Enhancing Efficiency: Understanding Automated Aluminum Profile Packing Machines
Aluminum profiles require careful handling and packaging to prevent damage during transport and storage. Automation plays a crucial role in streamlining this process, improving both efficiency and consistency. This guide explores the workings and benefits of automated aluminum profile packing systems, specifically those incorporating wrapping and tape banding.
1. What is an Automated Aluminum Profile Packing System?
An automated aluminum profile packing system is designed to handle the packaging of aluminum extrusions with minimal manual intervention. The system shown in the video below demonstrates a common configuration that combines profile wrapping (often with paper or protective film) and secure tape banding.
This type of automation is engineered for high-speed handling, often allowing a single operator to manage the entire packaging line for aluminum profiles.
2. How the Wrapping and Banding Process Works
While specific designs may vary, the core process generally involves several key stages:
2.1. Infeed Conveyor System
Aluminum profiles are fed into the machine via a conveyor system. The speed is typically controlled to ensure proper spacing and synchronization with the subsequent packaging steps.
2.2. Profile Wrapping (Paper/Film)
As profiles move through the machine, wrapping material (like protective paper or stretch film) is dispensed from rolls. Rotating mechanisms apply the material around the profile's circumference, providing a protective layer against scratches and surface damage. The machine automatically cuts the wrapping material to the correct length for each profile or bundle.
2.3. Tape Banding Application
Following the wrapping stage, adhesive tape is applied. Dispensers apply plastic adhesive tape, often both vertically and horizontally, around the wrapped profile or bundle. This securely binds the profiles together (if bundled) and keeps the wrapping material in place.
2.4. Output and Discharge
Once wrapped and banded, the finished packaged profiles are moved onto an output conveyor. From here, they can be transferred for further processing, stacking, or direct shipment.
3. Core Technology and Components
These automated systems rely on a combination of mechanical and electronic components:
- Sensors: Photoelectric, inductive, or proximity sensors detect the presence and position of aluminum profiles on the conveyor, ensuring accurate timing for wrapping and banding operations.
- Material Feed Systems: Rolls of wrapping film and adhesive tape are mounted on unwind stands with tension control systems. The feed speed is synchronized with the conveyor.
- Actuation: Pneumatic systems or servo motors power the moving parts, such as the wrapping ring/rolls, tape dispensers, cutters, and conveyor drives, enabling high-speed, precise movements.
- Control System: A Programmable Logic Controller (PLC) or industrial computer serves as the brain of the operation. It coordinates all actions, monitors sensors, and controls motors based on pre-programmed settings.
- Adjustability: Key parameters like wrapping tension, tape tension, the number of tape bands applied, and conveyor speed can often be adjusted via the control interface. This allows the machine to handle different aluminum profile sizes, shapes, and packaging requirements. Advanced systems may include features like automatic profile length detection and auto film cutting.
- Configuration: Machines can be designed for packaging profiles oriented either vertically or horizontally, depending on the application needs.
4. Key Benefits of Automated Aluminum Profile Packaging
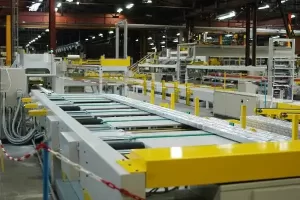
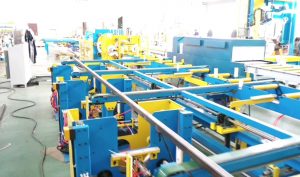
Implementing automated wrapping and banding systems offers significant advantages over manual methods:
- Increased Efficiency and Throughput: Automation significantly speeds up the packaging process, allowing output to match high-speed extrusion lines.
- Improved Consistency and Quality: Machines apply wrapping and tape uniformly every time, leading to consistent package quality and better product protection compared to manual variations.
- Reduced Labor Costs: Automation drastically cuts down the manual labor required for packaging, often allowing one operator to oversee a process that previously needed several workers.
- Enhanced Product Protection: Consistent wrapping and secure banding minimize the risk of scratches, abrasions, and other damage during handling and shipping.
- Streamlined Operations: Automated systems can often be integrated with other upstream (extrusion, cutting) and downstream (stacking, palletizing) processes for a fully optimized workflow.
5. Considerations for Implementation
When considering an automated system, factors to evaluate include:
- Range of profile sizes and shapes to be handled.
- Required packaging speed (throughput).
- Type of wrapping material and tape needed.
- Level of automation required and integration possibilities.
- Available floor space and budget.
6. Explore Further Solutions
Automated packaging technology offers diverse solutions for the aluminum industry. For a broader look at various systems including wrapping, tapping, stacking, and handling equipment, you can explore resources like the following:
https://www.fhopepack.com/Aluminum/index.html
In summary, automatic aluminum profile wrapping and banding machines deliver substantial benefits in terms of efficiency, consistency, labor savings, and product protection, making them a valuable investment for modern aluminum extrusion facilities.