Automated Steel Coil Packing: Bringing Your Factory into the Industry 4.0 Era
- Automated Steel Coil Packing: Bringing Your Factory into the Industry 4.0 Era
- 1. What is Industry 4.0 and Why is it Relevant to Steel Coil Packing?
- 2. How Automated Systems Revolutionize Steel Coil Packing
- 3. How Automated Packing Reduces Downtime
- 4. How Automation Ensures Stability in Coil Packing
- 5. How Automated Systems Reduce Labor Dependency
- 6. How Industry 4.0 Technologies Enhance Automated Packing Systems
- 7. How Automation Improves Product Quality and Customer Satisfaction
- Conclusion

In the era of Industry 4.0, where automation and smart technologies dominate, manufacturers face a critical decision: either adapt to the evolving landscape or risk falling behind competitors. For the steel coil industry, automation is no longer a luxury but a necessity. Steel coil packing, a traditionally manual and labor-intensive process, is being revolutionized by automated systems that not only streamline operations but also ensure consistency, precision, and stability. In this article, we will focus on how automated steel coil packing systems bring your factory into the Industry 4.0 era, exploring the key mechanisms and technologies involved in this transformation.
1. What is Industry 4.0 and Why is it Relevant to Steel Coil Packing?
Industry 4.0 marks the fourth industrial revolution, characterized by the integration of automation, artificial intelligence (AI), and data exchange into manufacturing processes. Industry 4.0 focuses on creating smart factories where machines are interconnected and communicate with each other to make real-time decisions and optimize production. This concept is particularly relevant for the steel coil industry, where automation can significantly reduce downtime, eliminate inefficiencies, and ensure high-quality packing and shipping.
In steel coil packing, automated systems can completely transform the way products are handled, packed, and prepared for shipment. These systems leverage smart technology to streamline operations, ensuring that every coil is packed with precision while reducing human error and labor dependency. Automation enables factories to increase throughput, reduce waste, and create a more efficient production environment—key goals of the Industry 4.0 vision.
2. How Automated Systems Revolutionize Steel Coil Packing
Manual steel coil packing involves significant labor and time, as workers have to individually handle each coil, wrap it, and secure it with straps. This process is prone to mistakes, inconsistencies, and delays. Automated steel coil packing systems bring a new level of efficiency by automating every step of the process. Here’s how they revolutionize packing:
- Precision and Consistency: Automated systems apply uniform tension in wrapping and strapping coils, ensuring that each coil is securely packed without variation. This consistency is difficult to achieve manually, where variations in technique or fatigue can lead to inconsistent packaging.
- Speed: Automated machines can pack coils much faster than human workers. They are designed to handle multiple coils simultaneously, with the ability to adjust settings automatically for different coil sizes. This not only reduces downtime between packing jobs but also allows factories to meet higher production quotas.
- Flexibility: Automation allows for real-time adjustments to packaging parameters. For example, sensors embedded in the system detect the size, shape, and weight of each coil, adjusting the wrapping and strapping process accordingly. This flexibility is critical for factories dealing with varying coil types, enabling them to switch between products without having to manually reconfigure machines.
By adopting automated systems, steel coil manufacturers can ensure that their production lines run smoothly and efficiently, eliminating the delays and errors that come with manual processes.
3. How Automated Packing Reduces Downtime
Downtime—whether planned or unplanned—can significantly impact a manufacturer’s bottom line. In manual packing processes, downtime is common due to the need for worker breaks, manual adjustments, or machine maintenance. These interruptions slow down production and reduce the overall efficiency of the factory.
Automated steel coil packing systems drastically reduce downtime by ensuring continuous operation. Here’s how:
- Continuous Workflow: Automated systems are capable of running 24/7 without the need for breaks or human intervention. Unlike human workers, machines don’t tire or need to stop for lunch breaks, ensuring that the packing process continues without interruption.
- Minimal Setup Time: When transitioning between different coil sizes or materials, manual packing often requires significant downtime to adjust settings or reconfigure the packing machinery. Automated systems, however, are equipped with programmable logic controllers (PLCs), which automatically adjust parameters based on the coil’s dimensions and packing requirements. This means that downtime is minimized as machines seamlessly adjust to different jobs without manual input.
- Integrated Maintenance Alerts: Automated systems often come with diagnostic tools that monitor performance in real-time, alerting operators when maintenance is needed. These systems can predict issues such as wear and tear on moving parts or material shortages, allowing operators to perform preventive maintenance without having to halt the production line unexpectedly.
Through these advanced features, automated packing systems significantly cut down on both planned and unplanned downtime, ensuring a smooth and efficient production flow.
4. How Automation Ensures Stability in Coil Packing
Stability is a key concern in steel coil packing, particularly because steel coils are heavy and must be securely packed to prevent movement during transport. Manual packing methods often lead to inconsistencies in wrapping or strapping, which can result in the coil shifting or becoming damaged during handling. Automated systems solve this problem by ensuring consistent stability in every package.
Here’s how automated systems enhance stability:
- Precision Tensioning: Automated wrapping machines control the amount of tension applied to each coil, ensuring that it is wrapped tightly without causing damage. This precise tensioning eliminates the risk of under- or over-tightening, which is common in manual operations.
- Consistent Strapping: Strapping machines in automated systems apply uniform pressure when securing coils. This consistency is critical for ensuring that coils remain securely bound during transportation. Variations in manual strapping can lead to coils loosening over time, increasing the risk of movement during shipping.
- Tailored Packaging for Different Coil Types: Automated systems are capable of adjusting the amount and type of packaging material used based on the coil’s size, weight, and shape. This ensures that each coil is packed according to its specific needs, further enhancing its stability during transport.
By maintaining a high level of stability in the packing process, automated systems reduce the risk of damaged products, which in turn minimizes returns and lost revenue.
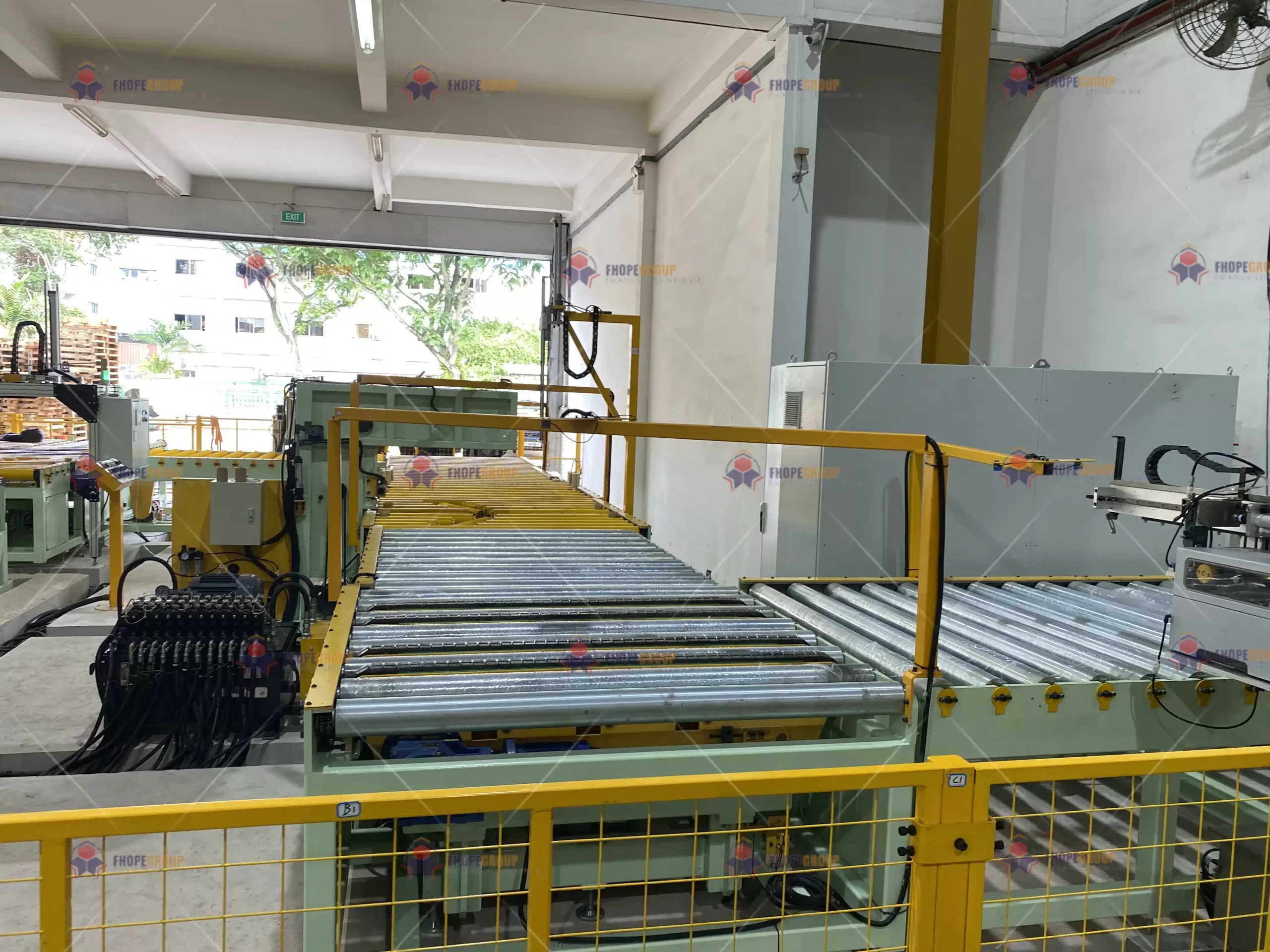
5. How Automated Systems Reduce Labor Dependency
The reliance on manual labor in steel coil packing has long been a challenge for manufacturers. Not only is the process labor-intensive, but it also poses safety risks due to the heavy and awkward nature of steel coils. Automated systems provide a solution by drastically reducing the need for human intervention in the packing process. Here’s how automation reduces labor dependency:
- Eliminating Repetitive Tasks: Manual packing involves repetitive tasks such as lifting, wrapping, and strapping, which can lead to worker fatigue and injury. Automated machines take over these repetitive tasks, reducing the strain on workers and improving workplace safety.
- Minimal Supervision Required: Automated systems are designed to operate with minimal oversight. Once the system is programmed, it can run continuously, only requiring human intervention for routine maintenance or adjustments. This allows manufacturers to reduce their staffing requirements, particularly for packing operations, which are traditionally labor-intensive.
- Improving Worker Safety: The heavy lifting and handling required in manual steel coil packing expose workers to a high risk of injury. Automated systems eliminate the need for workers to physically handle coils, significantly reducing the risk of accidents and improving overall safety.
By automating labor-intensive processes, manufacturers can cut down on labor costs, reduce workplace injuries, and reallocate human resources to more strategic roles such as system monitoring and optimization.
6. How Industry 4.0 Technologies Enhance Automated Packing Systems
Industry 4.0 is all about smart technologies that enable machines to communicate with each other, collect and analyze data, and make decisions in real-time. Automated steel coil packing systems, when integrated with these Industry 4.0 technologies, bring even greater efficiency and reliability to the packing process.
Here’s how these technologies enhance automated systems:
- Real-Time Data Monitoring: Automated systems equipped with IoT sensors collect data on every aspect of the packing process. This includes information on coil dimensions, material usage, system performance, and maintenance needs. This data can be monitored in real-time, allowing operators to make adjustments on the fly to optimize the process.
- Predictive Analytics: By analyzing data collected from sensors, manufacturers can use predictive analytics to anticipate issues before they occur. For example, data on machine wear and tear can alert operators to perform maintenance before a breakdown happens, reducing downtime and keeping the production line running smoothly.
- Remote Access and Control: Industry 4.0 technologies allow operators to monitor and control packing systems remotely. This is particularly useful for large manufacturing plants where machines are spread across different locations. Remote access allows for faster response times and more efficient management of the entire production line.
Through these smart technologies, automated packing systems become more than just machines—they become an integral part of a smart, interconnected factory that is capable of self-optimization and continuous improvement.
7. How Automation Improves Product Quality and Customer Satisfaction
One of the ultimate goals of Industry 4.0 and automation is to improve the overall quality of products while meeting customer expectations. In steel coil packing, automation plays a vital role in ensuring that every coil is packed with precision, reducing the chances of damage during transport and improving product quality.
Here’s how automation contributes to higher product quality:
- Consistency Across Every Package: Automated systems ensure that every coil is packed using the same parameters, resulting in consistent quality. This is particularly important for customers who expect a certain standard of packing to prevent damage during transport.
- Improved Protection: Automation allows for the precise application of packing materials, ensuring that each coil is adequately protected from external factors such as moisture, dust, or rough handling. This reduces the risk of product returns due to damaged goods, improving overall customer satisfaction.
By consistently delivering high-quality products, manufacturers can build stronger relationships with their customers
, leading to repeat business and a more loyal customer base.
Conclusion
As the steel industry continues to evolve, automated steel coil packing systems play a crucial role in bringing factories into the Industry 4.0 era. Automation reduces downtime, enhances stability, and minimizes labor dependency while improving product quality and consistency. By integrating smart technologies such as IoT, data analytics, and real-time monitoring, manufacturers can optimize their packing processes, improve operational efficiency, and prepare for the future of manufacturing.
In the Industry 4.0 landscape, automated packing systems are more than just machines—they are essential tools for transforming your factory into a smart, efficient, and competitive operation. Embracing automation is no longer an option but a necessity for steel manufacturers looking to thrive in the modern era.