What Makes an Aluminum Profile Packaging System Essential for Streamlined Operations?
In my role at FHOPEPACK, I often see how efficient packaging becomes essential for producers. A solid system streamlines tasks, saves costs, and brings consistent protection for aluminum profiles daily.
A well-planned packaging system handles aluminum profiles with care and speed. It uses automation and precise control to reduce errors. It also improves consistency and lowers manual labor. That results in smoother production. It allows uniform wrapping and safer transport. It adjusts tension, positions loads, keeps surfaces free from scratches.
I have worked with many packaging lines at FHOPEPACK. I see that an efficient system adds value to each step. It helps optimize handling, wrapping, and movement of aluminum profiles. I find that a good setup prevents wasted time. It also prevents product damage. That can add up to large savings. My personal experience shows that better packaging reduces manual rework and labor strain. This approach brings peace of mind to operators. They do not have to monitor every detail. The machine ensures uniform tension and alignment. This leads to consistent outcomes. I have seen shipping accidents decrease when products are wrapped properly. That raises trust among clients.
I think that a packaging system also improves workplace safety. Moving heavy aluminum profiles by hand can cause mishaps. Automated conveyors reduce the chance of injuries. They support better ergonomics. There is less lifting. There is also less twisting of the body. That means healthier staff. There are fewer production stops.
When production ramps up, a system that can handle volume is vital. Scaling output without losing quality is tough. But an automated line with a focus on tension and stability can make it happen. I have noticed that once staff members trust the process, they focus on other tasks. They do not worry about uneven wraps. They do not re-inspect each bundle. This speeds up the entire operation.
This post will explain how a packaging system improves workflow efficiency. Then it will show the key components for better performance. Finally, it will guide you in selecting the best option for your needs. I hope my observations will help you understand how these systems can transform your production environment. Please read on to learn more.
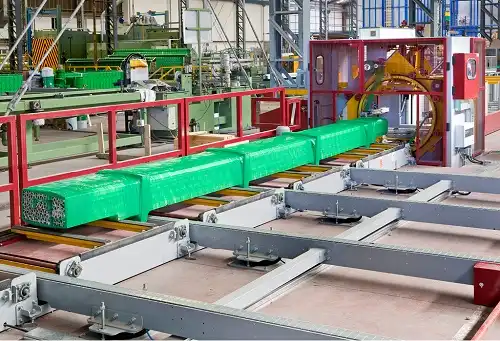
How Does an Aluminum Profile Packaging System Improve Workflow Efficiency?
In my view at FHOPEPACK, a strong packaging system sets the pace. It reduces delays, improves arrangement, and stops mistakes. That speeds up flow for aluminum profile operations quite often.
It accomplishes this by integrating conveyors, tension controls, and automated film application. That allows steady movement of profiles. Operators spend less time adjusting materials or redoing wraps. This consistent approach lowers wasted material and reduces the chance of damage. It leads to stable output and seamless scheduling on the floor.
One big factor in workflow efficiency is the way the system handles each aluminum profile. I have seen that a balanced, automated line ensures profiles move from one station to the next without needless waiting. This reduces idle time. It also prevents pileups that can slow the overall process.
Detailed Stages for Enhanced Flow
I like to look at each stage: loading, wrapping, and unloading. In the loading stage, the system’s conveyors or arms place profiles in the correct orientation. That helps with alignment, which then helps the wrapping part. In the wrapping stage, tension controls and film rollers work together. They apply the film at the correct tension, which stops slack or tearing. Finally, the unloading stage moves the wrapped profiles to the next area, like a palletizing station or shipping bay.
Stage | Primary Action | Benefit |
---|---|---|
Loading | Places profiles in correct position | Cuts misalignment and reduces delays |
Wrapping | Applies film with proper tension | Prevents damage and secures each bundle |
Unloading | Moves finished bundles to next step | Speeds transition and saves space |
These steps, when integrated, help maintain a continuous pace. I remember when we first implemented an automated line at a facility. We noticed that the consistent movement let us plan daily outputs with more confidence. We no longer relied on unpredictable manual handling. Operators could handle tasks like film changes or quality checks without stopping the entire operation.
Impact on Human Labor
In my experience, this approach means workers can focus on more skilled duties. They do not have to manually wrap each profile. They can manage the machine or troubleshoot minor errors. That leads to better job satisfaction and more stable results. I believe that when a machine takes care of repetitive tasks, staff can watch for issues or help with maintenance. That can stop major breakdowns.
Also, an automated system can track data points. For example, it can measure how many profiles get wrapped each hour. It can log machine downtime or tension adjustments. This data helps managers see bottlenecks. They can decide if they need extra staff or if they should adjust shift patterns. Over time, I have watched how even small improvements in these metrics can lead to higher throughput.
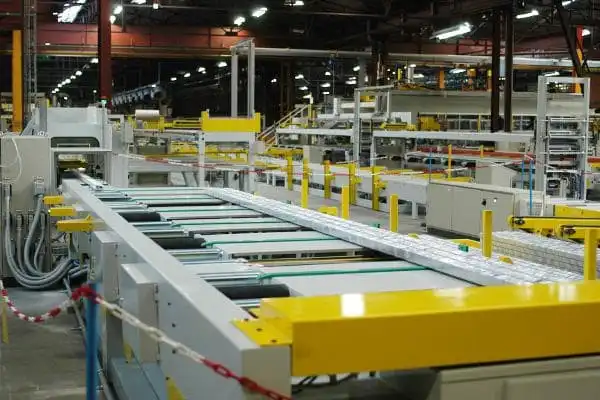
Reducing Unplanned Delays
Workflow efficiency also relies on preventing unplanned stops. A well-made system has sensors that detect problems, such as incorrect placement or film tears. The system pauses automatically, which lets an operator fix the issue quickly. This is better than ignoring it and causing more extensive damage or more downtime. In some cases, the system can reroute profiles to a different line. That keeps the workflow moving.
I recall a scenario where a sensor noticed a slight film jam. The machine stopped before the wrap got tangled. The operator cleared the issue and restarted the system. That took a couple of minutes. Without the sensor, we might have needed hours to fix a major jam. That difference shows the importance of automation in maintaining steady workflow efficiency.
All these factors—automated movement, consistent wrapping, data monitoring, and quick error detection—combine to improve the entire operation. When each step is synchronized, it is simpler to plan production schedules and meet client deadlines. This helps the business scale up or handle unexpected orders without missing key shipping dates.
What Key Components Drive the Performance of a Modern Packaging Solution?
I often notice that performance depends on the quality and arrangement of each part. A modern packaging solution relies on well-made components that work together for smooth operation and reliability.
These parts include conveyors, film dispensers, tension controllers, sensors, and sealing systems. They must run in sync to protect aluminum profiles. Sensors detect irregularities and help avoid damage. Conveyors maintain movement. Tension controllers keep the wrap tight. The sealing unit finishes the job. Good synergy produces consistent packaging results everywhere.
Performance is not just about speed. It is also about how each component interacts. I have seen lines that run quickly but fail to protect profiles because tension controllers were not calibrated. Other times, a perfect wrap was undone by a poor conveyor layout that caused collisions or misalignment. A balanced system pays attention to every component, from the simplest roller to the most advanced sensor.
A Closer Look at Essential Components
I like to examine the core elements. First, conveyors move profiles between stations. They should be sturdy and properly aligned. They must handle the weight and shape of profiles without jamming. Next, film dispensers feed the wrap at the correct rate. If the dispenser struggles, it can cause uneven coverage or film breaks. Then, tension controllers regulate the force applied to the wrap. I see that correct tension helps maintain product integrity. It keeps the film from ripping or from leaving gaps.
Component | Main Function | Common Pitfalls |
---|---|---|
Conveyor | Moves profiles from station to station | Misalignment or jams |
Film Dispenser | Feeds wrapping film at a set rate | Uneven coverage or film breaks |
Tension Controller | Adjusts film tension for uniform wrapping | Over-tightening or loose wraps |
Sensor | Detects placement, alignment, or film issues | False alerts or missed errors |
Sealing Mechanism | Secures film edges for a neat, final package | Weak sealing or incomplete sealing |
Sensors then check if each profile is in the right position. They also detect if the film is applied properly. If sensors are not configured well, the system can pause needlessly, or worse, keep running and damage the product. The sealing mechanism forms a secure package once the wrapping is done. If the seal is weak, the film might unravel in transit.
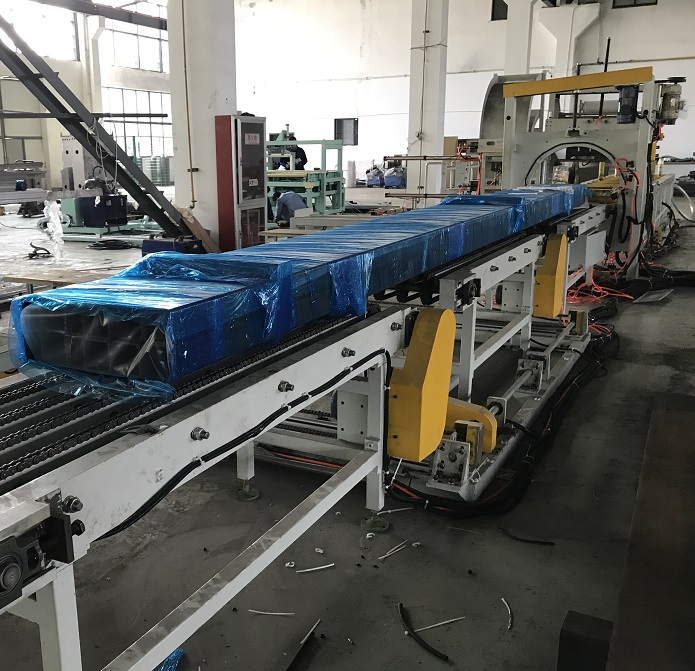
Importance of Integration
I have found that integration matters. If the conveyor does not sync with the tension control, you can get wrinkles or tears. If the sensor triggers too late, the sealing stage might miss the perfect position. This synergy relies on both hardware and software. Some systems use PLCs (programmable logic controllers) to coordinate each step. The PLC ensures that the line runs in a set sequence. It can also adjust speeds or tension levels for different profile sizes. In my experience, good software control is just as vital as strong mechanical parts.
Maintenance and Upgrades
Performance also depends on how well you maintain the system. Even the best components degrade without proper care. Lubricating bearings, cleaning sensors, and replacing worn belts can keep everything running at peak efficiency. I remember a time when ignoring a small sensor fault led to frequent stops. After we fixed the sensor alignment, the line worked much more smoothly. Regular checks can catch problems early, saving time and money.
Upgrades can also improve performance. If you add advanced sensors, you gain better detection. If you install a more sophisticated tension control, you can handle thinner films or heavier loads. The key is to ensure that each upgrade fits the rest of the system. I have seen attempts to add a high-speed conveyor to a slow wrapping station. That mismatch caused backups. A balanced upgrade approach yields the best results.
Overall Impact on the Bottom Line
When components function in harmony, the entire packaging process is smoother. This cuts down on labor needs, lowers error rates, and accelerates production. Each of these improvements raises profitability. Also, a system that uses robust components is more reliable. It can handle fluctuating demands without constant adjustments. This reliability boosts customer confidence. Clients receive their aluminum profiles on time and in good condition. That trust can lead to repeat business and a positive reputation.
I believe that focusing on component quality and integration is one of the best ways to improve packaging efficiency. People often underestimate the value of precise control. But from my perspective, every roller, sensor, or tension knob makes a difference in a fast-paced production environment. Investing in good parts and in thorough training can make a modern packaging solution run at its full potential.
How Do You Choose the Right Packaging Setup for Your Specific Requirements?
I have been asked many times about matching a system to unique production goals. People want maximum efficiency without overspending. The right setup depends on budget, volume, and functionality precisely.
I start by checking daily output targets. Then I see if the line needs specialized wrapping options. Next, I consider available floor space and power sources. Some setups fit small operations, while others handle large, automated flows. A tailored approach saves money and time. That can lead to better productivity.
Choosing the right packaging setup is a strategic decision. I often weigh factors like load size, wrapping speed, budget constraints, and the potential for future expansion. It is not just about buying the biggest or most advanced machine. It is about finding the right balance that fits the specific workflow.
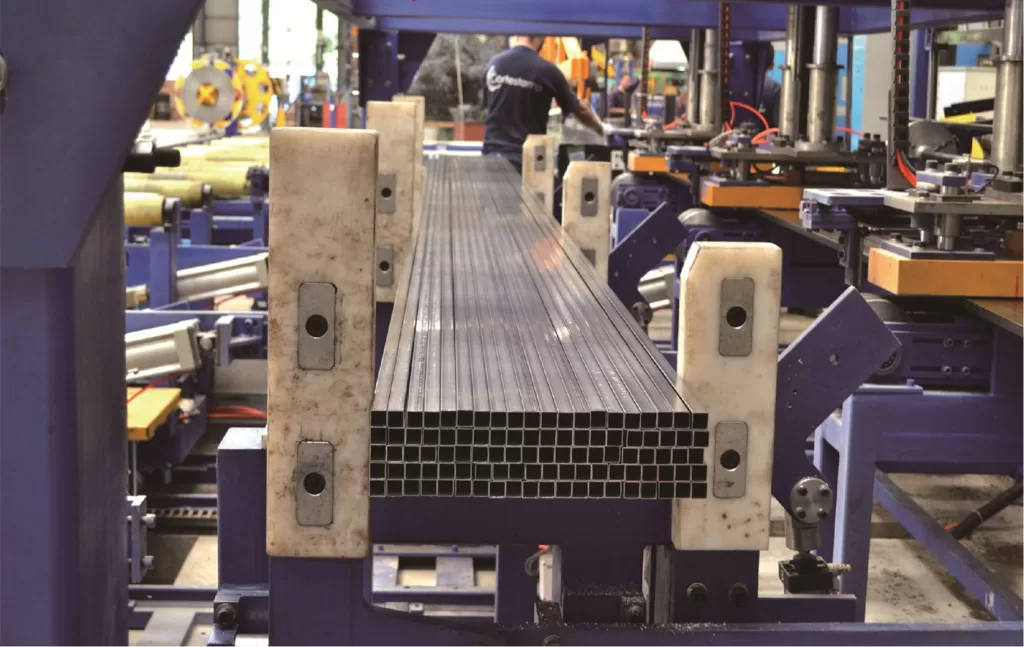
Step-by-Step Evaluation
I like to break down the selection process. First, analyze the average size, length, and weight of the aluminum profiles. That will show you what type of conveyor and tension system you need. Second, estimate daily or monthly volume. If you run massive batches, you might want a fully automated line. If your batches are smaller, a semi-automatic setup might suffice. Third, consider the shape of the workspace. Sometimes, a straight conveyor path is not possible. You might need a custom layout or a turntable to navigate corners.
Consideration | Why It Matters | Example |
---|---|---|
Profile Dimensions | Ensures correct conveyor and tension | Long profiles need stable conveyors |
Output Volume | Determines automation level needed | Large runs benefit from full automation |
Workspace Layout | Affects conveyor routes and equipment | Tight spaces may need special designs |
Future Expansion | Allows for upgrades when production grows | Modular units or additional stations |
Budget and Return on Investment
I know budget often shapes the final choice. A high-end system might speed things up drastically, but the initial cost can be steep. A simpler system could save money at first, but it might struggle as orders grow. I have seen factories opt for a mid-range solution that can be upgraded in steps. That strategy spreads out costs while keeping production flexible.
Return on investment should be part of the discussion. If a more advanced system cuts labor costs, film waste, and rework, the payback might happen faster than expected. I recall a case where adding better sensors and a robust tension controller decreased product damage by 20%. That alone justified the extra expense.
Tailored vs. Off-the-Shelf
Some setups come ready to go, which can be fine for standard profiles. But if you deal with unusual shapes or exotic finishes, you might need a custom approach. Custom features can include special rollers, film layering, or added safety guards. I recommend checking if the supplier offers design customization. That can save trouble down the road. I remember a time we tried to force a standard line to handle curved profiles. We had jam after jam. Eventually, we retrofitted the conveyor. That took extra time and money.
Service and Training
I place a lot of value on service and training. A great machine means little if your staff cannot maintain or operate it properly. Look for a supplier who offers training sessions. They should teach your operators how to adjust tension, replace film, or troubleshoot minor stops. Support plans also matter. Is there a local service center? Do they have spare parts on hand? I have seen machines sit idle for days because a key part was stuck in shipping. That can disrupt schedules badly.
Planning for Growth
Last, think about the future. Do you expect bigger orders in a year? Will you add new product lines? A flexible system might cost more now, but it can adapt when demands change. For instance, a modular conveyor can expand to fit new stations. Or you might install software that can track new data points. I find that forward-thinking choices usually pay off. They let you stay competitive without a full overhaul.
By following these steps and prioritizing what matters most to your production, you can choose a setup that supports both short-term and long-term goals. I believe that thoughtful planning and open communication with suppliers is the key. That way, you get a system that is efficient, stable, and ready for any shifts in market demands.
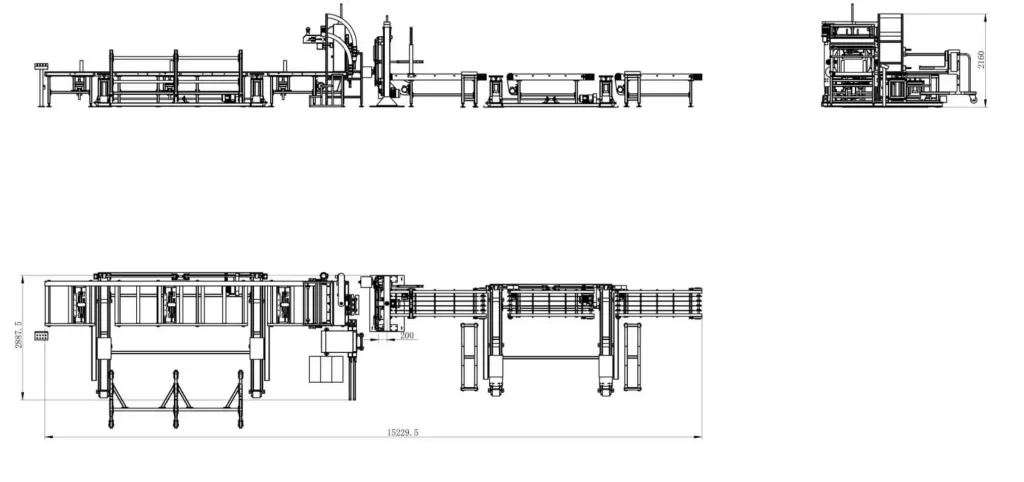
Conclusion
I have learned that a well-designed aluminum profile packaging system can make a real difference. It improves workflow, unifies different processes, and safeguards products. It uses integrated components and follows a systematic approach to fit specific needs. From my perspective at FHOPEPACK, I see that investing in a reliable setup increases speed and lowers errors. It frees up labor for other tasks. It also reduces film waste. The result is a higher standard of packaging, which pleases clients and elevates a company’s reputation. Choosing the right equipment involves comparing volumes, analyzing workspace, and planning for expansion. A robust system offers smooth operation and stable outcomes. I hope my experience helps others see the value of careful planning and good implementation. FHOPEPACK stands for knowledge sharing, and I trust this article clarifies how aluminum profile packaging solutions can drive productivity and success. Thank you for reading. I am also glad to see how these systems reduce repetitive strain for operators. They benefit from an orderly line that manages tension, sealing, and movement. In my opinion, a packaging solution should evolve with the business. As new needs emerge, the system can be adapted to maintain efficient, reliable performance. This fosters real stability.