing the need for manual labor, businesses can decrease the risk of workplace injuries. According to safety reports, manual handling of heavy loads is one of the leading causes of warehouse-related injuries. Automated systems significantly mitigate this risk, creating a safer work environment.
From an environmental perspective, automated systems can help reduce waste through more efficient use of materials and by minimizing product damage. Additionally, automation reduces energy waste by optimizing operation times, which contributes to a company’s overall sustainability goals.
While manual pallet inverters are often simpler in design and operation, they do not offer the same level of safety enhancements or environmental benefits as automated systems. This is an essential consideration when looking at the long-term ROI, especially for companies with a strong focus on sustainability and worker safety.
12. Conclusion: Which Pallet Inverter Offers the Best ROI?
In the battle between automated vs. manual pallet inverters, the right choice ultimately depends on your business’s size, industry, and long-term operational goals. For smaller businesses or those with low-volume operations, manual pallet inverters offer a cost-effective solution with minimal maintenance and flexibility. They can provide a decent ROI in environments where labor costs are manageable, and speed is not the highest priority.
However, for high-volume operations, the clear winner is automated pallet inverters. The long-term savings in labor, increased productivity, reduced downtime, and improved safety all contribute to a higher ROI. Although the upfront costs are more significant, the benefits of automation quickly make up for the initial investment, especially in industries where speed, precision, and safety are critical.
In conclusion, the best ROI comes from selecting the pallet inverter that aligns with your operational needs. Automated pallet inverters shine in environments where efficiency, volume, and safety are prioritized, while manual systems offer simplicity and cost savings for smaller-scale operations. By carefully considering these factors, businesses can make an informed decision that maximizes their return on investment.

Get Your Best Solution !